基于动态特性分析的机床主轴装配故障诊断硏究(下)
2017-7-14 来源:北京交通大学 作者:李凯旋
6.装配故障源位置识别的研究
上面章节通过对VCL850主轴箱区域的信号检测与分析,确定主轴箱可能存在动不平衡、角度不对中的装配故障。但不确定产生故障的具体位置。角度不对中故障为例,在主轴带轮配合处、电机带轮配合处均可能为装配不当的位置,并不确定在什么位置进行装配调整,如图6-1所示。这就是本章节研究的意义所在。
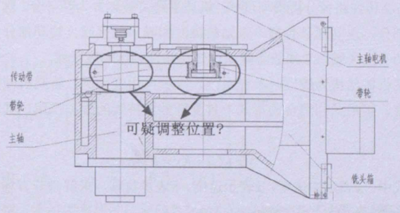
图6-!主轴箱区域可调整的装配位寬
在工况下,理想状态的主轴箱区域振动信号成分简单,故障源主要来自电机和主轴。由于加工制造、装配等误差的存在,在工作状态下,会衍生出额外的激励,由第二章可知:动不平衡故障导致离屯、力的出现;不对中问题衍生出二倍于转速周期的激振力。装配故障衍生的额外激励,作用在相关位置,表征出成分更加复杂多变的振动信号,通过巧不同形式振动信号的检测分析,判定机械故障。对机床进行故障诊断,首先利用相关的检测手段,确定机械故障的类型,其次利用装配故障源位置识别的方法确定产生振动信号来源的位置,进而针对性的进行调整,才能够从根本上解决机械故障问题。
6.1装配故障源位置识别的方法原理
本论文在假设机械系统是线性时不变系统的前提下,基于传递路径分析的原理.对存在装配故障的主轴箱区域的故障源进行识别。传速路径分析方法的核也在于研究机械系统自身的传递特性W及确定是否存在未知的故時源,本论文针对主轴箱区域力求建立一个较为完整的传递系统,并在此基础上根据传递系统某几点的响应特性,通过数值解析的方式确定研究区域的装配故障源位置。
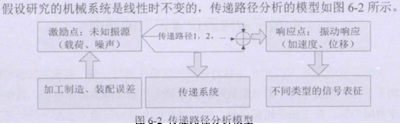
由围6-2传递路径分析模型可知:机械系统可被划分为两部分,称之为主动部分、被动部分,主动部分包括:未知故障源和噪声源区域,被动部分包括:传递系统和振动响应区域。未知故障源通过传递路径到达响应区域。
假设某机械结构为线性时不变系统,W单自由度为例,将某机械结构等价为质量、刚度、阻尼共同组合的形式,且受到外界持续的激振作用,其动力学方程为:
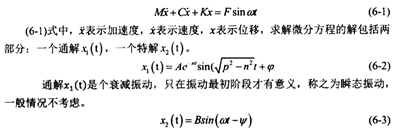
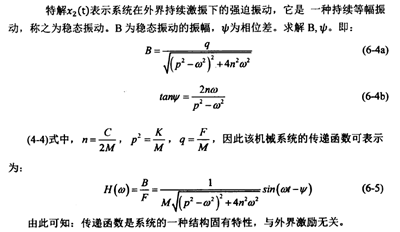
传递函数的获取可通过W下途径:每一个传递函数可W用来描述一个激励点自由度6对某一个响应点自由度之间的传递路径关系,称之为巧/.,针对某机械系统,假设布置n个激励点/响应点,则存在w=n2个传递路径,对于机械系统上的某一响应点,可认为是故障源通过各条传递路径达到目标位置线性叠加的结果,即;
