冷镦机床身的多约束拓扑优化与再设计
2017-7-5 来源:湖北理工学院 作者:何彬 ,李响
摘要:常规设计下的冷镦机床身存在较大的减重空间。 针对冷镦机床身的结构和工作特点,以床身整体应变能最小为目标函数,以体积、最大应力、最大位移和固有频率为约束,建立多约束拓扑优化模型;并以某型号冷镦机床身为例,运用Abaqus6.11 实现该床身多约束拓扑优化过程 ;在拓扑优化的基础上 ,对床身进行再设计 ,并着重围绕再设计中矩形孔过渡圆角半径的不同取值展开分析和比较,最终确定较优的设计方案。 再设计结果显示,在较好满足床身各项静态和动态性能指标的前提下,床身体积减少可达 9.6%以上。
关键词:轻量化;拓扑优化;冷镦机床身;再设计;Abaqus
锻压机床是机床中钢材消耗量最大的一类机床,实现锻压机床的轻量化是机床行业绿色设计与制造的战略要求[1-2]。冷镦机属于典型的锻压机床,是应用冷镦工艺 生产各类标准件、紧固件、异形件的工作母机。 冷镦机床身质量占到整机质量的一半以上, 在传统设计中, 床身的结构参数大多来源于设计人员的经验或与类似产品的类比,所进行的设计计算仅起到校核作用,设计安全系数大,使得床身存在较大的减重空间[1,3-4]。拓扑优化[5-6]是实现轻量化设计的最有效方法之一。
拓扑优化是将结构的最优拓扑问题转化为在给定的设计区域内寻求材料的最优分布问题。 运用拓扑优化方法实现冷镦机床身的轻量化设计, 须综合考虑床身的整体力学性能,建立有效的拓扑优化模型,选取合理的再设计方案,才能达到理想的减重和再设计效果。
1.冷镦机床身的多约束拓扑优化模型
在锻压机床床身拓扑优化设计中, 变密度法是目前用得最普遍的一种拓扑优化方法, 其把单元相对密度与材料弹性模量之间的对应关系以密度函数的形式表达出来,通过单元删减来寻求材料最优分布问题[7-8]。采用变密度法进行冷镦机床身的拓扑优化设计时,须遵循以下原则:
(1)冷镦机床身为三维实体结构,三维拓扑优化问题迭代过程复杂,容易产生奇异结构[9]。 如果采用多目标的优化函数[10](如同时以应变能和特征频率为优化目标),不仅增加了优化过程求解的难度,而且还由于权重的引入, 不同程度弱化了应变能或特征频率的优化效用,和单目标的优化结果相比,应变能或特征频率无法达到整体的最优。因此,冷镦机床身的拓扑优化可采用单目标的优化函数。
(2)床身静态、动态特性直接影响冷镦机工作时的镦断性能,而反映静、动态特性的一些重要性能指(如床身最大应力、变形量及特征频率等)很难通过目标函数来保证,只能采用等式或不等式约束加以限制。 同时,如果优化函数中含有相应的约束变量, 对其取值范围加以限制,则可间接约束目标函数变量的取值,加速目标函数的收敛,提高求解效率,使最终的优化结果更加可靠。 因而,冷镦机拓扑优化宜采用多约束的优化模型[10-11]。
根据上述原则, 针对冷镦机床身可建立多约束作用下的单目标优化模型,使床身在满足体积、应力、应变量等约束要求的前提下,能获得理想的优化结果。多约束拓扑优化模型为:
