车削用电主轴永磁同步电机电磁与热特性的研究(上)
2017-2-9 来源:沈阳工业大学 作者:闫佳宁
摘要: 电主轴是将机床主轴与主轴电机融为一体的高新技术产品,具有结构紧凑、重量轻、惯量小、动态特性好等优点,广泛应用于高档数控机床。随着永磁电机性能的不断增强以及在控制精度和调速范围中优越性的突显,永磁电机被越来越多的应用到加工中心的电主轴中。电主轴的轴头对温度变化非常敏感,温升过高会影响刀具的加工精度,严重时甚至引起电机部件变形、破坏电机绝缘材料,故而电主轴温度场的准确计算与分析具有重要意义。本文即是对应用于车削数控机床的电主轴电机展开研究。首先,根据要求的安装尺寸和性能技术指标,参考 SIEMENS 1FE1 系列永磁同步电主轴电机进行车削电主轴电机电磁方案的设计,确定电机的电磁负荷、各部分主要尺寸等关键参数,并采用有限元法进行电磁场数值计算,得到电机的磁场分布、空载反电势、负载转矩等,验证所设计电机电磁设计的合理性。其次,对电机弱磁运行时的磁路特性进行分析,得到交直轴电感,并对所设计电机能够达到的最高转速进行校核计算。此外,对电机所产生的的铁耗、铜耗、机械损耗、杂散损耗进行研究。重点比较电机定、转子铁心损耗以及永磁体涡流损耗在额定与弱磁时的情况。最后,对电机三维模型合理等效,计算各部位等效传热系数、生热率,并考虑装配间隙后,采用有限体积法计算电机的稳态温度分布。比较不同冷却水流速、不同槽绝缘材料下电机的最高温升。针对端部为温升最高点提出采用导热性能好的环氧树脂封装的方法降低绕组温升。本文对于同类型的电主轴永磁同步电机的设计和优化具有一定的参考价值。
关键词:电主轴电机,电磁设计,弱磁,温度场
第 1 章 绪论
1.1 课题的背景及意义
城镇建设和国民经济的发展与制造业息息相关,数控机床作为装备制造行业的核心部件,不断向高速、高效、高精度、高智能化发展,近年来数控机床领域出现了将机床主轴与电机融为一体的新技术,即电主轴技术。电主轴将变频电机的空心转子与机床主轴零件通过过盈配合套装在一起,带冷却机壳的定子直接套装在机床主轴的壳体内,实现了变频电机和机床主轴的“零传动”,此直接传动方式避免了传统皮带或齿轮传动所引起的高速打滑、振动噪声大、惯量大等问题,是数控机床传动系统的重大改革[1]。在多轴联动、复合加工等方面,电主轴单元更具有其它类型单元不可替代的优势[2]。图 1.1 所示的电主轴是将电主轴电机、高速轴承、冷却系统、润滑装置、编码器、换刀装置等部件集成为一体的一套组件,车削中心所使用的电主轴更应具备电机特性优良、热特性稳定等特点。
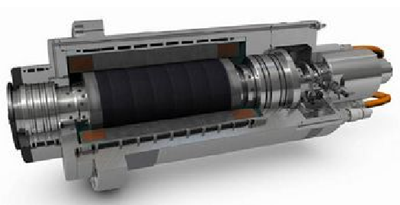
图 1.1 电主轴
电主轴的核心部件是无外壳电主轴电机,它决定着电主轴的最大功率、力矩及性能。过去受永磁电机功率限制,多采用异步电机作为电主轴电机,并通过矢量闭环控制满足定位准停和刚性攻丝的要求[3]。与异步主轴比,永磁同步电机具有结构紧凑、功率密度大、转子几乎不发热的优点,此外较硬的力矩特性更有利于实现电主轴的精密控制,提高加工零件的表面质量[4],近年来永磁同步电主轴已成为学术界的研究热点。我国的永磁同步型电主轴技术水平与欧美工业发达国家比有不小的差距,目前主要依赖进口,由于其结构的特殊性,尚有许多问题亟待解决,进行永磁同步电主轴的电磁设计、参数分析、热特性研究,对提高电主轴单元的性能,形成国产化、标准化、系列化和可批量生产的优质部件具有重要的现实意义。
1.2 课题的国内外现状
1.2.1 电主轴发展现状
20 世纪 60 年代,国内开始了对电主轴技术的研究。此时研制的电主轴功率低,刚度小,主要用于零件内表面的磨削,配备的无内圈式向心推力球轴承也限制了高速电主轴的产业化[5]。随着高速轴承的开发成功,80~90 年代陆续研制出了内圆磨床用、铣削用的高速、高刚度系列电主轴。以能够自主研发电主轴的洛阳轴研科技股份有限公司(原洛阳轴承研究所)为代表,“九五”期间研制的最高转速分别为 8000r/min、10000r/min、12000r/min、15000r/min 的内置式系列电主轴最大转矩可达 129N?m,目前已研制出转速高达 80000r/min 的永磁同步电主轴,但其关键部件(如轴承)仍从国外进口,未能实现完全的国产化,且只能用于低档数控机床中。2003 年湖南大学研制成功了我国首台高速高精密永磁同步电主轴,功率达 35k W,最高转速 18000r/min,回转精度 0.0015mm,填补了国内高速加工领域永磁主轴同步化的空白,使我国机床电主轴的研究取得了较大突破[5]。近年来,哈尔滨工业大学、广东工业大学、沈阳工业大学等高校也陆续进行了电主轴的相关研究,相关产业公司如广州昊志机电股份有限公司、安阳莱必泰中外合资等公司的成立也促进了电主轴的发展,但永磁同步电主轴仍未进入产业化阶段。
