【数控机床应用】 双线蜗杆在卧式车床的切削和加工技巧
2020-12-18 来源:中地装张家口探矿机械有限公司 作者:钱宝国
摘要:为解决双线蜗杆在普通卧式车床加工难的实际情况,本文针对蜗杆的导程大、齿形深、分线难等特点,从刀具的选用、刃磨、机床的调整、加工技巧及测量方法等方面做了全面阐述,制定了合理有效的加工方案,并取得了良好的效果。
数控机床的应用大大提高了生产效率,降低了工人的劳动强度,但是在单件加工和配件生产时,卧式车床又以其快捷、方便及可控性强而备受青睐。因此数控机床始终无法完全取代卧式机床。本文将重点介绍双线蜗杆在卧式车床上切削的加工技巧。蜗杆蜗轮传动常用于减速运动的机械传动机构中,蜗杆蜗轮的两轴相互交叉垂直,蜗杆转动带动蜗轮转动,因此蜗杆各部分尺寸的精度等级要求严格,齿形符合图样,表面粗糙度值小,径向圆跳动更不得大于公差范围。且双线蜗杆要求其螺旋线沿轴向等距分布来增加蜗杆的耐磨性和使用寿命,所以双线蜗杆的分线精度尤为重要。由于蜗杆的螺纹升角较大,这在生产中受到了很大的限制,笔者通过多年生产一线的实践工作,得出了一些有利于切削的加工技巧。
1. 车削蜗杆刀具的刃磨和装夹
在车削中 ,由于蜗杆的螺距大、齿型深及切削面积大,因此车削蜗杆刀具必须刃磨合理,装夹正确。蜗杆车刀一般选用切削刃锋利、韧性好且耐冲击的高速钢材料车刀,在刃磨时一定要保证车刀的刀尖角度及两侧刀刃光洁平整。双线蜗杆分轴向直廓蜗杆和法向直廓蜗杆,蜗杆的粗车刀(见图1)径向后角一般为 6°~ 8°,纵向前角为8°~10°,刀头宽度应小于齿根槽宽,两切削刃之间的夹角略小于两倍齿形角,这样有利于增加车刀的强度,使排屑通畅。蜗杆精车刀左右切削刃的夹角必须等于两倍齿形角。车削轴向直廓蜗杆的精车刀(见图2)其顺走刀方向的后角为3°~5°,相应加上螺纹升角,其背走刀方向后角为3°~5°, 必须相应减去螺纹升角,纵向前角为0°,这样可获得较高的齿形精度和较低的表面粗糙度值。
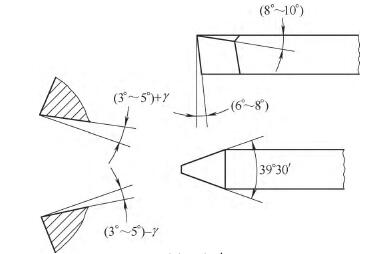
图1 粗车刀
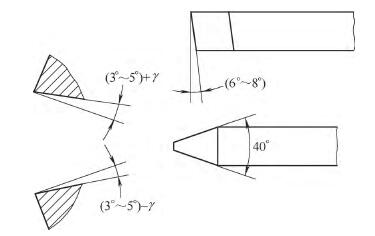
图2 精车刀
装夹刀具采用水平装刀法,通常采用万能角度器找正车刀刀尖角位置,如出现偏差,可转动刀架或重新装夹,来调整刀尖角位置。车削法向直廓蜗杆的精车刀两侧后角相等,均为3°~5°,纵向前角为0°,这样加工精度最高。但装刀时必须用可转动式刀杆装夹车刀,装夹刀具采用垂直装刀法,把可转动式刀杆的零位刻度线对准基线,然后装正车刀刀尖角,使其高于车床主轴轴线0.5mm左右并坚固,再根据螺纹升角的大小来确定车刀转过的角度。
2. 工件的装夹和机床的调整
因蜗杆的齿型较深、导程较大,这就要求在装夹工件时蜗杆与卡盘之间的距离应合理选择,如过小,车削时车刀容易碰到卡盘,过大会减弱工件的刚性,造成切削时的“扎刀”或“让刀”等不利于加工的因素。卡盘卡量不要过长,卡位要放在外径较大的部位以加大卡盘对工件的夹紧力。
