典型切削机床能耗模型的研究现状及发展趋势
2015-2-3 来源:数控机床市场网 作者:大连理工大学机械工程学院
(大连理工大学机械工程学院 李涛 孔露露 张洪潮 ASIF Iqbal )
摘要:机床作为机械制造行业的“母机” ,数量大、能耗高、效率低。近年来,学者们为建立精确的机床能耗模型已做大量工作。针对典型切削机床能耗的建模现状,从切削单元能耗、加工阶段整机能耗、工艺单元能耗三个层次进行综合分析。进而从节能优化、产品绿色性评估、企业资源配置、机床绿色设计四方面对机床能耗模型的应用进行论述。目前,机床能耗的建模逐渐面向高端数控机床,建模的目标性更加明确,与工业应用的结合也使得模型的实用价值不断提升。
关键词:典型切削机床;切削比能;整机能耗;工艺单元能耗;节能优化
1 前言
我国是全球机械制造业大国,同时也是机床生产、消费第一大国,拥有世界第一的机床保有量,目前约 800 万台。若每台机床额定功率平均为 10 kW,则我国机床总额定功率约相当于三峡电站总装机容量(2250万kW)的3倍多。而且,统计资料表明,机床能量利用率平均低于 30%,如果我国机械工业的各类机床的能效都提高 1%,则带来的节能效益相当于几千万吨标准煤。由此可见,机床量大面广,耗能多,但其能量利用率低,节能降耗潜力大,研究机床能量消耗对于提高资源利用率、实现绿色与可持续制造具有重要意义。同时,机床能耗也是评价机械加工环境性能的重要指标之一,研究表明,离散加工行业(车、铣等)机床对环境的影响 99%是由于消耗电能引起的。2010 年 10月 26 日,国际标准化委员会起草了机床的环境评估标准(ISO 14955),将节能减排的理念贯穿于机床设计到机床使用等主要耗能阶段。可以预见,未来能耗指标将成为评价机床产品的一个新指标。鉴于此,国内外学者针对揭示机床的能量特性、建立机床能耗模型开展了大量的研究工作,以探寻节能降耗途径、减少环境污染、推动绿色与可持续制造的发展。
机床能耗是一个多部件多层次的系统问题,其能耗部件繁多,由 ISO14955-1 可知,机床能耗涉及机床主传动系统、进给系统、辅助系统等多个能耗子系统,涵盖机电液三种类型,具有多源能耗特性。此外,文献[3]在机床的运行过程中,机床的各部分存在各种性质的能量损耗,这些损耗相互作用、相互影响,从而使机械加工系统的能量损耗规律变得复杂,国内外学者对此展开了多方面的研究工作。本文对当前典型机床能耗模型的研究现状进行了总结,已有的能耗模型可以归结为三个层次:切削单元能耗、加工阶段整机能耗、工艺单元能耗的建模研究。切削单元能耗指机床切削过程中,克服材料变形抗力将材料去除所消耗的能量,是机床总能耗中的有效能部分;加工阶段整机能耗是指机床处于切削加工阶段时,整个机床系统所消耗的能量;工艺单元能耗是指综合考虑机床不同运行阶段(装夹、启动、空载、加工、换刀等)整个机床系统所消耗的能量总和。这三个层次的关系可由图 1 描述。
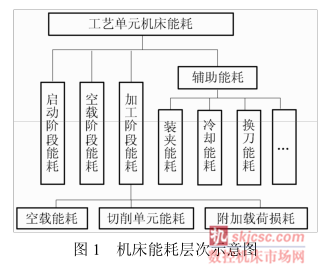
1 机床能耗模型层次化整合分析
1.1 切削单元能耗模型的研究
切削单元能耗由于受到切削参数工件材料、刀具参数、工艺条件、外部环境等各种变量的影响,这部分能耗难以进行精确量化。目前该部分的量化主要从分析切削力入手,或在各种理论知识支持的基础上通过分析材料去除机理定性地建立切削力预测公式,或基于实际加工经验数据运用数学拟合方法进行切削力的定量建模,进而对材料去除能耗进行计算。
1.1.1 基于材料去除机理的切削能耗模型
