温度致丝杠伺服系统直线度误差研究
2017-7-5 来源:天津商业大学机械工程学院机械系 作者:陈诚,陈瑞,周丹丹
摘要:滚珠丝杠副是精密伺服驱动系统核心零部件,随着丝杠运行,温度升高会导致丝杠单轴伺服系统直线度误差增加。为了明确该误差及其产生规律,建立滚珠丝杠副热误差模型,分别对滚珠丝杠副的热源、温度场以及热误差模型进行了研究。根据滚珠丝杠副的结构特点,确定其内部热源及温度场分布规律,分析热误差的特性。设计实验,检定温度变化前后的直线度误差,设定5min间隔分段运行,明确温度和直线度误差的变化过程及规律。实验结果表明,随着温度升高,丝杠直线度误差随着丝杠本身的弯曲状态会出现更为明显的弯曲,剔除丝杠自身存在的直线度误差和检定过程中斜率误差后,直线度误差增加了11.4μm。本文得到丝杠直线度误差随温度变化的规律,可以应用于其他空间驱动系统整体几何误差的检定和补偿,具有较强的工程应用前景。
关键词:滚珠丝杠;热误差;直线度误差;误差检定
1.引言
滚珠丝杠副是精密伺服驱动系统的核心零部件,实现驱动及精密定位,针对伺服驱动系统的高速高精度发展,要求滚珠丝杠具有更高的精度[1-3]。研究滚珠丝杠驱动系统热误差及其变形规律,是提高驱动系统精度、速度性能的关键。国内外众多学者针对滚珠丝杠驱动系统热误差,已经进行了大量研究。利用改进集总热容法,建立模型,分析滚珠丝杠副定位误差。针对丝杠支撑状态,分析得出 丝杠、轴承温升与热变形是非线性相互耦合的变化。以及多变化热源作用下丝杠的复杂热特性[4-6]。
以上方法多针对热变形产生的丝杠定位误差,并利用不同理论和丝杠热误差经验模型预测温度敏感点和丝杠轴向热变形的关系。而对于丝杠在热膨胀之后产生的直线度误差并没有太多的关注。在某些二维和三维驱动系统中,X、Y、Z3轴驱动系统是通过单轴驱动装置的相互连接来实现二维和三维运动的。因此支撑其他轴驱动系统的直线度误差会传递到被支撑轴,耦合成其成轴轴向的定位误差。本文以丝杠温度场模型为基础,结合非线性热膨胀特性,研究双端支撑丝杠在温度变化后,变形引起的直线度误差变化规律。
2.滚珠丝杠副温度场及热变形模型
滚珠丝杠副产生热变形的重要热源是丝杠与螺母间的摩擦发热以及两端支撑轴承摩擦发热,如图1所示。
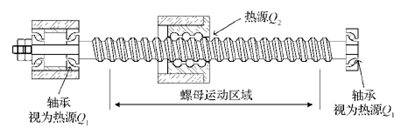
图1 滚珠丝杠副的主要热源
根据本文所用滚珠丝杠副的结构特点,将其传热特性简化为长度为L 的一维杆传热模型。由图1可知,移动螺母处的摩擦热源可以简化为一个往复运动的移动点热源,而支撑轴承的摩擦热源简化为一个固定热源。如图1所示,丝杠轴向长度l远大于其直径2R0,为了便于研究,忽略径向温差,视其为只存在轴向温度梯度的一维导热体,丝杠热传导方程为[7-8]:
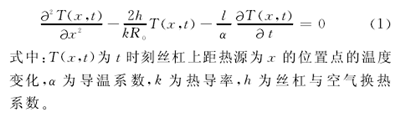
丝杠的温度响应由多个热源作用产生。由于热传导方程式(1)忽略了辐射以及传热时存在的非线性因素,式(1)是线性偏微分方程,满足叠加原理[8]。即多个热源同时作用下,丝杠的温度响应等效于各个单热源作用下丝杠的温度响应的线性叠加,如式(2)所示:

