车削用电主轴永磁同步电机电磁与热特性的研究(下)
2017-2-10 来源:沈阳工业大学 作者:闫佳宁
第 5 章 车削用电主轴永磁同步电机的温度场的计算与分析
本课题所设计的 28k W 车削用永磁同步电主轴电机的电磁负荷、功率密度都设计较高,且由于电主轴电机超过额定转速时采用弱磁控制,注入的弱磁电流会使得电机的铜耗急剧增大,从而引起温度升高,严重时甚至烧毁电机的绝缘材料。故本章采用上一章已验证的方法对所设计的车削用电主轴电机进行温度场计算分析。
5.1 水冷结构的选择
水冷系统从结构上的分类如图 5.1 所示,在设计时应遵循以下几点:
(1)流体接触面积尽量大;
(2)管道表面光滑,流体流动过程中沿程阻力小;
(3)流体断面形状规则统一,弯头要少,以减少局部阻力;
(4)流体表面传热系数应足够大,使热交换充分;
(5)使用环境安全、稳定并且维护方便。
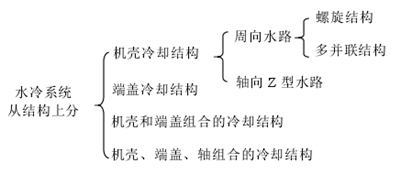
图 5.1 水冷系统的分类
端盖通水的冷却系统虽然效果明显,但解决水道转动密闭问题的技术含量较高,不易实现;机壳端盖组合的水冷结构和机壳、端盖与轴三者组合的水冷结构在冷却效果上略优于单独机壳水冷结构,但这两种结合的结构在工艺制造上相对比较困难;机壳水冷具有生产工艺简单、制造成本低的优点,所以选用机壳水冷结构。
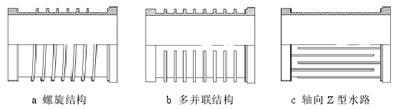
图 5.2 水冷结构图
机壳冷却结构又可分为螺旋结构、多并联结构和轴向 Z 型水路结构,如图 5.2 所示。这三种水路结构的优缺点如表 5.1[57]中所示。
表 5.1 三种水冷结构优缺点对比
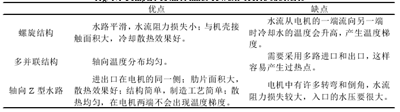
根据上面的介绍,考虑车削用电主轴电机的特点及应用环境,参考西门子 1FE1 系列电主轴的结构,最终选用螺旋结构的水道。
5.2 车削电主轴电机温度场计算前处理
(1)电主轴电机模型及边界条件
车削电主轴电机的电磁方案已由第 2 章确定,依据上一章的建模和等效方法,计算得到电主轴电机的定子绕组等效槽绝缘厚度为 0.9mm。参考 1FE1 系列电主轴电机结构图并进行适当简化,舍去不影响温度场分析的编码器等结构,建立电主轴电机的水冷结构模型如图 5.3。其中,综合衡量电机尺寸及所需的散热量,确定机壳上所开水道数量为 9 个,水道宽度为 6.5mm,高度为 15mm。
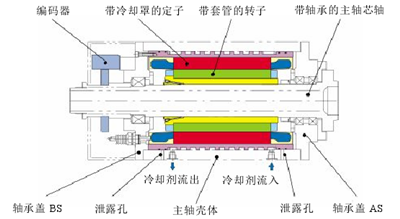
图 5.3 1FE1 系列电机结构图
考虑电机圆周方向对称性,建立电主轴电机的 1/6 结构模型与边界条件如图 5.4 所示,其中 S1 为散热面 WALL,需要设置散热系数,S2 为绝热面 WALL,9 个水道截面为速度入口 S3,与之对应的是压力出口(图中被挡住而未指出),其余一类面 S4 为传热面 INTERFACE。
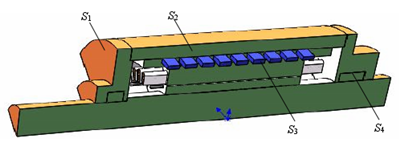
图 5.4 简化后电主轴电机模型及边界条件
(2)电主轴电机的剖分
