重型卧式车床几何精度检测与加工精度预估
2020-12-16 来源:天津中德应用技术大学机械工程学院 作者:马林旭 王丽娜
摘要: 以一台重型卧式车床为例,基于刚体运动学原理建立了机床几何误差模型,得到了各轴线几何误差源与加工误差之间的映射关系,而后采用激光干涉仪、水平仪等测量仪器获取了机床部分几何误差源的误差数据,并进而预估出机床全工作空间内的加工误差变化规律,可用于指导机床的误差补偿等工作,以提高机床的精度性能。
关键词: 重型卧式车床; 几何误差建模; 误差检测; 精度预估
重型卧式车床广泛应用于能源、石化、船舶、航天等领域,是车削各类大型回转类零件的重要工作母机,对国防军工、国民经济发展具有重要战略意义[1]。几何精度是重型卧式车床的重要性能指标之一[2],影响几何精度的因素主要包括主轴回转精度以及直线进给轴运动精度两类,而直线进给轴运动精度是影响整机几何精度的最重要因素。针对重型卧式车床几何精度检测,诸多学者开展了大量的研究工作[3-8],所采用的测量方法主要包括激光跟踪仪、激光干涉仪、自准直仪、水平仪以及步距规等,然而对于如何利用测量数据预估加工精度,并指导误差补偿以及加工工艺规划,尚未有系统性研究。本文以一台重型卧式车床为例,首先建立机床几何误差模型,并分析不同误差源对加工精度的影响规律,之后采用激光干涉仪开展误差检测实验,最后基于检测数据预估机床全工作空间内的加工误差。
1、 误差建模与分析
本文研究对象为一台 SKODA SR5-420 /16m 型号的重型卧式车床,如图 1 所示。该重型卧式车床主要由主轴箱、卡盘、刀架、尾座、床身与滑座构成,刀架进给方向为 x 向,滑座进给方向为 z 向。机床最大加工工件直径为 4 200 mm,最大切削长度为 16 m,最大加工工件质量为 250 t。为了描述运动部件刀架及滑座的运动误差对刀尖点加工误差的映射关系,建立如图 2 所示坐标系统。当刀架位于坐标零点位置时,在其所在导轨面中心点 X0处建立与导轨固定连接的坐标系 X0-xyz,并同时在刀架上与 X0点重合的 X 点建立与刀架固定连接的连体坐标系 X-xyz。这样一来,当刀架运动至坐标 x 处时,坐标系原点 X 与 X0之间的 x 方向坐标差即为 x。同理,对于滑座所在的 z 轴建立类似的坐标系 Z0-xyz 与 Z-xyz。
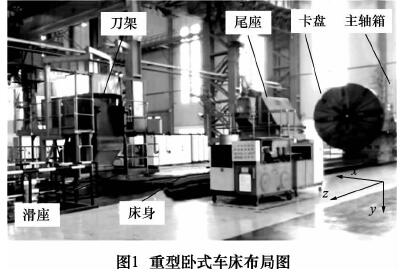
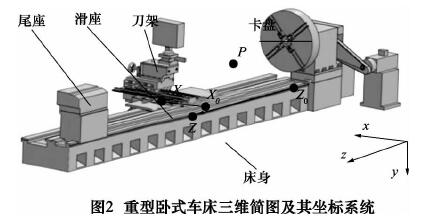
计刀尖点为点 P,利用刚体运动学基本原理,当刀架运动至坐标 x 处时,由刀架运动误差引起的刀尖点空间位置误差 Δr刀架可以表示为:
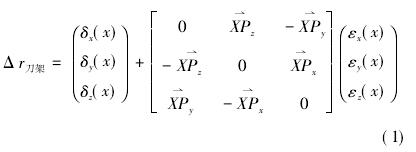
