大型深孔加工机床在线检测系统的研究与设计
2018-4-8 来源:广东工业大学 机电工程 佛山新成洪鼎 作者:刘洲 张平 李新涛 张国根
摘要: 目前大型深孔( d > 500mm,h > 80000mm) 现场加工机床的主轴定位均采用手工卡尺测量或是人工打表等方法,针对这些方法不足的问题,文章开发出了一套在线式自动检测与加工一体化装置。该装置运用激光位移传感器在线扫描被加工件内腔轮廓,采用互为基准的自动定心方法,应用双重迭代算法快速得到虚拟轴的空间位置。调整机构的快速响应和检测元件实时的反馈,使得机床主轴与虚拟轴自动调整重合并进行后续加工。在现场的实际应用表明系统很好地满足了便携式镗孔机自动定心要求,极大的降低了工人劳动强度,提高了定心精度和工作效率。
关键词: 在线检测; 自动定心; 迭代算法
0 引言
便携式镗孔机主要应用于大型重工行业,例如: 船舶加工制造业、军事加工制造业、核电产业等大型难加工,且加工精度要求特别高的行业。镗孔加工过程中镗杆轴线的位置决定了加工后孔的位置精度,同时对加工孔的形状精度也有直接影响。目前国内便携式镗孔机的定心方式均采用手动测量、人工估算、手动调整的定心方法,特别是针对有磨损的大型深孔修复时,使用这种调整方法不仅效率低、工人劳动强度大、定位精度差,而且工件加工后易产生废品,导致巨大浪费; 对于空间位置有限深孔或盲孔,受条件限制工人无法安装操作时,这就需要运用自动化手段实现镗孔机自动定心。
因此,开发便携式镗孔机的在线检测自动定心系统是现场加工行业的自动化发展的需求,对现场加工行业的发展有重要的推动作用。
1 、在线检测自动定心系统
依据现场加工环境,以及系统安装条件为了实现便携式镗孔机的自动定心功能,设计如图 1 所示的便携式镗孔机测控系统图。
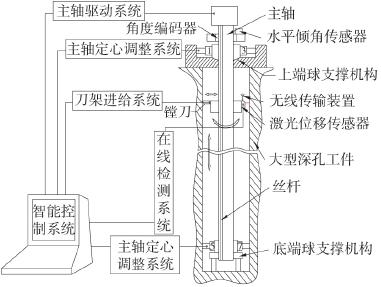
图 1 大型深孔现场加工机床智能控制系统
该机床的在线检测系统采用激光位移传感器的非接触式测量方式,通过多次测量调整来实现自动定心功能。测控系统主要分为三大模块: 数据采集模块、数据处理模块、运动调整模块。数据采集模块: 在选定的测量截面内控制刀架旋转从而带动激光位移传感器圆周运动,完成对工件内腔的圆周扫描,采集得到一组距离数据; 运用无线传输技术将这些数据传输给上位机,并存储在上位机中。通过对多个截面的圆周扫描后,得到多组原始数据点,实现对工件内腔原始数据的采集。
数据处理模块: 上位机对工件内腔原始数据进行合理的运算处理,计算出每个检测截面的圆心位置,然后通过拟合运算拟合出工件内腔的虚拟轴线; 根据内腔虚拟轴线与镗杆轴线的空间位置关系,在上( 下) 调整面内计算出虚拟轴线点和镗杆轴线点的空间位置偏差量。
运动调整模块: 上位机将空间位置偏差量传输给运动控制器,经过运动控制器的运算插补后,将插补信息传输给驱动装置,驱动装置驱使执行部件运动带动镗杆运动,从而实现镗杆的空间位置调整。
便携式镗孔机自动定心过程为: 首先,对进行机械本体各部件进行安装,然后进行测控系统的安装,将水平倾角传感器、激光位移传感器、角度编码器和压力传感器等检测元件以及各执行机构的电气元件同控制系统进行连接,形成一个闭环控制的测控系统。