依然采用前处理软件 Gambit 对模型进行剖分,在流体与温度场计算中,网格划分是基本功。鉴于求解过程对网格质量要求非常高,应尽量剖分为结构化六面体网格,并进行失真度检查,失真度越小越好,尽量不超过 0.75,否则剖分效果不佳会使得计算无法收敛。按照表 5.2 的剖分尺寸进行剖分,得到电机剖分图如图 5.5 所示,检查最大失真度为机壳处 0.63,其余部分更小,剖分效果良好。
表 5.2 28k W 电主轴电机各部位剖分尺寸表
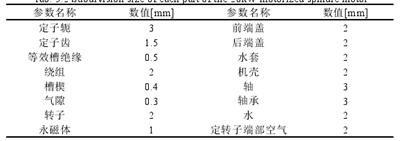
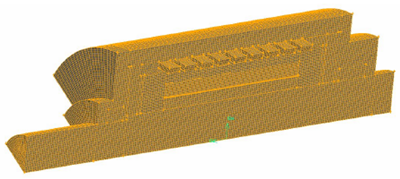
图 5.5 电机的剖分图
除此之外,还要一并设置面边界条件并进行体命名,方便在后续 Fluent 中根据已命名的名称进行查找与设置,完成上述过程后,输出.mesh 文件。
5.3 车削电主轴电机额定时的温度场分析
在Fluent中计算电机温度场的过程如图5.6所示,需要通过电磁场分析或实验得到电机各部位的损耗,采用前处理软件对模型进行剖分和名称定义后,在Fluent中进行设置再开始热计算。依据上一章介绍的方法,此小节仅对所求得的电主轴电机的不同结果进行阐述,相同部分不再重复说明。
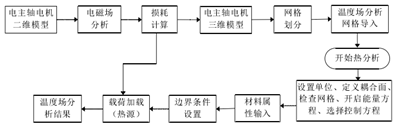
图 5.6 温度场计算过程
5.3.1 电主轴电机的传热系数、初始条件及热源分布
(1)传热系数
依据 4.4.1~4.4.3 节求得的参数如表 5.3 所示,其中电机尺寸不同转速不同,计算得到不同的气隙传热系数;电主轴电机定转子铁心叠压系数为 0.97 有所提高,故轴向传热系数也增大;等效槽绝缘的传热系数经计算为 0.11W/(m?K);所用永磁体的导热系数为 8W/(m?K);轴承采用陶瓷球轴承,导热系数为 32W/(m?K);其余材料与表 4.3 相同。
表 5.3 电主轴电机各部分材料和导热系数
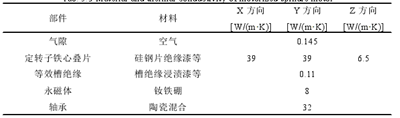
1)给定环境温度为 20℃(293K)。
2)给定速度入口 VELCITY_INLET,速度大小分析如下。使水冷系统内的流体处于湍流状态才能保证水冷散热的高效性,由公式(4.10)计算可得电主轴电机的水力直径为 9.07×10-3m。本课题以雷诺数 2300 区分层流与湍流,要使速度要满足湍流状态,则通过公式(4.11)可求得水速要大于等于 0.20m/s。则由公式(4.12)可知,不同水速对应不同湍流强度,当水速为 0.2m/s 时,湍流强度为 6%。
3)给定压力出口 PRESSURE_OUTLET,零相对压力,即标准大气压 101325Pa。
(3)热源分布
在第 3 章中已经求得了在所采用的弱磁控制方案下的损耗,定子铁耗分别加载到齿部和轭部上,机械损耗加载到轴承上,铜耗加载到绕组上,可以看到永磁体涡流损耗和转子铁耗的数值非常小,换算成生热率后与前几项损耗甚至不在同一数量级上,弱磁时求得各部分的生热率如表中所示。
表 5.4 电机各部分的损耗值和生热率
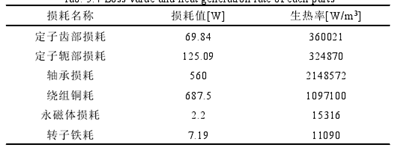
5.3.2 冷却水流速与电主轴电机温升关系研究