粗车采用夹一端、顶一端,目的是为了增加工件的刚性,使其能够承受较大的切削力矩。精车采用两顶并用死顶尖来保证工件的基准统一原则,最大限度地一次装夹加工出多个外圆和端面。在车削蜗杆前,为保证加工精度要先调整好主轴和丝杠的轴向窜动。调整主轴轴向窜动的方法是把短检验棒插入主轴锥孔,检验棒中心孔内放一钢珠,将百分表架固定在滑板上,百分表测量头压在钢球上,主轴缓慢转动,测得百分表读数的最大差值就是主轴的轴向窜动误差,如图3所示。调整丝杠轴向窜动的方法是将钢珠放入丝杠中心孔内,让开合螺母在丝杠中段处闭合,旋转丝杠,百分表读数的最大差值即为丝杠的轴向窜动误差,如图4所示。调整所有滑板镶条的松紧度,增大移动时的摩擦力,减小滑板窜动的可能性,防止切削时出现“扎刀”现象。
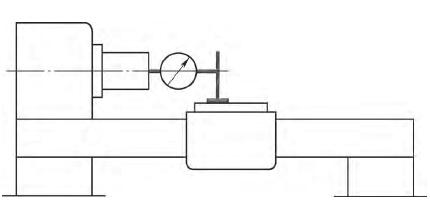
图3 检测主轴的轴向窜动
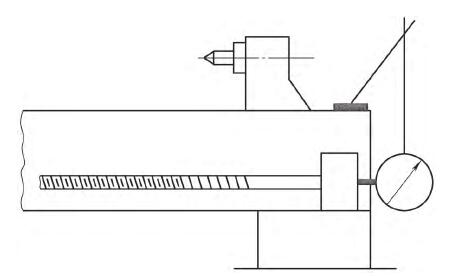
图4 检测丝杠的轴向窜动
为保证分线的精度 , 必须校对小滑板的有效行程对床身导轨的平行度,其方法是利用已车好的工件外圆(其锥度应在0.01m m/100m m范围以内),将百分表安装在刀架上,使百分表测量头在水平方向与工件外圆接触,手摇小滑板观察百分表针,使其不超过0.01mm/100mm,则机床调整完成。
3. 蜗杆的切削方法
车削时应采用开正反车切削,粗车时为提高生产效率,要选用大的切削用量和切削深度,减少停车测量的次数,应在蜗杆表面划出4条螺旋线,如图5所示。首先将小滑板刻度调整零位,用三角螺纹车刀在蜗杆部位表面上车出一条很浅的螺旋线,用卡尺校验其导程,正确后再将小滑板向前位移一个齿顶宽的距离,在蜗杆部位表面车出第二条很浅的螺旋线。再向前移动小滑板使其位移一个螺距减去齿顶宽的距离,车出第三条螺旋线,再向前移动小滑板位移一个齿顶宽的距离,车出第4条螺旋线,最后是以小滑板零位向前移动两个螺距,校验刀尖是否与第一条螺旋线重合,以确定螺距和分线是否正确,如不重合说明螺距或分线不正确,找出原因并解决。确定分线正确后装夹刀具移动小滑板使蜗杆车刀至划好的螺旋槽内,开始粗车蜗杆。众所周知,在蜗杆加工中切削深度越大,切削面就越大,切削力增大,切削就越困难,极易产生打刀现象,如果采用分层左赶刀法,就能有效避免这个现象。粗车时先用直进法车削一定的深度,再左右赶刀至两边所划的螺旋线,然后再往深车削,直至加工达到深度尺寸,第一条螺旋槽粗加工完成,把车刀移至第二条所划的螺旋槽内,按加工第一条的方法加工第二条螺旋槽并留0.2~0.4mm的精车余量,则蜗杆粗车完成。精车时应采用两顶的装夹方法,将小滑板刻度调整零位,先加工第一条螺旋槽的底径达到深度后,向前赶刀切削螺旋槽的左侧面,使其表面整体切削后,记住中滑板刻度。移动小滑板加工另一条螺旋槽的底径,用直进法切削使中滑板刻度与精车第一条螺旋槽的刻度相同,然后向前移动小滑板车削左侧面,直至小滑板向前移动为一个螺距(也可在小滑板上压一块百分表,根据百分表的读数值来确定小滑板的移动量,以保证分线的精度更高),则蜗杆螺旋槽的左侧面加工完毕。然后以同样方法加工螺旋槽右侧面,这样就能清除分线或赶刀时所产生的误差。