国外对电主轴的研究较早,技术水平也处于领先地位,大量电主轴组件生产制造商的出现使电主轴产品部件向系列化、商品化方向发展。世界著名精密机床制造商瑞士 MIKRON 公司所生产的最高60000r/min 的高速电主轴,采用矢量控制技术可满足不同的切削要求,使低转速时输出大扭矩,此外其通过恒温冷却水套对主轴电机和轴承进行冷却,通过高压油雾对复合陶瓷轴承进行润滑。其余著名的有瑞士的 IBAG 公司、德国的 GMN 公司、意大利的 GAMFIOR 公司、瑞士的 FISHER 公司等。表 1.1 给出了以上几家代表性公司应用于数控机床和加工中心的电主轴电机产品的最高参数。
表 1.1 国内外数控机床和加工中心用主要电主轴的参数表
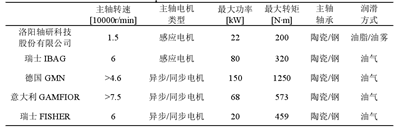
这些公司生产的电主轴较国内比主要有以下特点[5]:(1)功率大、转速高;(2)采用高速、高刚度轴承。主要为陶瓷轴承和液体动静压轴承,空气润滑轴承和磁悬浮轴承用于特殊场合;(3)精密加工与精密装配的工艺水平高;(4)配套控制系统的水平高。包括定转子冷却温度精密控制系统、轴承油气润滑与精密控制系统、主轴变形温度补偿精密控制系统、转子自动平衡系统等。
1.2.2 电主轴电机研究现状
电主轴电机的设计及温升分析综合了电磁学、流体力学、传热学等学科,近年来多位学者从不同方面对其进行了研究。在电机设计方面,文献[6-9]基于经典的麦克斯韦瞬态电磁场分析理论,采用有限元软件 Ansoft 对异步电主轴、永磁无刷直流超高速微细切削电主轴、分段式永磁体转子结构、同步电主轴等不同类型电主轴进行分析,研究了电机参数变化如轴向长度和气隙长度改变、不同极靴形状不同极弧系数等对电机性能的影响,并验证电机设计的合理性。文献[10]用 Speed 软件设计了一台额定功率 35k W,额定转速 3000r/min,最高转速 6000r/min 的交流永磁同步主轴电机,并将 Speed 结果与 Ansoft 结果比较。文献[11]根据瑞士 IBAG 公司 HF230.4A20 型电主轴(异步)的技术要求,借鉴传统电机设计方法,编写了基于 Matlab 的电主轴电机设计程序,并基于遗传算法,以功率密度为目标函数、以结构满足要求为约束对其进行优化。文献[12]探索了逆变器输出的电流高次谐波对高速电主轴(异步)电机效率、功率因数及电磁转矩的影响规律,并开发了一套高速电主轴电机电磁计分析计算源程序,随后开发了动态特性分析源程序以研究高次谐波脉动转矩受电机参数影响的变化规律。在弱磁研究方面,文献[13,14]比较了相同的控制条件下表面式和插入式永磁同步电动机的运行情况,指出插入式永磁同步电动机的转矩输出能力和速度范围都较大。文献[15,16]从“弱磁”的本质出发,分别提出了不同的更易于弱磁扩速的转子结构。文献[17,18]研究了电机定子电阻、电感对弱磁性能的影响,得到电机定子绕组电感越大,恒功率调速效果越好,但也会降低电机的转折速度这一结论。文献[19]采用有限元软件 Flux 计算了分流齿定子结构的永磁同步主轴电机的电磁性能,并研究了交直轴电感准确计算的方法及减小转矩波动的措施。文献[20]通过 Ansoft 计算了考虑交直轴耦合作用情况下的交直轴电感,并在 Matlab/Simulink 环境下搭建了永磁同步电主轴的仿真控制系统。文献[21]对永磁体分段与不分段两种结构形式下磁路饱对电感参数非线性的影响做了分析。
