脉冲当量鼓形齿轮如图1 所示, 常用于高速传动和机动车辆转向的齿轮离合器中, 其主要特点是齿轮的齿向呈圆弧曲线型。并且两端部齿厚需修型减薄, 以利于齿轮在使用中顺利地进入啮合位置。受现行制造能力的制约,此类变位齿无法在普通滚齿机上实施加工。应用经济型数控系统经过对滚齿机进行改造, 可以圆满解决上述零件的数控加工。
1 鼓形齿轮的数控加工原理
加工鼓形齿轮, 应使机床具有下列运动。
1) 滚刀的旋转运动和工件的旋转运动。这2个旋转运动应联动, 且按滚刀1 转、工件1 齿的运动关系来实现展成加工。
2) 沿工件的轴向运动和沿工件径向的进给运动。工件轴向、径向2 个进给运动应联动, 方可实现鼓形齿轮圆弧状齿向的加工要求。
选用Y3150E 滚齿机进行上述数控改造。JBK- 30M 经济型数控系统具有任意两坐标联动和三坐标联动的加工功能。使用一台步进电动机联接控制沿工件轴向位移的垂直丝杠; 使用另一台步进电动机联接控制工件径向进给的水平丝杠。当运行圆弧指令时, 就可通过步进电动机, 控制刀具和工件同时作沿工件轴向和径向进给运动的联动运行, 从而实现加工所需的圆弧齿向轨迹。
而Y3150E 滚齿机已具备工件与刀具旋转联动的展成运动, 因此满足了该特殊齿向齿轮加工的运动所需。
当进行数控加工时, 用原机床传动系统控制刀具和工件做各自旋转并且联动的展成运动, 来实现工件渐开线齿形的加工以及分齿运动; 与此同时, 数控系统控制刀具的垂直位移和工件的水平位移, 刀具圆心以半径R = R 1 ( 工件) + R2 ( 刀具) 为运行圆弧指令, 进行该特殊齿向齿轮的数控加工的运行。
2 齿端齿厚修型的数控加工
由数控加工原理可知, 在数控加工中圆弧指令控制( 旋转的) 刀具和( 转动的) 工件进行联动进给运行, 从而复合出圆弧轨迹, 达到实现控制鼓形齿轮圆弧齿向的加工。但由图1 所示可知; , 为有利于鼓形齿轮在工作过程中与齿轮的顺利啮合, 圆弧齿向的两端部齿厚应均匀减薄, 其齿厚最大减薄量为△S ( 图例中△S= 0. 2 mm) 。从实际应用的角度出发, 齿厚减薄段的轨迹曲线也应呈圆弧型。
齿厚减薄, 说明该截面处的分度圆减小。当加工中使齿轮滚刀切入齿轮工件的深度加大时, 可满足上述要求。而齿厚部分在定齿宽上均匀减薄, 则要求滚刀切入工件的深度也呈均匀变化, 即此段呈现为圆弧曲线形的变位齿轮变化; 当改变此段曲线的圆弧半径r 和圆心坐标时, 如图2 所示,就可实现圆弧型齿向部份齿厚呈圆弧状的均匀减薄。且该圆弧半径r 在B 点处与工件齿向圆弧R 162 相切( 见图1 与图2) 。
2. 1 圆弧半径r 的计算
点起刀具开始空运行圆弧轨迹, 当运行到A点时,滚刀开始切入工件, 当运行AB 段圆弧轨迹时, 使得圆弧状齿向的齿厚均匀地由薄变厚, 达到B 点时, 齿轮齿厚达到标准齿厚; 而从B 点起, 则运行以O 点为圆心, 以圆弧R 为半径运行工作段圆弧轨迹B C+ CB ( 图2 所示为一半, 见图1) , 最后以圆弧r为半径, 圆心为O2 进行齿轮另一端齿厚均匀减薄的加工运行。
由于O1 点在OB 线上, 所以, 两运行圆弧在B点相切, 说明当齿厚均匀地增厚到标准齿厚后不再变化, 齿厚轨迹为相切圆滑过渡而无拐点, 即为齿面上无过渡棱线, 由此实现了鼓形齿轮圆弧齿向的特殊加工要求。
此加工方式的优点还在于: 由于滚刀两侧刃同时切削工件, 所以齿厚两侧减薄的对称性较高, 而且在齿厚均匀变化的过程中始终保持这种良好的对称性。因此, 零件的加工制造精度高于图纸中技术要求, 同时又减少了常规加工时齿厚减薄修型的工序,能收到事半功倍的效果。
需要特别指出: 此加工方式的另一显著特点是,如果在鼓形齿轮的两端处再增加R 3~ R5 的圆弧运行, 可以实现齿轮加工的倒角工序; 并且在进行齿轮加工的倒角时, 将齿轮加工的毛刺全部排除在齿轮下端面处, 极大地有利于齿轮毛刺的清除; 在提高加工质量的同时, 达到了减少工序、提高加工效率的效果。
3 加工参数的转换计算
滚齿加工中, 沿工件轴向即垂直丝杠的运行速度是与滚刀与工件的转速密切相关的。Y3150E 滚齿机中, 此方向工件轴向进给速度vx 的范围在0. 4~ 4 mm/ r 内。而在数控加工中, 加工指令的轴向进给速度FX 的单位是mm/ min。所以数控滚齿加工轴向进给速度FX 的换算为:
FX = ( n/ z ) vx ( mm/ min) ( 4)式中: n 为滚刀转数( r/ min) ; z 为工件齿数;在数控加工中. 其运行轨迹是按插补原理进行的。由圆弧插补原理可知: 计算机控制2 台步进电动机按其插补方式来进行位移轨迹的运行, 且任意瞬间仅有一台步进电动机被控运行, 另一台无运行。因此可知: 圆弧指令中运行长度是其两分解运动的位移长度之和; 其运行速度在任意瞬间是单台步进电动机的速度, 或者为两运行方向的平均速度( Fx , Fz ) 之和。因为两方向运行长度是在同一时间t 内开始和完成的, 所以有:
L x= Fx t= ( nvx / z ) t, L z = Fz t , Fx= ( L x+ L z ) / t
因为: t= L x / Fx = L x z / nvx
式中:
Lx , L z—-圆弧轨迹X 向、Z 向分解的位移长度;
Fx , Fz —-圆弧轨迹X 向、Z 向分解的运行速度。
在数控加工中,由于滚刀半径也在运行轨迹的参数中,所以圆弧轨迹以R= R2 ( 刀具) + R1( 工件) 为半径运行, LX , L Z 值的长度如图3 所示。
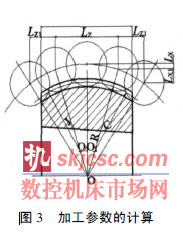
公 式( 5) 中选择
数控滚齿加工的圆弧轨迹运行速度, 其轴向进给速度FX 与原机床轴向进给速度VX 等值, 是采用类比法转换得到的。那么如果在VX 或 V X 值的一段范围内来变动运行速度, 则可弥补原滚齿机两轴向进给速度间的空档速度, 而使得数控加工中实际的轴向进给速度可以任意变换, 从而使得齿面上的表面粗糙度较常规加工更为理想, 并可根据具体情况选择其加工的经济精度, 来提高生产率和降低成本。
同理, 在鼓形齿轮的数控精滚加工中, 不改变滚刀的转速, 只变换程序加工中轴向进给的运行速度,就可以提高齿轮加工的表面粗糙度, 满足和达到齿轮的精度要求。
4 脉冲当量的选择
在滚齿加工中, 受展成运动的限制, 工件的旋转速度较低, 而沿工件轴向的进给速度则更低, 如若在数控加工中加大轴向的进给速度, 势必使得齿面的表面粗糙度和齿面的精度降低。经济型数控系统常规的脉冲当量不能满足此加工要求。脉冲当量是数控加工中控制位移的最小单位。
一般经济型数控系统取值, X 向: 0. 005 mm; Z 向: 0. 01 mm。在等速等长轨迹的运行时, 脉冲当量越大, 脉冲频率越低, 即单位时间内脉冲数越少, 运行速度越低; 反之相反。为实现滚齿加工中轴向进给速度低的需要, 因此在数控改造中选择确定的脉冲当量就应该减小。由此可知: 实现数控高精度加工和低速运行的措施是必须减小数控系统的脉冲当量。径向进给也同此。
此数控改造中选用的脉冲当量为, X 向( 工件轴向即垂直丝杠) : 0. 000 1 mm, Z 向( 工件径向即水平丝杠) : 0. 000 2 mm。两方向脉冲当量的比值i= 0. 001/ 0. 002, 与选用经济型数控系统原脉冲当量的比值i= 0. 005/ 0. 01 等值, 即将脉冲当量减小了i= 0. 01/ 0. 0002= 50 倍。如此在符合经济型数控系统内控软件约定的前提下, 实现了编程的简化。与原数控系统的不同之处在于, 在编程时必须使位移长度和运行速度增大i= 0. 01/ 0. 0002= 50 倍, 方可实现原位移长度。
在实际加工中, 虽然常规滚齿机的丝杠无法实现如此精确的运动位移, 但由于减慢了进给速度, 使得加工运行的连续性显著提高。再则, 脉冲当量的减小, 使得步进电动机的输出力矩增大了相同的倍数, 更有利于加工控制的稳定性。上述变化均使加工中各向运动的运行更为平稳, 加工效果更为提高。
按上述方法选择确定脉冲当量的不足之处在于, 第1 是数控系统单条指令中允许的最大运行长度需要相应减小相同的倍数, 指令中的运行速度也应该比原运行速度增大相同倍数, 编程计算略显麻烦; 第2 是数控系统圆弧指令中允许的最大圆弧半径为l0 m, 脉冲当量的改变使其半径许用值减小相同的倍数, 圆弧半径许用值R 仅为200 mm。由于Y3150E 滚齿机允许加工的工件最大直径是500mm, 所以改造后不能满足零件弧面半径超出此范围的加工要求。对于弧面半径超出此范围的零件加工, 则需要减小传动比, 增大圆弧半径许用值, 重新进行滚齿机的改造。
如果您有机床行业、企业相关新闻稿件发表,或进行资讯合作,欢迎联系本网编辑部, 邮箱:skjcsc@vip.sina.com