航空整体叶轮五轴数控加工仿真及参数优化研究 (中)
2016-11-21 来源:天津职业技术师范大学 作者:卢辉
第 3 章 叶轮五轴数控加工后处理
3.1 概述
现在叶轮粗加工大部分是使用球头铣刀五轴联动加工,由于球头铣刀切削性能差,故叶轮粗加工效率低下[49-51]。本文将使用立铣刀采用定轴加工方式进行叶轮的粗加工。目前针对五轴机床定轴加工的后处理算法是基于刀尖跟随功能(即始终保持刀尖相对于工件的位置保持不变)的。这种后处理算法简单不涉及X、Y、Z坐标变换,但后处理得到的NC代码不能输出圆弧插补且加工时不能锁定旋转轴,加工精度及刚性有待提高。为了实现航空整体叶轮的高速高效加工,针对定轴加工叶轮粗加工,将使用UG8.5软件后处理构造器对本文做实验使用HSC75 linear五轴高速加工中心编写后处理文件。
3.2 后处理算法
3.2.1 机床结构分析
在实际生产中,五轴数控加工机床一般指具有3个线性移动轴与两个旋转轴的机床。五轴联动数控机床有3种基本机构类型:刀具摆动与工作台回转、工作台双回转及刀具双摆动[52]。本文用于叶轮加工的是DMG公司的HSC75 linear五轴高速加工中心,控制系统是海德汉i TNC530,该五轴机床是刀具摆动与工作台回转,其空间运动坐标系如图3-1所示,C轴是依附在X轴上,工作台沿X轴作线性移动,工作台绕Z轴作旋转运动;B轴依附在
Z轴上,Z轴依附在Y轴上,主轴绕着Y轴作旋转运动。该设备的线性轴加工范围:X、Y、Z线性轴分别为885 mm、600 mm、600 mm,B轴的回转范围是–5°~110°,C轴的回转范围是–360°~360°。
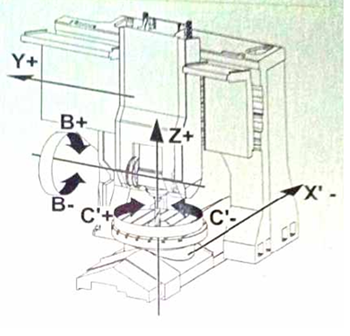
图3-1 机床空间运动坐标系
3.2.2 齐次坐标变换运算
海德汉i TNC530数控系统的圆弧指令只能在工件坐标系的主平面(XY、YZ、XZ)或者是平行于主平面的加工平面上使用。海德汉i TNC530系统的倾斜加工面功能可以对工件坐标系围绕坐标原点进行旋转,使得工件坐标的XY平面平行加工平面,这样就可以在所加工的平面上输出圆弧指令。由于工件坐标系进行了旋转变换,所以数控程序的坐标值也需要进行齐次坐标变换。
为了叙述方便,本文将旋转工件坐标系后得到的坐标系称为特征坐标系。使用UG编制五轴刀具轨迹时,一般只设定一个工件坐标系,这个坐标系必须与机床的加工坐标一致。为了更好地解释工件坐标系与特征坐标系的关系,本文列举一个简单的倾斜面加工的例子进行说明,如图3-2和图3-3所示。
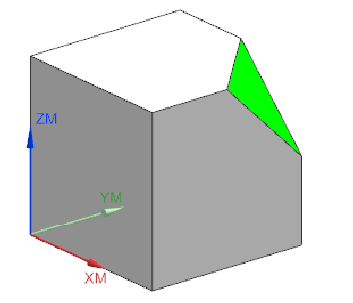
图 3-2 工件坐标系
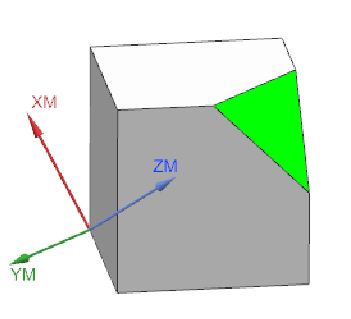
图 3-3 特征坐标系
如图3-2所示,绿色的平面是要加工的倾斜面。UG进行数控程序编制是在工件坐标系下计算的。而倾斜面加工的刀位文件是特征坐标系的机床运动坐标,需要通过后置处理将工件坐标系下的刀位数据转化为特征坐标系下的刀位数据。后置处理的关键技术是将工件坐标系下的刀位数据进行齐次坐标变换。 根据齐次坐标变换可知,已知某个直角坐标系中的一点坐标值,那么该点在另一个直角坐标系中的坐标可通过齐次坐标变换求得[53],对应于轴Y、Z作转角为θ的旋转变换,分别可得:
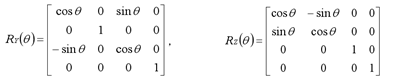
设u(Ux Uy Uz)为工件坐标系中的刀轴方向矢量,r(Xw Yw Zw)为工件坐标系中的刀位点位置矢量,h(Xs Ys Zs)为特征坐标系的刀位点位置矢量,旋转轴 B、C 初始角度分别为φB和φC。由齐次变换推导出:


将
和
代入(1)和(2),可得


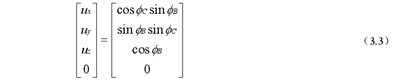
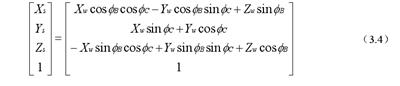
由式(3.3)和(3.4)得特征坐标系的刀位点位置矢量的计算公式:
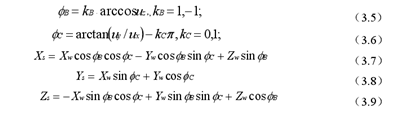
因为kB=1,-1 所以φB可能有2个解,根据旋转轴B轴的回转范围是10°~-110°来选取φB。在确定了φB后,在式(3.3)中,φC满足cosφC=ux/sinφB和sinφC=uy/sinφB sinφC=uy/sinφB ,所以φB和φC是唯一对应的。
3.3 后处理文件编写
3.3.1 UG后处理构造器简介
使用UG加工模块生成的刀轨包含着GOTO点和其他机床控制的指令信息。由于不同机床数控系统对数控代码的要求不一样,所以UG生成的刀轨源文件不能直接用于机床。因此,刀轨源文件必须经过处理转成特定的机床所能接受的数控代码,这一过程称为“后处理”。UG NX8.5提供了一个性能优异的后处理工具——NX/Post,利用它可以建立和机床控制系统相关的事件处理文件和事件定义文件,完成简单或任意复杂机床的后处理。利用UG后处理构造器建立后处理文件的过程如图3-4所示。
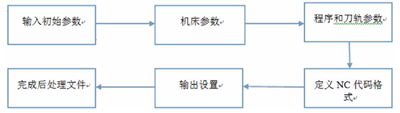
图3-4 建立后处理文件
3.3.2 后处理文件编写
启动Post Builder,在后处理名称中输入D750_post,选择公制的后处理输出单位、选择五轴带转头和轮盘的机床,选择Heidenhain控制器,完成初始参数的输入如图3-5所示。
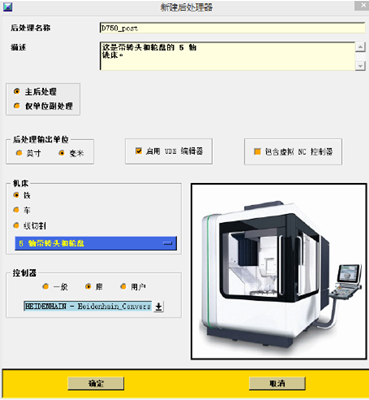
图3-5 输入初始参数
下面将输入机床参数。设置机床X轴行程为885 mm ,Y和Z轴行程设置为600 mm,将机床主轴矢量设置为I0、J0、K1,即将Z轴方向设置为主轴。在UG后处理构造器中,第四轴是非依赖轴,第五轴是依赖轴。对于五轴带一转台一摆头机床,摆头永远是第四轴,而转台则是第五轴。所以B轴为机床第四轴,旋转角度为–5°~110°,C轴为机床第五轴,旋转角度为–360°~360°。机床参数和机床示意图如3-6所示。
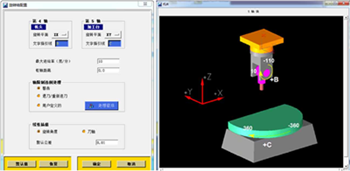
图3-6 机床参数和机床示意图
设置完机床参数之后,进行程序和刀轨的设置,这也是建立后处理文件最重要的步骤。