(1) 理论切削力模型的建立。金属切削过程的实质是被切削金属层在刀具前刀面的挤压作用下产生剪切滑移的塑性变形过程。虽然切削过程中产生弹性变形,但其变形量与塑性变形相比可忽略不计。针对包括铣削、钻削、镗削等在内的不同切削加工方法,虽然刀具和工件的相互作用形式有所不同,但工件材料在切削加工过程中的塑性变形规律以及切屑形成机理是相同的。本文采用直角切削模型从理论上说明金属切削加工的变形过程。直角切削模型是在揭示切屑变形本质和现象的基础上忽略一些次要因素建立起来的简化物理模型。该模型由美国学者 MERCHANT[8-9]在 1945 年提出,揭示了切削力与切削条件之间的关系式,并用最小功原理求出了剪切角。这一理论模型的提出奠定了进行切削力理论预测的基础,一直沿用至今,此后的理论模型大多在此基础上进行的修正。如图 2 所示为MERCHANT 的切削力模型。
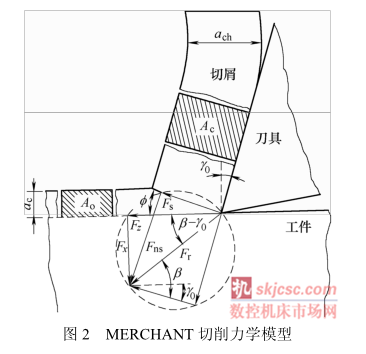
图 2 中,ac为切削层厚度;Ao为未切削前的切削层面积;Ac为切屑截面面积;ach为切屑厚度;γ0为刀具前角;为剪切角;β为切屑与刀具前刀面间的平均摩擦角;Fns为剪切面上的正压力;Fs为剪切力;Fr为车刀上的合力;Fz为切削速度方向的切削分力;Fx为进给方向的切削分力。
根据材料去除机理及各力间的几何关系可推导出
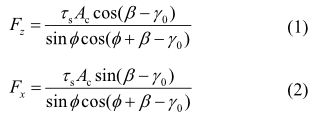
式中,τs为工件材料的名义抗剪强度。 自此,国内外学者对切削力预测争相研究。
1951 年, LEE 等开始利用滑移线场理论来研究理想塑性材料的切削现象。之后学者们建立了正交切削及斜刃切削的切削力模型。提出了考虑刀具磨损及加工硬化的切削力模型,应用摩擦学理论分析了后刀面与工件的摩擦作用力。张弘弢等考虑了温度-速度应变速度效应,不单纯用力学方法又考虑了被加工材料的物理力学性质,使得模型在大多数切削条件下,计算误差小于 3%。BARRY 等分析了金属基复合材料的局部大应变、高应变、高应变率并伴有大量热量生成的切削条件下的本构关系物理模型。
(2) 切削功率及切削能耗的计算。利用力与速度的物理关系可计算切削功率
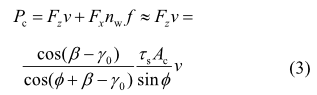
式中 v ——切削速度; nw ——工件转速; f ——进给量;
ap ——背吃刀量(在铣削中指铣削深度);
Pc ——切削功率。
切削能耗为去除一定体积的材料所消耗的能量

在假设切削功率不变的前提下,加工时间 

(V 为材料的总去除体积)。于是整个加工过程的切削能耗

1.1.2 基于实际加工的经验公式切削能耗模型
基于试验测量的经验公式切削能耗模型是利用测力传感器、扭矩测试仪等,通过大量试验,测定不同加工参数下切削力、扭矩的数值,然后利用统计分析及数值拟合建立了切削力、切削功率、切削能耗与切削参数之间的幂率公式。常用的典型工艺的经验模型如表 1 所示。表 1 中,C 为被加工金属和切削条件系数;x、y、z 为指数;K 为修正系数;Ps为铣削功率,Ks为单位铣削力,B 为铣削宽度;vf为铣削进给速度;M 切削扭矩;Cm为由材料确定的系数;D 为钻头直径。
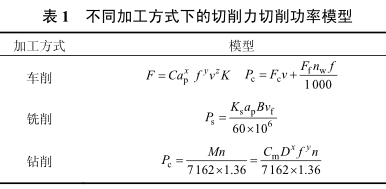
这类模型对于定量分析不同工艺不同切削条件下的能耗大小、指导工艺路线的制定、优化分析等有很好的指导作用。通过这类模型计算得到的结果与实际情况吻合良好,但由于加工条件的复杂性,该模型中附加了大量由实际情况来确定的修正系数,相对繁琐,必须查阅经验数值表才能确定。
