电机主轴与轴承的过盈配合设计
2020-2-8 来源: 福州泰全工业有限公司 作者:陈晔
摘要: 为确保汽车电动助力转向系统( EPS) 电机主轴与轴承过盈配合设计合理,通过理论计算对电机主轴和轴承的公差进行设计,并通过有限元软件 ABAQUS 对轴承与主轴过盈配合时内圈变形量和压入力进行分析,根据分析结果对电机主轴公差设计进行适当调整。最后制作极限样品进行 DOE 验证,样品满足使用要求。
关键词: 电机轴承; 深沟球轴承; 主轴; 内圈; 过盈配合; 有限元分析; DOE 验证
汽车电动助力转向系统( EPS) 是车辆最重要的系统之一,助力电动机是 EPS 系统的核心执行部件。电机轴承作为电动机的主要零部件,其工作状态直接影响着EPS系统的可靠性、舒适性。主轴与轴承的配合过盈量会直接影响轴承的径向游隙,进而影响轴承的载荷分布、电动机NVH( Noise,Vibration,Harshness) 性能及寿命,故有必要探讨主轴与轴承的过盈配合设计。
1 、助力电动机轴承选型
电机轴承安装位置示意图如图 1 所示。电动机最大输出扭矩 T 为 6. 5 N·m,主轴材料为 45#钢,其许用扭转应力[τ]为 120 MPa,主轴材料应满足材料强度要求,即:

式中: ds为主轴公称直径。计算可得主轴直径应满足 do≥ds= 6. 5 mm,根据经验主轴直径略大于ds较好,在此主轴公称直径取 10 mm。

图 1 轴承安装位置示意图
电机轴承最大工作转速为 5 000 r/min,最高工作温度为 120 ℃,径向载荷为 150 N,耐久试验要求为 196 h。根据设计要求进行设计计算,选择6000ZZCS12 深 沟 球 轴 承,其 主 要 参 数 为: 外 径26 mm,内径 10 mm,内圈宽度 8 mm,钢球直径4. 72 mm,轴承原始径向游隙 8 ~ 15 μm。
主轴材料为 45#钢,弹性模量为 206 GPa,泊松比为 0. 3。轴承内圈材料为轴承钢 GCr15,弹性模量为 245 GPa,泊松比为 0. 3。
2、 主轴与轴承的过盈配合量对轴承
径向游隙的影响对于深沟球轴承,内圈包含沟道,不能视为薄壁空心圆柱,内圈等效转换外径 d2i为:

式中: d2为内圈挡边直径; Kd为内圈挡边直径系数; Dw为钢球直径; A 为内圈沟道横截面面积,可由内圈尺寸计算得出; B 为内圈宽度。当主轴与轴承内圈以过盈量 Isi配合后,轴承内圈将会膨胀变形,内圈沟道直径也增大,其径向变形量( 径向游隙的变化量) Gsi为:

式中: d 为轴承内径; Ei为内圈材料弹性模量; Es为轴材料弹性模量; νi为内圈材料泊松比; νs为轴材料泊松比。在轴承压入轴后,轴承的径向游隙为

式中: Gb为原始径向游隙。由( 3) ,( 4) 式可知,主轴与轴承的过盈量将直接影响轴承的径向游隙。
3 、主轴与轴承内圈的过盈配合设计
在主轴公差设计时,为防止轴承在电动机运转过程中松脱,造成轴向窜动,需确保轴承有足够的脱拔力 F( 轴承从主轴推出力) ,通常要求 500 N <F < 2 800 N; 同时还应确定合适的轴承径向游隙,防止轴承因过盈配合变形而卡死、烧蚀。脱拔力 F 与过盈量的关系为:

