隔膜泵曲轴部装装配治具设计
2017-2-16 来源:中国有色(沈阳)泵业有限公司 作者:杨立业
摘要:本文重点介绍了隔膜泵曲轴部装装配治具的结构设计要点,通过对曲轴部装治具:液压升降支撑装置、结构件的定位支撑装置、滑轮平衡装置的结构优化设计,为高质、高效、高安全性的曲轴部装提供了技术保障,满足了快节奏高效率的曲轴部装需要,是极具使用价值和推广价值的一种曲轴部装装配治具。
关键词:曲轴;隔膜泵;部装;治具;装置
1.概述
隔膜泵是当今世界高腐蚀、高浓度、高压力、高温度固- 液两相介质长距离管道化输送的关键备,广泛应用于大型石化和煤化工等领域。隔膜泵主体由:传动系统、动力端、液力端、液压辅助系统、电气控制系统等部分组成,其中动力端是隔膜泵的重要组成部分,它由动力端箱体、偏心曲轴、连杆、轴承、十字头及导板、介杆等组成一个小的曲轴部装,是隔膜泵整体结构中的一个重要的部装传动结构。工作原理为:传动系统的电动机通过传动系统带动小齿轮、大齿轮、曲拐总成、连杆、十字头,使旋转运动转变为直线运动,带动活塞进行往复运动;曲轴的作用是把动力传动系统提供的旋转运动转化为直线往复运动。
偏心曲轴部装结构做为动力端的重要传动部件之一,承担着隔膜泵整个转动的最大负荷和全部传动功率的转化,承受着来致不同偏心曲轴、不同曲轴对应装配的连杆、介杆等强度、方向不断变化的弯矩、扭矩及长时间高速运转的联动作用,因此,曲轴各部件装配精度及装配质量的好坏,直接影响着曲轴部装运转联动作用发挥的效果,直接影响着设备的使用寿命。
以往曲轴部装采用V 型托辊支撑横装方法,将曲轴横放在V 型托辊上,用吊车将曲轴前端吊起,将三连杆套入曲轴上,虽然连杆可以平行装入,但是需要利用V 型铁支撑曲轴,每装入一个连杆转动120° ,连杆受自身重力影响,装配后三个连杆在不同角度与地面接触,加之由于曲轴重量大,与V 型托辊接触时连杆没转120° ,需要克服很大的摩擦力,也就是说,无法手动转动,只能通过天车的拉力才可以完成曲轴三个互成120°连杆的装配。这样,装配的效率大大下降了,而且由于摩擦力的作用导致曲轴的加工表面有划痕,严重的影响产品质量。图1 为采用V 型托辊进行曲轴部装的结构示意图:
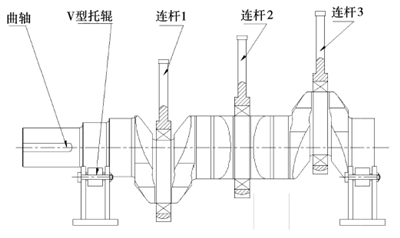
图1 采用V 型托辊进行曲轴部装的结构示意图
目前泵业公司加工的隔膜泵曲轴多为三拐曲轴,由于隔膜泵三拐曲轴长达(3 000 ~ 5 000) mm ,重量重达10 余吨,且有三个偏心,竖直安装时由于重心分布不均,极易导致倾斜偏移,而曲轴部装相关件:连杆(三个,各成120°) 、半套、轴承等其相互配合及装配精度要求很高,受场地条件限制,这种曲轴与之装配件间的调试困难,装配精度和工作效率极低,如何设计专用装配治具,提高曲轴部装装配质量、装配效率,是解决曲轴部装瓶颈问题的关键。
2.曲轴部装装配治具关键技术
2.1液压升降支撑装置的设计
图2 为液压升降装置结构示意图。
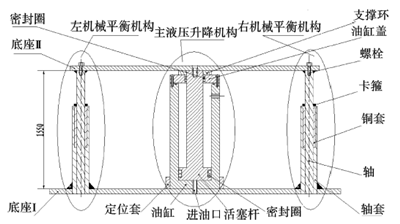
图2 液压升降装置结构示意图
它主要由底座Ⅰ 、底座Ⅱ 、主液压升降机构、左右机械平衡机构组成,主液压升降机构它主要由定位套、油缸、活塞杆、油缸盖、密封圈等组成,采用形式为普通液压升降油缸,液压油通过底座Ⅰ 的进油口进入油缸,在压力的作用下,活塞杆被顶起向上运动,同时带动整个液压升降支撑装置举升,当达到需要高度后,利用液压站的自锁功能,油缸停留固定在需要位置;降落时,利用缸体本身的进油口,将液压油泄压,活塞杆开始降落,直至缸体底部,从而实现了液压举升及降落的整个过程。