1.2 加工阶段整机能耗模型
在切削加工阶段,机床几乎所有的系统都参与运行,且增加了负载能耗,此时机床的能耗组成如图 3 所示(以数控机床为例),作为机床的有效加工状态,学术界给予了极大关注。由 GUTOWSKI 教授负责的麻省理工学院的环境意识制造小组对利用功率表测量机床能耗的方法进行了深入研究:JEFFREY 等通过试验数据建立了不同机床在加工阶段各部分能耗比例分配图,研究结果表明,机床能耗随着机床机构的复杂程度及先进程度的增大而提高,一个加工中心的能量利用率平均不足15%,而对于一个手动机床则在 30%左右。并且机床能耗与机床制造的资金密集程度及操作规程密切相关,机床的能效随着负载的增大而提高。
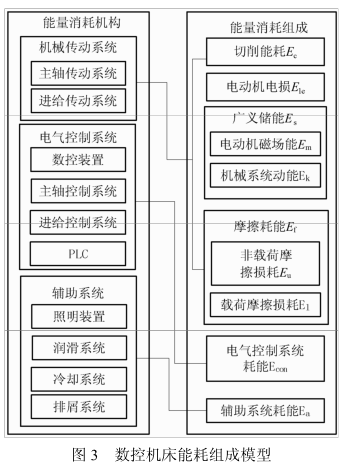
由于机床结构多样,润滑条件不同,机床整机能耗组成各有差异。而研究角度的不同,学者们对机床单元整机能耗的建模也各有特色。1.2.1 机床主传动系统运行能耗预测模型 主传动系统的能耗是机床全部能耗的主体,卧式车床主传动系统的能耗占机床总能耗的 95%以上,有很大研究价值。重庆大学刘飞等从机床电动机和机械传动系统一体化的角度出发,在考虑机床运行中多种能量损耗并存的情况下,以机电系统和各传动环节的能量流程为基础,建立了机床主传动系统的能量传输预测数学模型;提出了普通机床功率和效率计算方法、能量信息监控的方法和数学模型。
该理论认为机床能量消耗由切削能耗、空载能耗及各传动环节的附加载荷损耗构成,其中空载能耗由各子系统的广义储能(机械能、电磁能等)构成,是含有主轴转速、主轴摩擦、阻尼等多个变量的复杂函数,与转速近似成二次函数关系。图 4 为机床主传动系统能量流程图。图 4 中,PFe为电动机的铁耗;PCu为电动机的铜耗;Pad为电动机的附加损耗;Pmec0 为电动机的机械损耗;Em 为耦合场(电磁场)磁能;Eke为电动机转子动能;Pim为电动机的输出功率;Ekn为机械传动系统第 n 个传动环节的动能;Pmecn 为机械传动系统第 n 个传动环节的机械损耗 功率。
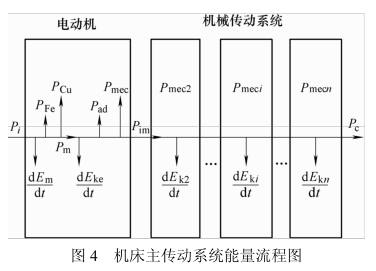
一般形式的机床主传动系统稳态下的功率传输模型为
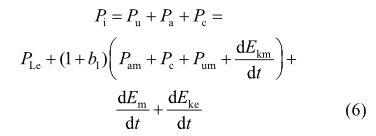
式中 Pi ——主传动系统总输入功率;
Pu ——机床空载功率;
Pa ——机床载荷损耗功率;
Pc ——机床输出功率;
PLe ——电动机的电损;
b1 ——电动机的载荷系数;
Pam ——机械传动系统载荷损耗功率;
Pum ——机械传动系统的非载荷损耗功率。
对式(6)中各部分分别在其相应的工作时间上进行积分,即可得到机械主传动系统的能量消耗 Ein为
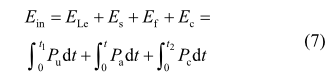
式中 t ——机床总运行时间;
t1 ——空载时间;
t2 ——切削时间。
1.2.2 基于材料切削比能的能耗模型
切削比能是指去除单位体积的材料所消耗的能量。金属切削过程是一个材料逐步去除的过程,切削比能是工件加工时瞬时耗能量的量化,能够反映出切削能耗与材料去除率之间的映射关系及机床能效能力,便于理解和计算。
LI 等利用不同的材料去除率对不同的材料进行切削,建立了材料的切削比能经验公式

式中 SEC——材料的切削比能;
MRR——材料去除率; C0,C1——系数。