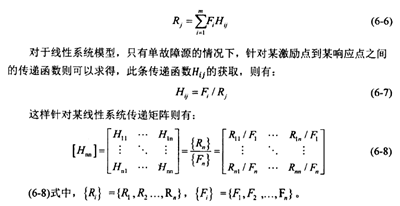
如果得到了某机械系统的传递函数矩阵,在装配故障源位置未知的的情况下,可根据测得的响应点的振动响应信号利用数值解析的方式大致确定未知故障源的位置。即:
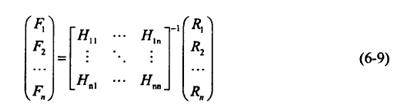
由(4-4a)可知,阻尼矩阵的存在,导致输入信号与输出信号存在相位差,多故障源激励下的响应点是单点故障源线性叠加的结果。W两点结构系统为例,对两点分别施加单激励,如園6-3所示。
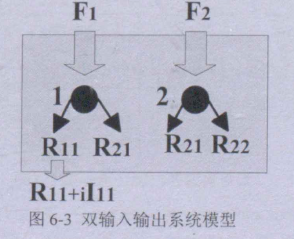
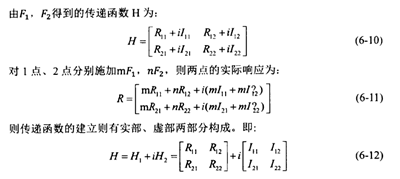
综上所述,针对某机械结构的故障源进行识别,大致可W分为H步:
(1)在非工作状态下,对某机械结构上的各个传递路径的源头进行单点激励,同时测量对应响应点的响应信号,建立频响函数矩阵。激励方式可为小链敲击瞬态激励的方式,也可采用激振器进行持续稳定的激励。
(2)工作状态下,测量机械结构上各个响应点的稳态响应信号。
(3)利用求得的频响函数矩阵求逆,通过数值计算的方式求得机械结构上的未知故障源位置。
6.2装配故障源位置识别的仿真分析
利用ANSYS软件的谐响应分析模块对主轴箱的故障源进行识别,验证实验方法的可行性。实验对象为主轴箱装巧体,主轴箱的主要参数如表6-1所示。
表6-1主轴箱的主要参数

拟布置六个激励点/响应点,对其一端采用固定约束的方式,如图5*4所示。首先对其进行模态分析仿真,确定其固有频率,并分析固有频率区间是否会对未知故障源的识别造成影响。
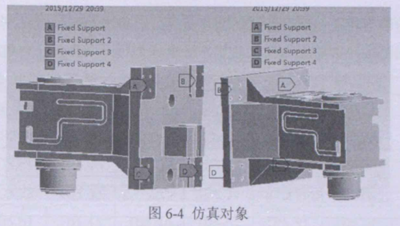
由模态分析结果可tJl确定一阶模态的固有频率为%3.16Hz,利用谐响应分析,对主轴箱装配体的六个点分别单独施加频率在200 ̄1000Hz区间的稳态载荷激励1000N,如图6-5所示。
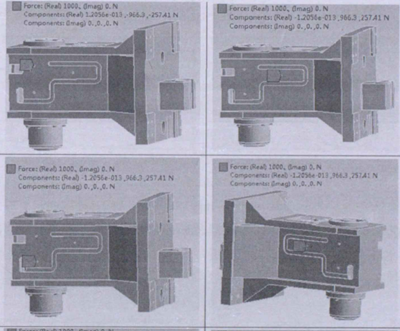
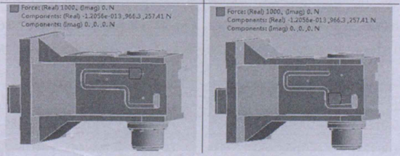
图6-5主轴箱装配体的载荷设置
每个点单独施加载荷时,得到六个点的响应特性,w第-点麵为例,得到的六个点的响应特性曲线伯德图如图6-6所示(上曲线为幅频曲线,横坐标为频率,纵坐标为加速度;下曲线为相频曲线,横坐标为频率,纵坐标为角度)。
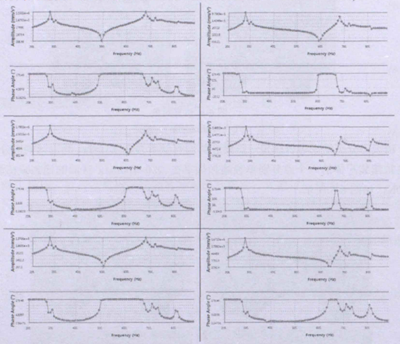
图6-6单点激励后的六点响应曲线