其中: δx( x) 、δy( x) 、δz( x) 与 εx( x) 、εy( x) 、εz( x) 分别表示刀架运动过程中沿 3 个坐标方向的位置误差与绕这 3 个坐标回转的转角误差,XP→表示由点 X 指向点 P的位置向量,脚标 x、y、z 表示向量XP→的 3 个分量。同理,当滑座运动至坐标 z 处时,由滑座运动误差引起的刀尖点空间位置误差 Δ r滑座可以表示为:
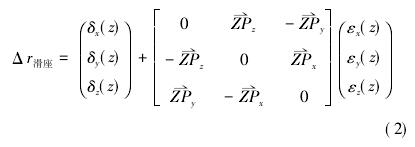
于是,同时考虑刀架与滑座的影响,刀尖点位置误差 Δr 可以表示为:
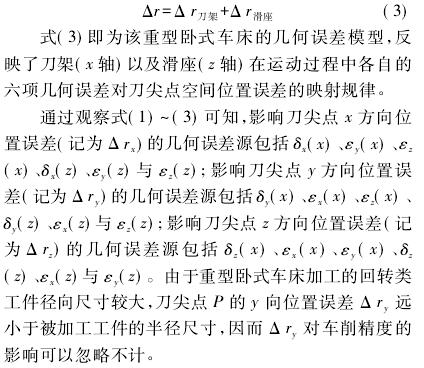
2 、几何误差检测
由上节中的分析可知,Δ ry对加工精度的影响可忽略,因而在误差检测与加工精度预测的过程中仅需重点关注与 Δ rx、Δ rz相关的几何误差源。由于对 Δ rx与 Δ rz的研究方法完全一致,本文仅针对与刀尖点 P的 x 向位置误差 Δ rx相关的几何误差源进行检测、分析与预测。下面将采用激光干涉仪以及电子水平仪等手段检测与 Δ rx相关的 6 项几何误差源。具体检测方法与检测结果如下。
2.1 刀架运动误差检测
三项相关的几何误差源均采用激光干涉仪进行误差检测。x 轴测量行程为 2 000 mm,每间隔 200 mm 测量一次,测量点位数目为 11 个。测量过程中 x 轴进给速度为8 m / min,每个测点停留时间为 5 s,越程量为 5 mm,具体测量流程参照 GBT 16462.7-2009 中所述方法。针对每一项误差源,一共往返测量 3 次,获取 6 组误差数据。利用激光干涉仪转角误差检测镜组检测 x 轴运动部件( 刀架) 绕 y 偏转转角误差 εy( x) 的现场照片如图3 所示。误差源 δx( x) 、εy( x) 与 εz( x) 的检测结果分别如图 4 ~ 6 所示。依据 GBXXX 所提供的数据评价方法,定位误差 δx( x) 偏转的定位精度为 0.796 mm,重复定位精度为 0.005 mm; 转角误差 εy( x) 的精度为 0.019mm / m,重复精度为 0.012 mm / m; 颠转转角误差 εz( x)的精度为 0.282 mm /m,重复精度为 0.013 mm /m。2.2 滑座运动误差检测直线度误差 δx( z) 以及偏转转角误差 εy( z) 采用激光干涉仪进行检测,倾转转角误差 εz( z) 由于旋转方向绕其轴线,用激光干涉仪误差检测,故采用电子水平仪进行检测。z 轴测量行程为 17 000 mm,每间隔 500mm 测量一次,测量点位数目为 35 个。测量过程中 z轴进给速度为 8 m/min,每个测点停留时间为 5 s,越程量为 5 mm。针对每一项误差源,一共往返测量 3次,获取 6 组误差数据。
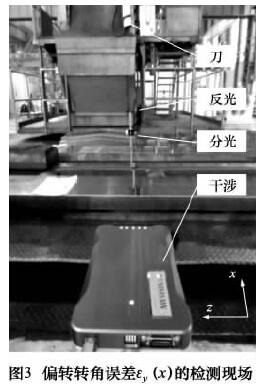