他认为材料的切削比能由装夹比能、机床运行比能、材料去除比能及非生产比能(即热损耗比能等)四部分组成。指出模型中的系数 C0、C1并非恒定,定性地分析了材料特性、刀具形状及主轴驱动方式对 C0的影响,机床自身对 C1的影响,但具体关系需要根据实际情况进行确定。这种通过切削比能来预测机床能耗的经验模型,为以后切削比能的研究提供了指引。
早在 1992 年,WARREN建立了切削比能的经验公式,以及 100 多种材料的切削比能基础数据。
随着技术的进步,工艺条件的改善,切削比能不断受到国际学者的关注和应用。GUTOWSKI 等在搜集了大量数据的基础上基于材料的平均切削比能建立了各种工艺的切削比能图谱,半定量地反映不同工艺的能效差异。ALESSANDRO 等[35]对高速切削条件下的切削比能与刀具几何参数与切削速度的关系进行试验研究。 AWADE 等 预测了高速切削铬镍铁合金 718 时,在主剪切区域内的切削比能解析模型,指出剪切比能是进给率的函数,随着进给率的减小而增大,在最低切削速度时,试验剪切比能达到最大。DIAZ 等通过试验分析一个微加工中心在不同的材料去除率下切削低碳钢的能量需求建立了切削比能模型,指出材料的切削比能随着材料去除率的增大而降低,并将该规律拓展到大型机械加工设备中。
1.2.3 基于热力学第二定律的机床能耗模型
BRANHAM 等[38]从热力学角度把机床系统看做一个输入输出系统,利用热力学第二定律通过计算输入输出过程中的减少值作为加工系统的能耗

式中 Blost——的减少值即系统能耗;
Bin ——系统的输入值; Bout ——输出值。
该思路比较新颖,但其计算结果的精度取决于熵、焓、的准确性,偏差仍比较大,同时由于各种材料和辅助材料的熵、焓、值难以直接获得,目前该方法仅在特定条件下进行了试验分析。
1.2.4 神经网络模型
神经网络方法对复杂不确定问题具有自适应和自学习能力,可以有效处理大量工艺参数之间复杂的非线性关系。谢东等利用 BP 神经网络法搭建了机床能耗与切削参数的模型,从输入层、隐含层、输出层的设计,网络的初始化,训练算法的选择,训练样本数的选择,学习速率的选择方面建立了 BP 神经网络,简化了经验公式繁琐的计算过程取得了较好的预测结果。
1.3 工艺单元能耗模型
在一个工件的加工工艺过程中,包括工件装夹、机加工、工件拆卸等步骤,在机加工部分机床的运行包括启动阶段、空载阶段、加工阶段、停机阶段等不同的服役时段。 在上述两层模型的基础上,利用万用表或功率分析仪通过试验测量不同阶段机床运行的能耗可建立机床工艺单元能耗模型。
在工件加工工艺中的总能耗是在各子部件、子过程能耗基础上的累加,因此该部分模型主要以宏观框架模型为主,目前已建立的工艺能耗模型见表2。由于研究目的的不同,有些学者也将机床间接能耗:材料生产能耗、刀具制造能耗以及产品清洗能耗考虑在内。
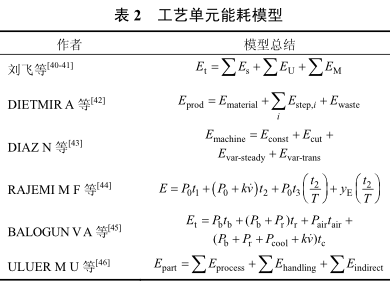
表 2 中,Et为机床总能耗;Es为启动能耗;EU为空载能耗;EM为加工能耗;Eprod为产品生产总能耗;Ematerial为材料生产能量;Estep,i为每个加工阶段能耗; Ewaste为浪费的能量;Emachine为机床总能耗;Econst 为机床功率恒定部分能耗;Ecut 为切削能耗;Evar-steady 为主轴等达到特定运行状态的能耗;Evar-trans 为主轴等启动机加减速阶段变化能耗;P0为空载功率;k 为系数;v 为材料去除率;T 为刀具寿命;yE为刀具制造能耗;t3为换刀时间;t4为刀具制造时间;Pb为基础功率;Pr为准备状态功率;Pcool为冷却系统功率;Pair为空载功率;tb、tr、tair、tc 分别为对应的时间;Epart为加工一个工件的能耗;Eprocess 为制造过程能耗;Ehandling为自动装夹系统及传送系统能耗;Eindirect为与保持环境清洁有关的非直接能耗。