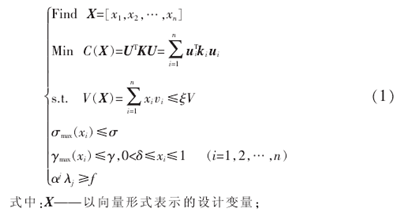
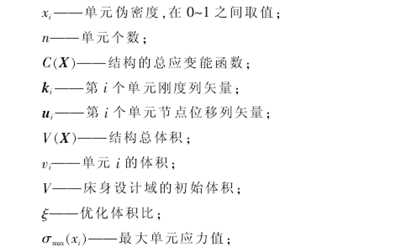
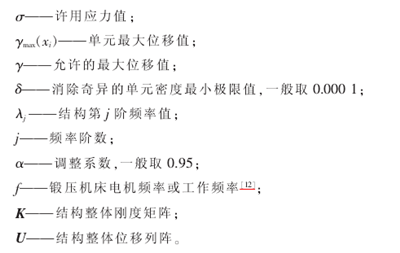
以总应变能 C(X)作为单一的优化目标,主要考虑到床身工作时受到较大的镦断冲击力, 必须优先实现整体刚性最优。运用敏度分析[13]方法,对目标函数进行求导,可得到:
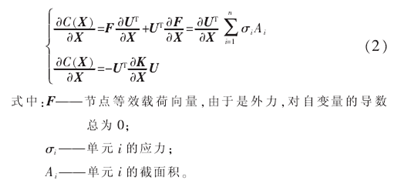
冷镦机床身通常为均匀实体材料, 在有限元分析时,当单元网格的类型和数量确定后,其截面积可视为定值。 因此,从式(2)可知,应力和位移对应变能的变化有直接影响,如果应力和位移为密度的函数,对应力和位移变量的取值范围加以限制, 则可间接约束自变量的取值,有利于目标函数的收敛。 可见,对于冷镦机床身的拓扑优化, 以总应变能作为目标函数的单目标优化中,除了体积约束外,增加应力和位移约束是可以尝试的。
2.冷镦机床身拓扑优化的实现过程
2.1 床身初始设计及分析
以某型号冷镦机床身为例, 该冷镦机相关参数如表 1 所示,床身的初始设计如图 1 所示。从工作时的受力来看,床身左边前压板受到 410 k N 方向垂直压板向左的冲击力, 右边两个轴承孔的右半部分别受到205k N 方向垂直压板向右的载荷[10]。
表 1 冷镦机床身主要结构、性能和关联参数

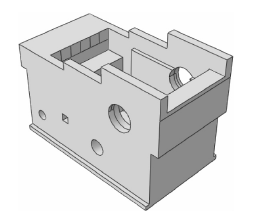
图 1冷镦机床身初始设计
在 Abaqus6.11 中, 对初始设计的床身进行有限元分析,首先划分网格,单元类型采用四面体,共生成19668 个单元。 再分别进行静态和模态分析,其中静态分析结果的应力和位移云图如图 2 和图 3 所示。 最大应力和最大位移均发生在床身右侧轴承孔受力方向上,其大小分别为 48.89 MPa 和 0.067 99 mm, 满足强度和加工精度要求。 模态分析结果显示的前 6 阶固有频率如表 2所示。 床身材料 HT250 的抗拉强度为 250 MPa,根据经验可取安全系数为 2,则床身的许用应力 125 MPa。由于最大应力远小于床身的许用应力 125 MPa, 且床身前 6阶固有频率皆远大于该型号冷镦机的电机频率和工作响应频率。 因此,静态和模态分析结果显示床身初始设计过于保守,存在较大的拓扑优化空间。
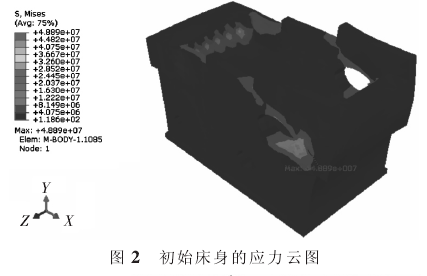
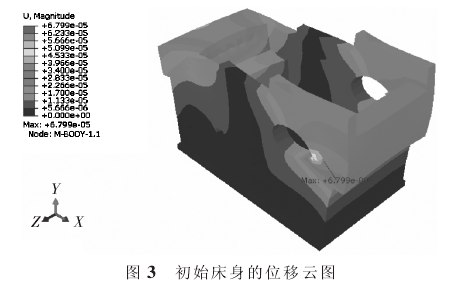
表 2 冷镦机初始设计床身的前 6 阶固有频率

2.2 冷镦机床身的拓扑优化
按照所建立的多约束拓扑优化模型, 分别对目标函数、体积约束、应力约束、位移约束和固有频率约束进行设置,如表 3 所示。 在 Abaqus6.11 的优化模块中,创建目标函数、设计响应(变量)、约束和优化任务,并设置对应参数。 其中,边界约束区域为床身底面,而在几何约束的设置中, 除了冻结受力区域外, 各待加工面、原有的孔洞面同样要进行约束,以保证拓扑优化过程中的材料剔除不会影响到原有的结构或工艺特征。