这个步骤主要完成程序头定义和程序尾的定义。UG后处理的事件处理文件是用TCL语言进行编写的,TCL语言定义了每一个事件的处理方式。本文使用TCL语言编写的定义程序头的事件处理文件,下面这是程序头的部分TCL程序。
MOM_output_literal "BEGIN PGM $file_name $mom_user_output_unit"
MOM_output_literal "M129"
MOM_output_literal "M140 MB MAX"
MOM_output_literal "PLANE RESET STAY"
MOM_output_literal "CYCL DEF 19.0 WORKING PLANE"
MOM_output_literal "CYCL DEF 19.1"
MOM_output_literal "CYCL DEF 247 DATUM SETTING~ "
MOM_set_seq_off
MOM_output_literal "Q339=1; DATUM NUMBER"
MOM_set_seq_on
其中,"BEGIN PGM $file_name $mom_user_output_unit"是定义输出数控程序的名称和坐标值的单位;"M129"是取消M128(刀尖跟随)功能;"PLANE RESET STAY"、"CYCL DEF 19.0 WORKING PLANE"和"CYCL DEF 19.1"是取消倾斜加工面功能;"CYCL DEF 247 DATUM SETTING~ "和"Q339=1; DATUM NUMBER"是启动预设表中1号原点作为加工坐标系的原点;MOM_set_seq_off是关闭数控程序的行号;MOM_set_seq_on是开启数控程序的行号。
与程序头定义相比,程序尾定义相对简单。程序尾主要定义停止主轴转速、关闭切削液、执行各运动轴回零动作等。其部分TCL代码如下。
MOM_output_literal "M129"
MOM_output_literal "M09"
MOM_output_literal "M5"
MOM_output_literal "L X-450. Y-10. M91"
MOM_output_literal "L B0.0 C0.0"
MOM_output_literal "M30"
MOM_output_literal "END PGM 100 MM "
NC代码格式定义主要是数控代码的定义和输出坐标值小数点后几位数,输出设置是定义后处理得到的数控程序文件的格式。完成以上设置后,点击保存文件完成后处理文件的建立。
3.4 验证后处理文件
为了确保后处理文件正确性,需要进行实验验证。首先在UG中建立零件模型,如图3-7所示。这是一个典型的五轴倾斜面加工零件,侧面的沉头孔需要五轴机床倾斜主轴头加工。生成刀位文件的主要操作是设置加工坐标系、零件毛坯、安全平面等;选择深度加工轮廓、指定切削区域、切削参数等相关参数后可生成CLSF格式的刀位文件,部分代码如图3-8所示。
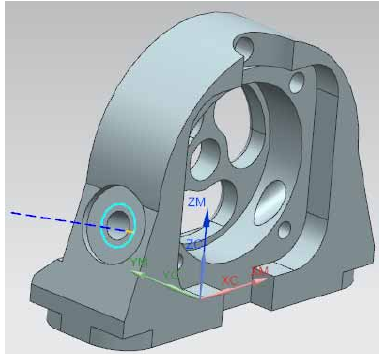
图3-7 机床参数和机床示意图
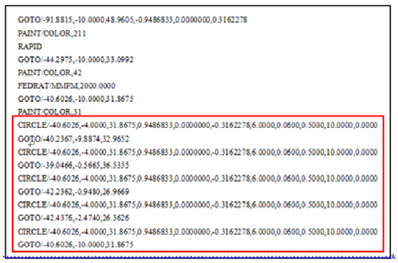
