加工中心主轴箱体制造工艺可靠性保障方法的研究 (下)
2017-6-30 来源: 吉林大学 作者: 谭壮
第 5 章加工中心主轴箱体制造过程关键工序质量控制点
控制图分析方法虽然能够发现加工中心主轴箱体制造过程存在异常,但不能判别出制造过程的异常波动是由哪一种具体异常原因所造成,因此需要花费大量的时间去寻找具体的异常原因并将其排除,而不能主动预防或者减少制造过程异常原因的出现。制造过程的异常原因来源于与加工中心主轴箱体制造过程密切相关的生产环境、工件材料、生产设备、生产人员、工艺方法、测量等六个因素(简称 5M1E)。基于上述六个因素的角度建立加工中心主轴箱体制造过程关键工序质量控制点,可以防止或者减少制造过程异常因素的出现,从而系统性的保障加工中心主轴箱体制造工艺可靠性。 加工中心主轴箱体制造过程关键工序质量控制点的内容包括提出建点计划、编制关键工序质量控制点作业文件、建立关键工序控制点档案以及管理关键工序质量控制点。本章将详细阐述上述四部分关键工序质量控制点内容。 5.1 提出建立关键工序质量控制点计划
5.1.1 一般关键工序
根据 Pareto 法则可以知道,加工中心主轴箱体制造工艺可靠性是由关键的少数工序所决定[60]。对这些关键的少数工序建立质量控制点有利于减少工作量提高工作效率,并有效保障加工中心主轴箱体制造工艺可靠性。提出建立关键工序质量控制点计划的主要内容是明确建点工序的名称、技术要求、相关作业文件及责任部门。 关键工序指的是对产品质量尤其是可靠性起着关键作用的工序[60]。在此定义的基础上,本文将需要建点的关键工序分为一般关键工序和特殊关键工序两种。一般关键工序指的是制造工艺可靠性评价指标不符合规定要求或者具有不符合规定要求的风险较大的工序,也称为薄弱工序,如工艺故障风险优先数高的工序、工序能力不足的工序、制造过程存在异常因素较多的工序等。不同的生产企业有不同的标准,因此需要按照生产企业的具体要求评定出一般关键工序。 本文第三章的制造工艺 FMECA 方法可以确定出加工中心主轴箱体制造过 程中风险优先数较高的工序,第四章的控制图分析方法可以确定出加工中心主轴 箱体制造过程中波动较大、异常原因较多、工序能力不足的工序,上述两章内容是确定加工中心主轴箱体制造过程一般关键工序的重要方法。
5.1.2 特殊关键工序
特殊关键工序指的是制造工艺可靠性评价指标符合规定要求或不符合规定要求的风险较小,但是对其它工序产生恶劣影响较大的工序。一般关键工序强调的是工序本身的薄弱,而特殊关键工序则是强调对其它工序的恶劣影响。 特殊关键工序应根据加工中心主轴箱体制造过程的具体情况进行具体分析,其中典型的情况为后续制造工序对之前已经完成的制造工序的影响,尤其是加工中心主轴箱体的主轴孔因生产原因优先完成加工,后续孔位的加工必然会影响到主轴孔的制造精度。这种影响可以分为两种,一种是有利的影响即提高了主轴孔的制造精度,另一种则是不利影响即降低了主轴孔的制造精度,因此为了能够采取针对性措施降低后续孔位对主轴孔的不利影响,需要量化分析出后续孔位对主轴孔的影响程度,对主轴孔制造精度不利影响程度较大的工序即可作为特殊关键工序。Zhuang Tan[84]研究了量化分析数控机床主轴箱体后续孔位对已加工完成主轴孔制造误差的影响程度,并对其研究方法进行了实例分析,本文以分析加工中心主轴箱体后续孔位对主轴孔制造误差的影响程度为例,说明其研究方法的原理,分析过程如下:
