叶轮加工工艺及其装夹解决方案
2018-1-12 来源:上海电机学院机械学院 上海凯士比泵有限公 作者:侯培红 洪张 赵桐和
摘 要:分析某叶轮的用途和工作条件。根据叶轮的材料、结构特点和技术要求,分析研究其加工方案,包括加工工艺、技术难点和采取的技术措施。提出在叶轮一端增设所需要的工艺夹具凸台和设计开发了一种专用夹具模子以满足叶轮加工要求的方案,不仅达到了图样的零件加工精度和形位公差要求,而且加工效率也得到很大的提高。
关键词:叶轮;加工工艺;专用工装;工艺改进
0 引言
立式混流泵广泛用于电站、电厂输送循环冷却水,海水淡化、城市给排水和泵站以及农业灌溉等领域,它对于城市的绿化、环保等起了很大的作用。由于叶轮是水泵转动的关键零件,技术要求比较高,因此其精确加工是一个很大的难题。加工精确可以减少由于水流引起的振动从而提高叶轮的使用寿命。立式混流泵的出水口径比较大(如4,1 800mm),叶轮与泵的对应孔中心线的同轴度非常重要。若同轴度不满足要求,则会碰擦叶轮室,使叶轮损坏,重者使泵咬死,无法工作,所以叶轮的加工精度和同轴度就显得尤为重要¨引。
1、 零件材料及其加工工艺性分析
1.1叶轮材料与毛坯特点
加工对象为图1所示的叶轮。由于其结构复杂,一般采用铸钢件毛坯。铸件毛坯切削余量比较多,若毛坯尺寸为4,1 250~4,2 000mm时,余量(单边)为23mm;若毛坯尺寸为4,800—4,1 250mm时,余量(单边)为21mm。叶轮的材料是ZGOFCRl9N19,为奥氏体不锈钢,含有Ni元素,而Ni的韧性很大,影响切削性能,刀具易因粘刀而损坏。奥氏体不锈钢还要进行1 0500C的固溶处理,其硬度一般在360~400HB之间,再加上奥氏体不锈钢铸造时产生的黑皮,所以其硬度较高,而且由于叶片的切削是不连续的,因此切削时易造成崩刀,所以叶轮加工对刀具要求比较高旧J。
1.2 叶轮加工的工艺性分析
由于叶轮形状复杂,硬度高,且JJn-r_时易粘刀,所以其加工难度大。加工方法也纷繁多样,其中DVT400:.:31/32型立车加工应用最广,但对工人水平要求很高,而且要用专用工装才能保证装夹的可靠性和切削的稳定性∞引。一般而言,叶轮加工存在如下问题。
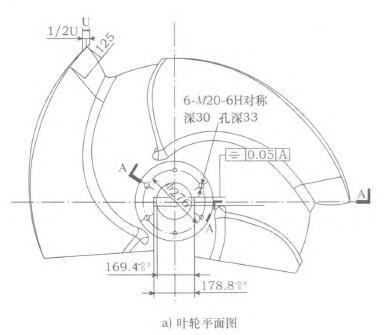
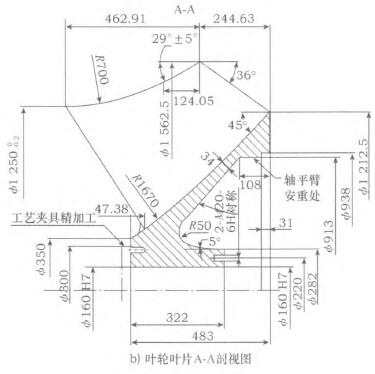
图1 叶轮零件图
1)找正时间过长。切削时对工件的径向(指向工件回转轴的方向)作用力极容易使工件产生振动,发生位移,这时需要第二次找正。
2)精度和工艺尺寸很难保证。叶轮叶片是外球形,精度要求比较高,再加上机床本身误差的影响,叶轮加工的精度很难保证。
3)生产效率低。加工叶轮叶片时的安装、调整等,辅助时间和机动时间过长,尤其是单件生产。
4)容易产生废品。加工的精度和工艺尺寸很难保证,使废品率提高,生产成本相应增加。
