3D 自动化无人加工过程控制
2015-1-20 来源:数控机床市场网 作者:瑞鹄汽车模具宋丹 刘玉明
近年来,国内各大汽车主机厂车型更新日益加快,换型周期越来越短,作为大型汽车覆盖件模具企业要达到高效率、高质量生产模具的目标,必须加快企业技术提升、技术创新的步伐。数控加工是模具制造过程最重要的环节之一,而实现数控机床自动化无人加工是模具厂家所追求的高层次阶段,是体现和衡量其加工技术水平、技术含金量的重要标准之一。
2011 年我公司开始全面实现了 (精铣) 数控加工中心的 3D 自动化无人加工。开发和推进中遇到了各种难题,由于编程、机加、刀具配送等部门的通力协作,通过技术提升和改善,在 3D 自动化加工方面取得了一定的成绩。覆盖件模具加工包括结构面2D 加工和型面 3D 加工,本文介绍的仅是型面 3D 自动化加工相关内容 (见图 1、图 2)。
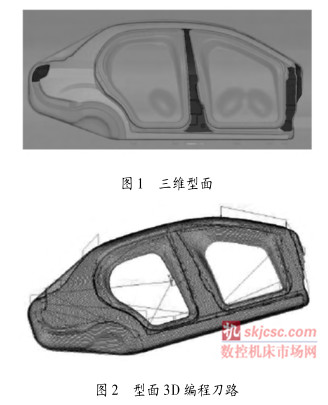
3D 自动化无人加工实施过程涉及模具数学模型标准化、数控编程标准化、刀具配置动/静态管理、机床刀具库管控、刀具寿命规范化管理、(不同控制系统、不同主轴附件铣头) 机床宏程序开发、工件机床坐标原点设定规范化、多环节全程安全保障标准建立等多个环节; 诸多环节涉及模具机加过程的所有工序,真正实现控制过程无错误发生在数控加工中心 3D 无人自动化加工中难度最大。任何一个环节出现小的错误和纰漏都将造成 3D 自动化加工中断、甚至是模具加工过切、刀具折断、撞机等严重事故发生,因此过程控制对于 3D 自动化无人加工(又称数控机床无人值守加工) 的实现至关重要。
一、3D 自动化无人加工控制过程及工作原理
覆盖件模具数控加工长期以来一直沿用由操作员调用单段独立 NC 程序加工的模式,这种加工模式应属于机械化加工范畴。机械化是将数控加工的基本动作由机床代替人工
来完成,但操作和管理加工过程基本动作的操纵工作需要操作员手动完成; 自动化是在机械化基础上,不仅数控加工基本动作由数控机床实现,还需要把操作和管理加工过程基本动作操纵工作交给机床来完成。机床代替人工实现操纵工作顺利完成是自动化加工的重要标志。
针对模具型面 3D 加工而言,原来机械化模式数控加工是由操作员实施手动装夹更换刀具,手动实施对刀、测刀、添加刀具补偿到数控系统中,通过人工调用诸多单一程序实施工件加工; 而 3D 自动化加工是将上述全部动作都交给数控加工中心无人操纵完成。
实现 3D 自动化无人加工硬件及系统环境要求是: 机床必须是数控加工中心; 配备了机床刀具库和自动换刀、自动测刀装置的数控机床才能称之为数控加工中心。
数控加工基本动作包括: 主轴及 (所有附件铣头) 正反转旋转运动; X/Y 工作台运动; Z 轴滑枕或套筒运动; W 轴的横梁运动; 五轴加工的 A/B/C 轴运动等。数控加工基本运动是通过机床控制系统执行 NC 代码 (G 代码、M 代码、S 代码等) 组成的程序段来实现数控设备机械化加工的。
数控加工中心操纵动作包括识别、检测、更换刀具,子程序顺序调用,附件铣头调用、自动加工安全预警等; 通过开发主程序自动生成软件和自动化加工过程控制来实现机床基本动作和操纵动作的全自动化过程,以此达到了数控加工中心无人值守加工的目的 (见图 3)。