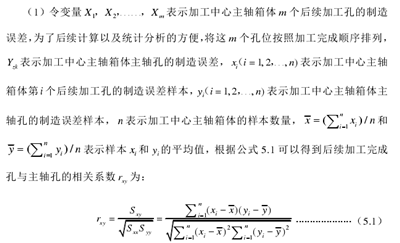
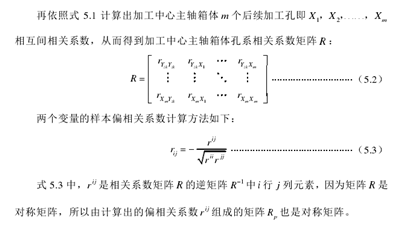
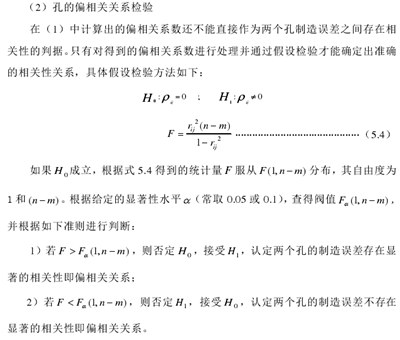
通过以上的计算步骤不仅可以找出与主轴孔存在偏相关系数的后续加工孔,也可以发现其它孔之间是否存在显著的相关性,并为后续的制造误差传递关系量化提供依据。
(3) 误差传递量化分析 偏最小二乘法(PLS)是研究两个相关数据块或矩阵的一种方法且能够在自变量存在相关关系且样本数量较小的情况下得到准确的回归[85-86]。因此为了得到后续加工孔与主轴孔的量化关系,本文采用非线性偏最小二乘法(NIPALS)对其进行回归分析。 通过上述相关性分析找出与主轴孔存在偏相关关系的 L 个后续加工孔,以这些孔的制造误差作为自变量? ?1 2 LX ,X ,??,X ,主轴孔的制造误差作为因变量? ?zkY , n 为样本数量,从而可以得到因变量与自变量的样本矩阵:
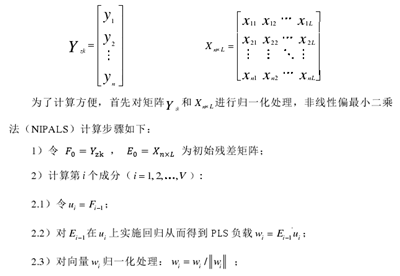
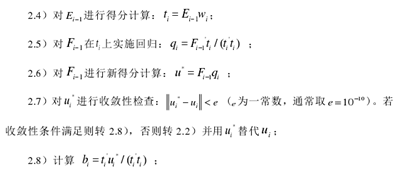
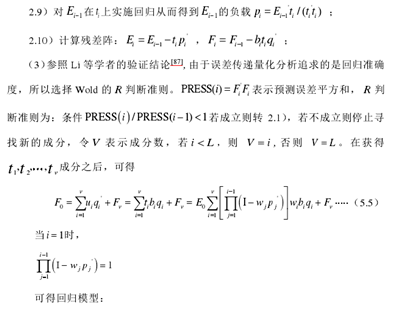
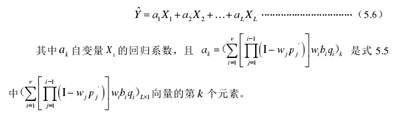
通过式 5.6 建立的误差传递量化关系数学模型,可以发现变量系数越大对主轴孔制造误差影响越大,当系数为正时,提高该孔的制造精度有利于减小主轴孔的制造误差,系数为负时,只能降低该孔制造精度才能减小主轴孔的制造误差,而孔的精度等级是由设计决定的,所以降低制造精度是不现实的。上述分析结论是从回归模型的数学关系中推导出的,实际上应当分析出这种回归模型背后的因素,即后续孔位加工时产生的热量或是切削力等原因造成主轴孔的变化,根据分析出的原因制定相关预防措施可以减少后续加工孔位对主轴孔制造精度的不利影响。
5.2 编制关键工序质量控制点作业文件
5.2.1 制造过程相关因素分析
加工中心主轴箱体制造过程涉及到多个生产因素,如图 51 所示,这些因素包括生产环境、工件材料、生产设备、生产人员、工艺方法、测量,简称 5M1E。造成工艺故障发生的异常因素必定与上述六个因素相关,因此针对上述六个因素制定一系列的控制文件将有利于减少异常因素的出现。
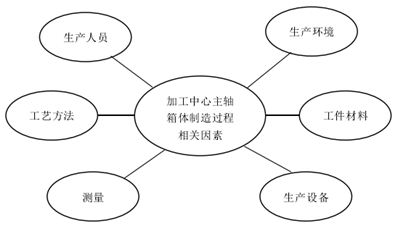
图 5.1 加工中心主轴箱体制造过程相关因素
图 5.1 中各个因素的具体内容如下: 生产环境: 加工中心主轴箱体生产现场的湿度、温度、照明、卫生清洁等; 工件材料:加工中心主轴箱体的毛坯质量、成分、物理化学性能等; 生产设备:加工主轴箱体所需要的设备仪器、工装夹具等的性能状况; 生产人员:加工主轴箱体的操作人员技能、积极性、责任心等; 工艺方法:加工中心主轴箱体的制造工艺流程、生产要求等; 测量:对加工中心主轴箱体工序质量进行检测时所采用的测量仪器、测量方法等。 明确了与加工中心主轴箱体制造过程相关的六个因素之后,需要从这六个因素的角度制定相应的控制文件,可以使加工中心主轴箱体制造过程更加规范,出现问题后也可以迅速查出问题的原因。
