微量润滑条件下 BTA 钻杆振动特性分析
2018-5-16 来源:转载 作者:李 波,苗鸿宾,沈兴全
摘要: 研究了深孔加工微量润滑条件下,BTA 钻杆的振动机理。结合理论分析,建立了钻杆振动有限元模型,利用 ANSYA 软件对微量润滑条件下深孔钻杆振动特性进行数值模拟。所得结论对BTA深孔加工的动态稳定性研究与深孔加工工艺的优化具有理论和实际意义。
关键词: 微量润滑; BTA 钻杆; 深孔加工; 振动
0、 引言
BTA 深孔钻是一种内排屑的钻削系统,钻孔过程中钻杆深入工件内部,切削液通过钻杆与工件间隙进入切削部位,通过钻头的排屑口进入钻杆内孔,最终通过钻杆的排屑孔排到外部。随着绿色制造技术的发展,加工过程中关于质量、费用和环境的问题引起了人们的关注。微量润滑是利用空气和液体的混合物来代替传统的油液润滑和冷却,利用微量润滑技术可以有效降低费用且绿色环保。研究微量润滑代替传统的油润滑成为目前的热点,闫鲁涛等研究了微量润滑对铣削力及刀具磨损的影响。石世发等研究了微量附水滴润滑在深孔加工中的应用。Bruce 等对微量润滑技术在自动化加工中的应用优势及所面临的关键技术问题进行了分析。Kishawy 等通过普通油液润滑、干式切削、微量润滑切削的实验对比验证了微量润滑的加工优越性。在深孔特殊的加工环境下,由于所采取的流体介质不同,在钻削过程中对钻杆的振动特性产生不同的影响。钻杆的振动将对工件的加工精度及刀具寿命产生直接的影响,周建东等通过在曲轴深孔加工过程中运用微量润滑技术,验证了这种绿色加工方法的可行性和实用性。Gessesse 等通过实验研究了在深孔加工过程中钻杆的振动与孔螺旋的关系。Ahmadi 等分析了钻削过程中不同形式的振动对刀具磨损的影响。笔者针对微量润滑条件下的钻杆振动问题,建立了有限元模型,分别以钻杆长度和切削液阻尼对钻杆振动的影响进行了分析。
1 、钻杆有限元模型
1. 1 模型建立
由于深孔加工过程中钻杆处于复杂的工作环境中,为了便于对其进行数值分析,进行了相应的简化,假设: 钻杆简化为均质弹性梁; 将钻杆看作一端简支,另一端承受钻削压力并滑动; 工件内孔为钻杆横向运动的约束边界,且钻杆轴线与工件内孔轴线重合; 相对于较长的钻杆部分,钻头处理为具有转动惯量的质量点。钻杆振动模型如图 1 所示。
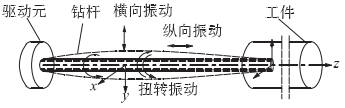
图 1 钻杆振动模型
1. 2 计算单元
利用 ANSYS 有限元分析软件对钻杆进行实体建模,选取 PIPE59 单元模拟钻杆。PIPE59 单元可承受拉、压、弯及流体动力作用,可以有效分析在切削液作用条件下钻杆的真实受力状况。并可以通过对钻杆内外流体密度进行设定,通过定义附加质量系数来考虑内外流体对钻杆振动的影响。采用自由网格划分方法,定义单元大小为 2mm,单元的刚度矩阵和质量矩阵与梁模型单元的刚度矩阵和质量矩阵相似。
1. 3 计算条件
以深孔加工中心的 BTA 深孔钻杆为研究对象,由实际参数对其进行有限元模型建立。钻杆与切削液的参数如表 1、表 2 所示。
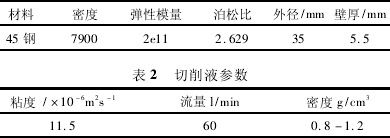
表 1 钻杆参数
不可压缩的流体通过空心钻杆,流体的运动特性取决于的雷诺数的值:
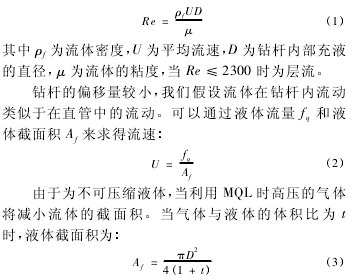
将表 1 与表 2 相应参数代入公式( 3) 和公式( 2)中分别求得切削液体截面积与切削液流速,将所求结果代入公式( 1) 中所得雷诺数 Re 范围远小于 2300,切削液在钻杆内部为层流流动。根据钻杆长度,切削液密度对钻杆纵向、扭转和横向振动特性进行分析。
2 、计算结果及分析
2.1 钻杆纵向振动
在钻削过程中钻杆沿其纵向的伸缩运动称为纵向振动。钻头与工件接触产生的垂直振动频率为钻杆固有频率的整数倍时,钻杆将处于共振状态,产生钻削时钻杆的纵向振动。根据所给模型分别探讨钻杆长度和切削液密度对钻杆纵向振动的影响。