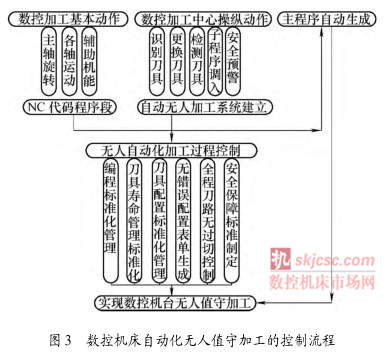
二、3D 自动化无人加工过程控制常见问题分析及解决方案
1. 3D 自动化加工刀具配置标准化管理阶段刀具成本难于控制的成因分析
3D 自动化加工时需要为一个数控机床配置几十把甚至上百把刀具,在刀具配置标准化管理阶段,这么庞大的配置量,刀具成本控制是个难题。壁如:覆盖件模具加工类型宽泛,包括了车身覆盖件外板、内板件的大、中型模具全工序都有加工; 因模具结构复杂程度不同,仅 3D 型面加工就需要配备多类型、多规格大批刀投入使用; 如果为了满足复杂模具加工的需求,配置数量过多的刀具,平衡各种类型模具加工时就会造成大量刀具闲置; 反过来如果尽量使配置刀具数量最小化,成本虽然降低了但却满足不了复杂模具的批量加工需求 (见图 4、图 5)。
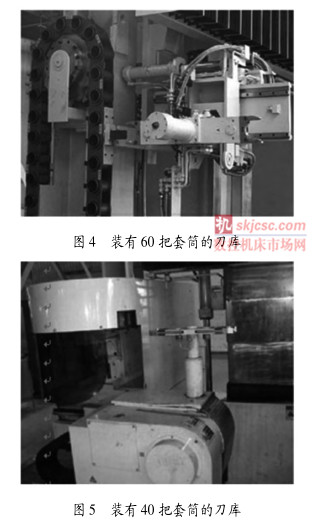
解决上述问题的思路是: 各工序模具 3D 自动化加工对刀具配置的需求量和刀具成本控制要找到一个平衡点,同一种类不同规格刀具数量配置比例要达到相对合理。从这两个角度入手上述问题可以解决。
2. 3D 自动加工配置刀具成本控制的解决方案
通过 3D 自动化加工试验,我们制定科学的刀具选用原则和刀库选刀方式具体解决刀具库配置和刀具成本控制等问题。
自动加工刀具选用原则归纳为以下三点: ①为保证刀具高的寿命和可靠性能,选用的刀具需由高效率、高性能、寿命长的材料制成。②选用镶装刀片结构的刀具更适合自动化加工。③实施高速自动化加工时要选用动平衡性能好的刀具。
按此选刀原则我们为 3D 自动化加工配置的精铣刀具实现了模具铸铁材料型面连续切削三十几个小时的目标,减少了每台机床不同规格相同伸长精铣刀具的配置数量。仅此一项五台加工中心刀具库共节省 15 把 30 球刀的配置量,节约成本约 5 万元。试验中我们确定用两种刀库选刀方式实施分析验证,分别为顺序选刀方式和任意选刀方式。
(1) 顺序选刀方式
严格根据工序的先后顺序依次将刀具安放在刀具库中,调用时按模具加工顺序逐一取出使用; 它的优点是控制简单,工作可靠;缺点是刀具库刀具配备数量较多,机床更换模具部件加工时机床刀具库必须重新排列刀具,频繁地配刀和排列刀具,导致人为错误产生几率加大,给 3D自动化加工带来极大的安全隐患。
(2) 任意选刀方式
是根据程序指令的要求任意选择所用刀具,刀具在刀具库中固定刀号存放,利用控制系统来识别、记忆所有刀具和刀座。其优点是相同的刀具在工件一次装夹中可重复使用,因此刀具数量较合理,自动换刀装置通用性强、应用范围广。
通过两种方式对比分析,考虑我公司模具加工实际情况,我们确定任意选刀方式用于 3D 自动化加工。根据 3D 自动化加工试验数据分析验证结论和大批量模具加工刀具使用频率的分析结果,我们为机床刀具库配置了一定数量的固定刀具,另外在刀具库中还预留多个刀座位置动态配置部分刀具,方法是: 用一套公用刀具供五台加工中心随机选用,节省了另外 4 台加工中心同类型刀具的配置成本; 此方法成功地避免了使用频率较低刀具的闲置现象发生,从而达到了刀具成本控制的目的。通过近一年的运行,运用现场 3D 自动加工数据统计分析和刀具使用频率分析等方法,对机床刀具库实施了刀具规格小范围的调整,使公司 5 台数控加工中心刀具库刀具配置达到了相对合理状态。