利用(4-8)式,得到了200?lOOOHz区间的任意频率处的频响巧数巧阵,由表4-4可知:固有频率处的相频值比较接近,因此对机械系统进行故障源识别建议避开对固有额率处。选取分析频率为280Hz的频响函数幅频矩阵如表6-2所示。
表6-2280Hz下的频响函巧幅频矩阵
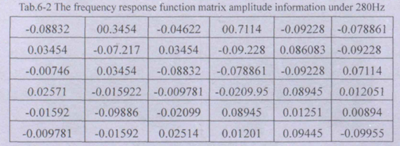
由表6-2可知,阻尼系数为化003,不同频率的输出响应与输出信号存在相位差,280Hz对应的六点的相位信息如表6-3所示:
表6-3280Hz下的频响画数相频矩阵
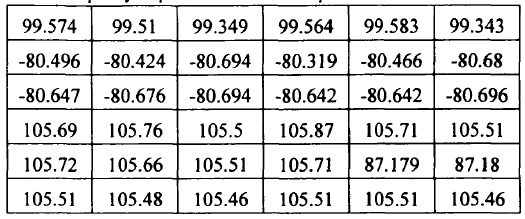
利用LabVlEW分别对实部的结构巧阵和虚部的结构矩阵求逆求逆,然后对得到的实部、虚部的解析力分别平方求和开平方根,即得到实际的解折力。程序框图如图6-7所示。
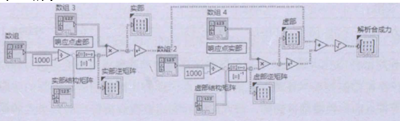
(1)单故峰源识别
对主轴箱装配体的任意某点分别施加载荷,得到六个点下的响应信息,例如对第六点施加3000N的持续激励用来模拟主轴箱装配休在实际工况下的受力情况,如下阁6-8所示。
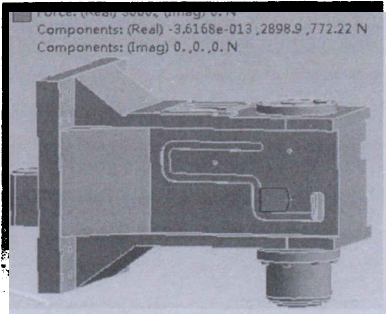
图6-8单故掩源下主箱箱装配体的受力情况
在实际载荷的激励下得到六个点的响应信息如表6-4所示。
表6-4六个点的响应信息

利用(4-4)式求解六个点的实际受为情况如表6-7所示。
表6-5解析山的受力情况

由表6>4、表6-5可知,某点单故障源激励得到的各点的响应信息与频响函数的某行存在比例关系,岛两者的相位信息是一致的。而频响函数矩阵的获取就是通过所有点的单独激励得到的。因此,实际利用数值解析得到的六个点的受力情况与实际十分符合,有效实现了故陣源的有效识别。只利用频响函数矩阵的幅值信息,就可W实现对单故降源的有效识别。
(2)多故障源识别
对主轴箱装酷体的任意两点分别施加载荷,得到六个点下的响应信息,例如对第一点施加2000N,第二点施加I000N,用来模拟主轴箱装配体在实际工况下的受力情况,如閱6-9所示。
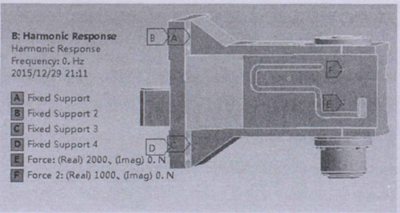
图6-9《巧障源下主轴箱装配体的受力情况
在实际载荷的激励下得到六个点的响应信息如表6-6所示。
表6-6六个点的响应信息
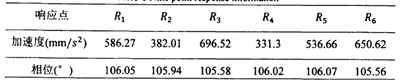
利用(4-4)式求解六个点的实际受力情况如表6-7所示。
表6-7解析出的受力情况

