刀具涂层技术现状与发展趋势
2015-1-19 来源:数控机床市场网 作者:田伟
摘要: 切削刀具表面涂层技术是近几十年应市场需求发展起来的材料表面改性技术。采用涂层技术可有效提高切削刀具使用寿命,使刀具获得优良的综合机械性能,从而大幅度提高机械加工效率。本文对涂层刀具类别、性能及涂层材料进行了介绍,对常用的涂层方法及一些新的涂层方法进行了阐述,并对涂层技术的国内外现状和发展趋势进行了综合分析与介绍。
关键词: 刀具; 涂层; 现状; 发展
1 引言
刀具涂层技术(在刀具材料表面涂覆高硬、耐磨、耐高温薄层的技术)是近几十年应市场需求发展起来的材料表面改性技术,采用涂层技术可以有效解决刀具材料的硬度、耐磨性和抗弯强度、冲击韧性之间的矛盾,有效提高切削刀具使用寿命,使刀具获得优良的综合机械性能,从而大幅度提高机械加工效率。涂层技术以其效果显著、适应性好、反应快等特点,对刀具性能的提高和切削技术的进步发挥十分重要的推动作用,被称为切削刀具制造领域的三大关键技术之一。
为满足现代机械加工对高效率、高精度、高可靠性的要求,世界各国制造业对涂层技术的发展及其在刀具制造中的应用日益重视。刀具涂层技术迅速发展,涂层刀具得到了广泛应用。目前工业发达国家涂层刀具已占 80% 以上,其 CNC 机床上所用的切削刀具 90% 以上是涂层刀具。本文对涂层刀具、涂层方法及涂层技术的国内外现状和发展趋势做了综合的阐述与介绍。
2 涂层刀具
涂层刀具是在强度和韧性较好的硬质合金或高速钢基体表面上,利用气相沉积方法涂覆一薄层耐磨性好的难熔金属或非金属化合物(也可涂覆在陶瓷、金刚石和立方氮化硼等超硬材料刀片上)而获得的。涂层作为一个化学屏障和热屏障,涂层刀具的构成减少了刀具与工件间的扩散和化学反应,从而减少了月牙槽磨损。涂层刀具具有表面硬度高、耐磨性好、化学性能稳定、耐热耐氧化、摩擦因数小和热导率低等特性,提高刀具寿命 3 - 5 倍以上,提高切削速度 20% -70%,提高加工精度 0.5 -1 级,降低刀具消耗费用 20% -50%。
涂层刀具有四种:高速钢涂层刀具,硬质合金涂层刀具,以及在陶瓷和超硬材料(金刚石或立方氮化硼)刀片上的涂层刀具。前两种涂层刀具使用最多。在陶瓷和超硬材料刀片上的涂层是硬度较基体低的材料,目的是为了提高刀片表面的断裂韧度(可提高 10% 以上),减少刀片的崩刃及破损,扩大应用范围。
2. 1 高速钢涂层刀具
高速钢是综合性能较好、应用范围最广的一种刀具材料。热处理硬度达 62 -66HRC,抗弯强度约3.3GPa,耐热性为 600℃左右,此外还具有热处理变形小、能锻造、易磨出较锋利的刃口等优点。高速钢的使用占很大比例,特别是用于制造结构复杂的成形刀具。例如各类孔加工刀具、铣刀、拉刀、螺纹刀具、切齿刀具等。
高速钢涂层刀具一般采用物理气相沉积(PVD)方法,常用的涂层材料有 TiN 和 TiC。TiC 的硬度较高(可达 3200HV 左右,抗磨损性能好,适用于涂覆产生剧烈磨损的刀具;但它性脆,膜层内部的内聚力相对较低,并且在 300℃ 的低温下就会开始分解。TiN 的硬度 ( 可达 2000HV,相当于 80 -85HRC)虽比 TiC 低,但其化学稳定性好,与金属的亲和力小,摩擦系数低,润滑性好,在空气中抗氧化性能比 TiC 好,刃口无倒圆,切削时可大大减少刀具的摩擦和磨损,防止黏结与冷焊,并且涂层呈金黄色、外观好,因而是一种较理想的涂层材料。