已求得使冷却水处于湍流状态的最小水速为 0.2m/s,图 5.7 为水速分别为 0.2m/s,0.5m/s,1m/s 下的水、机壳、水套的温度分布情况。
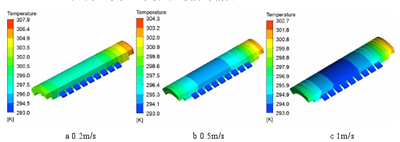
图 5.7 电机定子温度分布图
从图 5.7 可以看到,当水速为 0.2m/s 时,最高温升为 14.9K,机壳与水套的温度均有所上升,说明此时冷却水速度不足,冷却不够彻底,温度仍有下降空间。从 0.2m/s起逐渐增加水速,当水速为 0.5m/s,1m/s 时明显看出随着水速的增加,水套的最高温升有所下降,说明提高水速能够增强冷却效果。由第 4 章的分析并比较电主轴电机的热源分布情况,可知最热点出现在绕组端部。为了寻找最佳水速,绘制电主轴电机的最高温升与冷却水流速关系如图 5.8 所示。当水速超过 2.5m/s 时,即使再增大水速最高温升下降也并不明显,故此电主轴电机的最佳水速(饱和水速)为
2.5m/s。
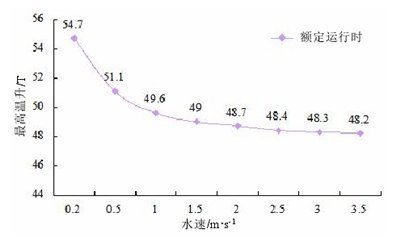
图 5.8 水速与电机最高温升关系
5.4 车削电主轴电机弱磁运行时的温度场分析
5.4.1 电主轴电机弱磁时的温度场分布
电主轴电机弱磁运行时处于去磁状态,定子磁通减少,弱磁电流的注入使得绕组铜耗急剧增大,因此为了避免弱磁运行时温升超过规定限度而损坏绝缘,进行温度场分析尤为重要。表 5.5 为弱磁情况下各部分损耗值及对应的生热率。
表 5.5 弱磁时损耗和生热率
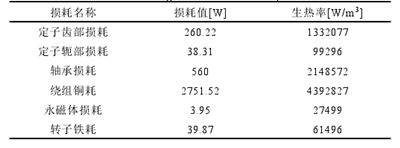
在最佳水速2.5m/s,电主轴电机弱磁时绕组及等效槽绝缘的温度分布如图5.9所示。可以看出端部下层的最高温度为 474.7K,温升更是达到 181.7K,这会严重破坏绝缘,故考虑采用导热系数更高的绝缘材料。
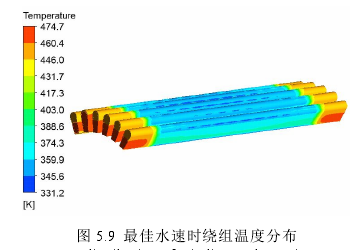
图 5.9 最佳水速时绕组温度分布
5.4.2 高导热槽绝缘材料对温升的影响
上小节温度场计算时,等效槽绝缘的传热系数为 0.11W/(m?K),绕组和槽绝缘的温度分布表明其不足以满足弱磁运行时的传热需求,现考虑采用导热系数更高的绝缘材料:等效传热系数为 0.26W/(m?K)的 F 级绝缘材料、等效传热系数为 0.5W/(m?K)的云母纸绝缘材料,分别计算得到绕组与槽绝缘的温度分布如图 5.10。
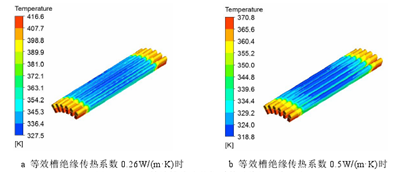
图 5.10 不同等效槽绝缘传热系数时绕组温度分布
明显看出当等效槽绝缘传热系数从 0.11/(m?K)变为 0.26/(m?K)又变为 0.5/(m?K)时,绕组最高温升同时也是电机的最高温升有显著下降,具体对比如图 5.11 所示。这是由于等效槽绝缘包裹着电机的最大热源——绕组,其传热系数的大小直接关系到热量是否能够通过槽绝缘经定子铁心和槽楔气隙有效传递出去,故而等效槽绝缘传热系数的准确计算也至关重要。
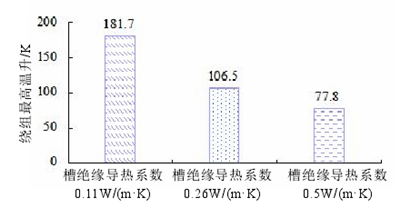
图 5.11 不同等效槽绝缘时温度比较
5.4.3 绕组端部环氧树脂封装对温度场的影响