2 机床能耗模型应用分析
机械加工过程实质上是一个材料的去除过程,期间将消耗大量的资源,产生的各种废弃物和排放物对环境将产生很大影响。机床能耗模型能够量化机床整个加工周期的能源消耗及能量利用率,并能够间接反应整个加工周期物料的输入输出情况。因此,利用机床能耗模型可以有效分析机械加工系统的资源能源消耗和环境影响问题。其应用主要可以归纳为以下四个方面。
(1) 节能性工艺优化指导。基于试验测量数据建立起来的能耗模型与实际加工情况有很好的吻合性,主要用于对特定机床的加工任务进行能耗监 控并通过对加工参数的优化得到最佳节能参数。DRAGANESCU 等通过试验,采用响应面分析法建立了机床能耗及能效与切削参数的影响关联模型,通过优化分析得到利用立铣床对铝合金材料进行端面铣削时的最佳节能参数,相对保守参数,去除相同体积的材料,当材料去除率由 6.4 cm3/min提高到 818.6 cm3/min 时,节能可达 93.98%。日本森精机有限公司采用正交试验方法建立机床能耗模型,分析了不同切削参数对机床能耗的影响,给出钻削 S45C 碳钢最佳节能参数,相对于初选参数,在材料去除率提高 25%的情况下材料的切削比能可降低 5%。谢东等采用粒子群优化算法对机床能耗函数进行寻优求解,得出了加工一低碳钢零件的节能性参数,采用优化后的参数能将加工能耗降低 22%,但刀具发热厉害,影响刀具寿命。施金良等根据数控机床主传动系统功率方程,建立了数控机床工步间空载运行时停机节能的理论决策模型,通过实际案例分析得到很好的节能应用效果。周丹等提出一种数控机床能量设计因子提取方法,并对提高机床的能量效率给出了建设性意见。但这些在特定试验条件下得出的结论,对机床节能性使用有一定的指导作用,但由于受实际加工质量要求及设备规范性使用的限制,其可行性及适用性还需要进一步的拓展研究。
(2) 绿色评估支持。将机械加工系统看作一个输入输出系统,将其消耗及排放考虑在内的过程模型对于加工过程的绿色性评估提供了很大支持。美国加州伯克利分校的绿色设计与制造联盟建立了一个将刀具、切削液、材料及能量消耗考虑在内的加工过程模型,对系统产生的废液、切屑、排放物等进行加权量化并评价加工各环节产生的毒性、可燃性、放射性等环境影响因子,寻找敏感环节辅助产品的环境设计决策。麻省理工学院的环境意识小组开发了一系列机械加工中的铣削加工、磨削加工等制造过程的模型,对其产生的资源环境属性进行评价,主要考虑了七种不同的资源消耗和环境影响因素:能量、固体废弃物、回收性、有毒材料、废水、废气、垃圾填埋物等。通过建立设备层模型和物料流模型,评价制造系统中的多种可选制造过程、制造工艺的资源环境属性。
(3) 资源配置,调度安排决策。近年来,绿色制造与可持续制造的理念越来越受到重视,国内重庆大学刘飞课题组提出的绿色制造理论中指出减少制造过程的资源能源消耗是绿色制造的重要目标之一。他们在机床能耗模型的基础上,从宏观角度,建立了面向绿色制造机械加工系统任务的调度模型,根据机床规格与零件加工要求的匹配性采用优化分析的方法获得满足最优零件与机床组合方案进行节能性调度,大大降低了机械加工系统所产生的环境影响和资源消耗。