丝杠螺母系统如图2所示,可认为该系统自身包含3个热源。1)轴承和电机可看成是热源 Q1,丝杠温度响应为T1(x,t)。2)螺母移动发热视为热源 Q2,实验设定,螺母在丝杠某确定范围内往返规律运动,故 Q2可以看成固定热源,温度响应为 T2(x,t)。3)远端支撑螺母热源 Q3,丝杠温度响 应 为 T3(x,t)。得到丝杠温度分布模型,如式(3)所示:
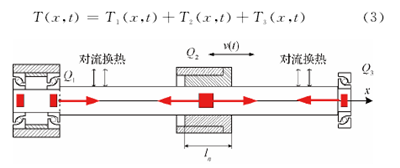
图2 滚珠丝杠副的一维杆传热模型
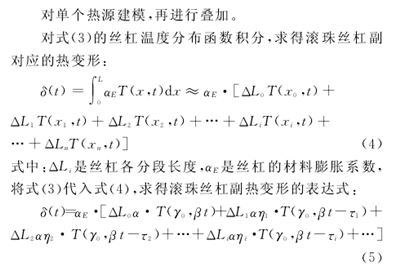
当滚珠丝杠工作摩擦生热,发生热膨胀,且丝杠两端轴承为预紧双端支撑形式,丝杠热膨胀之后会发生弯曲形变,通过搭建激光干涉仪实验系统,可以测量丝杠在热变形后的直线度误差,进一步研究该弯曲形变的规律。
3.丝杠驱动系统直线度误差检定实验
设计实验,对丝杠温升之前及热变形后直线度误差进行检定,利用 RenishawXL-80激光干 涉 仪 直 线 度 误 差 组件检测。温度传感器采用 PT100铂电阻,温度采集精度0.1℃,数据采集,选用 NI信号采集卡。精密丝杠驱动实验室直线度检测,如图3所示。实验过程中螺母在丝杠上来回 往 复 运 动,丝 杠 总 长 度 为 320 mm,运 行 区 间 为300mm,螺母运行速度为60mm/s。在 X 轴运动方向上存在Y、Z 两 个 方 向 的 直 线 度 误 差。分 别 搭 建 直 线 度 镜组,检定 X 轴在Y、Z 两个方向的直线度误差。利用温度传感器采集丝杠温度数据,从丝杠靠近电机端运行起点开始测量,每隔60mm 取测量点。共得到丝杠6个位置的表面温度。运行前初始状态采集原始温度,运行起始后,每隔5min采集一次实验数据。包括各点温度值和驱动平台在Y、Z 方向的直线度误差。丝杠表面温度变化如图4所示,当丝杠运行到20min之后,在环境温度和运行条件不变的前提下,丝杠表面和外界热交换达到平衡,丝杠温度趋于稳定。搭建激光干涉仪光路系统测量 X 轴在Y 方向的直线度误差。实验初始采集丝杠6点温度值,并采集在初始温度时丝杠的初始直线度误差,利用激光干涉仪软件剔除驱动系统和激光光路的斜率误差,只保留驱动系统两端对零。
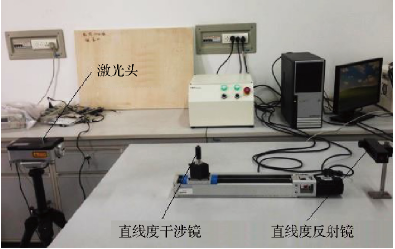
图3 精密丝杠驱动实验台直线度检测
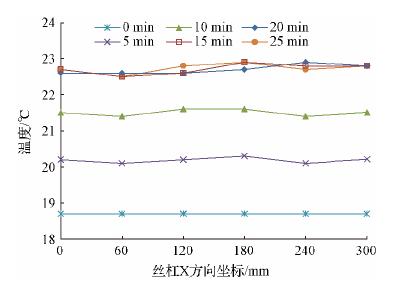
图4 丝杠温度变化后再运行区间的直线度误差
起始状态Y 方向直线度结果如图5所示,0min曲线显示,最大值为2.2μm,由于丝杠本身制造和装配存在直线度误差。
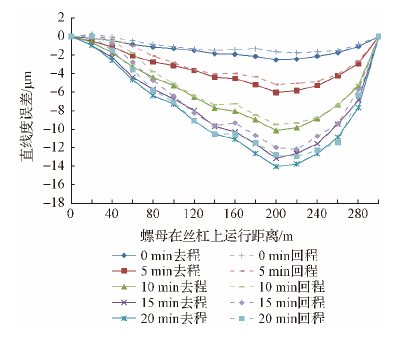
图5 丝杠Y 方向直线度误差