在电主轴电机温度场研究方面,文献[22-24]完成了异步电主轴电机选型、轴承及润滑系统、阶梯过盈套、冷却系统等主要机构参数的设计,将全部损耗粗略按照 2:1分别加载到定子、转子上,应用传热学理论,确定热边界条件,计算了电主轴电机内部各部分的对流换热系数后,采用 Ansys 进行有限元热计算。文献[25]的永磁同步电主轴详细给出了电主轴轴承摩擦损耗的计算方法,但仍粗略认为全部损耗均在定子上,对电主轴冷却系统、油-气润滑系统和内部散热特性进行分析并计算出相应的换热系数后,用 Ansys 分析了轴承温升和主轴热变形的影响因素,最后将永磁同步电主轴与异步电机电主轴的热态特性进行了比较。以上提到的粗略估计损耗后进行热分析并不准确,文献[26]通过电主轴加载试验,测量电主轴运转过程中的电参数,以此为依据计算定转子的主要能量损失——铜损和铁损,这样得到的损耗更具有参考价值。文献[27]对配备静压空气轴承的高速电主轴温度场进行了计算,提出了考虑轴向气流影响的热分析计算流程,并搭建了电主轴的温度测试平台,将测试结果与仿真结果对比分析以验证方法的正确性。文献[28]针对电主轴电机功率损耗发热和高速滚动轴承摩擦发热会引起热变形从而影响机床的加工精度这一问题,从合理场路耦合设计、改进转子、循环冷却结构、轴承及润滑等方面提出了几种具体的处理措施。文献[29]采用 Workbench中热模块计算瞬态温度场,分析了永磁无刷直流电机的温度分布,并基于遗传算法对电机参数进行了优化。
分析电机温度分布的方法主要有简化公式法,等效热路法和数值计算法。简化公式法是采用牛顿散热定律计算出电机各部分的平均温升,工厂中估算经常采用,但不够准确,不能满足日益提高的设计工作的需要。等效热路法将温度场简化成带有集中参数的热路进行温升计算,这里的热阻相当于电路中的电阻,直观简单,工作量不大,工程中应用方便,但无法获取最高点位置及温升。温度场数值解法是利用现代数值分析通过计算机求解电机内的热传递的方法,它解算出的结果具有实际意义,可得到电机内的温度场分布,便于进行变结构、变物理参数的优化研究[30],根据求解思想可分为:有限差分法、有限元法及有限体积法(Finite Volume Methor,简称 FVM)等,而其中有限体积法对于流体场和温度场耦合传热问题的分析更加准确,也是本文采用的温度场研究方法。
1.3 课题的主要研究内容
综上所述,针对永磁同步电主轴电机电磁设计和温升计算通用方法的空白,本课题以一台车削加工中心用电主轴永磁同步电机为研究对象,展开设计、弱磁、损耗、温升如下几个方面的研究:
(1)车削用永磁同步电主轴电机设计参考德国 SIEMENS 1FE1 系列同步主轴的技术要求,分析指定安装空间下电主轴电机主要尺寸、转子参数、定子参数的确定方法,并通过有限元计算软件对所设计的电主轴电机进行电磁场数值分析。
(2)弱磁特性分析与损耗计算
从永磁电机弱磁原理出发,分析永磁电机提高弱磁扩速范围的措施,研究电主轴电机弱磁磁路特性,交直轴电感参数的计算方法,弱磁控制时电机能达到的最高转速。此外,还对电主轴电机定、转子铁心损耗、永磁体涡流损耗以及绕组铜耗和机械损耗的计算方法进行阐述,重点比较弱磁时定、转子铁心损耗以及永磁体涡流损耗的变化。
(3)温度场研究
研究温度场计算所涉及到的简化模型建立方法、传热系数计算方法、装配间隙处理方法等,通过有限体积计算软件对额定和弱磁时温度分布情况进行研究,重点分析不同水速、不同传热系数材料下的温度场特点。
第 2 章 车削用电主轴永磁同步电机的电磁设计和仿真分析
永磁同步电机因其结构紧凑、占用空间小,近年来越来越多的被应用到高精度强力重载的加工中心高速电主轴中[31]。如何设计转子磁路结构、气隙大小、永磁体尺寸等电磁和结构参数使电机单位体积下的功率密度更高、体积和转动惯量相对更小具有重要意义。
为了完成一台车削加工中心用永磁同步电主轴电机的合理设计,本章根据技术要求,结合应用场合的特殊性,参考 SIEMENS 1FE1 系列主轴电机数据,进行了一款车削用电主轴永磁同步电机的电磁方案设计,并建立 Maxwell 2D 有限元计算模型对所设计的电机进行空载和额定运行工况分析。
2.1 车削用电主轴永磁同步电机的电磁设计
2.1.1 电机的技术指标
通过查阅相关资料获知,SIEMENS 同步内装式电机 1FE1 产品系列是配套用于直接驱动电主轴的三相交流电机。内装式电机是一种紧凑型驱动类型,对于这种驱动类型,电机的机械功率可不用传动元件而直接传递到主轴上,例如对于车床,仅通过一个 C 轴驱动即可实现。1FE1 内装式电机的标准规格为液体冷却的、磁铁永久励磁的同步电机,图 2.1 为其实物图,该电机作为组件供货,将电机部件安装到主轴上以后成为一个完整的电主轴单元。