3. 刀具在线识别和刀具寿命管理标准化问题原因分析
刀具库配置完成后,如何做到刀具配置标准化管理,又成了 3D 自动化加工的另一难题。实际上大家极易忽略的是刀具在线切削状态控制 (即为刀具自动识别) 和自动加工过程中刀具寿命管理标准化等问题对无人加工的影响,这些问题不解决,会导致模具加工质量问题频繁发生。
刀具初次装入刀具库前已经实施了刀具静态检测,保证刀具各项指标都在标准范围内,这方面容易控制; 大型复杂模具 3D 自动无人加工时间最长可达100 多小时,3D 自动加工过程中刀具磨损、崩刃、折断,切削缠绕、切削振颤、刀具跳动等均属于加工在线切削状态,如何做到能够在加工过程中自动识别和准确判断上述情况并作出对应的自动安全回应呢? 这些又是 3D 自动加工中需要重点解决的问题之一。
4. 刀具在线识别问题的解决方案
首先针对刀具库中各类型所有规格的刀具定义出对应在线加工状态下刀具变化限定值和限定范围;对不同形式的刀柄端面间隙做出互换设定; 限定和设定依据则是刀具性能和模具加工材料、机床主轴功率等技术参数,另外要参考以往积累的模具加工参数、刀具切削参数的经验数据库用于以上限定值的制定; 依据限定值编制出不同数控控制系统的机床宏程序,通过控制系统和机床刀长检测装置完成对刀具自动识别的工作,实现自动加工过程中对刀具磨损、崩刃、折断的线判断和安全回应 (见图 6、图 7)。
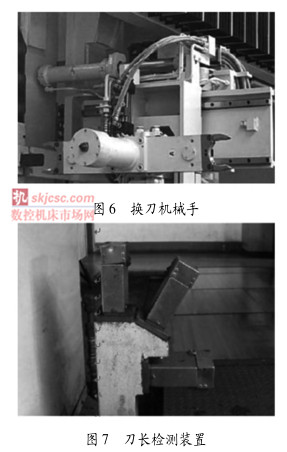
5. 刀具寿命管理阶段问题解决刀具寿命管理包括刀具装配标准规范、刀具更换标准、刀具库管理流程规范及无过错定义刀具等。
(1) 在线自动检测刀长实施补偿报警问题的解决方案
我公司 3D 自动化加工试运行初期,在线自动检测刀长实施补偿遇到瓶颈。主程序空运行试切(模拟运行) 时两台机床均出现了多把甚至是十几把刀具频繁报警的情况,经过排查,找到了问题的主要症结: 刀具装配超出了主程序中设定的有关刀具长度等的限定范围,超差仅为百分之几都会报警。经过分析有两点主要原因: 一是配刀沿用非自动加工的刀具装刀方式,没有按自动加工配刀标准执行;二是刀具库装刀后测量工具和测量方法不完善。
解决方法: 首先根据我公司实际情况制定刀具装配公差范围标准,同时制定严格的配刀管理制度来实施刀具装配阶段的过程控制。再则通过技术改善,提高刀具装配准确率。公司刀具配送和测量中心具体实施自动化刀具的装配和测量工作,其中有两个环节最容易导致刀具伸长装配误差,一是刀体与刀柄的装配均为人工操作,二是整体钨钢刀刃部磨损后要通过热夹方式多次更换装配。我们通过设计制造装刀辅助工具配合标准量具实施刀具装配,使 3D 自动加工刀具装刀和刀长限定均做到了在标准范围之内; 经过 3 个月的实施推动,完全消除了自动检测刀长实施补偿时出现报警的问题。
(2) 刀具更换标准难确定问题原因分析及解决方案