由表6-7可知,多故障源得到的各点响应信息实则是各点单故障源线性叠加得到的结果,因此相位信息也发生了改变。求解方式;分别提取各点响应信息的实部、虚部,对应与频响函数矩阵的实部、虚部进巧计算求解,解析得到六个点的受力情况。由表6-7可知;解析出的受力与实际十分符合,有效实现了故虜源位置的有效识别。
6.3装配故障源位置识别的实验论证
以双驱丝杠实验台上的弯板工件为研充对象,验证本次方法的可行性,由于设备的局限性,只开展对单故障源识别的实验验证。分别采用力链和激振器两种激励方法对故障源进巧识别。弯板工件的布点如图6-10所示。
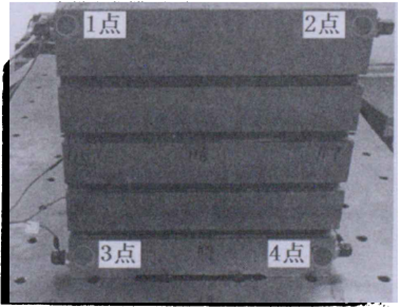
图6-10测试点布置
6.3.1力键敲击实验
首先利用力鍾对工件的四个点进行逐点敲击,工件的一阶固有频率为巧2Hz,
选取分析频率区间为512Hz,与此同时在四个点分别布置加速度传感器,由此得到16姐频响函数.进而求得工件上四个点的传迸兩数矩阵,实验现场如图6-11所示。
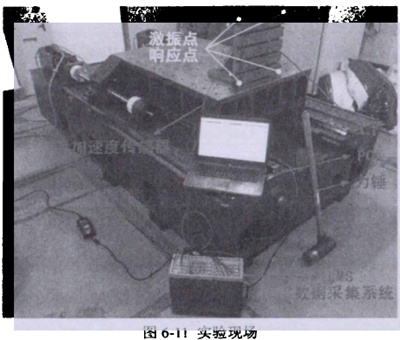
利用力键对某一点进行敲击,与此四点的加速度传感器得到响应信息,构成四组频响函数,在峰值处,频响函数的相频曲线较为集中,幅频曲线还是存在较大差异。如间6-12所示。
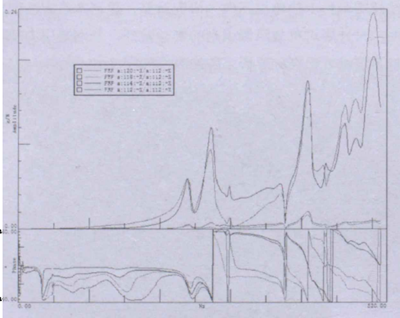
国6-12某点满励下的四姐频巧曲线
力链敲击的质量对能否获取正确的频响函数曲线脊很大的影响。进而影响到对故障源位置的有效识别。假如设置力键敲击五次,取五次平均值,利用相干性系数來评价五次力键敲击的好坏程度。
就单输入输出系统而言,一般利用常相干分析。图6-13为单输入输出示意图,图中H(/)为系统的频响函数。
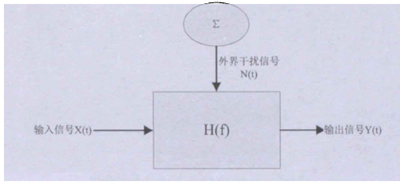
图6-13单输入输出系统
例如某机械系统中存在输入信号乂(t),输出信号^〇;),引入互谱幅值的一个重要不等式:
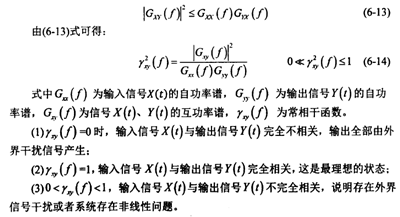
某点的五次相干性系数如图6-14所示。可见在50?150Hz频率区间的相干性系数接近1,此频率区间的频响函数矩阵是可信赖的。
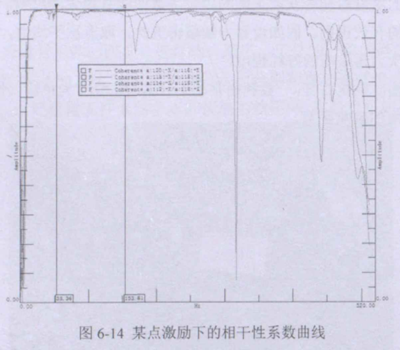
对四个点中的第二点进巧敲击,得到四个点的响应曲线如图6-15所示。
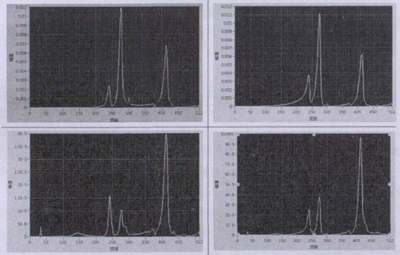
图6-15第二点激励下的各点响应曲线
