锻压机床系统设计优化路径
2018-6-14 来源:中铁十八局机械厂 作者:张唐善
摘要:利用遗传算法对锻压机床系统进行优化设计,在该方法基础上开发一种多目标优化的设计平台,运用 Pro/E 的建模和分析能力,既能够保障模型的精确性,又能够保障分析结果的准确性,实现多参数和目标的优化,进而提高锻压机床系统的设计效率。
关键词:锻压机床;系统设计;遗传算法;多目标优化 DOI:10.16621/j.cnki.issn1001-0599.2017.03.26
0、 前言
锻压机床作为汽车制造和交通运输行业等重要领域的基础装备,对其系统进行优化设计能够提高运行的效率,优化性能,进而为企业的维修节省费用。结构优化的主要内容包括尺寸、拓扑和形状等的优化,其目的都是在于确定最优的设计方案,提高锻压机床的运行效率。机床结构的优化主要包括对其整体结构的优化以及对其尺寸和零部件的优化,进而提高锻压机床整体的运行效率。这些优化都是对锻压机床结构域的静态优化和改善,能够提高锻压机床在运动状态中的稳定性能,进而达到节省材料的作用。本研究主要是运用遗传算法,结合上述的优化设计方法,以优化全局的思路对锻压机床的关键部件以及结构进行优化设计,设定锻压机床在开关状态下的目标函数,以达到稳定的性能,同时运用遗传算法进行多目标的优化设计,进而获取锻压机床最优的结构参数,减少锻压机床的机身质量,提升机床的性能和运行效率。
1 、多目标优化设计平台的结构和优化流程
近年来随着 CAD/CAE 技术的快速发展,锻压机床优化设计在 CAD/CAE 软件中应用的范围逐渐的广泛,能够将机床系统进行分析计算以达到最优的设计效果。有限元静态分析主要针对锻压机床的机身部件的硬度以及强度进行分析,达到最优的结构和质量,进而降低成本,达到较高的经济效益。Pro/E,UG 等实体模型软件能够将机床的实体模型建立起来并通过 CAE 进行分析,为结构的优化设计提供指导的方向,但也有自身缺点,不能实现多参数的协同优化。MATLAB 等数字分析软件能够实现多个参与情况下模型之间的协同优化,但缺少对模型实体的分析,优化的结果不精确。利用 Pro/E 软件的二次开发功能,结合数字分析软件 MATLAB 的扩展功能,集成一个多目标的优化设计平台,对锻压机床系统进行优化设计,对锻压机床的实体模型进行有限元分析,并结合遗传算法实现多目标参数的优化。
1.1 平台结构
多目标优化设计平台结构见图1,实体模型库、调度管理系统、分析计算系统以及参数优化系统 4 个主系统构成了该平台的主要系统,每一个系统有着自身独特的优点和性能。实体模型库系统主要是运用 Pro/E 软件实现对零件的三维建模,实现装配模型的功能,进而建立 SQL Server 数据库,构建出的锻压机床模型数据库完善且精确。分析计算系统主要是是利用 Pro/Mechanical 平台,优化实体模型的参数和结构,加载计算零件和组织的参数,计算出各种应力和应变的计算结果。参数优化系统是在 MATLAB 软件平台下对各种参数进行分析,利用调度管理系统获得分析和计算的结果,在目标函数的引导下对分析和计算的结果进行多次的处理,优化参数。调度管理系统主要是负责管理其他 3 个系统的管理,也是该平台的核心系统,能够将模型库输入到分析计算系统中,然后将分析计算系统中的结果输入到参数优化系统中,获取优化的结果能够对模型库的参数进行修改,分析计算后获得最优的参数。
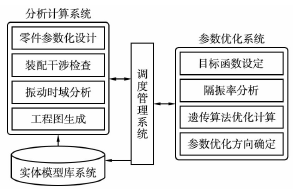
图 1 多目标优化设计平台的结构示意图
1.2 平台优化流程(图 2)
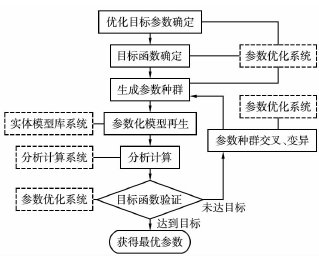
图 2 多目标优化设计平台优化流程的性能和运行效率
多目标优化平台的 4 个主系统分工合作,共同优化锻压机床的各个参数。优化平台能够根据分析计算的结果对模型库参数进行设计,根据锻压机床的工作特性以及预先确定的最优目标函数,设计出锻压机床各个构建的最优参数,通过调度管理系统实现对模型库参数的改进载入到分析计算系统中得到结果,获得最优的目标函数,针对结构进行参数的处理和筛选,再次进行迭代计算,获取最优的参数。
2、 系统设计
2.1 模型库系统和分析计算系统设计
模型库系统的主要功能是对锻压机床的零件以及组间模型进行存储,生成文件系统,为外部的调度管理系统提供零件和部件修改的参数,并且能够快速的将组间的模型参数结果计算出来。锻压机床模型作为一种三维实体模型,是在 Pro/E 条件下建立的,能够分类存储锻压机床各个零件的参数,模型库中包含了锻压机床模型的名称、结构信息以及位置等,能够通过调度管理系统查看相关的模型。