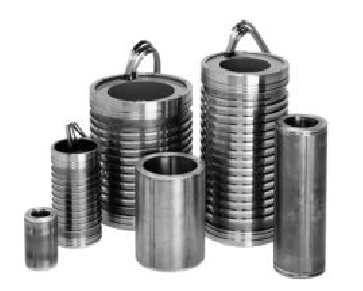
图2.1 SIEMENS 同步内装式电机 1FE1 的组件
1FE1 系列内置电机有两种主要型号:高转矩系列和高转速系列。高转矩系列为 6极或 8 极电机,具有转矩利用极高的特性,适用于具有中等转速的车床和磨床,转速范围为 1:2。高转速系列为 4 极同步电机,用于铣削,优化可用于高最大转速以及转速范围超过 1:4 的场合,对于以最大转速运行的这些电机,需要使用限压模块。课题所需设计的电主轴电机用于加工中心的车床,则参考高转矩系列,在 SIEMENS 设计手册查阅到 1FE1093-6WN10-1BA...(A 表示转子不带套管)的技术数据如表 2.1 所示。
表 2.1 1FE1 的技术数据

1):由于去磁不允许超过最大电流。图 2.2 和表 2.2 给出了与其对应的尺寸数据。
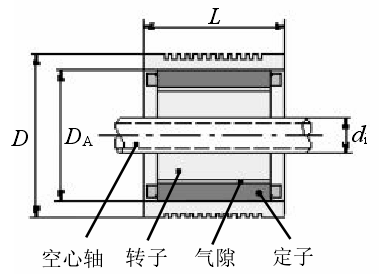
图 2.2 1FE1 电机
表 2.2 1FE1 内装式电机的尺寸

数控车床的运行要求在低速时有优良的加工性能,高速时又要有一定的出力可以提供小进给切削,则弱磁倍数不宜过大,且需与特定机床配套使用,参考以上资料,拟定为二倍弱磁调速范围的 6 极电机,为了满足装配要求,空间尺寸限定为:最大外形尺寸≤205mm×250mm,最小外形尺寸≥92mm,性能要求为:额定电压 380V,额定转矩≥90N?m,额定转速为 3000r/min,最大转速≥6000r/min,则将问题归结为特定空间内的、达到技术指标要求的永磁同步电主轴电机的设计。
2.1.2 基于场路耦合的设计方法
永磁同步电机设计的传统方法是等效磁路设计法,即将空间中实际不均匀的磁场看成多段磁路,并近似认为每段磁路中的磁通沿长度和截面分布均匀,完全用路算代替场算,最后通过系数修正使各段磁路的磁位差与磁场中对应点之间的磁位差相等[32]。
此法需积累大量修正系数,准确进行设计和计算比较困难,精度较低。目前设计电机时通常采用的是场路结合的设计方法,它以有限元分析为基础,电路参量由路算得到,而磁路参量由有限元计算得出。有限元法(Finite Element Method,简称 FEM)是运用变分原理把磁场边值问题转化成相应的变分问题,即能量泛函求极值问题,在离散的网格单元内运用插值函数逼近各点磁位,得到一组多元代数方程组,再加入边界条件对方程组强行修改,可解得每个节点的磁位矢量,这种方法的计算精度比传统的等效磁路法要高出很多,得到普遍采用。商用有限元软件 Maxwell 中的 RMxprt 模块,就是基于电机的等效电路和等效磁路进行有限元计算,它为快速确定电机结构和电磁方案提供了有效途经。首先用直接设计法(根据技术指标以经验数据和公式对电机主要尺寸作原始假设)确定电动机的主要尺寸后,建立 RMxprt 电机模型并导入到 Maxwell 2D 瞬态场进行计算,得到磁场、电磁转矩和电流变化等规律,将这些用场计算出的参量带回到电机的等效磁路中,确定其它的参数和性能。最后考察计算结果,根据性能要求对电机的电磁方案进行调整和优化。该方法充分利用了直接设计法调整结构尺寸的灵活性和有限元法的准确性。图 2.3 为 Maxwell 对电机进行有限元分析的流程图。
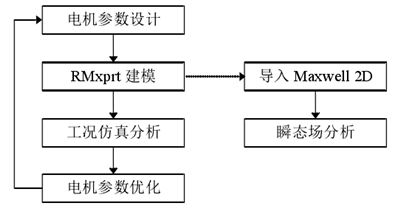
图 2.3 Maxwell 有限元分析流程图
2.1.3 电磁参数的设计
(1)主要尺寸关系
由于车削用电主轴电机需要与机床配套使用,安装尺寸便受到了应用场合的严格限制。电主轴的外壳大小直接决定了电机的定子体积,首先利用公式并结合有限元分析软件推算电磁参数和性能指标,实现电机本体的总体设计。
1)主要尺寸
永磁同步电主轴电机的主要尺寸与普通电机一样,即定子内径i1D 和电枢计算长度efL ,它们可由电机所需的性能指标——最大转矩和动态响应确定。电主轴永磁电机最大电磁转矩emmaxT 与电磁负荷和电机主要尺寸有如下关系
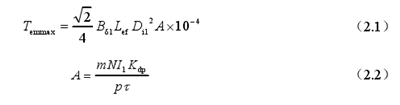

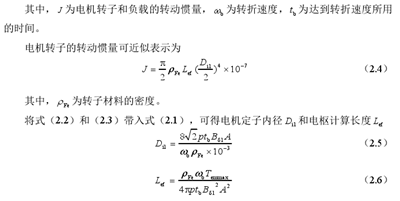
2)气隙长度
