薄板零件成组加工技术研究及应用
2018-6-14 来源:中车唐山机车车辆有限公司 作者:王宏图 张乙宙 李春来 刘洋 郭继祥
摘要:随着城市轨道交通事业的发展,轨道车辆需求的逐渐增多,由于轨道车辆自身特点,车辆的大中型构架均为焊接结构,焊接背板是焊接工艺必要组成部分,焊接背板是一种薄板件,厚度为 1-4mm,在焊接过程需求量非常大,一台构架焊接需要加工 64 个环形焊接背板,且需要机械加工来满足其精度要求,但是加工时采用液压夹持会使薄板件变形,手动单个装夹会严重影响生产效率。在此情况下将研究成组技术应用于数控车床,解决了加工效率低的问题;同时根据薄板件设计专门支撑和定位结构,增加了加工过程的稳定性,满足了一次装夹便可完成多个环形背板的加工任务,缩短了工艺流程,提高了生产效率。
关键词:成组技术;薄板零件;加工;焊接背板
0 引言
随着城市轨道交通市场的发展,轨道车辆需求的逐渐增多,由于轨道车辆自身特点,车辆的大中型构架均为焊接结构。焊接背板是焊接工艺必要组成部分,焊接背板是一种薄板件,厚度为 1-4mm,在焊接过程需求量非常大,一台构架焊接需要加工 64 个环形焊接背板,且需要机械加工来满足其精度要求。在此情况下将研究成组技术应用于数控车床,解决了加工效率低的问题。
1 、薄板件成组技术研究
经过统计分析,不同环形背板,尽管其结构、尺寸不同,但可以将其视为相似件,例如某种制动导柱背板基本尺寸为 66×5mm、66×3mm、66×2mm,加工精度为±0.2mm。故此在机械加工时,将将多种背板按照其尺寸的相似性分类成组,然后按照零件组拟定成工艺规程,选择工艺装备,下达生产任务组织批量加工。同时改变车间的生产组织和管理模式,由传统的按照产品组织生产、加工质量由专门人员控制改为多种产品混线作业,一工多能的方向发展
2 、薄板件成组加工工装制造和应用
由于薄板件厚度小、壁薄,径向只能承载不大于 0.5t压力,轻微的装夹力都会导致工件翘曲,故此采用轴向(厚度方向)压夹方式,通过锁紧螺栓施加压力来锁定制动导柱背板,保证锁紧有效和夹持稳定性。在工件定位方式上,采用机械圆周定位,定位圆周内腔的直径与薄板件外径差值不大于 0.2mm,保证了定位的准确性。
在工装长度方向上,内腔容纳长度的长度为 45mm,保证了一次装夹即可完成多个薄板加工要求,实现成组加工提高了加工效率。如图 1 所示。
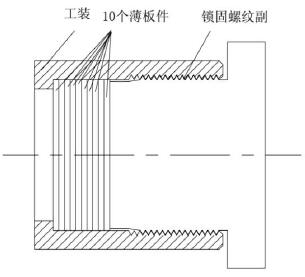
图 1 车削成组加工工装示意图
3 、薄板件成组加工工艺参数设定
环形薄板件加工时会优先选用车床,车床加工成本低、效率高,但成组薄板件和单个实体零件相比,车削工艺参数需适当调整。车削用量选定原则根据实际工况选择切削深度、进给量、切削速度,并兼顾刀具耐用度。合理择切削用量,需综合考虑生产率、加工质量和加工成本。薄板件刚性偏低,适合采用较小的切削深度和进给量,采用较高的切削速度。线速度设定为刀片厂商推荐最低值得80-95%。
4 、薄板件成组加工优点
①生产效率高。合理设计的工装内腔深度可保证了一次装夹即可完成多个环形柱背板加工要求,极大提高了加工效率。②工艺准备周期短。采用机械圆周定位,只需根据不同的板件放入工件即可实现定位,无需找正,且只需要一次对刀即可,工件二次装夹后不需要反复校正 0 点。③生产成本低。工装为机械结构,易于制造且免维护,螺纹锁紧力大,自锁性好,工装材料为 45 钢,稳定性好,避免了因为大量制造专用工装带来的附加成本。
5 、结论
薄板件成组加工技术研究及应用,解决了加工薄壁件效率低,工艺准备周期长的问题;缩短了工艺流程,提高了加工效率;降低了专有工装带来的附加生产成本。该方法的不仅可满足大批量薄板件的生产,也可向异形件、焊接件等零部件制造推广,对提升企业的竞争力有着很好的实用价值。
投稿箱:
如果您有机床行业、企业相关新闻稿件发表,或进行资讯合作,欢迎联系本网编辑部, 邮箱:skjcsc@vip.sina.com
如果您有机床行业、企业相关新闻稿件发表,或进行资讯合作,欢迎联系本网编辑部, 邮箱:skjcsc@vip.sina.com
更多相关信息