2 、叶轮叶片加工工艺处理
2.1基准面的确定
根据工艺要求,选择非加工面作为粗基准面。从图1所示的叶轮零件图可以看出,妒13mm和R50组成的成型面与叶片根部左上侧的45。斜面为非加工面,可以作为粗基准面。但由于其为非加工表面,所以作为基准面,校准是非常重要的,而且必须要求这两个面同轴。如果基准面校正不准,则会影响动平衡的去重。如果基准面校正偏差过大,动平衡去重过多,定会影响叶轮的强度,甚至会引起报废,因此为避免因去重造成不良影响,校正基准面和保证壁厚就显得尤为重要。
2.2 叶轮叶片加工工艺处理
根据以上讨论,需要夹住叶片根部左上侧45。斜面校准,但是由于叶片结构为3片式,而且是圆弧面,若用图1a上左侧6个M20的孔无法夹牢,这6个孔只能用于粗加工夹紧,因此增厚左侧工艺凸台,并在上面加工6个M24的螺孔,用作装夹。在用左侧工艺夹具凸台夹紧时,先校正妒13mm和R50mm组成的成型面并作为基准,然后粗车61 212.5mm外圆,和右端4,1 212.5mm的大平面,再后以妒13mm和R50mm组成的成型面作为反向基准,校正左上侧450斜面的上、中、下三点(上、下两点可选在从外端30mm处,中点可选斜面中点位置),最后再粗车切平左端工艺凸台平面。
若左右两端的平面由于铸造的原因而出现偏差,可以两面均留有一定的切削余量,这样可以减少由于铸造的偏差而造成的不平衡量过多而引起的零件报废。有了叶轮两端的基准,就可以按表1所示的叶轮叶片机械加工工艺过程,进行后续的切削加工H引。
表1 叶轮叶片机械加工工艺过程

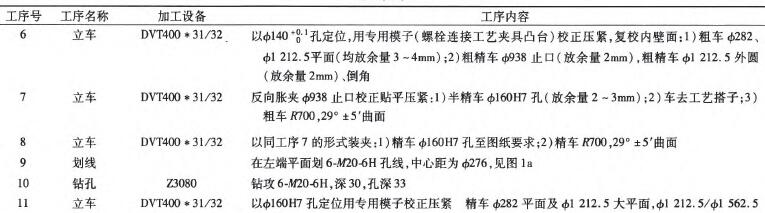
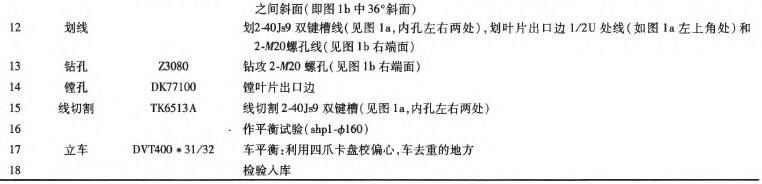
根据以上分析知道,利用立车加工叶轮的方法必须改进,以达到加工精度和批量生产的需要。如通过改进模子,既能达到高的加工精度,而且加工设备简单,操作和调整也方便‘1‘2]。
3 、叶轮加工工装及其解决方案
3.1一般叶轮加工装夹方式
根据一般立车的加工工艺,当从粗加工到最后进行精加工西1 212.5mm外圆、右端面和qb282mm处右端,车咖938mm止口,需要调换压板,分别采用图2a所示的压板式叶轮加工装夹和图2b所示的利用内孔叶轮加工装夹方式。在调换压板过程中,由于时间过长,又不稳定,使零件精度下降,不能达到图样要求。还有,在利用内孔夹紧时,由于+160H7内孑L面过小,接触面小,压紧时稳定性比较差,而加工西1 212.5mm外圆及其右端面时的切削力较大,而且材料又是奥氏体不锈钢,也增大了切削难度,切削不小心就要梗刀而翻身,轻者使零件报废,重者发生伤亡事故。为了提高劳动生产率,保证加工质量,降低劳动强度,需要对叶轮加工装夹方式改进。
3.2 叶轮加工装夹改进方案