永磁同步电机的气隙长度? 比同规格异步电机的气隙长度要大,随着电机中心高和功率等级的提高,同等级永磁同步电机与异步电机的气隙长度差值也越大,且不同用途的永磁电机有不同的气隙取值气隙越大,漏磁越多,气隙磁密越小,故气隙长度不宜过大;较高的功率因数需要较小的气隙长度,但气隙过小又会带来装配困难,由此可见,气隙作为机电能量转换的重要场所,其长度的合理选择尤为重要。对于表面式转子结构的永磁同步电机,由于瓦片形磁极固定在转子表面,气隙长度可大些;对于表面插入式和内置式转子结构的永磁同步电机,通常要求具有一定的恒功率运行的速度范围,则气隙长度不宜过大,否则直轴等效气隙过大,直轴电感过小,弱磁能力不足将难以达到电机的最高转速。一般取值在 0.2~1.2mm 之间。
3)电磁负荷
电主轴电机设计中的关键电磁参数——气隙磁密与线负荷的值是依据制造和运行经验所积累的数据来选取的。电机硅钢片中的磁密值与气隙磁密有很大关系,同时铁心损耗与硅钢片中磁密的平方成正比,为防止过高的磁密使硅钢片饱和以及铁心损耗过大降低电机效率,应在满足电机性能基础上设计较小的气隙磁密[33]。电主轴永磁同步电机的气隙磁密通常在 0.5~0.75T 范围内。考虑电主轴电机的出力情况,期望电机有较大扭矩则需要设计较大的线负荷,而电机的热负荷与线负荷成正比,在保证热负荷不太高或散热条件允许的情况下,可以设计较高的线负荷,通常在 150~500A/cm 之间。
(2)转子参数的设计
1)永磁体的放置方式
永磁同步电主轴电机属于永磁同步电机的一种,根据永磁体在转子位置上的差异,可分为三种不同形式:表贴式、内置式、爪极式。表贴式转子磁路结构的制造工艺简单、成本低,易于转子磁极结构尺寸的优化设计从而获得正弦气隙磁密,较多应用于矩形波永磁同步电机。爪极式转子磁路结构的缺点很多,如极间漏磁大,自起动能力不足等,但由于其相对简单的结构以及制造工艺,在一些小型的发电机等设备上使用比较广泛[34]。机床电主轴永磁电机采用内置式永磁体结构已成为电机设计界的共识,其原因在于[35-37]:
①永磁体磁化方向长度和气隙长度相同时,内置式转子磁路结构的直轴同步电感比表贴贴式大,有利于恒功率弱磁扩速;
②交直轴转子磁路结构不对称产生的磁阻转矩转矩可被充分利用,则可将永磁磁链设计得较低,有助于提高电机的电机的弱磁扩速能力。同时,磁阻转矩的利用可以提高电机单位定子电流产生的转矩,从而提高电机过载能力和功率密度;
③由于永磁体与气隙磁路不直接接触,外表面与定子铁心内圆之间有铁磁物质制成的极靴,可以保护永磁体,同时也可最大限度的避免气隙谐波在永磁体内产生涡流损耗增大温升引起不可逆退磁;
④内置式转子的机械强度比表贴式更高,更适合高速运转。为此,本课题着重研究内置式转子结构,按照永磁体磁化方向与电机旋转方向的空间关系可分为径向式、切向式和混合式三种,如图 2.4 所示。径向式转子结构具有漏磁系数小,极弧系数易控,转子冲片机械强度高,永磁体固定方便,不易变形的优点。与径向式相比,切向式转子结构可提高气隙磁密,但漏磁系数较大,需要采用相应隔磁措施,加大了转子加工与装配的难度。此外切向式转子在高速运行时为克服离心力的作用对机械结构要求较高,增加了制造成本和复杂性。混合式结构综合了径向式与切向式的优点,但结构复杂,生产成本高。故本课题选择采用径向式磁路结构。
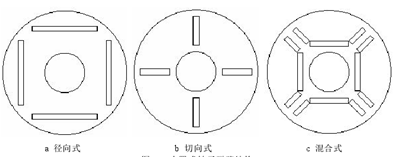
图 2.4 内置式转子磁路结构
径向式磁路结构中磁钢有“一”型、“V”型、“W”型等,制造工艺最为方便的为“一”型磁钢,考虑到本课题电机转子尺寸的限制,安放磁钢的转子轭部体积固定,“V”型、“W”型等占用空间大,与“一”型比较优势并不显著,反而增加机械加工复杂度,使成本升高,故本课题设计时优先选用“一”型磁钢,将其直接嵌入永磁体槽中。且根据本电机配套机床转轴较粗、转子轭部空间极其有限的情况,转轴采用导磁的 45 号钢以在转子中形成完整闭合磁路减少漏磁。
2)永磁体材料
永磁材料种类多样,性能差异也很大,在设计时应考虑电机工作特点予以选择。数控机床用电主轴电机的永磁体材料在选择时应基于以下原则:
①永磁材料具有足够的剩磁密度rB 以满足不同运行工况的磁场需求。较高的rB 可以减小永磁体磁化方向长度,进而增大直轴电感,增强电机弱磁性能,同时可以缩短永磁体宽度,节省成本;
②永磁材料应具有很高的矫顽力cH 和较低的温度系数,从而避免在实际工作环境和高温、短路等极端条件下发生不可逆去磁;