江苏某机械制造厂在 48 × 39.5 × 8 和 60 ×50. 5 ×10 两把高速钢花键滚刀上采用 TiN 涂层后,其耐用度比涂层前的滚刀提高了 5 - 7 倍。上海工具刃具厂使用 TiN 涂层后的高速钢拉刀耐用度可比未涂层的拉刀提高 5 - 10 倍,而且加工出孔的表面粗糙度值也较小。成都工具研究所对高速钢涂层刀具作断续冲击切削实验,结果表明其寿命比未涂层刀具提高 3 -5 倍。因此涂层刀具不但适用于连续切削加工的刀具,也适用与铣刀、插齿刀等断续切削工作的刀具。但应指出,TiN 涂层刀具一般不适用来加工钛合金材料,否则涂层与工件材料之间会产生化学反应,从而影响使用效果。除上述两种涂层材料外,还有新的涂层材料:TiCN、TiAlN、AlTiN、TiAlCN、DLC(类金刚石类涂层)等。它们各有特点。
TiCN 复合涂层:蓝—灰色,耐热高温达 400℃。有高韧性,可用于丝锥、成形刀具。TiAlN 高性能涂层:紫罗兰—黑色,耐热高温达800℃,可适用高速加工。在基体 65HRC 的高速钢上涂 2. 5 -3. 5μm,刀具寿命比 TiN 明显提高约 1 -2 倍,但涂层费用较高。
AlTiN 高铝涂层:耐热温度达 800℃,有高硬度、高耐热性,适合对硬材料加工。TiAlCN 复合涂层:耐热温度达 500℃,有高韧性、高硬度、高耐热性、低摩擦性能,适合制造铣刀、钻头、丝锥。可加工 60HRC 的高硬度材料。DLC 涂层:耐热温度 400℃,适用于加工硬木材的成形刀具。
2. 2 硬质合金涂层刀具
硬质合金是由高硬度、难熔的金属碳化物(WC、TiC 等) 微米级粉末采用 Co、 Mo、 Ni 等作粘结剂烧结而成的粉末冶金制品,其高温碳化物含量超过高速钢,允许的切削温度高达 800 -1000℃,常温硬度达 89 - 93HRA,在 540℃ 时为 82 - 87HRA,与高速钢常温时硬度(83 - 86HRA)相同,760℃ 时硬度达 77 -85 HRA,并具有化学稳定性好、耐热性高等优点。硬质合金刀具切削速度可达 100 - 300m/min,远远超过高速钢,寿命是高速钢的几倍到几十倍。发达国家 90% 以上的车刀和 55% 以上的铣刀都采用硬质合金材料制造,目前使用比重仍在增加。另外,硬质合金也用来制造钻头、铣刀、齿轮刀具、铰刀等复杂刀具,硬质合金以其优良的性能正在更多的场合替代其他的刀具材料,现在已成为主要的刀具材料之一。
涂层硬质合金早在 20 世纪 60 年代已出现。采用化学气相沉积(CVD)方法,在硬质合金表面涂覆一层或多层(5 - 13μm)难熔金属碳化物。涂层合金有较好的综合性能, 基体强度韧性较好,表面耐磨、耐高温。但涂层硬质合金刃口锋利程度与抗崩刃性不及普通硬质合金。目前硬质合金涂层刀片广泛应用于普通钢材的精加工、半精加工及粗加工。
1969 年德国克虏伯公司和瑞典山特维克公司研制的 TiC 单层涂层硬质合金刀片首次投入市场后,世界各国都进行了研制、生产。瑞士巴尔查斯涂层公司的 Baliniti 系列产品,丹麦尤尼莫克公司的 C1 -C5 及 C7Plus(涂层材料为 TiAlSiN)系列产品和日本日立公司号称跨世纪水平的 CrSiN、 TiSiN 等新型刀具涂层材料都代表了世界的先进水平。国内, 成都工具研究所开发了国内首创的 TiCNOAl 和 TiCNB两个系列共 3 种高性能多元复合涂层;贵阳工具厂也研究开发了种类齐全的 PVD 涂层刀具产品。