5.2.2 关键工序质量控制点作业文件
5.2.2.1基于生产人员的控制点作业文件
生产人员的操作水平将直接影响到加工中心主轴箱体制造工序的质量,具有很强的柔性即波动性较大,并且受招聘条件、培训水平及企业激励政策等条件影响较大,因此企业有必要针对上述影响条件制定相应方案,从而充分调动操作人员的主观能动性。 结合加工中心主轴箱体生产过程实际情况,只要有利于提高生产人员的操作水平的措施均可以作为针对生产人员的控制点作业文件。本文提倡使用效率较高,应用广泛的《人员操作规范要求》,目前许多企业都有相似标题的文件,但是仅局限于一般性的要求如时间要求、行为要求等。本文提出的《人员操作规范要求》不仅具备一般性要求,还应具备针对一般关键工序所需要的设备操作要求、针对特殊关键工序所需要的特殊操作要求等。
5.2.2.2基于工艺方法的控制点作业文件
根据加工中心主轴箱体设计要求,采用合理的工艺方法,制定合理的工艺要求不仅可以提高加工效率,也可以减少工艺故障的发生提高成品率。目前许多企业只重视产品设计而轻视制造工艺,许多工艺文件陈旧多年不更新,生产线操作人员多凭生产经验进行生产,无法保障制造工序质量的稳定。因此为了确保关键工序的质量稳定,有必要完善相关的工艺文件包括工艺内容、装夹要求、切削要求等。
5.2.2.3基于生产设备的控制点作业文件
生产设备是完成加工中心主轴箱体制造工序的关键工具,生产设备的性能将直接影响到工序的质量,也是异常因素发生较多的区域。因此有必要针对关键工序制定相应的生产设备控制点作业文件,常用的有《加工设备日常点检卡》如表5.1 所示,可以用来监测加工设备每天的性能状况;《加工设备周期检查卡》如表5.2 所示,可以用来监测加工设备每个阶段的性能状况;《加工设备管理与维护保养要求》可以用来维护加工设备的性能,使其满足生产需要;《工具、工装管理规定》可以用来维护、管理工装夹具的使用性能,确保其满足生产要求。
表 5.1 加工设备日常点检卡(示例)
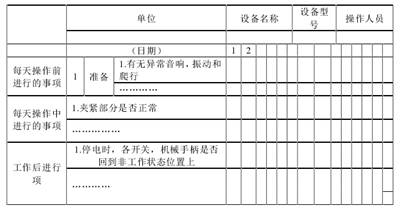
表 5.2 加工设备周期检查卡(示例)
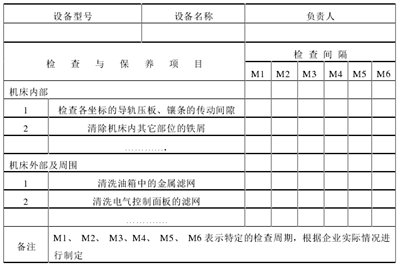
5.2.2.4基于工件材料的控制点作业文件
加工中心主轴箱体的毛坯通常是铸造而成,铸造水平低容易造成零件存在砂眼、气孔等问题,因此为了确保毛坯的各项性能符合生产要求,本文提出制定《铸造工艺可靠性检查表》,如表 5.3 所示。《铸造工艺可靠性检查表》可以针对需要满足的工艺要求进行核对,防止出现疏忽遗漏某项工艺要求的情况。
表 5.3 铸造工艺可靠性检查表(示例)
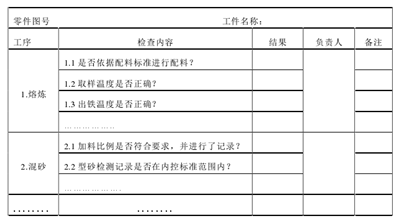
5.2.2.5基于测量的控制点作业文件