③应具有一定的机械性能以便加工和装配;
④价格适中,不过度增加电机成本。
铁磁材料中的钐钴和钕铁硼在剩磁、矫顽力、磁能积等磁化性能方面较其它材料具有明显优势,且钕铁硼略强于钐钴,钐钴在冷却条件差、温升较大场合的温度特性较钕铁硼更好[10],而本课题所做电主轴电机采用水冷方式,冷却条件充足,又考虑到钕铁硼价格比钐钴低,最终出于磁性能和经济性的综合考量,选择钕铁硼作为本课题
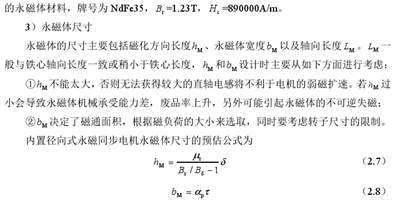
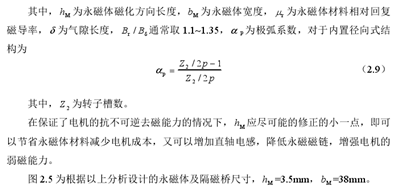
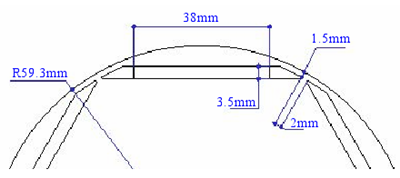
图 2.5 转子永磁体尺寸
(3)定子参数的设计
1)槽数、槽型与尺寸文献对永磁同步电机可能的极数槽数组合作出了清晰的总结,这些可能的组合中有些是分数槽设计,有些是整数槽设计,而这一点关系到永磁电机的齿槽转矩。对于槽/极比为整数时,每个磁极的边缘与槽排列在一起,会产生齿槽转矩;槽/极比为分数时,很少的极边与槽排列在一起,可以有效减小齿槽转矩。在实际应用中,若采用整数槽则需要使用斜极或斜槽等方式来减小齿槽转矩。本课题根据要求,拟定为 6 极、36 槽的常用配合,并采用定子斜槽的方法削弱电机的转矩波动。定子槽型设计时需要有足够大的截面积来放置槽导体,且在槽型允许下使槽满率尽量高些,但槽满率过高会不易嵌线,一般成型绕组机器嵌线控制在 70%以下,功率不大的小型电机人工嵌线可在 75%左右。其次,槽型的选择影响着电机的磁密和磁力线走向,对于平行齿结构,主要用于散线绕组并配以梨型槽和平底槽,非平行齿结构主要用于成型绕组,并配以开口或半开口的矩形槽[38]。电主轴电机的定子槽型一般采用半开口梨型槽,这是因为槽开口较小可以大大减小铁心表面损耗和齿中脉振损耗(即空载铁心附加损耗),且槽面积利用率高,绝缘层不宜受损,冲模寿命长。如图 2.6 a所示,槽口宽s0b 一般取 2~3mm,满足机械加工和下线的情况下,尽量选择较小的值;槽口高s0h 主要从机械加工角度考虑,不能过小,一般取 0.5~2mm;其余尺寸的选取依赖于定子齿磁密t1B 和轭磁密 Bj1 的限制,最佳t1B 取值范围在 1.35~1.55T,Bj1 取值范围在 1.3~1.6T,并尽可能小,以减少电机的铁耗。图 2.6 b 为所设计的电主轴电机的槽型尺寸。
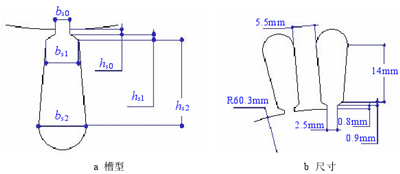
图 2.6 定子槽型及尺寸
2)硅钢片
电机铁心采用的材料为硅钢片,其作用是构成电机的主磁路,不同种类和规格硅钢片的导热性、机械强度和重量相差不大,但导磁特性以及磁场在硅钢片中产生损耗多少的差异很大。硅钢片有热轧硅钢片和冷轧硅钢片之分。前者价格相对较低,但由于热轧工艺限制,通常较厚,使铁心的涡流损耗较大,此外其导磁特性也略低于冷轧硅钢片,若出于成本考虑,可应用于对性能要求不高的场合,现如今的电机都采用冷轧硅钢片。按照微观晶粒的排布又可将冷轧硅钢片分为冷轧取向硅钢片和冷轧无取向硅钢片,前者晶粒呈现各向异性,主要用于变压器中,后者晶粒呈现各向同性,主要用于电机中[10]。国内的冷轧无取向硅钢片一般为 0.35mm 厚和 0.5mm 厚,电主轴电机有调速要求,超过额定转速时频率升高,铁耗会增大,出于减小铁心涡流损耗的考虑,应尽可能选取薄的硅钢片。随着叠压技术的进步,目前 0.35mm 的硅钢片叠压系数能够做到 0.97,叠压系数高说明硅钢片间的非磁性材料少,导磁率高,性能好。结合以上分析,本课题选用叠压系数为 0.97 的 DW310_35 作为硅钢片材料。
3)绕组
交流绕组可分为单层绕组和双层绕组,单层绕组嵌线方便、槽利用率高,主要用于 10k W 以下的小型电机。双层绕组主要用于大、中型电机,并利用短距与分布的方法改善感应电动势和磁动势波形,使电机获得较好的电磁性能。双层绕组又可分为波绕组和叠绕组,波绕组用于多极、导线截面较大的交流电机以节约极间连接用铜,叠绕组为多匝线圈,多用于额定电压不太大的中、小型感应电机和同步电机的定子绕组中[39]。本课题设计的电主轴电机定子采用星型连接,可以消除线电压中的三次谐波,此外采用双层短距设计,使基波分量尽可能大谐波分量尽可能小,节距为 5 以削弱 5、7 次谐波,三路并联,每槽 26 匝,线径 1.18mm,两股绞线并绕。