目前,硬质合金涂层材料已由早期的 TiC (1969 年)、TiN(1971 年)、Al2O3(1972 年) 等单涂层发展到TiC—TiN,TiC—Al2O3等双涂层及 TiC—TiN—Al2O3等三涂层,最多的可达 13 层涂层(如联邦德国的Widalon 刀片),它们的特点:TiC 涂层具有很高的硬度与耐磨性,抗氧化性好,切削时能产生氧化钛薄膜,降低摩擦系数,减少刀具磨损,切削速度可提高 40%左右。TiN 涂层在高温时能形成氧化膜,与铁基材料摩擦系数较小,抗粘结性能好,能有效降低切削温度。TiN 涂层刀片抗月牙洼及后刀面磨损能力比TiC 涂层刀片强,适合切削钢与易粘刀的材料,加工表面粗糙度较小,刀具寿命较好,此外 TiN 涂层抗热振性能也较好。
TiC—TiN 复合涂层:第一层涂 TiC,与基体粘结牢固不易脱落。第二层涂 TiN,减少表面层与工件的摩擦。
TiC—Al2O3复合涂层:第一层涂 TiC,与基体粘结牢固不易脱落。第二层涂 Al2O3,使表面层具有良好的化学稳定性与抗氧化性能。这种复合涂层能像陶瓷刀那样高速切削,寿命比 TiC、TiN 涂层刀片高,同时又能避免陶瓷刀的脆性、易崩刃的缺点。
3 涂层方法
目前,常用的刀具涂层方法有化学气相沉积法(CVD)、物理气相沉积法(PVD)、等离子体化学气相沉积(PCVD)、盐浴浸镀法、等离子喷涂及化学涂敷法等,其中以 CVD 和 PVD 应用最为广泛。
3. 1 化学气相沉积法
CVD(即化学气相沉积法)是利用金属卤化物的蒸气、氢气和其它化学成分,在 950℃ -1050℃高温下,进行分解、热合等气固反应,或利用化学传输作用,在加热基体表面形成固态沉积层的一种方法。其工艺原理如图 1 所示,在常压或负压的沉积系统中,将纯净的 H2、CH4、N2、TiCl4、AlCl3、CO2等气体按沉积物的成分,将其中的有关气体按一定配比均匀混合,依次涂到具备一定温度(一般为 1000 -1050℃)的硬质合金刀片表面,即在刀片表面沉积TiC、TiN、TiCN、Al2O3或它们的复合涂层。
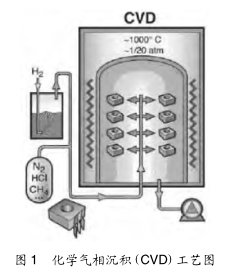
1969 年德国克虏伯(Krupp)公司和瑞典山特维克(Sandvik)公司研发成功了化学气相沉积(CVD)涂层技术,并向市场推出了 CVD TiC 涂层硬质合金刀片产品。此后,美国、 日本和其他国家也相继推出 CVD 涂层硬质合金刀具。40 年来,CVD 涂层技术不断发展,改进了基体材料和涂层工艺,使用多种和多层涂层材料,出现了第二代、第三代直至第五代、第六代涂层刀具产品。CVD 涂层工艺温度约为1000℃,结合力可靠,但也带来了一些性能上的缺陷,如刀具切削刃需经过钝化预处理,刀具表面易出现残余拉应力,且不能用于高速钢刀具表面涂层。可通过降低工艺温度,改变基体材料组份,改进切削刃钝化方法,使 CVD 涂层硬质合金的性能得到提高。
3. 2 物理气相沉积法
PVD(即物理气相沉积法)是指在真空条件下,采用低电压、大电流的电弧放电技术,利用气体放电使靶材蒸发并使被蒸发物质与气体都发生电离,利用电场的加速作用,使被蒸发物质及其反应产物沉积在工件上。物理气相沉积法与化学气相沉积法类似,只不过物理气相沉积是在 500℃ 左右完成的。PVD 涂层技术过去主要用于高速钢刀具,而近年来随着 PVD 涂层技术飞跃发展,也成功用于硬质合金刀具,占领了硬质合金涂层刀具的一半阵地,化学气相沉积法大多是多层涂层,而物理气相沉积法则可以是单涂层与多层涂层, 其工艺原理如图 2 所示。
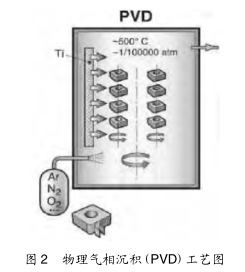