测量方法是否正确、测量器具的准确性等均会影响到对加工中心主轴箱体制造工序质量的判断,为了避免测量对制造工序质量产生不利影响,需要针对测量相关的因素制定控制文件,目前应用较为广泛的是《计量仪器周期检查卡》如表5.4 所示、《计量器具使用、维护和保养规范》。
5.2.2.6基于生产环境的控制点作业文件
加工中心主轴箱体生产现场的湿度、温度、光照强度、卫生清洁等对工序质量都会产生一定的影响。一般而言,关键工序对生产环境的要求都是比较严格的,因此有必要对生产环境制定相应的规范,目前应用较为广泛的是《生产车间管理规定》,该规定能够针对生产环境、仪器摆放等作出详细要求,从而保障加工中心主轴箱体车间环境符合生产要求。
表 5.4 计量仪器周期检查卡(示例)
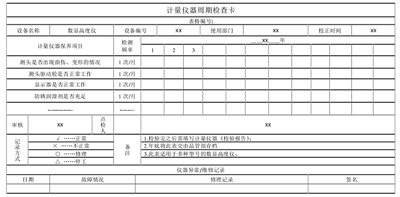
5.2.2.7基于多种因素的控制点作业文件
上述关键工序质量控制点文件均是针对单一的影响因素,然而从制造工艺的设计到执行结束的整个阶段涉及到多个影响因素,为了能够防止某个环节出现遗漏或者疏忽,本文提出针对关键工序建立《制造工艺可靠性检查表》如表 5.5 所示。
表 5.5 制造工艺可靠性检查表(示例)
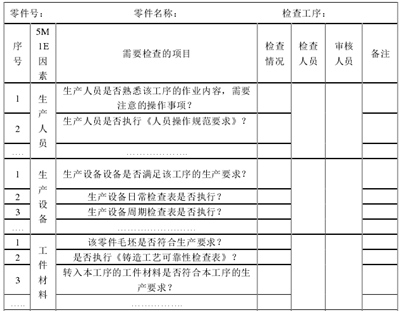
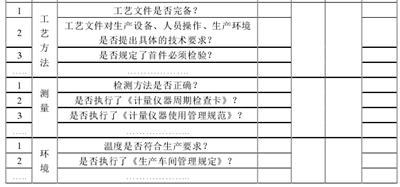
需要指出的是,上述控制文件应根据企业的实际生产需要进行增减或者更改,制定相关文件时应尽可能使文件内容明确。 5.3 建立关键工序质量控制点档案上一节针对与加工中心主轴箱体制造过程密切相关的 5M1E 因素建立了相应的控制文件,上述文件经过批准后需要建立关键工序质量控制点档案,档案应包括所有关键工序质量控制点文件,建立档案可以便于控制点文件的实施和检查控制点文件实施情况。
5.4 管理关键工序质量控制点
明确加工中心主轴箱体关键工序质量控制点所涉及人员(包括生产操作者、技术人员、生产设备管理人员、检测人员等)的职责和要求如表 5.6 所示,涉及人员应严格按照规定要求履行各自的职责并有效控制加工中心主轴箱体的制造过程,预防异常因素的发生,保障加工中心主轴箱体制造工艺可靠性。
表 5.6 关键工序质量控制点涉及人员的职责要求(示例)
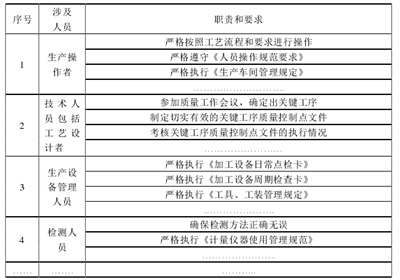
5.5 关键工序质量控制点应用实例
在与企业进行项目合作期间,对加工中心主轴箱体制造工序 23 建立了关键工序质量控制点并进行了实施,部分实施文件如图 5.1、图 5.2、图 5.3、图 5.4、图 5.5、图 5.6 所示。其中图 5.1 为实施的《机械加工作业指导书》,对加工中心主轴箱体的装夹、检测内容等作出了详细的要求;图 5.2 为实施的《设备日常点检卡》,可将其贴放在加工设备上或者工作桌上,按要求对各项内容进行检查,如果检查结果没有问题在相应的表格中打√,如果检查结果出现问题在相应的表格中打×;图 5.3 为实施的《计量仪器周期检查卡》,由负责计量器具维护人员进行管理维护,并按规定频率对各项内容进行检查,校正时间为执行校正的年度,如果检查结果没有问题在相应的表格中打√,如果检查结果出现问题在相应的表格中打×;图 5.4 为《加工中心主轴箱体制造过程可靠性检查表》,对制造过程涉及到的 5M1E 因素进行核对,防止出现遗漏,如果核对没有问题在相应表格中打√,相关负责人进行签字确认;图 5.5 为实施的《工序质量分析单》,对各个工序质量特性包括尺寸精度、粗糙度、形位误差进行评定,并给出整个工序质量的分析结果;图 5.6 为实施的其它文件,并进行了存档。