2.1.1 钻杆长度对纵向振动的影响
图 2 为钻杆前 3 阶固有频率计算结果,由图中可以看出,钻杆纵向振动受钻杆长度变化影响较大。根据数据,钻杆长度由1500mm增加到 2500mm时,第3阶固有频率由 22. 6Hz 变化到16.2Hz,转换为钻杆转速为 216 ~ 155 r /min,微量润滑钻削时钻杆钻速一般位于 160 ~ 210 r /min,位于 155 ~ 216 r /min转之间,钻杆极易产生纵向振动。
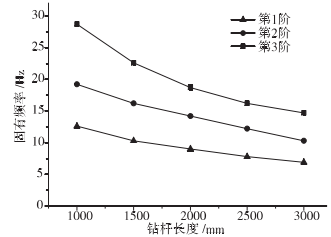
图 2 钻杆长度对钻杆纵向振动影响
在深孔加工中心进行钻削加工时,当钻杆转速为190 ~ 210 r / min时,位于 155 ~ 216 r / min的临界转速范围内。由现场的加工情况来看,钻杆振动加剧,所加工工件精度降低,这正是由于钻杆产生纵向共振引起的。
2.1.2 切削液密度对纵向振动的影响
图 3 显示了切削液对钻杆振动的影响,图中可以看出普通切削油液润滑时,纵向振动的固有频率比微量润滑时频率低很多。分析可知,切削液密度为 1. 0g / cm3时,第 1 ~ 3 阶固有频率比微量润滑时降低了15% 左右,且切削液密度越高,钻杆的固有频率越低。
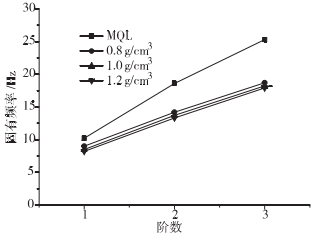
图 3 切削液密度对钻杆纵向振动影响
钻杆在进行轴向进给钻削的时候,钻杆将受到切削液的粘滞作用。根据液体流变原理,密度越高粘度越大,对轴向钻削产生的阻碍会随之增大。钻杆纵向振动固有频率受到切削液的影响,进而对钻杆的纵向振动临界转速产生影响。所以在微量润滑深孔加工时,这种影响需要引起足够的重视。
2.2 钻杆扭转振动
钻杆的扭转振动主要表现为在 BTA 钻头切削过程中,切削刃与工件作用下切削力扭矩产生的交变剪切力经钻头传递到钻杆。当钻杆转速达到某一临界值时,钻杆可能出现扭转共振现象。钻杆扭转共振时,若交变的剪切应力达到较大的数值时,会造成钻杆的疲劳破坏。利用计算模型,从钻杆长度和切削液密度方面考虑对钻杆扭转振动的影响。
2.2.1 钻杆长度对扭转振动的影响
图 4 为计算结果,图中钻杆扭转振动固有频率随钻杆长度的增加而逐渐减小。图 4 中出现了 22Hz 的扭转振动固有频率,转换为钻杆的临界转速为 210r / min,与实际微量润滑钻削加工过程钻杆钻速十分相近,易导致钻杆共振。则在实际钻削加工过程中,根据不同钻杆长度,选择合适的转速,避免扭转共振的发生。
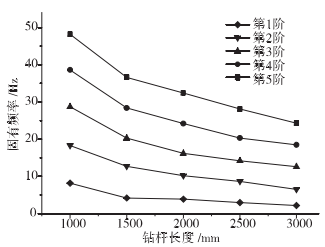
图 4 钻杆长度对钻杆扭转振动影响
2.2.2 切削液密度对扭转振动的影响
考虑微量润滑和不同切削液密度的条件下钻杆扭转振动,其计算结果如图 5。由图中可以看出随切削液密度的变化,钻杆扭转振动的固有频率保持不变。
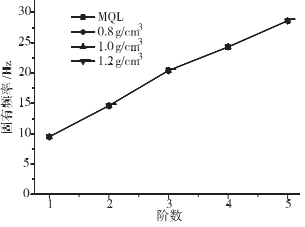
图 5 切削液密度对钻杆扭转振动影响
2.3 钻杆横向振动特性分析
横向振动是指垂直于钻杆轴线方向的振动,在切削液作用下发生横向振动时,由于切削液的迟滞作用,增加了钻杆的横振惯性质量,与钻杆发生耦合振动。由实验统计数据可知横向振动是导致钻削过程失稳,甚至导致工件报废的主要原因。横向共振可以导致共振段钻杆在自转的同时以一定速度绕工件孔轴线进行公转,由此产生的弯曲应力将破坏钻削稳定性。钻杆与工件内壁的周期性碰磨,也将降低被加工工件的精度并加速钻杆的疲劳破坏。选择合适的加工切削参数,避开横向共振频率,是减小钻杆横向振动的关键。采用计算模型,主要考虑钻杆长度和切削液密度对钻杆横向振动的影响。
2.3.1 钻杆长度对横向振动的影响