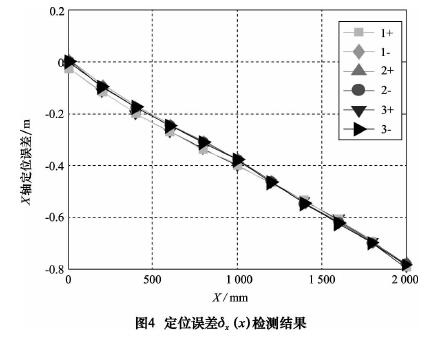
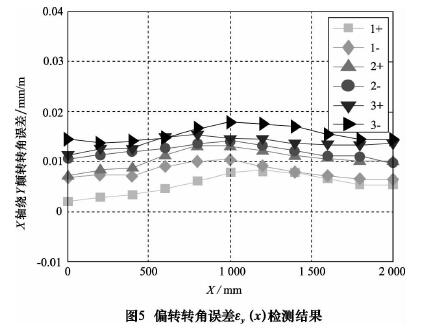
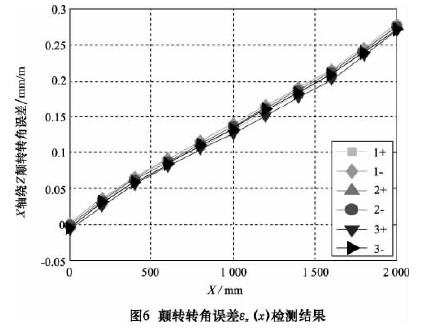
利用激光干涉仪直线度误差检测镜组检测 z 轴运动部件( 滑座) 沿 x 方向直线度误差 δx( z) 的现场照片如图 7 所示。误差源 δx( z) 、εy( z) 与 εz( z) 的检测结果分别如图 8 ~ 10 所示。直线度误差 δx( z) 的精度为0.054 mm,重复定位精度为 0.018 mm; 偏转转角误差εy( z) 的精度为 0.067 mm /m,重复精度为 0.018 mm /m; 倾转转角误差 εz( z) 的精度为 0.042 mm /m,重复精度为 0.007 mm/m。
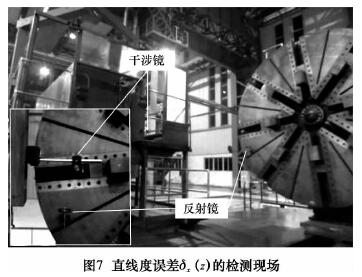
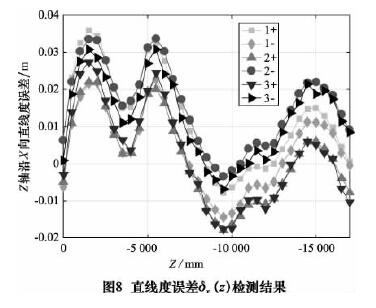
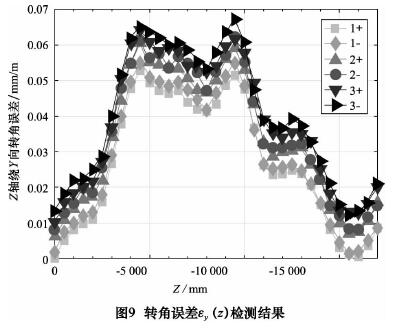
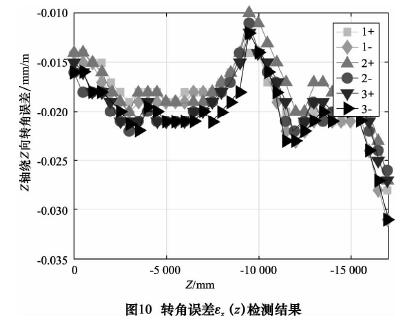
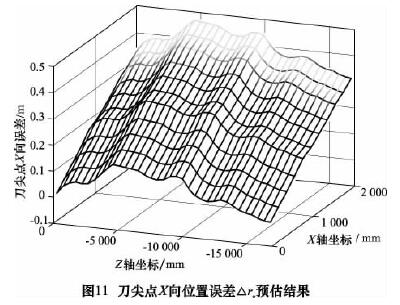
3 、加工精度预测
重型卧式车床的工作空间为由 x 轴和 z 轴构成的经过主轴旋转轴线的矩形平面区域。依据车床几何误差模型式( 3) ,将第 2 节中检测得到的 6 项几何误差源数据代入到误差模型中,即可预估出刀尖点的 x 向位置误差在全部工作空间中的变化情况,具体结果如图 11 所示。可以看出随着 x 坐标的增大,即刀尖点远离主轴旋转轴线,刀尖点误差 Δ rx呈逐渐增大的趋势; 随着 z 坐标的变化,Δ rx呈波浪形变化,无明显规律。全工作空间中,Δ rx的平均值为 0.246 mm,最大值为 0.479 mm。刀尖点 z 向位置误差Δ rz也可利用相同的方法获得。基于上述结果,我们可以获取车床运动至工作空间任意一点处的加工误差,并基于此修正加工程序,抵消机床误差对加工精度的不利影响。
4 、结语
本文以一台重型卧式车床为例,为了提高其加工精度,基于刚体运动学原理建立了机床几何误差模型,得到了各轴线几何误差源与加工误差之间的映射关系,而后采用激光干涉仪、水平仪等测量仪器获取了机床部分几何误差源的误差数据,并进而预估出机床全工作空间内的加工误差变化规律,可用于指导机床的误差补偿等工作,以提高机床的精度性能。
投稿箱:
如果您有机床行业、企业相关新闻稿件发表,或进行资讯合作,欢迎联系本网编辑部, 邮箱:skjcsc@vip.sina.com
如果您有机床行业、企业相关新闻稿件发表,或进行资讯合作,欢迎联系本网编辑部, 邮箱:skjcsc@vip.sina.com