经过一段时间的实施,关键工序质量控制点的控制文件对于预防异常因素的发生取得了良好的效果。
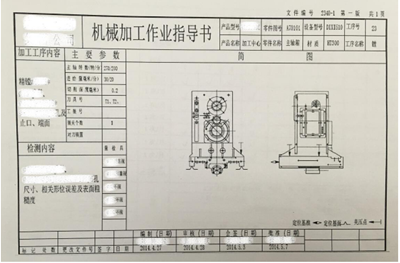
图 5.1 机械加工作业指导书
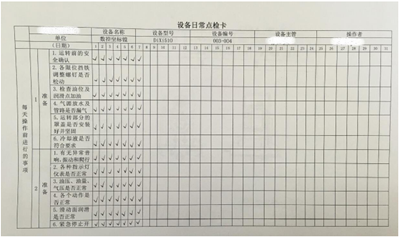
图 5.2 设备日常点检卡
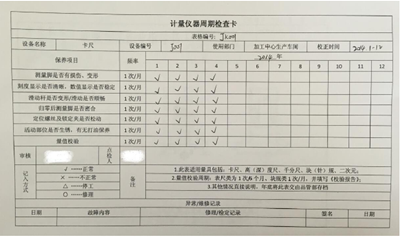
图 5.3 计量仪器周期检查卡
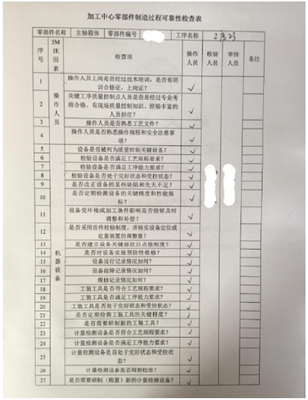
图 5.4 加工中心零部件制造过程可靠性检查表
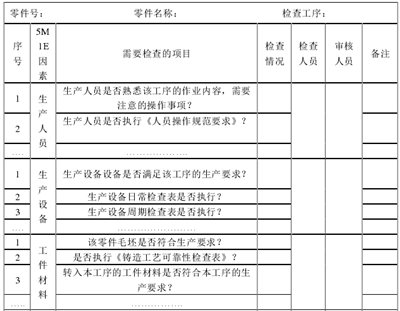
图 5.5 工序质量分析单
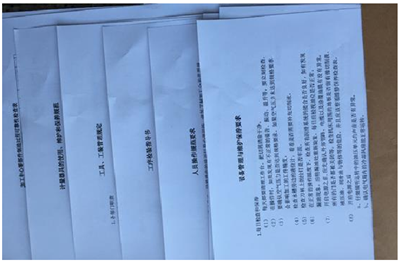
图 5.6 实施的其它文件
5.6 本章小结
本章详细介绍了加工中心主轴箱体制造过程关键工序质量控制点的内容,包括提出建立关键工序质量控制点计划、编制关键工序质量控制点作业文件、建立关键工序控制点档案以及管理关键工序质量控制点。提出了一般关键工序和特殊关键工序的定义,确定关键工序需要采用的方法,分析了与加工中心主轴箱体制造过程密切相关的 5M1E 因素,并针对各个因素制定相应的控制文件,描述了建
立以及管理关键工序质量控制点的方法,最后通过实例表明关键工序质量控制点具有很强的可实施性,对于预防异常因素的发生,保障加工中心主轴箱体制造工艺可靠性具有重要意义。
第 6 章 总结与展望
6.1 论文总结
本文以加工中心主轴箱体制造工艺可靠性保障方法为研究对象,在深入的分析总结了现有相关研究成果的基础上,结合企业的长期实践,从多个角度并逐层加深的对加工中心主轴箱体制造工艺可靠性保障方法进行了探讨,本文的研究内容总结如下:
1.分析了加工中心主轴箱体的结构及其在加工中心整机中的作用,说明了不同型号加工中心主轴箱体在制造工艺上的相似性。从加工中心主轴箱体制造过程符合规定要求能力的角度,给出了加工中心主轴箱体制造工艺可靠性的定义,同时提出了用于评价加工中心主轴箱体制造工艺可靠性的指标体系,包括工艺可靠度、工艺故障风险优先数、工艺稳定性、平均工艺故障间隔时间、平均工艺故障修复时间、合格工序平均完成时间、单个合格工件平均完成时间,并详细描述了各个评价指标的含义与计算方法。
2.对加工中心主轴箱体制造过程应用工艺 FMECA 分析方法,为了解决数据不足的问题,本文将风险优先数定为评判原则,对以故障原因为单位的工艺故障模式应用梯形模糊数评判方法,从而得出各工艺故障模式的风险程度排序,再对加工中心主轴箱体整个工艺系统进行综合评判,确定出系统风险等级,为是否实施改进措施提供依据。对加工中心主轴箱体应用制造工艺 FMECA 方法能够从发生工艺故障的角度制定相应的改进措施,从而直接有效的保障加工中心主轴箱体制造工艺可靠性,并为建立关键工序质量控制点确定出薄弱工序。
