蒸汽发生器管板深孔钻加工及清洗防护
2018-1-2 来源: 中国一重大连加氢反应器制造有限公司 作者:李占伟
【摘 要】蒸汽发生器是核岛内的主设备之一,是压水堆核电厂一回路、二回路的边界,它将反应堆 产生的热量传递给蒸汽发生器二次侧,产生的蒸汽经一、二级汽水分离器干燥后推动汽轮发电机发电,管板又是蒸汽发生器一二次侧的压力边界,其中管板钻孔是整个蒸汽发生器制造的关键工序,本文主要介绍蒸汽发生器管板深孔钻加工过程、注意事项以及加工后清理防护,以保证后序穿、焊换热管的顺利进行。
【关键词】蒸汽发生器管板 深孔加工 钻头 过程控制 清洗防护
1 、前言
“十三五”期间,国家将大力推进核电站的建设,蒸汽发生器是压水堆核电厂一回路、二回路的枢纽,它将反应堆产生的热量传递给蒸汽发生器二次侧,产生蒸汽推动汽轮机做功。管板又是分隔蒸汽发生器一次侧、二次侧介质的屏障,管板是蒸汽发生器中一二次侧压力边界的一部分。蒸汽发生器管板与换热管之间采用全长度胀管加端部密封焊由此来保证管子与管板间的密封性,消除管子与管板的间隙。
因此,对于蒸发器管板孔的孔径公差、孔距公差、形位公差及孔的粗糙度要求都很高。[1]某项目蒸汽发生器管板本体是 18MND5 低合金高强度钢锻件,最终加工后的厚度为 576mm,属于超厚锻件,管板一次侧与堆芯冷却剂接触的表面堆焊一层 INCONEL600 镍基隔离层,厚度约为 9mm,需要加工 8948 个 19. 28 的换热管孔,因此,深孔钻成为了蒸汽发生器制造的关键工艺,也是决定管板制造周期的重要因素。
2、BTA 深孔加工的特点
由于蒸发器管板孔直径为 19. 28( - 0. 03,+ 0. 07) mm,粗糙度要求 Ra6. 3,尺寸及粗糙度要求较高,对于机床的加工精度提出较高要求,且管板上需钻近 9000 个孔,为了缩短加工周期,需要多钻头同时加工。为了将影响深孔加工质量的不良因素的影响控制到最小,此项目蒸汽发生器管板深孔加工采用某进口 BTA 内排屑深孔钻,该 BTA 采用三轴同时加工,大大缩短了产品的加工周期,BTA 系统加工有以下特点:
( 1) 切屑由钻杆内部排出,切屑不会划伤已加工孔表面,已加工表面质量较好,排屑顺畅。
( 2) 由于排屑空间大,相对的冷却润滑压力比枪钻低,一般为0. 5 - 3Mpa,对密封及供油系统的要求比枪钻低。
( 3) 钻杆为圆形截面,其扭转刚度及弯曲强度比枪钻高,因此可以采用较大的进给量钻削,生产效率高。
( 4) 加工范围广,内排屑深孔钻既可用于较大孔径的深孔加工,也可用于较小孔径的深孔加工。[2]
3 、加工前准备
为保证加工产品是万无一失,在正式加工产品前需进行试验件的加工,试验件应与产品为同材质、同厚度、同样的热处理条件等等,做到完全模拟产品加工状态。管板全厚度方向包括锻件本体 18MND5 及镍基防腐蚀堆焊层,由于镍基与合金钢的加工性有很大差别,因此需要采用分层钻削的方式,即镍基堆焊层与管板本体采用不同的切削参数,经过大量的钻孔对比试验,最终确定切削参数: 镍基合金部分: 转速 n =1200r/min,进给量 f = 60mm/min; 本体部分: n = 1450r/min,进给量 f = 130mm/min。在该参数下切削综合得出管孔的精度、粗糙度较好且加工效率较高。