图3-8 CLSF文件代码
通过开发后处理文件将CLSF刀位轨迹转换成NC代码,得到与CLSF语言源程序相对应的海德汉i TNC530数控加工程序,如图3-9所示。
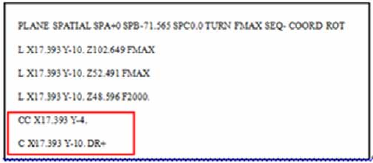
图3-9 NC文件代码
将两程序对比可知,图3-8红框中CLSF刀位轨迹的坐标经过后处理转变成图3-9红框中的圆弧指令。在实际加工之前,为了防止撞刀事故的发生,先在VERICUT软件上进行仿真,如图3-10所示。从VERICUT的仿真结果看,并没有发现过切的红色区域,说明后处理的程序没有问题。将数控加工程序传输到机床进行实际加工,验证了上述后置处理算法的正确性。
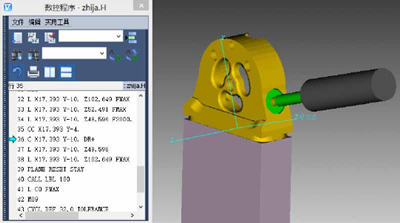
图3-10 VERICUT仿真结果
3.5 叶轮加工程序后处理
通过前面验证本章编写的后处理文件是可行的,下面使用该后处理文件对航空整体叶轮刀具轨迹进行后处理。如图3-11所示,是对叶轮粗加工程序进行后处理,并在VERICUT软件中进行数控仿真,检查粗加工程序。由仿真结果可知,加工程序中输出圆弧指令能够减少直线插补误差,提高加工精度。
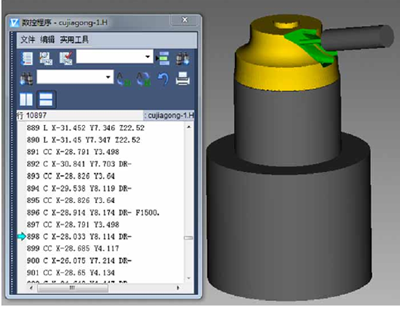
图3-11 后处理得到叶轮程序
3.6 本章小结
本节编写的后处理文件可以实现五轴定轴加工方法进行叶轮粗加工。首先针对海德汉i TNC530数控系统的倾斜加工面功能,通过对CLSF刀位轨迹进行齐次变换运算,提出了机床运动坐标的数控程序后处理算法。使用UG NX8.5/Post Builder编写后处理文件,通过NC代码分析、程序仿真及实际加工验证了后处理方法的正确性,同时对航空整体叶轮加工刀具轨迹进行后处理,能够提高叶轮的加工精度。该方法可以为五轴机床加工带倾斜面类零件有指导意义,对提高五轴加工的生产效率有着重要意义。
第 4 章 航空整体叶轮加工的颤振稳定域获取
4.1 概述
高速铣削加工由于其具有较高的材料去除率,可大大缩短切削加工时间,提高加工效率,因此被广泛应用于航空、航天等领域。而在航空整体叶轮加工中,颤振制约高速切削的使用,降低叶轮加工效率。颤振是发生在切削过程中一种强烈的自激振动,颤振会降低切削效率、降低零件的加工精度、破坏零件的表面粗糙度、损坏刀具甚至机床本身[54]。切削加工中避免出现颤振的有效方法是对机床-刀具系统、机床-工件系统进行颤振稳定域的分析。
4.2 航空整体叶轮加工的机床和刀具
航空整体叶轮因其曲面的复杂性和加工精度高,使其成为典型的难加工零件,因此本文选用的是DMG公司的HSC75 linear五轴高速加工中心,控制系统是海德汉i TNC530。HSC75五轴机床B轴是刀具摆动,C轴是工作台旋转。
本文中研究的整体叶轮片型面为直纹面,总叶片数为12个,主叶片与分流叶片各6个,叶轮直径为125mm,高度为60mm,叶片最厚处为4mm,相邻主叶片与分流叶片间最小间距为7.3mm,叶根圆角半径为3mm,如图4-1所示。
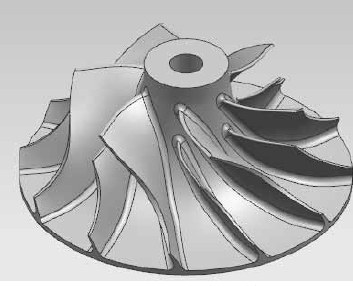
图 4-1 整体式叶轮