表 3 冷镦机床身拓扑优化的参数与约束设置
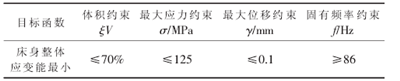
提交拓扑优化任务,经过 10 次设计循环后,目标函数趋于收敛,拓扑优化后的床身模型如图 4 所示,收敛过程如图 5 所示。从图 4 可知,材料剔除区域不存在棋盘格式,体现了优化模型、参数设置及优化过程的合理性。拓扑优化完成后,床身的整体应变能达到最小值24.03 N·m,而床身的体积则减少到原来的 69%。 而从拓扑优化后床身的应力和位移云图来看, 最大应力增加到 114.8 MPa,实际安全系数为 2.18,如图 6 所示;最大位移 0.067 86 mm,和优化前基本相等,但是承受较大变形的区域明显扩散,如图 7 所示。
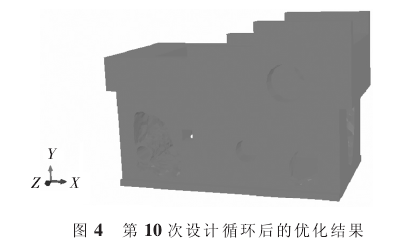
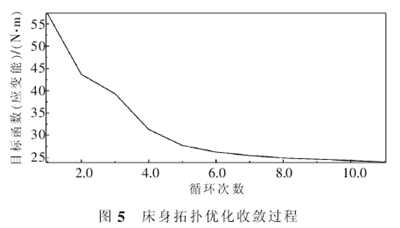
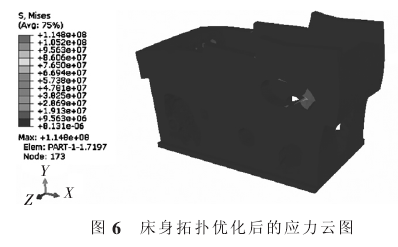
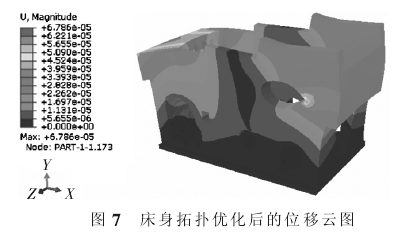
拓扑优化结果说明,由于单元的删减,减少了床身体积,也使得床身的整体刚性和优化前相比有所削弱,但在约束的作用下, 优化后的床身仍然能够满足规定的要求。同时,由于拓扑优化剔除材料所形成的孔洞形状是非规则的,不符合可制造性的原则,因此对拓扑优化后的床身进行再设计是必要的。
3.床身的再设计
3.1 冷镦机床身的拓扑优化
冷镦机床身的再设计应解决 3 个问题: 再设计区域如何选取;再设计中孔洞形状的确定;再设计孔洞中关键尺寸(如矩形孔的过渡圆角)的取值。冷镦机床身的拓扑优化是采用变密度法, 其实质是通过去除传力路径中不通过该处的结构单元[14]来剔除材料,从而寻求最优的材料分布。冷镦机床身的再设计是建立在床身的拓扑优化基础之上的, 其再设计区域应选取在拓扑优化后所形成的孔洞区域以内。 由于再设计区域包含于拓扑优化中单元去除区域, 同样属于传力路径不通过的区域, 因此再设计区域按照这种原则选取可以保证床身再设计后不影响原有应力等约束的满足性。对于再设计中孔洞形状的确定,主要根据可制造性原则,先满足铸造工艺性,通常方孔和圆孔是最常用的形状;其次,为了有效减轻床身质量,再设计孔洞的形状应最大限度地利用好拓扑优化后材料剔除的区域。 关于再设计孔洞中关键尺寸的取值,可以根据多个尺寸方案的有限元分析结果,选取综合性能参数较优的方案。
3.2 床身的再设计过程
按照床身再设计的第 1 和第 2 条原则,在拓扑优化后床身模型的基础上进行二次设计,如图 8 所示。 根据同一铸件圆角半径大小应尽量相同或接近的工艺要求,在图 8 中,再设计的矩形孔洞圆角半径都取 5 mm。 对再设计床身进行静态和模态分析,静态分析结果如图 9 和图 10 所示, 模态分析结果的前 6 阶固有频率如表 所4 所示。 相比拓扑优化后的床身,最大应力和最大位移都有不同程度减少,前 6 阶固有频率虽然比拓扑优化前的床身有所降低,但仍然远大于电机频率和工作响应频率。