表 2.3 为结合以上内容设计的 28k W 车削用永磁同步电主轴电机的主要参数表。
表 2.3 车削用电主轴永磁同步电机主要参数
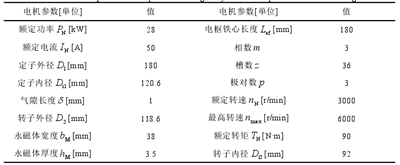
2.1.4 轴承的选用
电主轴中最常采用的支撑轴承为滚动轴承,且以高速性能较好的角接触球滚动轴承使用最为广泛,流体静压轴承和磁悬浮轴承分别因标准化程度低和电气控制复杂而普及不高。为减小轴承高速运转时滚球所产生的巨大离心力和陀螺力矩带来的动载荷,常将滚球用 Si3N4 制造。试验表明,角接触混合陶瓷球轴承的工作寿命是同规格、同精度钢质轴承的 3~6 倍,同时轴承温升可降低 30%~40%[40]。将其配以永久脂润滑时的最高转速可与轴承钢加油气润滑组合时相同,还省去了一套油气润滑部件,使维护工作大为简化[41]。
2.2 车削用电主轴永磁同步电机的有限元计算分析
为准确计算电机的电磁性能,对 2.3 节所设计的 28k W 车削用电主轴永磁同步电机进行电磁场有限元数值计算,利用有限元分析软件 Maxwell 分别进行空载运行与额定负载运行情况下的仿真分析,判定电机设计的合理性。
2.2.1 空载特性分析
电机在空载时只有永磁体励磁,将 RMxprt 模型一键导入到 Maxwell 2D 后,此时软件已自动设置将 A 相绕组轴线与转子 d 轴对齐,再将全部位于 d 轴的定子电流源赋为零,即为电机空载状态,得到电机空载磁力线分布与磁密云图如图 2.7 所示。从图2.7 a 可以看出空载时电机磁力线分布均匀,位于永磁体中心线处的定子齿磁力线较密集,相邻永磁体间存在一小部分漏磁。从图 2.7 b 可以看出磁感应强度在永磁体隔磁桥处最大,最大值约为 2.27T,此处磁密过饱和是为了限制永磁体的极间漏磁,使得永磁体所提供的磁通更多的经由气隙进入定子,与相邻的永磁体有效匝链,构成主磁通。定子齿部磁密不超过 1.35T,轭部磁密不超过 1.55T。
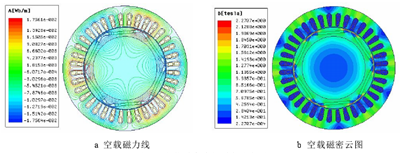
图 2.7 空载磁力线与磁密分布图
空载反电势是永磁电机的重要参数,电机在运行过程中,反电势需低于供电电压才能保证电机处于电动状态,空载反电势的大小也直接影响着电机的调速性能。兼顾变频器容量及电机输出转矩能力,本文将电机反电势设计在 178V 左右,图 2.8 为设计电机的空载三相反电势波形。从图中可知,空载反电势三相对称,且互差 120°,每相有效值约为 178V,相比于供电电压 220V 留有一定裕量,使得起动时电流能快速灌入,保证了车削机床电机的快速响应特性。
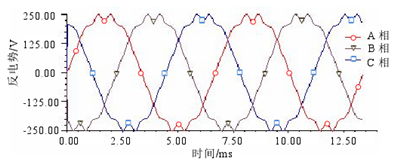
图 2.8 空载反电势
图 2.9 和图 2.10 分别为空载气隙磁密和空载齿槽转矩图。
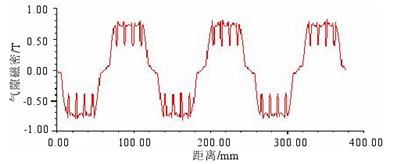
图 2.9 空载气隙磁密
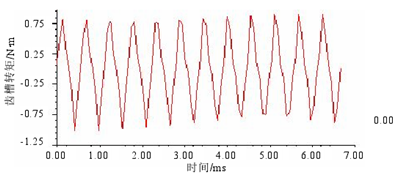
图 2.10 空载齿槽转矩
从图 2.9 中可以清楚看出该电机为六极电机,每极下气隙磁密突然减小是由于定子开槽所致,定子槽口与永磁体相互作用,开槽处磁阻变大则磁密减小。气隙磁密幅值约为 0.7T。图 2.10 为电机在一个周期内的空载齿槽转矩波形,最大波动约为 1.82N?m,占额定转矩的 2.02%。
2.2.2 额定负载特性分析
给定子三相绕组施加额定电压源,且采用软件自动设置的机械瞬态,得到额定负载下电机磁力线分布和磁密分布云图如图 2.11 所示。可以看出额定负载情况下,电机的磁力线分布发生了一定的畸变,这是由于永磁同步电动机的电枢反应造成的。定子轭部磁密最大不超过 1.72T,齿部磁密最大值不超过 1.75T,定子磁密较空载运行时有所增加,说明额定负载运行时,电枢反应使得电机处于増磁状态。
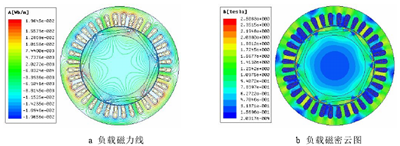
图 2.11 额定负载磁力线与磁密分布
图 2.12 为额定负载运行一段时间稳定后的电机相电压曲线。作为电动机,额定运行时要保证电机端电压不能超过供电电压。从图中可知,额定负载时相电压有效值约为 215V,接近并未超过供电电压 220V,为正常电动状态。
