一副压铸模的开发成功,是一系列细致的分析与计算设计的结果。在设计中需要考虑零件的技术要求、设备条件、结构工艺性、模具结构等,有时还需要模拟分析。现在以一个电子壳体零件的压铸解决方案为例进行分析。
1 零件的技术要求和设备条件
图1是一个电子零件的壳体结构件,材料为A380铝合金[1],外形尺寸为240mm×166mm×130mm,要求组织致密,表面完整,并满足气密性要求。压铸设备为WOTAN700,其额定锁模力为7000kN;其最大料缸直径为80mm,拉杠间距为750mm,最大模厚为900mm;设备有一个液压抽芯装置。
2 结构工艺分析
该零件形状复杂,台阶多,5个面有腔体结构,一个面有散热筋,壁厚不均匀,最大壁厚为12mm,最小壁厚为2.5mm,平均壁厚为3.2mm。零件的压铸填充过程遵循主干型腔填充原则,即应遵循主干型腔的填充———优质填充区满足70%的要求;非主干型腔的填充———金属液互相冲击区约为30%[2]。
图1a为原壳体零件,从任何一个方向选择浇注系统,优质填充区域不超过50%,其中有一个面将全部是金属液冲击区。这种结构不具备压铸工艺性,需要进行结构更改。经过结构分析,将图1壳体箭头1所指位置的盖揭开,变成图1b箭头4所指的无盖位置,基本达到了主干型填充原则要求。
3 锁模力的计算
在压铸过程中,铝合金液在分型面投影面积上的反压力P反要小于压铸机的额定锁模力,即:P反≤P锁·k (1)P反=ΣF·p×0.1 (2)式中,ΣF 为铸件在分型面上的总投影面积,cm2;p 为压射比压,MPa;P锁为压铸机额定锁模力,kN;k 为许用安全系数,对于铝合金,k=0.8。计算得到零件的总投影面积为690cm2,气密件一般选用比压为70MPa,代入式(2)得P反=4 830kN;而WOTAN700压铸机的额定锁模力P锁=7 000kN,代入式(1)得P反≤P锁·k≤5 600kN,满足模具要求。
4 浇注位置的选择
浇注位置的选择应符合金属液填充流线原则,即内浇道与压铸件主干型腔所属范围内的任意部位可通达的金属流线的应是最短的;内浇道压出的金属液的流动方向应基本一致,并沿着主干型腔型面的方向扩展填充[3]。按照金属液填充流线原则,浇注系统设计见图2,以保证金属流线最短,同时为了保证金属液沿主干型腔型面的方向顺利填充,在图2中箭头所指位置增加了3处导流筋。
5 浇注系统计算
5.1 内浇口截面积的计算
根据W.Davok经验公式:Ag =0.485 V (3)在壁厚为2.4~3.2mm时有一定的适应性。根据G.Lieby经验公式:Ag =5 000 V/(V +10 000) (4)在壁厚为3~5mm时有一定的适应性。式中,Ag为内浇口截面积,mm2;V 为零件体积,cm3。使用Pro/E三维分析可得到零件体积V =790cm3,用式(3)计算得Ag=383mm2,用式(4)计算得Ag=366mm2,设计时,取两者中间值Ag=370mm2。根据零件的平均壁厚为3.2mm,取内浇口的厚度为b=2mm,内浇口长度L=Ag/b=185mm。
5.2 料缸的选择
5.2.1 料缸截面验证
按连续性原理,流体流过某一限定部位,在一段时间内流体连续地充满这个部位,因此在这个时间内流入、流出的流量Q 是相等的。
Q =Vg·Ag =Vp·Ap
Vg =Vp·Ap/Ag (5)
式中,Vg为充填速度;Vp为射料杆压射速度;Ap为料缸截面积。
射料杆压射速度Vp一般以1.5~2.5m/s比较合适,设计时选择Vp=2.4m/s,料缸直径为80mm 时,Ap=5 024mm2,代入式(5)得Vg=32.5m/s,符合一般经验填充速度为30~50m/s的要求。
5.2.2 充满度验证
料缸直径为80mm时,料缸能容纳金属液的最大总质量为5.8kg,而带浇注系统的零件总质量为3.5kg,充满度为3.5/5.8=51.7%,符合充满度30%~75%的要求。所以选择型号为WOTAN700压铸机、直径为80mm的料缸符合设计需求。
6 模具总装简图的设计
由于该零件复杂,外形偏大,需要4 个滑块抽芯———两个液压油缸抽芯和两个斜拉杆抽芯。图3是模具总装简图。
图4为充填型腔不同步的情况,其中模具外形尺寸为830mm×750mm×700mm,偏心距为200mm。而7000kN压铸机拉杠间距为750mm,最大模厚为900mm,模具不能直接装入压铸机。通过计算,将模架切去下面两个角,并将模具动模和定模分开来安装,可以将模具装入压铸机。
压铸机只有一个液压抽芯装置,通过三通结构,可用一个液压抽芯装置带动两个液压缸,直径分别是150mm 和125mm。合模时推杆与滑块会有干涉,设计先回程机构可以有效解决这个问题。
7 模拟试验
考虑到该壳体零件结构工艺的复杂性,为慎重起见,进行了压铸仿真模拟试验,将压射杆射速设定为2.4m/s,浇注温度设定为650℃,快压射的切入点选择为4支横浇道全部充满时,零件收缩率为0.6%,划分网格数为3 500万,模拟时间为5.5h。试验结果:①4支浇道不能同步填充,中间两支先进入型腔,见图4;②部分区域填充不完整,见图5。
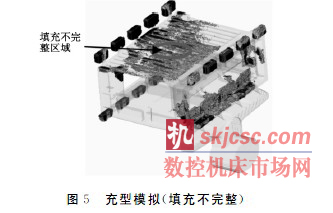
8 工艺修
根据仿真模拟分析的结果,对壳体零件进行了工艺修改:①将4支浇道改为两支,以保证浇道同步填充,见图6;②更改零件局部位置壁厚,减少填充阻力,保证金属液填充流线原则。图1a、图1b分别是修改前和修改后的壳体,将箭头2、3所指的壁厚2.5mm分别改为箭头5、6所指的3.5mm及4.5mm。其中箭头所指的修改壁厚不影响使用结构,箭头所指的修改壁厚则可以通过铣削加工去除。
9 结 语
壳体零件通过以上工艺分析、计算、模拟和修改,试模获得成功,零件表面完整,内部组织致密,满足气密性要求。
如果您有机床行业、企业相关新闻稿件发表,或进行资讯合作,欢迎联系本网编辑部, 邮箱:skjcsc@vip.sina.com