分析系统的是利用 Pro/E 软件中的 Pro/Mechanical 平台建立的,主要功能是对三维实体模型进行有限元分析。分析系统能够根据调度系统中的模型库,给锻压机床设计预先的载荷、约束等,将零件的应变力和局部变形结果计算出来,并且将计算的结构传送到调度系统中。
2.2 调度管理系统设计
调度管理系统主要的功能是帮助其他的几个子系统访问模型库,修改模型库的参数,管理机床的分析数据,得到计算的结果,并将计算的结果进行传输,获得最佳的优化方案。调度管理系统主要是运用了 Pro/E 软件的二次开发功能,能够实现对数据库的调度和管理,以编程的方式实现特定的功能。在调度管理系统的优化平台设计中利用 C++的 MFC 类库,利用二次开发的功能对系统进行优化设计。调度管理系统能够将模型的 ID 存储在模型库中的实体模型中,然后按照模型的参数和尺寸进行重新的配置,检查装置是否符合约束的条件。如果条件满足,就按照最优的设置参数进行模型的设计,建立优化后的模型,利用软件的分析功能实现模型的驱动。调度管理系统的优化流程见图 3。调度管理系统能够优化设计的参数主要是在软件平台上开发一个动态的链接库。参数的优化能够通过参数种群进行分析和筛选,获得的计算结构反馈给参数优化系统,进而设计目标函数,在遗传算法的基础下进行参数的优化,最终得到优化的参数。
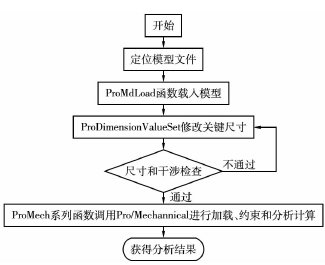
图 3 调度管理流程
3 、基于遗传算法的参数优化算法
3.1 变量设计
本系统变量的设计根据不同型号的锻压机床优化的目标不同,经过分析和判断,将锻压机床的上下横梁的纵横向板厚以及板间距作为变量。
3.2 目标函数
锻压机床设计的主要目的在于提高锻压机床的准确度和稳定性能,并且将锻压机床的材料质量缩小到最低,在应力范围内设计锻压机床的材料,进而降低锻压机床的成本,达到稳定的性能。因此本文的目标函数主要作用在锻压机床的上下横梁的纵横弯曲度以及最大应力和机身的质量上。本系统锻压机床的精确度和稳定性主要依靠机床上横梁的纵横向弯曲度来确定,弯曲度越大,说明锻压机床的精确度越高,抗振性能越高。说明该参数下锻压机床较为稳定。在设置优化目标函数时也将这两个变量作为设计的依据。为了提高锻压机床的运行效率和生产成本,在保障其精确度的条件下,优化目标函数将锻压机床的机身作为一个考虑的因素。另外应力集中也是优化目标函数需要重点考虑的一个问题。相关实验表明,锻压机床集中应力越大,其磨损度就越严重。因此通过以上的分析可以得到以下的目标函数。
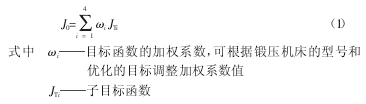
3.3 遗传算法
本系统的编码采用自定义函数,变量的数目为 4 个,变量离散值个数为 mi个,设计变量为 x。设置遗传算子,采用 MATLAB进行,并将其作为比例函数的 Rank,参数的选择采用随机分布的方式,参数的再生利用遗传算法的缺省进行,约束的处理采用惩罚函数法,每一个个体的适应度上添加一个惩罚因子,这样能够满足个体的适应度,也就是:
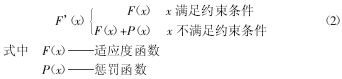
4、 实例计算
本文以某型号的锻压机床为例对其系统进行优化设计。表1 和表 2 为优化前后锻压机床各参数的变化情况和技术指标对比。

表 1 优化前后参数的变化

表 2 优化前后技术指标的变化
锻压机床经过多目标优化后,纵向变形差缩小到 0.28mm,横向变形差缩小到 0.38 mm,最大应力减小到 196 MPa,机身的总重量减小到 255 880 kg,达到了多个目标的优化,同时能够减轻机身的质量,使得机床的结构更加的稳定,性能提高,应力分配在数值范围内,提高了锻压机床的运行效率。说明多目优化的遗传算法能够将锻压机床系统设计到最佳的性能。
5 、结语
通过对锻压机床进行优化设计,设计出一个保障锻压机床设计性能的良好平台,在该平台上进行调度管理系统、分析计算系统和参数优化系统的设计,实现对锻压机床机身结构以及参数的协同管理和优化计算,利用有限元分析和多目标的遗传算法,优化锻压机床纵横向的变形差、最大应力以及机身的质量,实现了最优的目标。
投稿箱:
如果您有机床行业、企业相关新闻稿件发表,或进行资讯合作,欢迎联系本网编辑部, 邮箱:skjcsc@vip.sina.com
如果您有机床行业、企业相关新闻稿件发表,或进行资讯合作,欢迎联系本网编辑部, 邮箱:skjcsc@vip.sina.com