基于机器视觉的车床主轴径向跳动误差测量方法研究
2020-3-6 来源:主轴; 径向跳动误差; CCD; 亚像素 作者:彭凯 杨泽青 杨伟东 刘丽冰
摘 要: 非接触测量是解决主轴在线测量的途径。为此研究一种机器视觉系统用于机床主轴径向跳动误差的测量。该系统由面阵 CCD 相机、镜头、光源、计算机和图像处理软件组成。CCD 传感器记录主轴边缘点的跳动图像,经过图像数据处理得到边缘点的跳动数值。设计长像距镜头,使得物象比例接近 1,结合亚像素定位算法,提高边缘实际定位精度。经过分析验证,系统测量得到的径向跳动误差达亚微米级。表明该方法可以用于检测机床径向跳动精度,适用于转速较低的加工机床主轴跳动误差在线测量。
关键词: 主轴; 径向跳动误差; CCD; 亚像素
主轴是机床整机系统中极其重要的部件,对于主轴的研究、测试及实验[1-3],就是为了主轴系统能达到基本设计要求。机床主轴的运动误差是评价机床动态性能的一项重要指标,直接影响其加工工件的几何精度和表面粗糙度。对于机床主轴径向跳动误差的测试,可以判断机床在理想加工条件下的加工精度等级。测试结果在线反馈给数控系统则能够部分补偿回转误差带来的精度损失。因此主轴径向跳动误差测试方法一直为广大学者和工程技术人员所关注。
在 20 世纪 60 年代,日本的大园成夫提出了基于三点法测量回转误差,即对安装在主轴上的标准球进行单点或多点测量,采集的数据受到标准球的安装和形状误差的干扰,需进行误差分离才能得到主轴回转误差,其关键技术在于误差分离[4-7]。基于误差分离技术的传统测量方法很多,基本以圆度误差检测与误差分离方法应用最广,随着现代测量技术的发展已经相当完善。基于机器视觉的测量方法,尽管精度相对较低,但是其非接触测量,测量系统结构简单,为部分研究人员所关注,并设计了一些机器视觉方法测量主轴回转误差的系统,通过在主轴上设置标志点,实现离线的主轴回转误差测量[8-9]。
本文在此基础上提出边缘聚焦测量主轴跳动误差,并且可以在线进行该误差测量。
1 、测量原理
主轴的跳动误差从宏观表象即是主轴绕轴线转动过程中存在一定的跳动,该跳动可以从主轴边缘的跳动观察到。因此只需要能观察到边缘跳动的数据,即可计算得到主轴跳动的误差。机器视觉是模拟人眼观察外界场景的变化,主轴的跳动测量可以转化为主轴边缘图像的测量,通过测定主轴在回转过程中主轴边缘位置的变化得到跳动误差。
摄像机成像测量基本原理是针孔成像,即物像关系满足高斯公式( 1) :

相机拍摄的物距一般远大于像距,因此往往成像要比实际物体小,为了获得边缘的高精度定位,需要增加像距,则物距变短,对应的景深也会减小。经过测算,物距与像距相等时,景深值大约 2 mm 左右,所以在构建测量系统时,调整镜头与物像位置将比较困难。
2 、实验系统构建
系统结构图如图 1 所示。
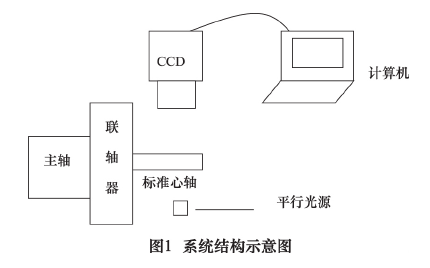
实验系统由机床,平行投影光源,面阵 CCD 摄像机和带数据处理软件的计算机组成。CCD 摄像机采用高速相机,能抓拍主轴旋转时的清晰图像; 镜头在标准 50 mm 镜头的基础上增加增距环,使得像距 150mm,这样使得 CCD 相机能成清晰的像时,物距也接近80 mm,物像放大率接近 1。照明采用背光投影方式,可以保证主轴边缘与背景有最大的对比度,便于实现边缘的高精度定位。即使得相机与单色平行光源布置于标准心轴两侧,调节相机的位置和镜头焦距,将成像共轭平面调整至主轴最大直径边缘位置,拍摄主轴边缘图像如图 2 所示。
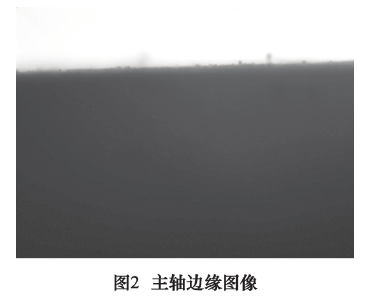
3 、亚像素边缘定位