车削电主轴的运行是对零件精准加工的过程,温度升高会影响加工精度,因而力求降低温升。上一小节分析得到,采用导热系数为 0.5/(m?K)的云母作为槽绝缘材料时,车削电主轴电机的最热点位于端部绕组处,温升达 77.8K。为了解决端部温升偏高的问题,可采用端部封装环氧树脂的方法,这是因为环氧树脂的导热系数远高于端部空气,西门子一款 1FE1 水冷电机定子端部封装如图 5.12 所示。
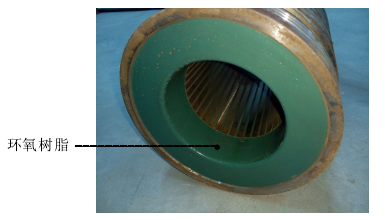
图 5.12 绕组端部封装环氧树脂示意图
经查找得到,6286 进口高温环氧树脂灌封胶(Hasuncast 6286 A&B)是一种低粘度、阻燃环氧数值灌封密封化合物,能长期在 160°温度范围内保持坚硬,并具有良好的导热性,这些特点使其广泛的应用于精密组件的灌封、密封上,其导热系数可达 4.8/(m?K),数据来源于深圳市华胜同创科技有限公司。将车削电主轴电机定子绕组端部用 6286 进口高温环氧树脂封装前后的绕组、槽绝缘及其端部质的温度分布对比如图 5.13 所示。图中 5.13 a 虚线左侧高长方体仍为电机定子与端盖形成的腔内空气,虚线右侧与绕组接触部分为环氧树脂,对称位置类似。从图中可以明显看出,采用环氧树脂时绕组端部最高温升为 66.8K,比未采用环氧树脂温升 77.8K 下降了 11K。从图中的颜色分布来看,a 中虚线中部与最高温度的温差为28.7K,另一侧温差为 16.4K;b 中两端分别相差 24.6K 和 0K。导热性能越好的介质,温度传递越均匀,越接近等温体,显然 b 中采用环氧树脂灌封的方式使得一端的温差更小,温度向外传导更多,较 a 更接近等温体。
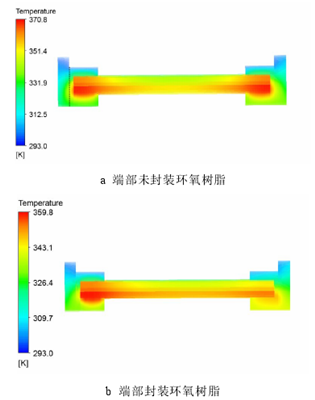
图 5.13 封装环氧树脂前后绕组温度分布
电主轴电机其余部分的最高温升结果如图 5.14 所示。
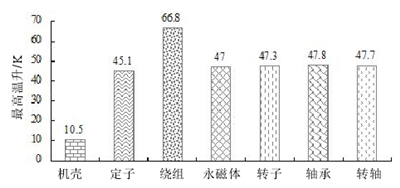
图 5.14 最终方案下电机各部分温度分布
从图 5.14 中可看出,绕组的最高温升为 66.8K,是绝缘能够承受范围内;车削加工中对轴头要求较高,不允许超过 50K 以免影响刀具定位精度,由有限体积计算得到的轴承最高温升为 47.8K,亦满足要求。
5.5 本章小结
本章对所设计的电主轴电机进行了温度场计算分析,得到结论如下:
(1)保证冷却水处于湍流状态的最小水速为 0.2m/s,水速增加到 2.5m/s 后温度几乎没有变化,则此冷却结构应通水速为 2.5m/s,以获得最大供水效能。
(2)此电主轴电机在弱磁时损耗大大增加,温升过高会损坏绝缘,故而考察了采用导热特性优良的云母做槽绝缘时的温升。当等效槽绝缘传热系数为 0.26W/(m?K)时,电机最高温升为 106.5K,而等效槽绝缘传热系数为 0.5W/(m?K)时,电机最高温升为77.8K,降低了 28.7K,更说明等效槽绝缘传热系数的计算对温度场至关重要。