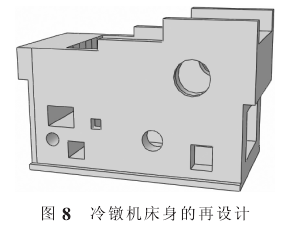
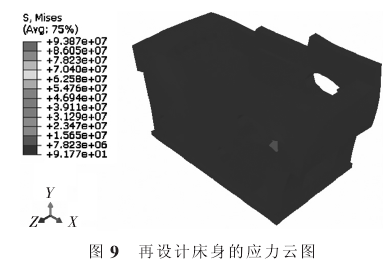
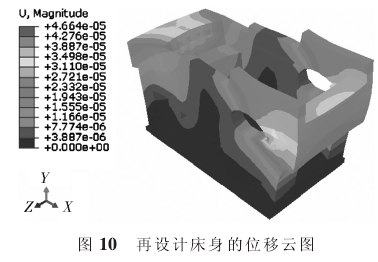
表 4 再设计冷镦机床身的前 6 阶固有频率

铸造孔的圆角半径对应力集中等床身力学性能有直接影响,为了确定力学性能较优的圆角半径,选取从10~50 mm 公差为 5 mm 的一组数据,分别进行有限元分析, 其静态和动态分析结果及体积减少情况如表 5所示。从表 5 可以看出,该尺寸范围内的圆角半径对床身前 6 阶固有频率影响不明显;随着圆角半径的增大,体积减少量有所下降;对床身的最大位移略有影响,对最大应力的影响显著,在圆角半径为 45 mm 和 30 mm时,最大应力值较小。 因此,如果优先考虑力学性能的因素,可选取 45 mm 的圆角半径;如果更多从减重的角度考虑,则选择 30 mm 的圆角半径。
3.3 结果分析
从再设计床身的有限元分析可知,与床身初始设计和拓扑优化结果相比,在拓扑优化后材料剔除区域内设计的规则矩形孔洞可以改善床身位移幅值,说明最大位移所在单元的应力由于再设计而得到了部分抵消;而从不同圆角半径的数据分析可知,矩形孔洞过渡圆角半径尺寸对床身最大位移和前 6 阶固有频率影响较小,而对床身最大应力影响较大,但后者并不随矩形孔洞过渡圆角半径的增大而减小,说明对于冷镦机床身这样的三维实体结构, 其关键尺寸与应力之间存在较为复杂的关系,须通过具体数据的验证才能合理取值。
表 5不同圆角半径动静特性与体积减少量比较
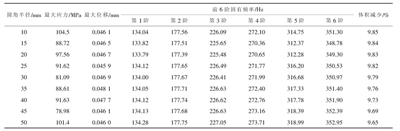
4.结论
针对冷镦机床身的结构和工作特点, 建立了床身的多约束拓扑优化模型, 并实现了床身的拓扑优化和再设计。再设计结果表明,再设计中孔洞形状和尺寸对床身的综合力学性能有不同程度影响, 通过不同再设计方案的择优, 可保证床身各项性能指标得到较好满足的前提下,使床身的整体质量明显减轻。结合文中研究,以下两个方面的工作须做进一步的深入:
(1)如何建立矩形孔过渡圆角半径与床身最大应力等力学性能指标之间的关系模型, 从而为床身再设计提供理论依据和参照。
(2)由于拓扑优化剔除材料后体积减少显著 ,但所形成的孔洞形状是非规则的, 因此拓扑优化过程如何同形状优化结合起来,以保证孔洞形状的合理性,以提高冷镦机床身的轻量化实施效果。
投稿箱:
如果您有机床行业、企业相关新闻稿件发表,或进行资讯合作,欢迎联系本网编辑部, 邮箱:skjcsc@vip.sina.com
如果您有机床行业、企业相关新闻稿件发表,或进行资讯合作,欢迎联系本网编辑部, 邮箱:skjcsc@vip.sina.com
更多相关信息