20 世纪 70 年代初,美国本夏(R.Runshan)和拉格胡南(A.Raghuran)研发了物理气相沉积(PVD)工艺,并于1981 年将 PVD TiN 高速钢刀具产品推向市场。欧洲的 PVD 涂层技术水平最高,领先于其他国家和地区。知名的厂商有德国赛利(CemeCon)涂层技术有限公司、欧瑞康巴尔查斯(OerlkonBalz-ers)公司、德国 PVT 等离子真空技术公司和丹麦尤尼莫克(Unimerco)公司等。他们的 PVD 涂层设备和工艺先进,涂层材料品种多,涂层刀具和其他产品使用性能好。
目前 PVD 技术不仅提高了薄膜与刀具基体材料的结合强度,涂层成分也由第一代的 TiN 发展为TiC、TiCN、ZrN、CrN、MoS2、TiAlN、TiAlCN、TiN- AlN、CNx等多元复合涂层,且 ZX 涂层(即 TiN- AlN 涂层)等纳米级涂层的出现使 PVD 涂层刀具的性能有了新突破,这种新涂层与基体结合强度高,涂层膜硬度接近 CBN,抗氧化性能好,抗剥离性强,而且可显著改善刀具表面粗糙度,有效控制精密刀具的刃口形状及精度,其精密加工质量与未涂层刀具相比毫不逊色。
3. 3 新的涂层方法
(1) 等离子体化学气相沉积法
国外采用 CVD 与 PVD 相结合的技术,最新开发出一种低温涂层新工艺,称为等离子体化学气相沉积法(PCVD),它利用等离子体来促进化学反应,可把温度降低至 600 ℃ 以下。由于涂层温度低,在硬质合金基体与涂层材料之间不会发生扩散或交换反应,因而基本上可保持刀片原有的韧性,所涂刀片在铣削普通钢、合金钢时显示出比普通 CVD 涂层法获得刀片有更优异的切削性能。目前 PCVD 法的涂覆温度已可降至 180℃ -200℃,这样低温的工艺不影响焊接部位的性能,因此这种方法还可用在涂覆焊接硬质合金刀具。据报道,日本三菱金属公司在一种焊接硬质合金钻头上采用了 PCVD 法涂层,结果加工钢件时的寿命比高速钢钻头高 10 倍,效率提高 5 倍。
(2) 离子束辅助沉积技术
离子束辅助沉积技术(IBAD) 是一种新兴的PVD 涂层技术。离子辅助气相沉积技术是指在冷相沉积涂层的同时,用具有一定能量的离子束轰击不断沉积的物质,使沉积原子与基体原子不断混合,界面处原子相互渗透溶为一体,从而大大改善涂层与基体的结合强度。它具有气相沉积和离子注入的优点,使沉积温度可以降低到 200℃ - 500℃,因而可以在较低温度下制备 C N、B 化合物、立方氮化硼和金刚石超硬涂层,可用于因结合力欠佳而难以涂层的硬质合金。
4 涂层技术现状与发展趋势
欧洲刀具涂层技术自 20 世纪 80 年代中期以来得到了广泛的发展,尤其是物理涂层技术,代表了当前世界的最高水平。纵观涂层技术的发展现状,欧洲的 PVD 涂层技术水平最高,领先于其他国家。知名的厂商有德国、瑞士、丹麦等的专业涂层技术公司。这类公司从涂层设备、涂层工艺、涂层材料等各方面领先世界,涂层刀具产品使用性能远远好于国内。国外知名工具厂大多使用购自涂层专业技术公司的涂层设备和最新工艺,而不是自行研制。这也使得欧洲的专业涂层技术公司研发新型涂层能力更强,水平更高,更具针对性。值得关注的是,国外高效高性能齿轮刀具等精密复杂高速钢刀具几乎100%需要经过涂层后使用,而中国不仅刀具涂层技术有很大差距,涂层刀具的数量也差得很远,精密复杂刀具采用涂层后使用的不足全部刀具 20%。