实际情况下,只能测得响应信息,另外根据之前获得的传递歯数矩阵,求解判定故障源的位置。利用LabVIEW编写的程序对己获取的信息进行求解,得到四个点的故障源幅频曲线如图6-16所示。加速度传感器的频响量程在5?5000Hz,OHz附近的数值不予考虑,由图6-16可知,第二点处求解的振源曲线在50Hz?150Hz
区间远远高于其他兰点。因此解析得到的结果与实际相符,因此对故障源实现了有效的位置判别。
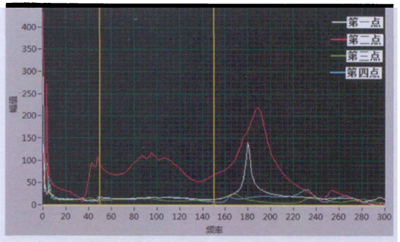
图6-16敲击第2点解析得到的振源幅频曲线
实际情况下,若要实现对圭轴箱区域故障位置的有效识别,必须保证对所有可能产生故障区域进行布点。但可能并没有在故障区域布置测试点,建立全面的传递函数矩阵。如图6-17所示,实际激励位置没有在四个点上,利用此位置上激励得到的四点响应信息,求解激励。
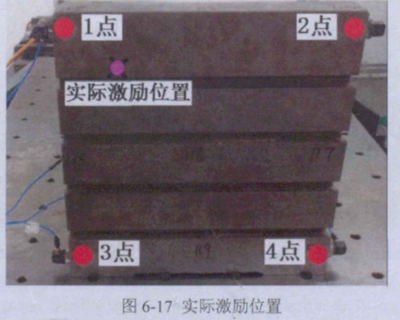
如图6-18所示。可W看到在相干性系数较高的频域,解析出的振源位置为第一点, 实际激励位置与第一点比较靠近,因此解析得到的结果较为理想。
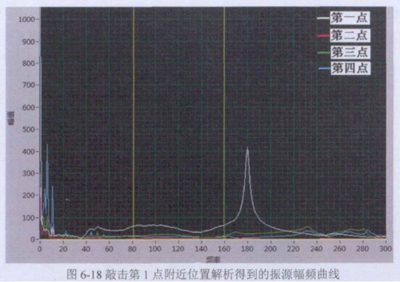
假如利用力键敲击的实际激励位置在弯板工件的中间位置,与布置的任何一点都不靠近,如图6-19所示。
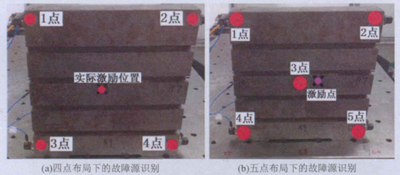
图6-19不同点布局下的故障源识别
利用此点激励得到的四点响应信息与传递函数矩阵进行计算,解析得到的各点振源曲线如图6-20所示。发现无法判定振源的实际位置。应对的办法是对预判的故障源位置进行更加密集的布点。如图6-21所示,得到了理想的识别效果。
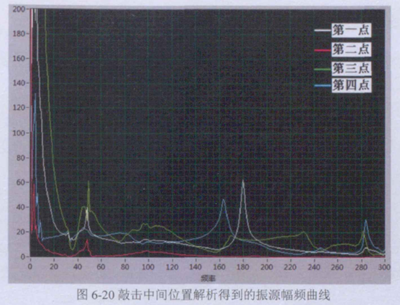

结论:有^文上实验可知:对故障源进行有效识别的前提:对某机械结构布置测试点,构造传递函数矩阵,一定要尽量包含可能存在故障源的所有区域,不一定布置的测试点恰好对应未知故障源处,但是远离故障区域,将无法实现对未知故障源的有效识别。应对的办法是对预判的故障源位置进行更加密集的布点。
6.3.2激振器激励实验
对某特定关屯、频率的装配故障源位置进行识别,可采用激振器的方式进行激励,如图6-22所示。
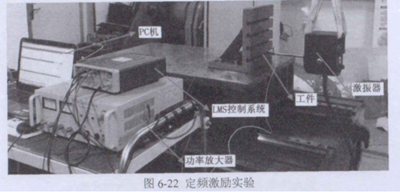
实验设备包括激振器、LMS控制系统、功率放大器、PC机等。LMS控制系统同时具备信号发生器和信号采集两个功能,LMS输出特定频率的正弦信号通过功率放大器,将信号放大输入到激振器,激振器作用于工件上,给工件施加特定频率的正弦激励,与此同时,力传感器和加速度传感器将测得的信号采集到LMS中。这样形成了一套信号发送与采集的闭环系统。