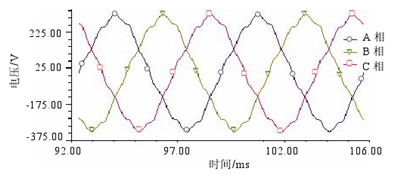
图 2.12 额定负载反电势
图 2.13 为额定负载时的三相电流,100ms 后逐渐趋于稳定,有效值为约 53A,与额定电流 50A 相差 6%。
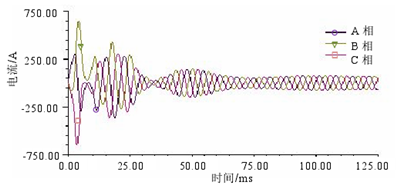
图 2.13 额定负载电流
图 2.14 为电机额定时的输出转矩,稳定后转矩平均值约为 90.2N?m,达到最初要设计一台输出转矩达到 90N?m 的电机这一要求。但可以看出转矩波动为 10.39N?m,占额定转矩的 11.5%,波动过大无法满足车削机床低速平稳性、高定位精度的需求,需进行改进。

图 2.14 额定输出转矩
影响电机低速转矩波动的主要原因有电动势谐波或电流非正弦而产生的波纹转矩和齿槽转矩。减小转矩波动可以采取的措施有:合理选择定子槽数,使电机绕组采用短距分布绕组或采用分数槽结构;增大气隙长度;进行气隙磁密波形的优化;减小定子槽口宽度、采用磁性槽楔[42],或采用无齿槽定子结构;采用定子斜槽或转子斜极;采用阻尼绕组等。出于电磁方案已经确定的考虑,拟采用定子斜槽的方式来改善电机的转矩波动情况。
现在不改动电机尺寸的前提下,在 RMxprt 中设置 Skew Width 为 1,即定子斜 1个齿距,并导入到 Maxwell 3D 中进行有限元分析,得到转矩平均值依然约为 90N?m。未采用斜槽与采用斜槽稳定后的输出转矩对比如图 2.15 所示。从图中可以明显看出转矩波动有所减小,采用斜槽后转矩的波动大小约为 1.6N?m,波动百分比为 2%,说明定子斜槽有效的减小了电机的转矩波动,提高了车削电主轴电机在加工中的精度,并达到了设计要求。
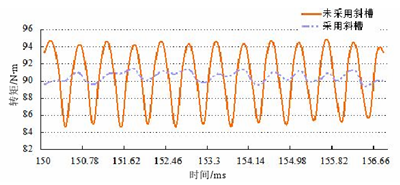
图 2.15 转矩对比图
此外需要额外说明的是,在图 2.13 和图 2.14 中计算开始的瞬间,电流和转矩分别有一个或正向或负向的冲击,这是因为转子处于恒转速运行时,仿真对应的工况是转子在零时刻前就已达到其额定转速,零时刻突然加电,故在到稳定运行前存在正负震荡的情况,100ms 以后趋于稳定,此阶段不同于电机实际的起动情况,分析时应舍去。
2.3 本章小结
本章根据性能指标要求和机床规定的空间安装尺寸,设计了一台 28k W 车削电主轴永磁同步电机,并进行有限元仿真分析,验证电磁设计方案合理性,得到结论如下:
(1)所设计的电主轴电机转子采用内置“一”型永磁体,牌号为 d Fe35,永磁体磁化方向长度 3.5mm,宽度 38mm。定子采用半开口梨型槽并确定了尺寸,硅钢片采用 DW310_35,叠压系数 0.97,绕组为双层短距设计,每槽 26 匝,两股绞线并绕。其它设计参数为额定功率 28k W,额定转矩 90N?m,额定电流 50A,定子外径 180mm,定子内径 120.6mm,气隙长度 1mm,6 极 36 槽配合。此外,确定此电主轴电机的轴承为角接触混合陶瓷轴承,并配以永久脂润滑。
(2)采用有限元分析得到电机磁力线和磁密分布合理,空载反电势为 178V,空载气隙磁密为 0.7T,空载齿槽转矩占额定转矩的 2.02%,负载转矩波动在采取斜槽方式后大大减小,由 11.5%降低到 2,可以满足车削中心对低速平稳性的要求。第 3 章 车削用电主轴永磁同步电机的弱磁分析与损耗计算车削中心要求有较广的加工范围以满足不同加工进给速度的要求——低速时有较大输出转矩以进行大进给切削,高速时恒功率调速以满足高转速小切削量的要求。“弱磁”问题作为永磁同步电机的重点和难点一直阻碍着永磁电机在数控机床和加工中心中的进一步发展。对于低速要求高的电主轴,基速下采用高性能的矢量变频控制,超过额定转速时需要采用弱磁控制,对于设计好的电机在某种弱磁控制方案下能否达到所需转速的研究便十分重要。与此同时,弱磁控制时若是注入弱磁电流将使电机的损耗增加、温升升高,为了保证电主轴的热态性能稳定,准确计算损耗是进行热态性能分析的前提。
投稿箱:
如果您有机床行业、企业相关新闻稿件发表,或进行资讯合作,欢迎联系本网编辑部, 邮箱:skjcsc@vip.sina.com
如果您有机床行业、企业相关新闻稿件发表,或进行资讯合作,欢迎联系本网编辑部, 邮箱:skjcsc@vip.sina.com
更多本专题新闻