式中: F 为脱拔力; B 为内圈宽度; f 为摩擦因数,取 0. 11; C1为内圈材料刚性系数,取11 000; C2为轴材料刚性系数,取 - 8 000。为满足脱拔力要求,由( 5) 式可得过盈量为0. 001 ~ 0. 02 mm。根据过盈量要求分配主轴及轴承内圈公差带,主轴尺寸为
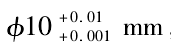
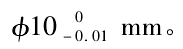
通过 ( 3 ) 式进行初步验算,设计要求轴压入轴承后轴承实际径向游隙大于 0,考虑 2 种 极限情况: 1) 主 轴直径 上限 为10. 01 mm,轴承内径下限为 9. 99 mm ( 极限情况1) ; 2) 主轴直径下限为 10. 001 mm,轴承内径上限为 10. 00 mm( 极限情况 2) 。在极限情况 1 条件下径向游隙为 1 ~ 8 μm,在极限情况 2 条件下径向游隙为 7 ~ 14 μm,两者均满足设计要求。
4 、基于 ABAQUS 的仿真分析
( 3) 式 仅 能 对 内 圈 的 变 形 量 进 行 粗 略 估算,故需采用有限元法对轴承内圈沟道的变形量及主轴压入力进行分析计算,分析时考虑 2种极限情况。
4. 1 建模
建立主轴及轴承内圈的简化模型,只模拟主轴与内圈,不考虑保持架对内圈变形的影响。将两零件设置为轴对称、可变形及壳结构,如图 2 所示。并将模型采用四面体网格进行划分,单元类型为线性缩减积分单元 CAX4I,以便精确分析主轴压入力,网格划分结果如图 3 所示。
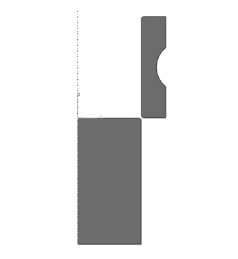
图 2 简化模型
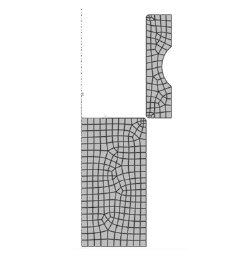
图 3 网格划分
4. 2 接触和边界条件设置
为确保仿真分析的准确度及提高效率,将主轴压入过程分为 2 步: 1) 主轴与轴承未发生接触时分析步长设置为 1; 2) 主轴与轴承发生接触时分析步长设置为 0. 04。在压入过程中材料存在非线性变形,故在分析步骤设置中允许非线性计算。
接触设置: 将主轴表面设置为主面,将轴承表面设置为从面,接触属性为面面接触,摩擦公式选择罚函数法,动摩擦因数设置为 0. 2,两者的截面属性均为各向同性。
边界条件: 1) 在主轴和轴承未接触时,设置“边界寻找”为“创建”,主轴沿轴向移动,同时禁用“压入设置”边界条件; 2) 在主轴和轴承接触时,设置主轴继续沿轴向移动,启用“压入设置”边界条件,将主轴压入轴承中。
4. 3 仿真分析