用高速钢车刀精车蜗杆时要低速车削,由于切削深度和切削面积大,加工中极易产生“啃刀”现象,所以应仔细观察切削情况,合理选择切削用量,避免三面吃刀。控制主轴低速旋转要采用“晃车”的方法,通常也叫“抖车”,即开车瞬间就停车,利用主轴转动的惯性,但不能停住,用腕力控制离合器手柄反复开车、停车,这样可以有效地避免刀、啃刀”现象,使蜗杆的尺寸精度及表面粗糙度达到理想的效果。同时在切削中,切削液的正确选择可以减小切削变形,降低切削力,提高刀具寿命。粗加工时,为了降低切削温度,一般选用以冷却性能为主的切削液,如3%~5%的乳化液或合成切削液。精加工时,为保证表面粗糙度,提高加工精度,一般选用以润滑性能为主的切削液,如极压切削油或高浓度的极压乳化液。
4. 蜗杆的测量方法
蜗杆的测量一般用齿厚测量法,即用齿厚游标卡尺测量蜗杆中径齿厚。测量前先计算出蜗杆中径处的法向齿厚值和一齿的一个面与另一齿的相反面中径处的距离,即相邻两齿中径处的法向距离值。在半精车和精车的切削过程中要随时停车测量,根据测量结果计算出分线和齿厚的误差,通常会出现以下4种情况。
1 )第一种:测得两齿厚相同,相隔两组面的法向距离相同,这说明分线和齿厚均正确。可根据测得尺寸与计算尺寸的差值,分别车削两槽内的相同面,去掉多余量,按精车蜗杆的方法加工至中径处的法向齿厚,符合图样要求。
2 )第二种:测得两齿厚不相同,相隔两组面的法向距离相同,则说明分线正确,齿厚不正确。分别车削较厚齿的两侧面,切记去掉的多余量为两齿厚差值的一半,保证齿厚相同后,出现第一种情况,然后利用第一种方法保证最后尺寸。
3 )第三种:测得两齿厚相同而相隔两组面的法向距离不相同,说明分线偏差而齿厚正确。则车削齿厚游标卡尺测量两面尺寸值较大的两个面。切记分别车掉与另一较小尺寸差值的一半,保证相隔两组面的法向距离相等,则出现第一种情况,仍利用第一种方法车削保证最后的尺寸要求。
4 )第四种:测得两齿厚不相同且相隔两组面的法向距离也不相同,说明分线和齿厚均不正确。则车削较厚齿的一个面且这个面是测量相隔组两面距离尺寸较大时,齿厚游标卡尺卡爪所接触的那个面。在车削测量时,将会得到一组尺寸相等,即两齿厚相同或相隔两组面法向距离相同,则会出现第二种或第三种情况,此时就可以按照上面的方法进行加工,直到保证尺寸。
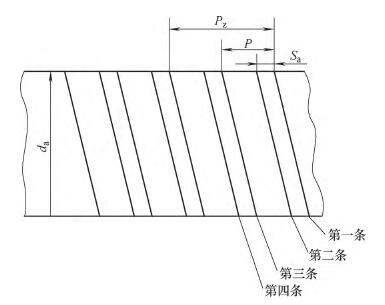
图5 蜗杆切削划线
以上几种情况是在测量法向齿厚尺寸和相隔两面之间法向距离的分线尺寸都大于或等于其图样要求尺寸完成加工要求的,如果测得的尺寸有一个尺寸小于其图样要求尺寸,则说明蜗杆已经作废,不可以再进行加工。
5. 结语
实践证明,此加工方法不仅可以用来加工双线蜗杆,改变刀具的角度和形状,也可以用来加工双线梯形螺纹。因此,生产中积累的一些小发明、小改进是达到生产目的和保证产品质量非常
有效的方法,在行业中具有极强的可选用性和推广性。
投稿箱:
如果您有机床行业、企业相关新闻稿件发表,或进行资讯合作,欢迎联系本网编辑部, 邮箱:skjcsc@vip.sina.com
如果您有机床行业、企业相关新闻稿件发表,或进行资讯合作,欢迎联系本网编辑部, 邮箱:skjcsc@vip.sina.com
更多相关信息