根据相邻主叶片与分流叶片间最小间距为7.3mm,本文选取直径为6mm硬质合金立铣刀进行粗加工;根据叶根圆角半径的大小,采用R3硬质合金球头铣刀进行叶轮的半精加工和精加工。高速切削的刀具料要求具有高的热硬性和化学稳定性,如高熔点、高的氧化温度、好的耐热性、强的热冲击性和高温强度[22]。不同的刀具材料,适用加工的工件材料不同,针对本文叶轮材料和工艺安排,选用硬质合金圆柱立铣刀进行粗加工和球头铣刀进行精加工。硬质合金圆柱立铣刀材质为CO10%,WC90%(德国进口原材料),具有极细微粒的碳化钨母材,硬度高,带有Ti Al N涂层[55]。硬质合金铣刀参数见表4-1。
表4-1 硬质合金铣刀参数见表

4.3 基于Cutpro9.0的颤振稳定域获取
目前,针对颤振稳定域分析应用软件有加拿大UBC大学MAL实验室研发的Cutpro9.0、英国Technicut公司开发的METALMAX软件、北航自主开发的铣削加工动力学仿真系统Simu Cut和数控机床动力学特性参数测试与分析Dyna Cut系统。使用Cutpro9.0动力学仿真软件,能够仿真切削过程预测主轴功率、切削力、表面粗糙度等,为优化切削参数提供参考。该系统由享有国际声誉的制造自动化实验室(MAL)开发,Cutpro9.0在金属切削领域为提高生产率提供了很好的解决方案,所以本文采用Cutpro9.0获取颤振稳定域。
Cutpro9.0是一款高级加工软件,Cutpro9.0软件包括2.5轴铣削模块、车削模块、镗削模块、模态分析模块、传函测量软件MALTF、基于PC的数据采集和分析软件Mal DAQ、主轴设计与分析系统SPINDLEPRO和虚拟CNC模块组成。并且此软件可协助解决切削加工问题包括:确定无颤振条件下的主轴转速、进给量和切深,在保证良好表面质量的前提下提高材料的去除速率;以较高的材料去除速率加工淬硬钢宇航耐热合金,确保在加工过程中不发生颤振和崩刃;确定在给定的加工条件下机床和复杂刀具能否提供足够的转矩、功率和刚度进行加工零件;可利用经过科学验证的软件在全球重要厂商提高加工生产率;快速确定并调整弱刚性夹具和加工过程中的安装问题。
4.3.1 基于Cutpro9.0颤振稳定域获取过程
在进行颤振稳定域仿真之前,首先要对机床-刀具系统和机床-工件系统进行动力学分析,即要获取加工系统的频响函数。一般情况下系统传递函数的获取方法有两种途径:一种是试验模态分析法,对于复杂系统和几何结构相对稳定的系统采用该方法最为有效;另一种是理论模态分析法,即采用基于有限元分析的方法[56]。本节中的被测系统频响函数FRF的获取可以通过Cutpro9.0软件频率响应函数(FRF)或传递函数(TF)测量模块得到。频率响应函数(FRF)或传递函数(TF)测量模块都有一个基于脉冲锤测试的TF测量系统。在脉冲模式下的传输函数测量采取的多个样本取平均,得到一个传递函数的更好表达。机床的振动在加工行业中起到重要的作用,因为过度的振动会导致工件表面光洁度较差,刀具磨损,并可能损坏主轴系统。首先,一个简单的结构只有单一自由(单自由度)可以用一个通用公式来建模。