国内 PVD 技术的研发工作始于上世纪 80 年代初,80 年代中期研制成功中小型空心阴极离子镀膜机及高速钢刀具 TiN 涂层工艺技术。由于对刀具涂层市场前景看好,国内引进了热阴极离子镀及阴极电弧(多弧)离子镀技术与装备。技术及装备的引进推动了国内刀具 PVD 技术的第一次开发热潮,并于 90 年代初开发出多种 PVD 设备。但由于大多数的设备性能指标低,涂层工艺稳定性差,预期的市场效益未能实现,从而导致了近十多年国内刀具 PVD技术处于徘徊不前的局面。尽管 90 年代末国内成功开发出了硬质合金 TiN—TiCN—TiN 多元复合涂层工艺技术,并达到了实用水平,但在随后的发展过程中也并未得到市场认可。随着我国汽车工业的迅速崛起。先进制造技术的大量引进,以及数控加工技术大面积的普及。自本世纪初,PVD 技术在国内掀起了第二次开发热潮。与 90 年代不同,目前国内PVD 技术的发展更具多元性及创新性,归纳起来有以下几种类型:阴极电弧技术、磁控溅射技术、空心阴极技术等。
目前国际上刀具涂层技术正处在一个重要的更新换代时期。涂层结构已从单元和多元单层涂层向多元多层涂层和纳米晶复合涂层方向发展,这些新型涂层显著提高了刀具的硬度、 结合力和抗氧化性等重要性能。同时,基于加工材料和不同加工工况的专用涂层的研究也在深入开展。“硬” 涂层刀具追求高的硬度和耐磨性,目前应用的刀具硬涂层材料有金刚石、类金刚石、氮化碳、立方氮化硼以及TiC、TiN、TiCN、Al2O3、TiAlN 等及其组合,其中以黄金色的 TiN 涂层的应用最为广泛。然而,诸如航空航天工业使用的许多高强度铝合金 钛合金或贵金属材料等都不适合用 “硬” 涂层刀具加工,仍主要使用无涂层的高速钢或硬质合金刀具 。“软” 涂层刀具的开发则可较好地解决此类材料的加工问题,刀具“软” 涂层的主要成分为具有低摩擦系数的固体润滑材料,如: MoS2、WS2、CaS2、TaS2等,在特殊使用条件下具有优良的摩擦学特性,如: 摩擦系数低、承载极限高、高温下化学稳定性好、物性变化小、能适应 1200℃以上的工作温度范围和很宽的摩擦副运动速度范围,适于在高温、高速和大载荷等特殊环境条件下使用。目前“软” 涂层刀具技术在国内研究较少,但“软” 涂层刀具可应用于干切削,对阻止粘结、减小摩擦、提高刀具寿命、降低加工成本等具有重大的理论和实际意义,具有广阔的应用前景。
结合当前涂层技术日益重要的地位和广泛的市场需求,在吸取先进技术和设备的基础上发展拥有自主知识产权的工业化涂层技术及设备具有极大的现实意义,这不仅需要刀具行业加强对涂层技术的重视程度,增加对涂层技术开发的投入,同时也需要大专院校与刀具企业加强沟通和交流,只有将市场、企业、院校有机地结合起来才会使国内刀具涂层技术健康的发展。
5 结语
介绍了涂层刀具的类别、性能及其应用情况,并对高速钢涂层刀具、硬质合金涂层刀具及其对应的涂层材料进行详细阐述;对常用的刀具涂层方法(如化学气相沉积法、物理气相沉积法等)进行了论述,对等离子体化学气相沉积法及离子束辅助沉积技术两种新的涂层方法进行了介绍;对国内外涂层技术的现状及发展趋势进行了分析。纵观刀具涂层技术与设备的研发与应用的国内外现状,该行业所体现的市场经济专业细化分工的特征极为明显。尖端技术主要掌握在有限的几家公司,但随着应用领域的不断拓展,国内企业在引进设备的同时,积极开发自主的涂层工艺仍不失为一个明智的选择,否则在涂层技术的推广应用方面必将受到垄断价格的影响,从而丧失产品的市场竞争力。
投稿箱:
如果您有机床行业、企业相关新闻稿件发表,或进行资讯合作,欢迎联系本网编辑部, 邮箱:skjcsc@vip.sina.com
如果您有机床行业、企业相关新闻稿件发表,或进行资讯合作,欢迎联系本网编辑部, 邮箱:skjcsc@vip.sina.com
更多相关信息