取其 5 ~ 10 阶时的固有频率值进行比较,振动受钻杆长度的影响如图 6 所示。钻杆固有频率随着长度的增加而明显降低。钻杆长度的变化对横向振动特性影响十分明显。根据计算结果将固有频率转化为钻杆对应的转速,在钻杆钻速为 150 ~ 250 r /min,钻杆长度为 1000mm 时有 5 阶; 钻杆长度为 1500mm 时有 8 阶,钻杆长度为 2000mm 时有 13 阶,钻杆长度为 2500mm时,有 15 阶之多。
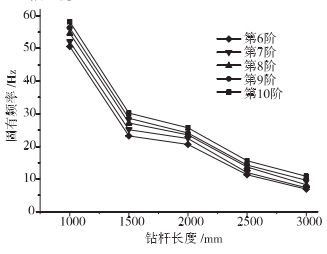
图 6 钻杆长度对钻杆横向振动影响
钻杆横向振动的低阶固有频率数值较小,其固有频率间隔很小,在相同的钻削工况条件下钻杆横向振动特性受其长度变化影响程度较大。采用不同钻杆长度,将引起横向振动固有频率的变化。钻杆越长,横向振动固有频率数值越小,各阶频率间隔也越小,在临界钻速范围内的阶数就会相应增加,钻杆发生横向共振的概率也就越大。这也说明了,在实际深孔钻削加工过程中,钻杆的横向振动是难以完全避免的。
2.3.2 切削液密度对横向振动的影响
考虑微量润滑条件和不同切削液密度条件下钻杆的横向振动计算结果如图 7 所示。由图中可以看出在采用常规切削液润滑时,钻杆横向振动固有频率较微量润滑条件下频率要低许多。切削液密度为 1. 0 g/cm3时,各阶频率比微量润滑时降低了 18. 63% 左右,且钻杆固有频率随切削液密度升高而降低。因此,切削液性能对钻杆横向振动固有频率影响较大,随切削液密度的变化,对钻杆固有频率产生不同程度的影响。
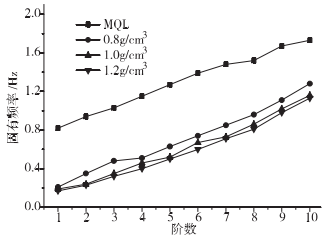
图 7 切削液密度对钻杆横向振动影响
2.4 耦合振动
由于钻杆动态特性表现为非线性,因此在一定条件下,钻杆有可能出现动力失稳现象,发生横向、纵向和扭转的耦合振动,耦合振动对切削加工的稳定性影响较大,因此有必要对耦合振动的发生机理进行研究。
从图 8 可以看出: 在微量润滑钻削中钻杆横向振动 3、5、6 阶固有频率分别等于扭转振动 4、5、6 阶频率,表明当外界激振频率达这 3 种频率时,钻杆发生横向与扭转耦合振动。钻杆的第 3 阶纵向振动和横向振动固有频率与 4 阶扭转振动频率相同,表明当外界激振频率达这 2 种频率时,钻杆将发生 3 种振动形式的耦合振动。因此在设计钻杆和选择切削工艺参数时,要考虑这些参数对钻杆振动特性的影响,以避免耦合振动的发生。
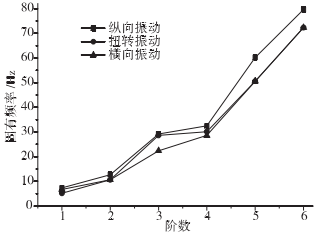
图 8 微量润滑下钻杆三种频率曲线
3、 结论
(1) 分析了深孔钻削过程中切削液流体流动特性,通过雷诺方程说明了在深孔微量润滑钻削加过程工中切削液的流动形式为层流。
(2) 通过对钻杆的振动特性分析,随着切削液密度的降低,导致动态钻削过程中阻尼作用变小,使钻杆固有频率升高振幅增大。
(3) 钻杆纵向振动和扭转振动各阶固有频率数值较大,其间隔也较大,安全转速范围选择较宽; 横向振动低阶固有频率数值较小,且其间隔也较小,安全转速范围较窄。
(4) 钻杆长度对 3 种振动形式的固有频率影响较为明显,各阶固有频率随钻杆变长而逐渐减小,其间隔也随之减小,安全转速选择的范围较窄。
(5) 微量润滑时,容易产生某一个方向的共振,或3 种振动形式的耦合振动,共振产生的交变应力将加剧钻杆的疲劳破坏并影响钻削过程的稳定性。根据钻削加工条件计算不同振动形式的临界转速,进而选择合适的转速可以避开这 3 种临界转速,才能够减少钻杆共振,提高深孔加工过程的稳定性。
来源: 机械工程与自动化学院; 山西省深孔加工工程技术研究中心
投稿箱:
如果您有机床行业、企业相关新闻稿件发表,或进行资讯合作,欢迎联系本网编辑部, 邮箱:skjcsc@vip.sina.com
如果您有机床行业、企业相关新闻稿件发表,或进行资讯合作,欢迎联系本网编辑部, 邮箱:skjcsc@vip.sina.com
更多相关信息