由于激振器自身会受到50Hz交变电压信号的干扰,因此选取频率要避免是50Hz的倍数,选择特定频率为212Hz,每次给定5N左右的激振力,同时对四个点的加速度信号进行采集。测试界面如图6-23所示。
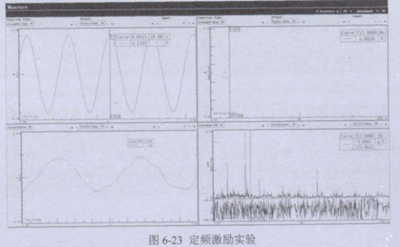
从左到右,从上到下一次为激振时域信号、激振频域信号、某点的时域响应信号、频响函数曲线。
利用激振器得到的212Hz处的频响函数矩阵如表6-8所示。
表6-8212Hz下的频响函巧矩阵
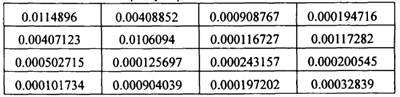
第四点进行激振,只利用在此点激励下的响应信息判定激振点位置。解析得到的四点激励如表6-9所示。
表6-9解巧出的受力情况

由于外界的交变电压信号、随化噪声等干扰,频响函数矩阵经过逆矩阵变换会产生很大的数值变化。解析出的激励幅值与实际并不相符。可对解析得到的所有激励信息求和,然后计算各点的激励信息与总体激励信息的权重关系。
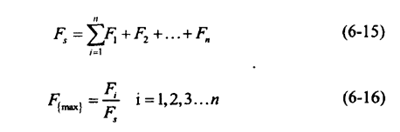
利用(4-13)、(4-14)显然第四点所占的权重最大,占78.8%,由W上信息可知,利用激振器同样实现了对故障源位置的有效识别。
针对主轴箱民域可能引发角度不对中的位置布置测试点,如图6-24所示。
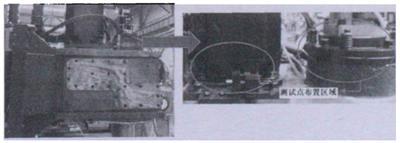
图6-24主轴|g区麵试点的布局
关心频率区间为二倍于转速的频率附近。首先在离线状态下建立测试点之间的传递函数矩阵,然后在工作状态下利用加速度传感器对主轴箱区域进行优化布置,获取准确有效的响应信息,对未知装配故障源的位置进巧识别判定。
6.4本章小结
本章承接上面章节,通过开展信号测试与分析的实验研巧,确定了主轴箱区域存在动不平衡、角度不对中等装配故障,明确了不同类型装配故障所对应的信号特征。本章对"判别特定类型装配故障的位置"这一问题开展研究。基于传递路径分析的原理,对装配故障源位置识别的理论基础进行了简要介绍,利用ANSYSWorkbench有限元软件采用谐响应分析的方法对主轴箱装配体上的六个测试点进行仿真分析,对装配故障源位置进行了有效识别。分别采用力键、激振器两种激励方式对上述方法进斤实验论证,均得到了较为理想的结果,实现了对装配故睹源位置的有效识别。
7.结论
7.1结论
装配是工程机械领域的重要环节,装配精度与机床的加工性能紧密相关,能够准确诊断出装配环节的故障类型、发生故障的位置,对于指导现场工人迅速排除装配故障,保证机床高质高效的出厂具有重要的指导意义。本论文在前期大量调研现有文献的基础上,W南通科技生产的VCL850立式加工中屯、主轴箱为实验对象,对不同的装配故障形式的信号特征、故障特征识别方法、故障源位置识别等内容进行了较为深入的研巧。