其中m是质量,c是阻尼的系数,k是系统的刚度,当阻尼常数为0时,系统振荡的固有频率ωn。当阻尼存在,我们获得阻尼固有频率ωd时需要考虑的阻尼比ε。此外,可以发现谐振角频率ωr是阻尼固有频率的最大值。
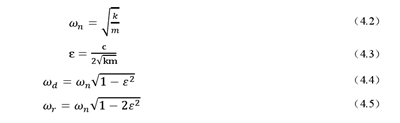
所有的机械系统都会表现出一些阻尼,并且大多数金属结构的阻尼比ε<0.05或更小。通常情况下,当系统的阻尼比很小或系统在共振频率时可以忽略阻尼对系统的影响。通过假设x(t) = X sin(ωt +f )我们可以得到下面的公式:

所得谐波振动的振幅和相位是

传递函数的实部和虚部如下:

当 r = ω /ωn和Φ(ω) = G(ω ) + j H (ω),通常情况下,Φ(ω)被称为系统的频率响应函数,是位移的复振幅与强迫函数F的大小的比率。另外,Φ(ω)的实部和虚部(s平面)被称为传递函数(TF)。
Cutpro9.0颤振稳定域获取过程:
1.根据加工工艺要求,确定加工机床、刀具;
2.通过锤击实验获得加工系统(机床-刀具系统和机床-工件系统)的传递函数;
3.如果所研究的工件材料已存在于Cutpro9.0软件中,仿真时可直接使用;否则应通过切削力辨识实验,获取刀具-材料对切削力系数。切削力辨识实验需制作专门的试件并配备测力系统。
4.由加工工艺确定切削宽度;
5.进行颤振稳定域仿真,获取无颤振条件下的主轴转速和轴向切深关系图(稳定域叶瓣图);
6.根据仿真出的颤振稳定域图形及考虑具体加工条件限制确定优化的主轴转速和轴向切深。
4.3.2 锤击试验
锤击试验是单输入单输出模态实验的主要方法之一[57]。在上个世纪80年就已经开始使用锤击实验获取研究对象的动态特性,由于此方法方便简单故在机械工程方面应用广泛[58]。锤击实验是在刀具与机床组合系统的情况下进行的,使用力锤对测试点进行敲击,并用加速度传感器采集刀尖点的振动信号。实验装置图如图4-2所示。
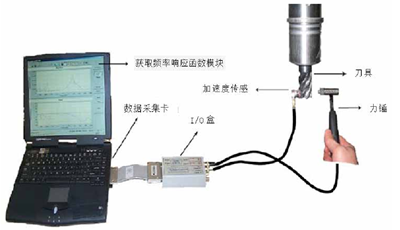
图4-2 实验装置图
实验条件:
1.机床:五轴机床HSC75,其最高主轴转速为18000r/min,最高进给速度为90m/min,机床主轴功率为 35k W 。
2.刀具:硬质合金φ6mm立铣刀和R3mm球头铣刀;
3.工件材料:航空铝7075。航空铝7075是拉伸变形铝合金材料,其组成成分和力学性能如表4-2和表4-3所示。
表4-2 航空铝7075组成成分
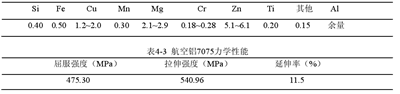
4.实验测试系统:本实验采用的是Cutpro9.0动力学分析软件自身的测试系统,组成测试系统的构件包括:MSC-1冲击力锤,相应500kg力传感器;YD67小型加速度计,灵敏度为0.3 ,频率范围为1-18,000 Hz;USB接口四通道数据采集器AD8304。
锤击试验的实验操作:将I/O盒子通过USB数据线与计算机连接,力锤接I/O盒子0通道加速传感器接1通道、再把加速度传感器黏结刀尖处,力锤在另一侧进行敲击,经处理可得到力-位移FRF曲线。下面分别对刀具和工件进行敲击,如图4-3所示。
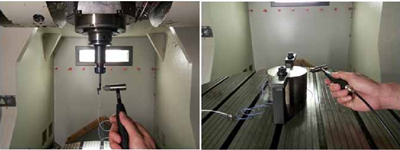