叶轮加工工艺及其木模工装改进,须从粗基准质量保证为起点。如本文第2章所述,先从叶轮外壁非加工面开始,校正左上侧45。斜面的上、中、下三点(上、下两点可选在从外端30mm处,中点可选斜面中点位置),粗车左端面和两端浇铸上去的外圈与平面,反向校正妒13mm与R50mm组成的成型面作为基准面,若叶轮内壁与外壁有偏差,可以两壁均留有一定的切削余量,这样就可以减少由于浇铸带来的壁厚误差。
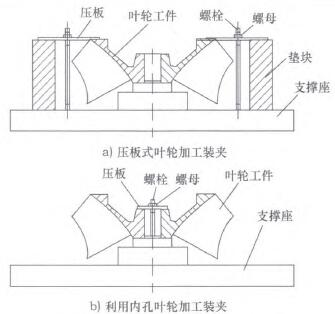
图2 一般压板式叶轮加工装夹方案
如车右侧qb282mm端面、咖1 212.5mm右端面与外圆,可以先划图1a所示零件中6-M20-6H孔线,再钻6-M20-6H孔,然后在立车时,利用该6-M20螺纹孑L,将其在如图3所示的叶轮车削夹具模子上压紧,车qb282mm外圆面,车西l 212.5ram右端面及其外圆面。夹具模子定位、夹紧叶轮状态如图4所示。木模工装适合叶轮体批量加工,使得叶轮体的夹紧可靠、方便和快捷,这样的叶轮体加工工艺、方法,易使加工精度和形位公差满足图样要求,使叶轮体加工更为合理Hd 0|。
3.3 叶轮加工夹具模子及其定位说明
叶轮车削夹具模子结构如图3所示,以零件tkl60孑L定位,将零件安放到模子上,其下端用螺母拧紧,即利用图4所示夹具模子与零件左端端面上6个螺纹孔配合,首先在零件上拧紧长为120mm左右的6根M20双头螺柱,然后在模子中心与零件中心用M30的螺柱将压板夹紧。基准定位采用图la所示叶轮体左侧端面与夹具的平面的接触部分,相当于3个支撑点限制3个自由度;叶轮体的左端6160内孔面和夹具的凸台侧面接触相当于2个支撑点限制2个自由度,最后一个自由度是靠压板保证。
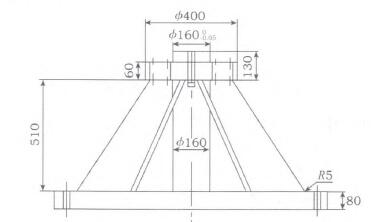
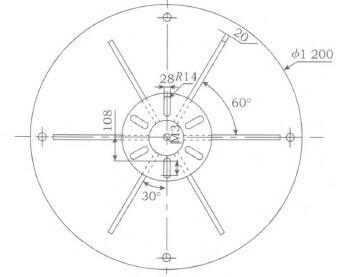
图3 叶轮车削夹具模子结构
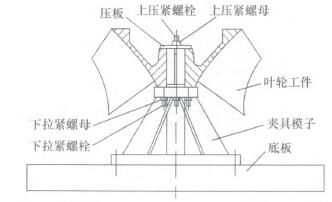
图4 夹具模子定位、夹紧叶轮状态
4、结语
叶轮在校不准基准面情况下加工,严重影响叶轮平衡,使叶轮与轴承产生振动,造成叶轮室等零件损坏。若水泵出现故障时将严重危害电厂的运行安全,甚至还将导致重大事故的发生。通过使用改进夹具模子等操作后,加工精度和形位公差均完全满足图样的设计要求,加工效率提高40%左右。夹具模子定位方法合理,夹紧可靠、方便且快捷,使叶轮的加工质量保持稳定,满足了批量制造,提高了劳动生产率,降低了生产成本,提高了经济效益,增加了产品在市场上的竞争力。
投稿箱:
如果您有机床行业、企业相关新闻稿件发表,或进行资讯合作,欢迎联系本网编辑部, 邮箱:skjcsc@vip.sina.com
如果您有机床行业、企业相关新闻稿件发表,或进行资讯合作,欢迎联系本网编辑部, 邮箱:skjcsc@vip.sina.com