3.对加工中心主轴箱体制造过程应用控制图分析方法,利用 MATLAB-GUI(图形用户界面)编制了加工中心主轴箱体制造过程 x ?s 控制图分析软件,该软件具备数据录入、数据计算处理、绘制控制图、判断制造过程是否异常、记录工艺故障数据等功能,通过实例分析表明所编制软件能够准确快速计算样本数据、绘制分析用S 图和 x 图、判断出加工中心主轴箱体制造过程是否存在异常,通过对异常因素和异常样本数据的排除可以生成相应的控制用控制图,用于监测加工中心主轴箱体制造过程的波动情况。对加工中心主轴箱体制造过程应用控制图分析吉林大学硕士学位论文 76 方法,能够从减少制造过程异常波动、预防工艺故障发生的角度保障加工中心主轴箱体制造工艺可靠性,并为建立关键工序质量控制点确定出薄弱工序。
4. 对加工中心主轴箱体制造过程薄弱工序或其它特殊关键工序建立关键工序质量控制点。提出了加工中心主轴箱体制造过程一般关键工序和特殊关键工序的定义,以及确定关键工序需要采用的方法。说明了加工中心主轴箱体制造过程关键工序质量控制点的主要内容,包括提出建立关键工序质量控制点计划、编制
关键工序质量控制点作业文件、建立关键工序控制点档案以及管理关键工序质量控制点。分析了与加工中心主轴箱体制造过程密切相关的 5M1E 因素,并针对各个因素制定相应的控制文件,描述了建立及管理关键工序质量控制点的方法,企业应用实例表明关键工序质量控制点具有很强的可实施性,能够有效的从预防异常因素发生的角度保障加工中心主轴箱体制造工艺可靠性。
6.2 论文展望
目前国内外对数控机床零部件制造工艺可靠性保障方法的研究尚处于起步阶段,本文所研究的加工中心主轴箱体制造工艺可靠性保障方法虽然取得了一定的成果,但由于时间和精力有限,因而还有很多方面值得继续深入研究。
1.本文虽然提出了可用于定量计算的加工中心主轴箱体制造工艺可靠性指标体系,但是并未对建立加工中心主轴箱体的制造工艺可靠性模型进行探讨,可靠性模型能够用于估计或预算制造工艺系统的可靠性,因而值得进一步研究。
2.本文所探讨的控制图分析方法以及编制的 x ?s 控制图分析软件主要是用于判别加工中心主轴箱体制造过程是否存在异常,并不能直接诊断出该异常因素是何种异常、发生在何处,后续研究可以将质量诊断理论应用于加工中心主轴箱体制造过程中,提升排除异常因素效率,保障加工中心主轴箱体制造工艺可靠性。
3.为了能够进一步保障加工中心主轴箱体制造工艺可靠性,可以通过振动传感器、摄像机等对机床、刀具、加工表面情况进行实时监控,并能够在出现异常情况时自动报警。如何能保证监控装置不影响工件的正常加工并自动准确判别出加工异常是一个值得深入研究的课题。
投稿箱:
如果您有机床行业、企业相关新闻稿件发表,或进行资讯合作,欢迎联系本网编辑部, 邮箱:skjcsc@vip.sina.com
如果您有机床行业、企业相关新闻稿件发表,或进行资讯合作,欢迎联系本网编辑部, 邮箱:skjcsc@vip.sina.com
更多本专题新闻
专题点击前十
| 更多