当机床精度( 定位精度,重复定位精度,BOZA( 内孔) 相对位置度) 检定合格,钻管、钻套、铜套钻管支撑等确认合格后,按照实验切削参数在试验件上连续加工出 124 个孔,一次检查合格后,方可进行产品的加工。将两块 V 型铁下垫可调垫铁放置于工作台上,将管板组件放置于 V 型铁上,管板一次侧正对主轴,按照管板端面及分隔板短节加工面找正管板垂直、水平、扭别均在 0. 1mm 以内。V 型铁用压板固定到机床工作台上,用链条压紧筒节,在管板一次侧端面,外圆压块机二次侧靠下部外圆,共设置 4 块百分表,在 BOZA 顶紧和钻孔过程中,操作人员应随时监测百分表指针示数,确保管板不出现移动、震动现象。
4 、使用刀具
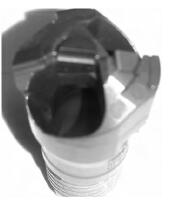
图1
BTA 深孔加工使用 19. 28mm 的多刃错齿内排屑深孔钻头( 如图 1) ,由于切屑刃错齿排列,故该种深孔钻能够实现完全分屑,加之有断屑台,容易形成“C”形切屑,有利于切屑的顺利排出。
钻头的刀片布置比较合理,可以使径向力始终压向导向块,导向块紧贴已加工孔壁向前推进,钻孔直线度比较好。由于错齿分屑,切削力及扭矩都比较小,切削变形小,产生的切削热较少。[2]在每一个新钻头用于管板钻孔之前,操作者须目视检查确认钻头切削刃完好,并在试验件上钻一个孔,测量、确认钻孔的直径、表面粗糙度和垂直度满足相关要求,孔内表面无任何突出的毛刺、螺旋沟等缺陷,为保证钻削质量,每个新钻头的使用寿命规定为最多钻 12 个孔,用过的钻头进行统一编号,记录加工每个孔所用的钻头编号。
5 、过程质量控制
( 1) 在加工过程中,机床始终保持“人不离机”,时刻注意观察切屑情况,出现长切屑 应停机检查;
( 2) 操作者应时刻注意观察刀具监控系统曲线变化,出现异常波动、升高或自动退刀后应停机检查;
( 3) 时刻注意观察功率、扭矩、切削油压力、流量监控,出现异常或自动退刀后应立即停机检查;
( 4) 时刻注意观察切削油温度情况,油温超过 28 - 38℃ 范围应停机检查;
( 5) 时刻注意观察工件所压百分表状态,表针变化大于 0.02mm 时停机调整;
( 6) 各班次使用的钻头,必须在交班前由各班次全部消耗掉,若有未达到寿命的钻头也不再使用;
( 7) 管板钻孔过程中,没加工最多 10 个钻孔循环几每次换刀间隙,操作人员检查各孔的直径、表面粗糙度、孔心距几垂直度满足管板先关参数要求,并记录。
6 、加工后清整及清洗
BTA 深孔钻加工完成 8948 个管板孔后,管板一次侧、二次侧孔口均存在飞边及毛刺,为保证后续换热管能顺利穿入管板孔,并且保证管子 - 管板密封焊合格,需要对管板二次侧用专用倒角刀加工出 C0. 7 的倒角,并用专用百叶轮修磨管板一次侧毛刺。
当倒角、清整完成后,需要对管板一次侧、二次侧表面、管板孔内部进行清洗,去除表面杂质,清洗合格后,要将所有管板孔两端用毛毡塞堵好,同时用气相防锈膜将管板一、二次侧表面密封防护,与外界隔离,以满足后序穿换热管时对管板清洁度的要求。
7 、结语
该台蒸汽发生器管板孔已全部加工完毕,且百分之百检查合格,说明按照此工艺加工以及过程控制有效,现已清洗封存完成,为后续换热管的穿、焊打下良好基础。
投稿箱:
如果您有机床行业、企业相关新闻稿件发表,或进行资讯合作,欢迎联系本网编辑部, 邮箱:skjcsc@vip.sina.com
如果您有机床行业、企业相关新闻稿件发表,或进行资讯合作,欢迎联系本网编辑部, 邮箱:skjcsc@vip.sina.com