(3)当对绕组端部采用导热系数 4.8W/(m?K)的 6286 进口高温环氧树脂灌封胶时封装时,电机端部最高温升为 66.8K,比未采用时降低了 10K,降低约 14%,此时端部散热情况达到要求,说明端部封装环氧树脂能够显著降低绕组端部温度。其余各部位温升分别为:机壳 10.5K,定子 45.1K,永磁体 47K,转子 47.3K,轴承 47.8K,转轴47.7K,各部位最高温升均在可承受范围内。
从图 5.14 中可看出,绕组的最高温升为 66.8K,是绝缘能够承受范围内;车削加工中对轴头要求较高,不允许超过 50K 以免影响刀具定位精度,由有限体积计算得到的轴承最高温升为 47.8K,亦满足要求。
第 6 章 结论
本文针对车削用电主轴永磁同步电机展开研究,根据车削电主轴电机的空间尺寸和技术指标,设计了一台 6 极 36 槽 28k W 的车削电主轴电机,并对其电磁参数、弱磁性能、损耗及温升进行了分析计算,本文主要工作及结论如下:
(1)结合配套机床的安装尺寸及规定的技术指标进行设计,确定电机电磁方案。建立电机二维模型,采用 Maxwell 2D 进行仿真分析,得到空载、额定负载时的磁密磁力线分布,空载反电势、齿槽转矩、气隙磁密,负载电流、输出转矩等,验证了电磁方案的合理性。
(2)对电机的弱磁特性和损耗进行了较为全面的分析与计算,得到交直轴之间磁路存在交叉饱和影响后,基于场的方法求得直轴电感值,进而得到电机能达到的最高转速为 6936.4r/min,并找到当极限电流为 100A,控制角为 81.8 度时能达到二倍弱磁速度的要求;最后采用基于 Bertotti 铁耗分离计算模型的有限元法对定转子铁心损耗、永磁体涡流损耗进行计算,得到二倍弱磁时,定子铁耗增53.1%,转子铁耗增加455.5%,永磁体涡流损耗增加 54.8%,但后两者从数值来讲较定子铁耗小很多,低频时通常可忽略不计。
(3)对 20k W 永磁同步水冷电机进行了温度场仿真计算,给出了建立三维模型时绕组端盖、轴承、转轴等的等效方法,等效材料传热系数和散热系数的计算,装配间隙的处理以及基本假设和边界条件等。用仿真结果与实验进行对比,得到电机绕组平均温升误差 5%,绕组最高温升误差 6.7%,端盖最高温升 6.5%,满足工程需求,且温度分布趋势与实验结果一致,验证了所用温度场计算方法的准确性。
(4)确立电主轴电机为螺旋周向冷却水道,对其温升进行研究。得到额定时不同冷却水流速下各部分温升情况,找到饱和水速为 2.5m/s,针对弱磁时损耗大大增加的事实,对比了不同等效槽绝缘下的温升情况,得到槽内绝缘材料采用导热系数较高的云母,方能满足散热需求,此时电机最高温升为绕组端部 77.8K;并采用端部封装环氧树脂的方法降低绕组端部温升,当采用导热系数 4.8W/(m.K)的 6286 进口高温环氧树脂灌封胶时,绕组端部最高温升为 66.8K,降低约 14%,其余部位的温升为:机壳 10.5K,定子 45.1K,永磁体 47K,转子 47.3K,轴承 47.8K,转轴 47.7K,各部位最高温升均在可承受范围内。
投稿箱:
如果您有机床行业、企业相关新闻稿件发表,或进行资讯合作,欢迎联系本网编辑部, 邮箱:skjcsc@vip.sina.com
如果您有机床行业、企业相关新闻稿件发表,或进行资讯合作,欢迎联系本网编辑部, 邮箱:skjcsc@vip.sina.com
更多本专题新闻