本论文从上述完成的主要研巧内容分为^式下方面;
(1)L^LabV圧W为开发平台,构建了用于信号采集处理与分析的测试系统,具有数据采集和保存、降噪滤波、时频域分析、轴也、轨迹测试、相位检测、轴必轨迹识别等功能。
(2)基于模态动能法与有效独立法的原理,利用有限的传感器寻找主轴箱区域的最佳测试点,为解决运行状态下传感器优化布置的问题提供了一种思路。
(3)通过对采集的加速度信号进行分析发现:主轴箱区域的基频、二倍频信号特征突出,主轴在径向的基频幅值与转速存在正相关关系,证明主轴区域可能存在动不平衡问题;主轴在不同转速下的轴也轨迹呈外八字形,且基频、二倍频信号明显。通过与正常工作的机床主轴的轴也轨迹进行对比,确定VCL850存在主轴与电机角度不对中的装配问题。
(4)基于SVD和不变矩两种方法W巧也轨迹作为判定故障类型的特征指标,对VCL850主轴的轴屯、轨迹进行判定,识别出主轴箱存在角度不对中的装爾故障。取得了较为理想的效果。
(5)基于传递路径分析的原理,对VCL850主轴箱区域的故障源位置进行识别:并利用ANSYSWorkbench[^^1主轴巧为对象进行了仿真分析,有效实现了主轴箱区域故障源位置的判定。通过:开展实验针对某化械结构,采用激振器、力链两种不同的激励方式模巧实际工况,论证了本方法的可行性。
7.2工作展望
本论文W南通科技生产的VCL850为实验对象,对主轴箱区域的装配故障进行诊断,力求建立一套行之有效的装配指导方案,机床出现故障问题时,工人可通过本论文成果确定装配故障问题的类型,找到发生装配故障的具体位置,保证在出厂阶段,有效排除机床的装配问题。由于客观条件的限制レッ及本人的能力有限,对于本论文的研巧工作远不够完善,接下来可在a下几方面开展研兜:
(1)虽然利用电祸流位移传感器对两个机床的主轴轴屯、轨迹进行了测试,但并未对挣在问题的机床主轴箱进行装配调整。另外机械松动、碰摩故障的转子轴屯、轨迹特征表现形式应该开展大量的实验,反复论证。
(2)本论文对故障源位置进行识别,在信噪比较为理想的状态下开展实验,取得了理想的结果。实际工况下的故障源复杂多变,环境噪声强烈,还要在实际工况下的机床主轴箱上开展实验,并对本方法进一步完善。
投稿箱:
如果您有机床行业、企业相关新闻稿件发表,或进行资讯合作,欢迎联系本网编辑部, 邮箱:skjcsc@vip.sina.com
如果您有机床行业、企业相关新闻稿件发表,或进行资讯合作,欢迎联系本网编辑部, 邮箱:skjcsc@vip.sina.com
更多本专题新闻