(4) 绿色设计指导。部件层的机床能耗模型不仅分析了机床部件的能耗特征及其节能潜力,而且为高效部件的结构设计提供基础。ABELE 等分析了机床主轴单元的能耗特性,并指出了节能潜力。ZULAIKA 等提出一种加工过程的轻量化设计方法,同时考虑了减少可移动部件的质量和最大化材料去除率两个因素,用该方法设计了一台大型铣床,结果表明该方法可以将生产率提高一倍,同时因可移动部件质量减少 20%可降低能耗 13%。
3 机床能耗模型研究趋势
近年来,随着大量新工艺、新设备、新技术在机械制造领域的应用,机床能耗的建模对象逐渐转向高端设备,面向特定目标的建模使得模型的实用价值不断提升。当今机床能耗模型的研究趋势可归结为如下。
(1) 对具有机-电-液多源能量融合特征的高端数控机床,从部件层开展深入研究,分析加工过程能量在各子系统流动、融合与分布特性,构建高端数控机床加工过程能耗模型。重庆大学刘飞教授带领的团队在建立了普通机床主传动系统的能耗模型的基础上,建立了变频调速数控机床主传动系统及进给系统的功率平衡方程,揭示了变频器的能量损耗规律,进一步对数控机床空载运行下的能量参数(包括空载功率、空载电流和功率因数)特性进行了分析,并揭示了变频数控机床当电源频率小于基准频率时空载功率是单调递增的,电源频率大于基准频率时主传动系统的空载功率的增减性与其结构参数有关的独有特性。但这些已建立的模型尚处在理论层面,模型中大量模糊影响系数的存在使得与实际情况的吻合性上还有待进一步的试验探究与建模修正。
(2) 建立加工单元过程能耗、物耗、环境数据清单,支持产品生命周期的经济属性、环境属性、社会属性的评估。MICHAEL 等以钻削一种特定零件为例提出了建立单元制造过程离线物耗、能耗分类管理数据清单,为产品设计生命周期评价提供数据支持。黄海鸿等从产品设计角度出发,在分析产品能量消耗特性的基础上导出了产品全生命周期能量过程模型,并加以定量化描述,从而为产品设计提供合理和可行的能量分析手段和应用方法。该思路的提出为推动产品生产的可持续性提供了有力的量化评估方法,所需的清单数据尚需进一步健全。
(3) 机床能耗建模正向多领域交叉化发展,机床能耗建模技术与机电控制技术、智能制造技术、信息通信技术的交叉集成,将推动能耗模型与工业应用的结合。德国德马吉公司开发出虚拟机器、自动停机管理、绿色代码等节能技术。例如,开发的机械加工仿真模拟技术替代试切过程,节约该环节能耗;建立的机床智能管理平台,用户可通过数据系统控制面板设置不同的系统关机时间,控制机床进入休眠状态,最大限度降低能源消耗,还支持唤醒和预热功能。
4 结论
从切削单元能耗、加工阶段整机能耗、工艺单元能耗三个层次对机床能耗的建模进行总结,并对机床能耗模型的应用及研究趋势进行了分析。通过整合分析发现机床能耗模型的研究不断完善,表现在:机床能耗向多层次拓展,向下延伸到材料去除过程的能耗建模,向上拓展到机床层、工艺层乃至车间层;从理论的概念模型细化到具体机床执行具体工艺的能耗随工艺参数变化的精确模型,模型的精度不断提升;模型的应用范围逐渐由单纯节能优化扩展到产品生产的绿色评估、绿色设计及企业资源配置上,面向特定目标的建模技术更具针对性。但还有许多方面需要进一步探究:面向高端数控机床的多源能量流耦合特性尚需完善,局部关键问题尚待研究;面向产品生命周期评估的物耗、能耗、环境清单数据尚待开发;机床能耗建模技术尚待与智能化技术及工业应用结合拓展。
投稿箱:
如果您有机床行业、企业相关新闻稿件发表,或进行资讯合作,欢迎联系本网编辑部, 邮箱:skjcsc@vip.sina.com
如果您有机床行业、企业相关新闻稿件发表,或进行资讯合作,欢迎联系本网编辑部, 邮箱:skjcsc@vip.sina.com