驱动系统开始运行,实验过程中螺母在丝杠上来回往复运 动,丝 杠 总 长 度 为 320 mm,螺 母 往 复 运 行 区 间 为300mm,给定螺母运行速度为60mm/s。程序设定,螺母连续运行5min后停止,在停止前采集最后一个往复来回的直线度误差,停止后,迅速采集丝杠上6个分布点的温度。之后立刻运行下一个5min的往复运动周期。重复进行上述实验,直到20min,丝杠温度达到和外界环境的温度平衡。丝杠的形变也达到稳定状态。丝杠的直线度误差变化如图5所示。丝杠温度变化和形状变化集中在前15min,且形变和温度变化的趋势呈现合理的一致性,随着温度的增高,丝杠会出现膨胀,当温度趋于稳定,丝杠的形变也随之稳定。如图6所示,丝杠在起始阶段和运行温升形变后的直线度误差。在两端轴承的作用力下,丝杠在原来弯曲的趋势下,呈现更为明显的扭曲,体现在直线度误差的明显变化。
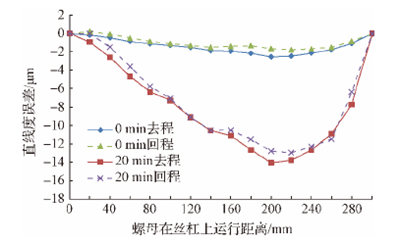
图6 丝杠Y 方向起始及温升后直线度误差
为了更加明确直线度误差的变化,将起始阶段和20min后,丝杠单程来回行程的直线度误差平均,如图 7所示。对该两项平均误差做差,得到丝杠整体直线度误差的相对变化。为丝杠在温度变化后,纯粹由温度变化引起的直线度误差。可以看到,温度变化对丝杠形变会带来影响,当丝杠两端存在支撑轴承,丝杠不能自由伸长的时候,会产生膨胀后的弯曲,引起直线度误差的变化,本实验结果验证该实验条件下,丝杠有温度升高带来11μm 的直线度误差。
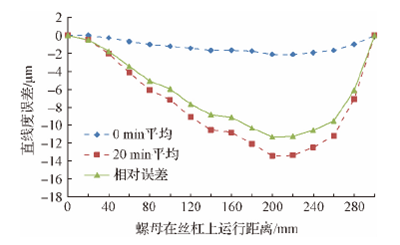
图7 丝杠Y 方向直线度误差平均值及相对变化
单轴伺服驱动系统存在两个方向的直线度误差,调整激光干涉仪镜组的方向,重复上述实验,来检定该驱动系统在Z 方向上的直线度误差,包括初始直线度误差和随温度变化后的直线度误差。实验结果如图8所示。可以看出丝杠在Z 方向的直线度误差变化不明显。
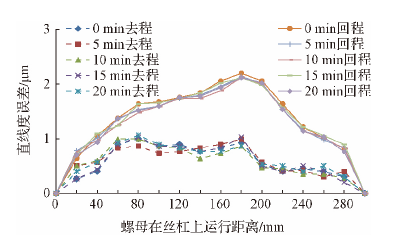
图8 丝杠Z 方向直线度误差
4.结论
滚珠丝杠驱动系统在运行过程中,螺母轴承等环节存在摩擦生热,丝杠发生热膨胀,在丝杠两端轴承固定支撑的前提下,热伸长的丝杠会在本身存在直线度误差的基础上发生更为明显的扭曲,体现在直线度误差的变化上。本文实验系统为单轴伺服驱动系统,利用激光干涉仪搭建误差实验系统,检定该单轴驱动系统在运行过程中垂直运行轴向两个方向的直线度误差。首先检定丝杠在初始没有温升的条件下,本身存在的固有直线度误差。通过消除斜率计算,到实验用丝杆本身存在2.2μm 的直线度误差。丝杠运行后,间隔5min采集丝杠温度变化及丝杠的直线度误差。随着温度升到,丝杠直线度误差随着丝杠本身的弯曲状态会出现更为明显的弯曲,最大直线度误差达到13.7μm。可以看出,随着温度的变化,直线度误差增加了11.4μm。本实验检定的单轴直线度误差会耦合到二维和三维驱动结构的整体误差中,而本文得到丝杠直线度误差随温度变化的规律,可以应用于其他空间驱动系统整体几何误差的检定和补偿,具有较好的工程应用前景。
投稿箱:
如果您有机床行业、企业相关新闻稿件发表,或进行资讯合作,欢迎联系本网编辑部, 邮箱:skjcsc@vip.sina.com
如果您有机床行业、企业相关新闻稿件发表,或进行资讯合作,欢迎联系本网编辑部, 邮箱:skjcsc@vip.sina.com
更多相关信息