其次,标定激光位移传感器发光点距主轴轴心的距离为 r0,获取一个原始距离值。以水平倾角传感器检测方向为标准,标定坐标系方向,并建立 O-XYZ 测量坐标最后,通过激光位移传感器对工件原始内腔的逐层旋转扫描如图 2 所示。
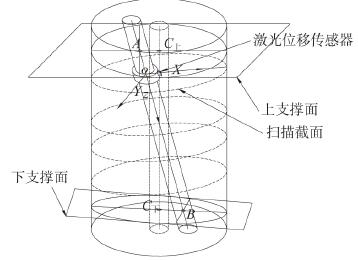
图 2 工件内腔检测模型
获取工件内腔的原始数据; 将得到的每层原始数据运用最小二乘法进行圆形拟合,从而得出每个截面扫描圆的拟合圆圆心及半径; 然后每个截面处拟合的圆心再通过拟合运算,得出虚拟内腔圆柱的轴线; 在调整截面内计算出两轴线与截面相交点之间的位置偏移量和,通过数据和与直线度 d 进行判别比较确定是否需要调整,如若需要调整则通过调整机构实现镗杆自动调整。
经过多次测量、调整后达到定心精度的要求,完成自动定心,然后进行后续加工。2 最小二乘法定心算法根据图 2 所示,工件内腔轮廓扫描过程中将被测工件内腔沿镗杆轴线方向划分为若干个截面,每个截面内在圆周上均分为若干个采样点,则每个采样点的极坐标为:
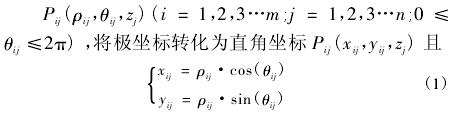
由于工件内腔截面轮廓为非标准圆,取测量截面中第 K 个截面( k≤n) 为研究对象,如图 3 所示。
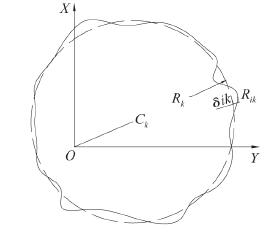
图 3 第 K 个截面扫描图
采样点的位置不可能完全在拟合圆周上,必定会存在误差,设误差为 δik。采用最小二乘法拟合圆曲线 ,其原理如下:
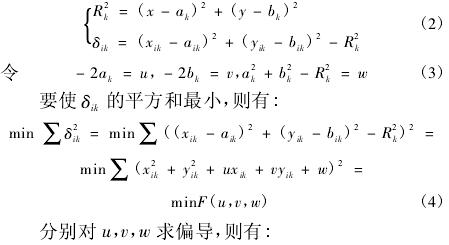
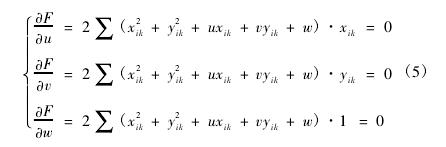
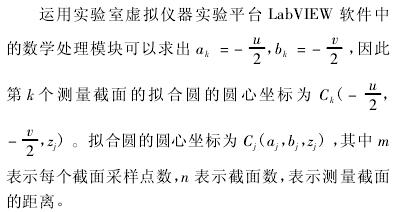
测量 n 个截面可以得到 n 个拟合圆心,将这些拟合圆心值选用最小二乘法进行线性拟合运算,拟合运算后能够得到一条理想空间直线 C上C下,如图 4所示。
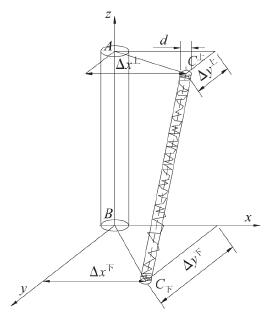
图 4 自动定心模型
直线 C上C下为镗杆所要调整目标的位置轴线,镗杆上下调整面的调整量为 Δx,Δy ,调 整 范 围 量 为C上C下的直线度误差 d,根据调整量使镗杆上下支撑的中心点 A 和点
B 分别与点 C上和点 C下重合,完成一次镗杆的自动调整。
3 、实验分析
运用实验室虚拟仪器实验平台 Lab VIEW 软件,开发测控系统软件 。根据工件内腔建立实体模型,并进行镗杆自动定心模拟实验验证。工件的原始内腔曲面模型可以自行建立,其母线可为直线,斜线,单叶双曲线等,其截面可为圆或是椭圆。本文建立的模型为椭圆斜柱模型,其工件内腔各截面 x轴向半径为 350mm,y 轴向半径,半径偏差范围为,截面个数为,截距为,相对水平面 x 轴向偏角 α = 10°,y 轴向偏角,生成工件内腔原始数据。
并通过原始数据进行多次迭代自动调整模拟,调整过程及结果如图5、图 6 所示:
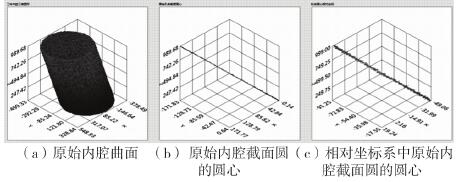
图 5 未调整时原始内腔的三维信息图
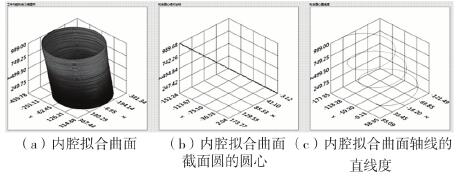
图 6 未调整时拟合内腔的三维信息图
经过三次迭代运算、调整后的图形如图 7 和图 8所示
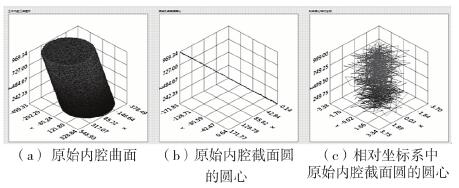
图 7 三次迭代调整后原始内腔的三维信息图
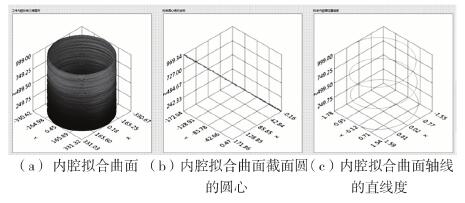
图 8 三次迭代调整后拟合内腔的三维信息图
以建立椭圆斜柱工件内腔模型时的坐标系为绝对坐标系,检测装置在工件内腔内部,沿镗杆方向运动,对工件内腔进行圆周扫描测量从而获得的的原始曲面如图 5a,对原始内腔圆的圆心在绝对坐标下显示如图5b,将原始内腔截面圆的圆心转化为在以镗杆为 Z 轴的相对坐标系下的坐标如图 5c。对原始曲面进行拟合得到内腔拟合曲面如图 6a,把图 6a 中拟合曲面圆的圆心在绝对坐标系中显示如图 6b,将图 6b 中一系列的圆心进行运算,便可得到内腔拟合曲面的圆柱直线度如图6c。
经过合理的处理获得上下端的调整量,根据调整量对镗杆进行模拟调整,一次调整完成后再次进行数据采集、模拟运算然后进行调整。经过三次迭代运算、调整后得到图 7 和图 8 分别对应于图 5 和图 6。为了实现从原始内腔曲面模型的建立到自动运行调整完成的过程中,对测量数据和调整结果进行记录和保存,最终生成检测报告,以便于输出和打。自动检测定心软件可以自动形成表 1,如下所示。
表 1 自动定心实验数据
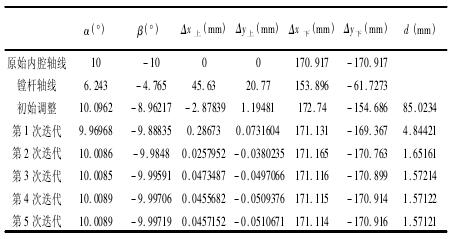
以上实验数据和调整的图形中可以看出,该自动定心系统用于定心时,经过第三次迭代调整后,能够得到很好的定心效果。定心偏差结果如下:
角度偏差:

上端偏差为:
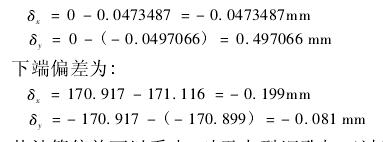
从计算偏差可以看出,对于大型深孔加工过程中通过虚拟软件控制调整,说明该自动定心系统能够很好的实现自动定心要求,并且定心误差能达到 μm 级,实现现场加工设备的高精度检测和精确定位。
4 、结论
综上所述,本文采用互为基准的方法,对便携式镗孔机的自动定心测控系统进行了设计,并通过实验验证,结果表明:
( 1) 该系统能够实现在线检测,快速进行数据处理,定心精度高,系统稳定,操作方便。
( 2) 该系统具有多用性,不仅能用于加工前的系统自动定心,还能够用于加工后被加工工件的质量检测,可以实现定位检测和加工质量检测一体化。
( 3) 运用自动化系统,大大降低了操作人员的劳动强度,提高了工作效率,提升了安全性能。同时也提高了现场加工机械的自动化程度,为其他机械自动化的发展提供了参考。
投稿箱:
如果您有机床行业、企业相关新闻稿件发表,或进行资讯合作,欢迎联系本网编辑部, 邮箱:skjcsc@vip.sina.com
如果您有机床行业、企业相关新闻稿件发表,或进行资讯合作,欢迎联系本网编辑部, 邮箱:skjcsc@vip.sina.com