通过分析可得主轴及轴承内圈沟道压入某时刻的变形云图,如图 4 所示。提取轴承沟道节点、挡肩节点的变形,在轴承压入过程中各节点的变形曲线如图 5 所示,在极限情况 1 时变形量约为 8μm,在极限情况 2 时变形量约为 3 μm。在主轴压入过程中压入力的变化曲线如 6 所示,在极限情况 1 时最大压入力约为 2 500 N,在极限情况 2 时最大压入力约为 550 N。根据经验压入力与脱拔力几乎相等,在 2 种极限情况下轴承脱拔力均符合 500 ~ 2 800 N 要求。但在极限情况 1 时,轴承沟道处的径向变形量为 7. 9 μm,接近轴承径向游隙的下限,为确保留有安全裕量,将主轴尺寸原上限从 10. 01 mm 减小 2 μm,主轴尺寸应设计为
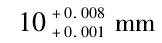
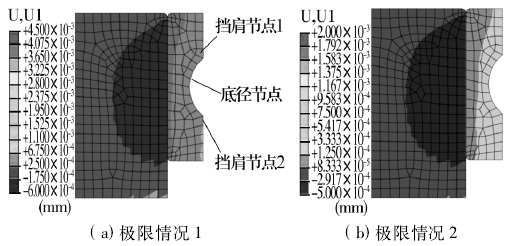
图 4 变形云图
5 、极限样品 DOE 验证
为进一步验证尺寸设计的可靠性,制作极限样品进行 DOE 验证 。将主轴直径、轴承内径以及轴承压入速度列为 3 因素,通过田口法将数据分为 9 组进行正交试验,分别对压入力进行监测,由表 1 可知该样品满足设计要求。
由于该电动机的固有频率特性,电动机 以2 000 r / min运转时,轴承直接影响的频域区间为2 500 ~ 4 000 Hz。电动机 NVH 检测( 主要指振动加速度测试) : 对电动机振动的时域信号进行快速Fourier 分析,提取 2 500 ~ 4 000 Hz 的信号均方根数据( 表 1) ,该电动机设计要求为振动加速度不大于 3. 5 m/s2,通过表 1 可知无异常振动。
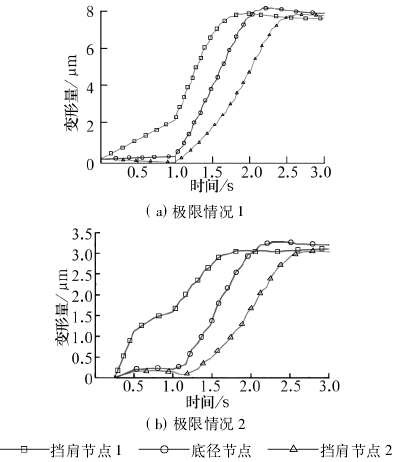
图 5 内圈沟道和挡边节点变形曲线
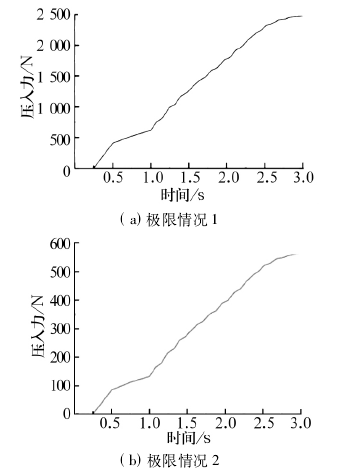
图 6 在主轴压入过程中压入力变化曲线
表 1 正交试验表
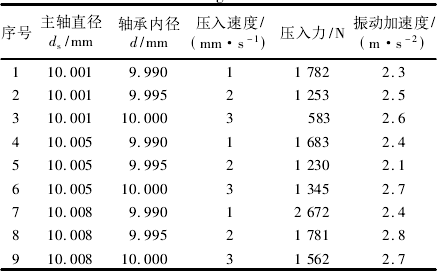
为确认电动机样品的耐久性能,将电动机以1 000 r / min运行 240 h,环境温度在 - 40 ~ 80 ℃ 循环变化,所有轴承均能正常工作。
为确保轴承无任何轻微损伤,将轴承进行拆解检查。首先检测成套轴承的音质,其次拆解确认轴承内、外圈沟道是否有挤压或擦伤痕迹,再次进行沟道真圆度检测。结果表明所有轴承均无损伤现象。
6 、结束语
介绍了某型电机主轴与轴承的过盈配合设计方法,并进行 DOE 试验验证。通过该设计方法进行过盈配合设计,经实际应用,很好地满足了用户需求。分析结果可为该类轴承的设计提供参考。
投稿箱:
如果您有机床行业、企业相关新闻稿件发表,或进行资讯合作,欢迎联系本网编辑部, 邮箱:skjcsc@vip.sina.com
如果您有机床行业、企业相关新闻稿件发表,或进行资讯合作,欢迎联系本网编辑部, 邮箱:skjcsc@vip.sina.com
更多相关信息