3D 自动加工刀具更换依据和标准不好确定,镶片刀刀片和整体钨钢刀磨损量是以加工时间为准还是以磨损情况为准? 检测手段是以设备检测数据为准还是以目视检测破损程度为准? 如果每次自动加工结束后都把所有刀具从刀具库取下来送到刀具测量中心检测,一台检测设备根本无法在规定时间内检测完成;如果自动化加工前没有制定出完善的刀具检测更换标准和管理制度,就会有刀具检测更换不及时情况发生,将直接影响 3D 自动加工模面质量。
解决方案: 制定数控加工中心自动化加工刀具日点检制度,加工结束后由机床检查刀具情况 (见图 8),精加工刀片即刻更换,用于多刀清角的钨钢刀根据加工时间标准进行及时更换。磨损的钨钢刀和刀片由配送中心实施检测,磨损量在规定范围内的刀具将用于半精铣和单刀清角; 刀具检测中心实施待更换刀具的装配和配送,并配合机加工人员用对刀座号的方法准确将刀具放置到机床刀具库中。
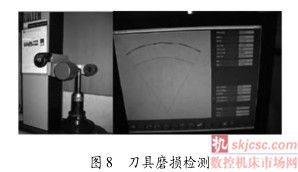
(3) 全程刀路无过切过程阶段问题— — —动态刀
具定义易产生错误的解决方案前面提到,为了合理控制刀具成本,我们采用的是刀具库固定一定数量刀具结合批量刀具动态管理的方式管理刀具库;
其中采用的任意选刀方式,避免了机床刀具库使用频率较低刀具的闲置问题,降低了刀具成本。可是此种模式中公用刀具需要编程员人为动态选取并命名刀具号,要求编程员对动态刀具定义必须完全正确。
刀具库固定刀具已在软件中设定成库直接调用,动态刀具则需要编程员在库中调用后重新定义刀具号,有了人为操作就不可能达到真正 100% 无过错;尽管编程制定了刀具定义的标准也实施了培训,但在 3D 自动化运行两年的时间里还是出现了因动态刀具定义错误、动态刀具号定义重复问题导致模具型面局部过切的问题发生。
解决方案: 开发刀具批定义软件,限定固定刀具号范围和动态刀具号范围,通过软件方式自动识别过滤掉重复刀具号和错误刀具号; 这一改善去除了刀具定义环节的人为操作,通过自动方式生成了动态刀具,具体实施后彻底解决了此问题。
三、结语
3D 自动化加工在日本等国外大型汽车模具公司应用较普遍,国内仅有一汽模具和一汽丰田模具等个别大型企业真正实现了 3D 自动化加工。一些企业自动加工试运行阶段因过程控制手段不完善,频繁出现过程问题点,导致模具数控加工效率下滑,故而中止了自动加工试验和开发。
我公司在 3D 自动化加工试运行阶段对本文提到的过程控制问题点制订出有效的解决方案,做到了3D 自动化加工在试运行阶段就能够稳定运行; 在保证提高加工效率和加工质量的前提下,我们通过科学数据统计、任意选刀等方法的应用,做到了合理配置自动加工刀具库,避免了闲置刀具问题发生,使刀具成本得到了很好的控制。
目前我公司 3D 自动化加工平稳运行已经超过了两年的时间,机加车间五台数控加工中心实现了真正意义上的 3D 型面无人值守加工。尤其节假日(长、短假期),周六周日和中夜班等时段,机加车间都合理安排加工中心实施 3D 型面无人值守加工,在提高数控机床劳动生产方面发挥了优势作用。
投稿箱:
如果您有机床行业、企业相关新闻稿件发表,或进行资讯合作,欢迎联系本网编辑部, 邮箱:skjcsc@vip.sina.com
如果您有机床行业、企业相关新闻稿件发表,或进行资讯合作,欢迎联系本网编辑部, 邮箱:skjcsc@vip.sina.com
更多相关信息