由于在举升及降落的过程中,定位安装套及曲轴重量及直径过大,考虑到曲轴部装时间过长,液压升降装置的自动泄压问题,同时为保证曲轴举升及降落过程的平稳性,避免因左右倾斜导致装配质量及安全性问题,设计开发了左、右机械平衡机构,他代替了以往没有平衡支撑机构或采用左右单缸液压升降机构的设计模式,通过机械锁紧的平衡机构的设计,降低了设计成本及繁琐的液压系统,而且通过液压、机械双锁紧的方式,实现升降平面的平稳,避免了两侧不平衡现象的发生及曲轴升降过程的倾斜,确保了新型液压升降装置升降过程的平稳。
该液压升降支撑装置主要由轴套、轴、铜套、卡箍等组成,结构形式为:将机械锁紧平衡机构分别固定在底座两侧,通过焊接将其与底座形成一体,轴套与轴之间采用间隙配合的方式实现轴的上下自由移动,为避免轴与轴套间的刚性摩擦及相对稳定,在轴与轴套之间镶嵌了定位及减缓摩擦及平衡作用的铜套,同时设计了专用卡箍,当主液压升降机构升降到装配需要位置及高度时,利用卡箍的锁紧功能,将轴卡紧在固定位置高度,实现了液压、机械双锁紧;该左右机械锁紧机构,结构简单,操作方便使用灵活,现应用在曲轴装配中,使用效果很好。
2.2结构件的定位支撑装置设计
图3 为定位支撑装置结构示意图:
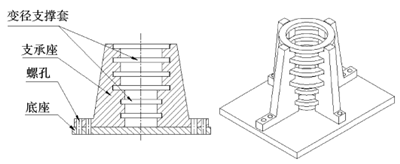
图3 定位支撑装置结构示意图
定位变径支撑装置主要由:底座、支承座、变径支撑套等部分组成,采用新型结构件的定位支撑装置:将定位支撑套设计成与三拐曲轴轴颈匹配的变径直径,放置在支承座上,支承座通过高强度螺栓与底座固定,当被加工曲轴轴径发生变化时,只需要调整支承座位置,将不同直径的支撑套放置在支承座上,即可实现轴径的变径功能,定位更加准确稳定,减少安装调试过程中,由于稳定性差而导致的曲轴装配精度低等问题;既便于安装又节省材料,提高了曲轴装配的稳定性、支撑强度及定位精度。
2.3滑轮平衡装置的设计
图4 为滑轮平衡装置结构示意图。
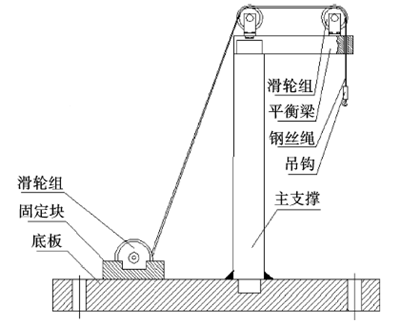
图4 滑轮平衡装置结构示意图
滑轮平衡装置主要由:底板、固定块、滑轮组、主支撑、平衡梁、钢丝绳、吊钩等部件组成,以往曲轴部装时无论是竖装还是横装,连杆的装配都需要借助装配场地的吊车进行三连杆不同部位,彼此相互位置120°的装配,由于连杆自身重量因素,在装配时三连杆的平衡定位相当困难,而且由于天车受人工控制因素影响,很难准确定位三连杆的准确装配平衡位置,装配精度差,耗费时间长,装配效率低,人为调动天车移动连杆时,安全隐患极大。采用自行设计的滑轮平衡装置后,有效解决了上述问题,为曲轴部装时各装配件的装配质量提供了质量保障,提高了生产效率。
工作原理:首先将底板通过高强度螺栓与地面固定,形成稳定可靠的地基,然后将主支撑竖直插入底座中,利用地板预留的定位孔将主支撑竖起,为确保其稳定性,采用焊接的方式将底板与主支撑焊接稳固,平衡梁与主支撑通过定位孔及把和螺栓稳定连接,滑轮组安放在地板及平衡梁上,根据曲轴部装时三连杆高度要求位置,通过滑轮控制钢丝绳、吊钩的升降来准确定位连杆的位置,当第一个连杆装配结束后,再进行第二、第三连杆的装配。
3.结语
(1) 本曲轴部装装配治具设计新颖,结构简单实用,通过滑轮平衡装置的设计,实现了曲轴部装时相关部件位置、高度的准确;
(2) 通过设计液压升降装置,实现了曲轴的平稳升降,保障了曲轴装配部件的地面装配,提高了装配质量,提高了装配效率,确保了装配才安全性;
(3) 采用结构件定位支撑套,实现了曲轴装配的精准定位,同时由于系列化定位套的使用,降低了加工成本,实现了高效、快捷的现代化装配。
投稿箱:
如果您有机床行业、企业相关新闻稿件发表,或进行资讯合作,欢迎联系本网编辑部, 邮箱:skjcsc@vip.sina.com
如果您有机床行业、企业相关新闻稿件发表,或进行资讯合作,欢迎联系本网编辑部, 邮箱:skjcsc@vip.sina.com