基于机器视觉的数控车螺纹修复方法
2020-5-21 来源: 安徽工程大学 作者:俞俊杰,刘有余
摘要: 螺纹工件在加工或在使用过程中容易造成螺纹牙的损伤,结合数控车床修复螺纹工件的方法,提出基于机器视觉的数控车床螺纹修复方法。方法是利用 CCD 摄像机对所需修复的螺纹工件进行图像采集,并对图像进行分析处理,得到螺纹工件相对于数控车床卡盘的位置变化信息; 对数控程序中刀具移动参数的进行修正,控制数控刀具在加工过程中的准确定位,实现数控车床对螺纹工件的修复。本方法不需要在车床卡盘上标记点,也不需要多次调整工件,效率高,利于批量加工,提高经济效益。
关键词: 螺纹修复; CCD 摄像机; 图像处理
引言
螺纹零件是最重要的机械基础性零件之一,在螺纹的生产或使用过程中,会因各种不同的情况而导致螺纹零件无法正常地使用。如在刀具磨损的情况下,加工的螺纹工件的螺纹深度就会出现偏差,这就导致在使用过程中螺纹工件无法正常使用; 在使用过程中,螺纹工件受到挤压会导致螺纹局部变形,这就导致螺纹工件在拆卸后无法再次使用。为了减少材料的浪费,降低生产和使用成本,对于无法使用的螺纹工件需进行修复,以降低生产成本,提高经济效益。
目前,研究人员已提出了多种的螺纹修复方法,数控车修复螺纹是目前普遍使用的修复方法,如范芳洪等人提出可通过主轴编码器一转零脉冲信号位置和螺纹起始位置重合的关系,通过设计一种主轴一转零脉冲信号制动电路,利用对刀点计算确定螺纹入刀点,但是由于经济型数控机床不具备定向功能,在使用主轴自定位方法时,对机床需要改造,这样的修复方式太过繁琐,且经济效益不高; 李恒征等人提出了一种利用固定程序段在待修复工件上找正螺纹,通过将找正螺纹起点与待修复螺纹起点重合的方式实现对螺纹修复的方法,但是此方法不但需要在车床卡盘上标记,而且在加工过程中需通过卡盘标记点多次调整工件,才能完成修复工作,这种修复方式太过繁琐,不利于大批量修复。
针对上述的不足之处,本文提出了一种基于机器视觉的数控车螺纹修复方法,此方法其重点在于,利用定位安装好的 ccd 摄像机对螺纹工件进行图像采集,把拍摄的数据传送至电脑,运用 mat-lab 软件的图像处理功能对采集图像数据进行分析计算,根据图像分析计算获得螺纹某一点的轴向移动变量,运用螺距与螺纹旋转角度的关系,计算出这一点的移动变量相对应的螺纹旋转角度,利用弧长与角度的关系,结合螺纹半径把旋转角度转换成弧长,通过数控加工中的主轴转速和刀具移动速度,把螺纹的弧长变量转换成刀具的移动补偿量,在数控程序中对刀具移动进行修补,从而输出指令使刀具准确定位,完成螺纹的修复加工。
1、 总体方案
在修复工作前,先试加工一件标准件,然后通过 CCD 摄像机对标准件的螺纹图像进行采集,并传输给电脑。接着拆下标准件将待修复的螺纹工件送入机床卡盘,对待修复螺纹进行轴向定位并夹紧工件,通过 CCD 摄像机获取修复工件的螺纹图像信息并传输给电脑,通过 matlab 图像分析标准件与被修复工件的螺纹图像,通过重叠对比的方式获得螺纹的轴向信息,同时计算出刀具的移动补偿值,操作人员只需修改加工程序中刀具移动参数,便可实现自动对刀,运行修复程序。螺纹修复步骤如图 1 所示。
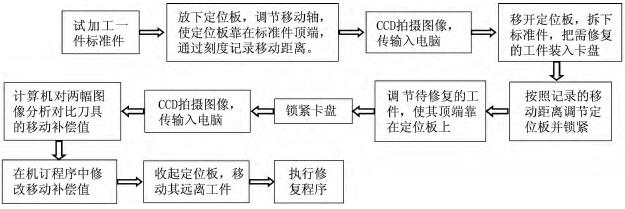
图 1 螺纹修复步骤的流程图
螺纹工件送入机床卡盘,螺纹右端靠上定位板之后锁紧卡盘,启动 CCD 相机对螺纹图像进行采集传输,接着松开锁紧螺栓,旋转定位板并移动CCD 相机远离被加工件,在数控车床的程序中输入计算结果,实现自动对刀。
由于 CCD 摄像机易受飞屑损伤、冷却液遮挡等,因此在摄像机的外部加装防护罩,并设计成可伸缩的形式,通过固定轴上的刻度,调节 CCD 相机的位置,从而达到 CCD 相机的定位准确,这样保证拍摄出来的图像的一致性,为后面图像处理对比的准确性提供了保障。相机安装图如图 2 所示。
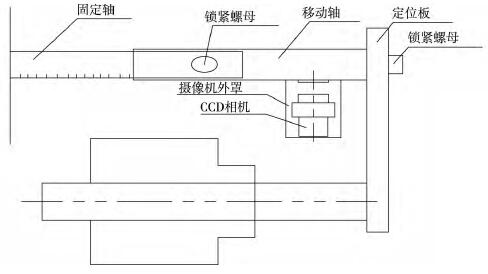
图 2 相机安装图
2、 螺纹修复系统
2. 1 机械部分
2. 1. 1 定位板的运动轨迹