图4-3 锤击刀具和工件
一般而言,锤击受力点位置、力的大小和方向都会影响频响函数的获取,如果敲击不当则会产生较大的误差[59]。在脉冲模式下的传输函数测量采取的多个样本取平均,得到一个传递函数的更好表达。Cutpro9.0软件MALTF模块能够过滤掉不好的敲击信号,比如敲击的时候连击或锤击力太大。图4-4、4-5、4-6分别是平底铣刀D6、球头铣刀R3、工件的力-位移FRF曲线。
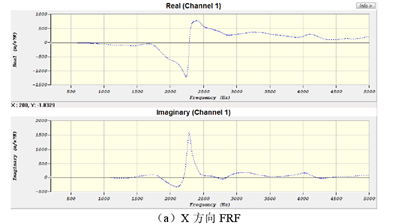
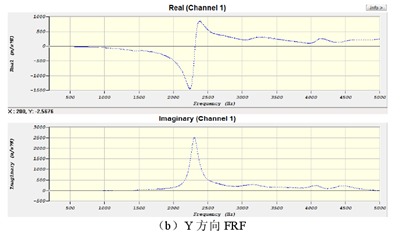
图 4-4 平底铣刀 D6 的力-位移 FRF 曲线
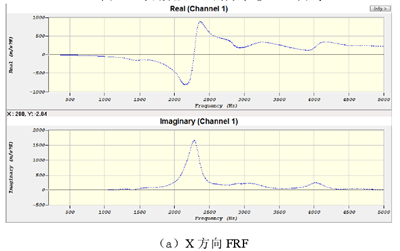
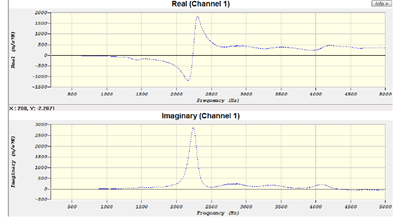
图 4-5 球头铣刀 R3 的力-位移 FRF 曲线
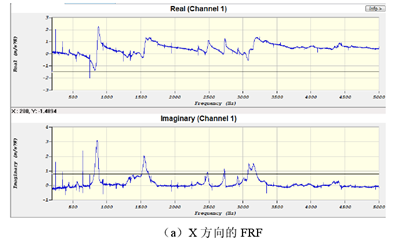
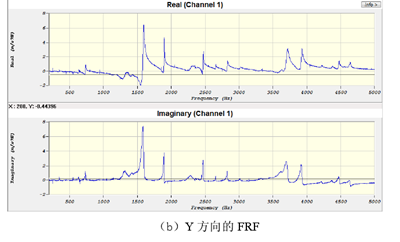
图 4-6 工件的力-位移 FRF 曲线
4.4 颤振稳定域获取
通过以上锤击实验获得的加工系统的频响函数,在特定切削深度条件下进行颤振稳定域仿真,获取无颤振条件下的主轴转速和轴向切深关系图(稳定域叶瓣图)。在 Cutpro9.0软件中下,颤振稳定域分析是通过使用线性稳定性理论来建模。在线性稳定性分析时,非线性因素如刀具跳跃切削,再生过程阻尼,非线性切削系数等被忽略,这使得它能够非常快地进行仿真。
首先对叶轮加工进行颤振稳定域分析。打开 Cutpro9.0 软件选择 Analytical Stability lobes 模块,第一步设置刀具参数为四刃圆柱形立铣刀,直径为 6mm,螺旋升角为 30°,前角和后角为 5°;第二步设置机床-刀具为动态振动,选择由锤击试验得到的 X、Y 传递函数文件;第三步设置工件为刚性,选择顺铣,每齿进给量为 0.1mm/z,径向切宽为 3mm。点击运行仿真,可以得到主轴转速与切削深度的颤振稳定域图如图 4-7 所示。
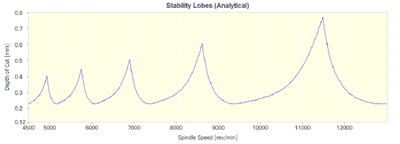
图 4-7 颤振稳定域分析解
4.5 本章小结
本节根据航空整体叶轮的结构特点,选用HSC75五轴机床进行叶轮的加工,选取直径为6mm硬质合金立铣刀进行粗加工,半径为R3mm硬质合金球头铣刀进行叶轮半精加工和精加工。使用Cutpro9.0软件进行颤振稳定域的分析得到无颤振稳定叶瓣图。Cutpro9.0颤振稳定域获取的一般过程:通过锤击实验获取机床-工件系统和机床-刀具系统的传递函数,进行颤振稳定域仿真,获取无颤振条件下的主轴转速和轴向切深关系图(稳定域叶瓣图)。
投稿箱:
如果您有机床行业、企业相关新闻稿件发表,或进行资讯合作,欢迎联系本网编辑部, 邮箱:skjcsc@vip.sina.com
如果您有机床行业、企业相关新闻稿件发表,或进行资讯合作,欢迎联系本网编辑部, 邮箱:skjcsc@vip.sina.com
更多本专题新闻