确定主轴跳动量,关键在于精确定位主轴图像边缘的位置。确定目标图像的边缘位置时,亚像素定位算法能有效提高边缘的定位精度[9]。采用背光投影法能提高图像边缘清晰度,但是由于边缘散色效应,边缘图像仍然是呈现灰阶过渡带; 并且成像过程中增加像距,相应的物距成倍减小,成像的景深也变得很小。仅成像共轭平面附近能成清晰像,景深范围不超过 2mm,当共轭平面对准主轴边缘附近时,远离 CCD 区域将成模糊图像,靠近 CCD 区域仅景深范围内清晰,其他区域因离焦成模糊图像。主轴边缘图像呈现直线特征,因此利用 Hessian 矩阵算法实现直线边缘的亚像素定位[10],定位精度能达到 0. 2 pixel。周围的一些杂散点通过尺寸信息可以滤除,那么亚像素边缘点经过直线拟合,得到主轴边缘投影的位置信息。
一帧图像可以获得主轴边缘在某个时刻的位置信息,连续拍摄多帧图像,这些图像需要覆盖主轴回转的各个角度时的姿态,计算主轴在各个角度时的位置信息。两帧图像之间主轴边缘的直线距离作为主轴跳动。
4 、相机参数标定
相机拍摄主轴轮廓位置,得到 CCD 上像素单位的长度数据,主轴的跳动值反应了像素数量的变化,实际跳动值与像素间距和成像放大率均有直接关系。由于测量系统仅针对主轴边缘处测量,测量位置相对于相机几乎不动,因此仅需要在被测量平面处放置一块标定板,让相机拍摄几幅图像,通过标定板上的标准方格尺寸,换算对应的成像像素数量,从而计算 CCD 像面象元间距对应水平和垂直方向物点的实际间距。
标定板的方格尺寸为 1 mm×1 mm,精度 1 μm,拍摄图像如图 3 所示,棋盘格图像中一个方格的图像经过亚像素算法计算得到的尺寸为 608. 45 pixel×608. 02pixel,镜头焦距 50 mm,通过增加增距环,像距大约 150mm,对准物距大约 80 mm 左右,所以像面上两个像元之间横向与纵向距离对应棋盘格板位置的实际两个物理点间距,对应分别是 1. 643 μm 和 1. 645 μm。由于图像边缘定位算法的精度约为 0. 4 pixel,于是该系统的边缘定位精度在 0. 6 μm。
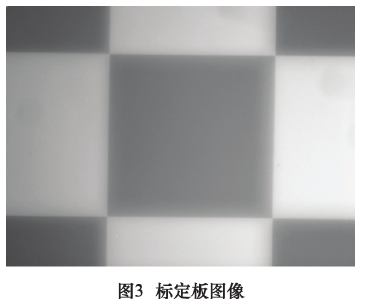
当标准心轴圆度误差极小时,测得值可以直接处理为回转误差,否则需要分离回转误差和圆度误差。由于检测是标准心轴边缘数据,其圆度误差可忽略,可以认为测得数据的圆度误差即为主轴跳动误差。
5、 实验
选取数控车床作为实验平台,使用高速 CCD 传感器采集主轴边缘图像,采集帧率 30 帧/s。以任意位置作为起始点,连续拍摄 50 幅主轴背光投影图像。由于主轴以匀速转动,所采集的图像均以固定角度转过,采集到的数据为均匀等角度分布在主轴外径上。被测量主轴直径 12 mm,设定主轴转速 50 r/min。
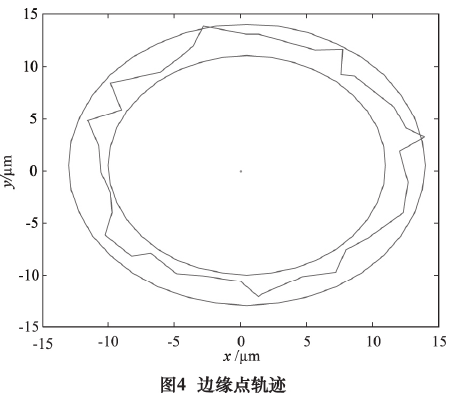
CCD 连续拍摄主轴边缘数据,将边缘位移数据叠加到基准圆上形成的测量圆数据。将 50 个主轴边缘跳动数据导入标准圆上,如图 4 所示,进行圆拟合和回转误差分离。为了更加清晰显示跳动值大小,标准圆直径并非采用 12 mm 直径,而是将跳动值按等角度添加到标准圆上。再用区域圆拟合法,其中内圆为最大外接圆,外圆为最大内接圆,用最小区域法评价圆度误差,径向跳动误差接近 3. 251 μm。
6、 结语
本文提出一种机器视觉的方法测量机床主轴径向跳动误差。利用 CCD 相机连续拍摄边缘图像,计算主轴跳动数据,经过误差分离获得径向跳动误差,由于不需要安装标准轴或者标准球,避免引入偏心误差。且通过 CCD 传感器获取主轴回转误差,能实现远距离非接触测量,可以实现在线主轴径向跳动误差测量。为了获得更准确跳动误差,可以连续采集更多主轴回转图像参与跳动误差评价。
投稿箱:
如果您有机床行业、企业相关新闻稿件发表,或进行资讯合作,欢迎联系本网编辑部, 邮箱:skjcsc@vip.sina.com
如果您有机床行业、企业相关新闻稿件发表,或进行资讯合作,欢迎联系本网编辑部, 邮箱:skjcsc@vip.sina.com