定位板通过螺栓连接在移动轴上,移动轴通过螺栓连接在固定轴上,移动轴采用轴向伸缩式,定位板采用上下移动式,当要修复螺纹时,先移动定位板至合适位置,再调节移动轴使定位板靠在试加工标准件的螺纹顶端,锁紧螺母,为需修复螺纹定位,完成定位后,移动定位板至不妨碍刀具加工的位置。
2. 1. 2 相机外罩设计
因修复的精度的高低与图像采集的清晰度息息相关,保护相机镜头免收加工中飞屑的划伤和切削液的侵入至关重要,所以相机的外罩必须设计成可移动式,在需要拍摄时移动至拍摄位置,在加工时,移动至远离加工工件的位置,以达到保护镜头不受飞屑和冷却液的侵入。此外相机焦距与曝光度的调节直接关系图像的清晰度,因此相机的外罩必须留有可调节窗口,这样可方便调节镜头使其拍摄的图像更加清晰。相机外罩上的调节窗口不应是开放式的,需安装遮挡帘,以保护内部的相机。
2. 2 图像处理部分
2. 2. 1 图像预处理
图像会因采集设备镜头的分辨率、外部场景的光线等一系列的原因导致图像变得模糊,且在图像的扫描、采样、量化的过程中,会引入噪声,最终导致传输进电脑的图像因噪声污染而变得画质下降,由于图像质量的高低直接影响后续的处理效果,所以必须消除噪声对图像的影响,因此对图像需要做预先处理。本文所采样的处理方式是先对图像做灰度化处理,接着对图像做平滑处理,最终对图像做锐化处理。其效果图如图 3 所示。
2. 2. 2 目标区域的提取
在图像预处理后,需对图像进行分割处理,其目的在于把图像中的重点信息与无关背景信息区分开来,通过分割的方式获得准确的特征图像,本文的分割的方式是: 根据图像直方图特征,选择合适的阈值,从而将物体与背景分离出来。其结果如图 4 所示。
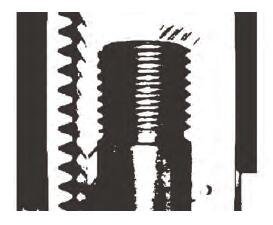
图 3 图像预处理图
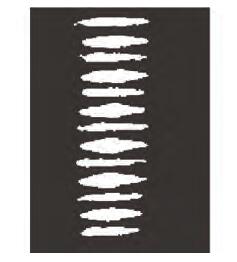
图 4 目标区域提取图
2. 2. 3 获取螺距变量
目标区域的提取后的图像通过连通域分析剔除小面积,对于其他目标进行质心坐标,接着通过对质心坐标进行排序,如图 5 所示,选取所需要的质心坐标,并求出之间的差值,其差值就是螺纹的螺距,图 6 所示,最终两组螺距求差就可得到螺距的变量,如图 7 所示。
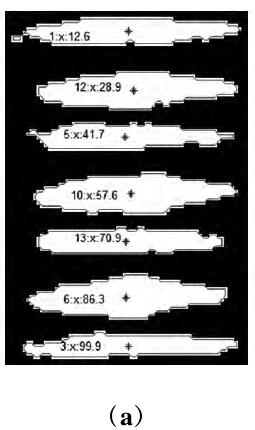
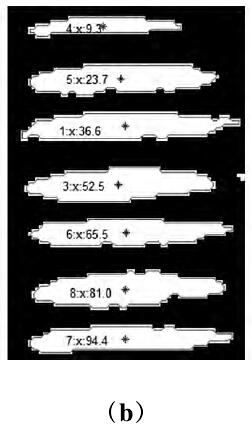
图 5 质心坐标图
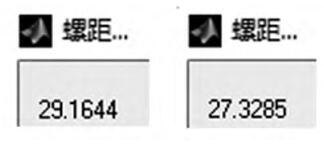
图 6 螺距对比图
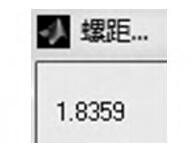
图 7 螺距变量图
2. 2. 4 刀具对刀补偿计算
因沿原螺旋线轨迹对螺纹进行修复,必须保证刀具在开始车削前定位到螺纹入口端点位置,但是由于螺纹工件装夹时无法保证周向定位,所以在不重新对刀的前提下,刀具在移动到起始点的位置时,螺纹旋转后与刀具相接处的点未必是螺纹的入口端点,这样就会对螺纹造成更加严重的破坏。
要完成自动对刀必须使螺纹的旋转周向移动量转换成刀具得轴向移动量,其计算公式为:
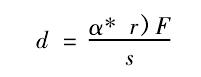
其中: d 为刀具的轴向移动量; α 为螺纹旋转角度的变化值; r 为螺纹半径,s 为主轴转速,F 为移动进给速度,如图 8 所示。
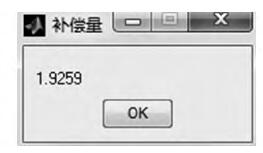
图 8 刀具移动补偿图
结论
作者提出的基于机器视觉的数控车螺纹修复方法,实现了对螺纹的非无接触检测定位,避免人工手动测量定位带来的螺纹修复误差,操作人员只需在机床程序中对刀具的移动参数进行修改就能精确而高效地实现螺纹的修复。
投稿箱:
如果您有机床行业、企业相关新闻稿件发表,或进行资讯合作,欢迎联系本网编辑部, 邮箱:skjcsc@vip.sina.com
如果您有机床行业、企业相关新闻稿件发表,或进行资讯合作,欢迎联系本网编辑部, 邮箱:skjcsc@vip.sina.com
更多相关信息