基于自适应神经模糊推理系统的刀具磨损监测
2017-5-9 来源:华中科技大学 船舶与海洋工程学院 作者:朱永猛,吴 军,吴超勇,苏永衡
摘要: 为精确地监测高速铣床刀具在加工过程中的刀具磨损量,通过采集高速铣床加工过程中的振动信号、电流信号和噪声信号,经数据预处理与数据融合,建立基于自适应神经模糊推理系统的刀具磨损过程变化模型,实现在高速铣床不停机的前提下对铣床刀具进行状态监控。实验结果显示: 针对铣床刀具磨损量的监测平均准确率为95. 21% ,最大监测准确率为 99. 74% 。这表明文中所采用的方法具有较高的可行性。
关键词: 铣床; 刀具磨损监测; ANFIS
高速铣床作为一种较为先进的智能制造装备,在加工过程中,刀具加工工件,产生磨损,影响最后的成品品质。刀具的磨损受到科研人员的极大关注,曾尝试用各种不同的方法监测刀具的磨损。
1.国内外研究现状
早期的科研人员利用单一传感器采集到的信号数据,如噪声信号[1]、振动信号[2]和切削力信号[3],进行刀具的状态监控( tool condition monitoring,TCM) 。伴随着科学技术的不断发展一些通过建立刀具磨损动力学模型进行刀具磨损量监测的方法,显示了广阔的适用性。对于模型的建立,一般有 2 种: ① 假设可以完全通过数学模型描述刀具磨损过程中所有的物理规律,基于这种假设提出“白盒子”方法[4]; ② 假设刀具磨损过程为不可知,也没有任何的先验知识,但可以通过采集数据获得未知模型的输入、输出关系,实现对未知过程的认知,这样的方法称为“黑盒子”方法。“黑盒子”方法最大的优点,是可以在不需要对磨损过程中的物理意义有任何了解的前提下,通过采集准确的实验过程数据,进行磨损过程模型的搭建[5],最大的缺点是对磨损过程中物理意义的认知缺乏。实际应用过程中,最好是将 2 种方法进行融合,得到“灰盒子”方法[6]。但是,在复杂的工况下,难以采集准确的过程数据,以及缺乏经验知识,都对刀具磨损过程的动力学模型正确搭建造成不良影响。
Jang 于 1991 年提出了基于模糊神经网络的自适应模糊推理,1993 年又撰文将之前提出的算法称为自适应神经模糊推理系统( adaptive network - based fuzzy inference system,AN-FIS) 。模糊推理系统使得显性知识更加详尽和精确,神经网络通过学习算法建立数学模型解释隐性知识,这使得模糊神经网络的优势更加凸显,这也是模糊神经网络被广泛应用到刀具磨损量监测领域的原因。Chen S L 等人则利用多个传感器数据,如振动信号和切削力信号,提出新的数据融合算法,结合 ANFIS 进行刀具磨损状态的监测[7]; Uros Z 等人利用切削力信号,对比了三角形隶属度函数和梯形隶属度函数应用到 ANFIS 中的刀具磨损量监测结果[8]; Gill S S 等人利用经过低温处理的 M2 高速钢车刀在加工过程中的切削速度、工作时间和低温浸泡均热温度等参数,结合 ANFIS 进行刀具磨损量的监测[9]; Rizal M 等人利用刀具切削速度、切削深度、进给速率和融合系数等参数,结合 ANFIS 进行刀具磨损量的监测[10]。
本文利用高速铣床加工过程中的主轴和工作台振动信号、主轴直流电流和交流电流信号、主轴与工作台噪声信号,结合自适应神经模糊推理系统 ANFIS,实现对刀具磨损量的监测。实现过程中,首先对传感器信号进行预处理和特征融合,再经过 Takagi-Sugeno 模糊推理进行模糊规则划分和隶属度函数的计算,最后利用神经网络训练模型,实现刀具磨损量监测。
2.基于 ANFIS 的刀具磨损监测模型
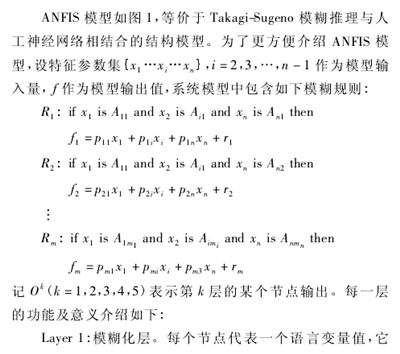
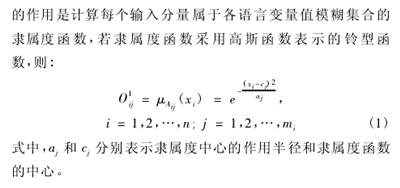
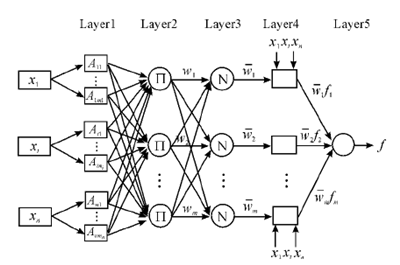
图 1 基于 Takagi-Sugeno 模糊推理的 ANFIS 网络
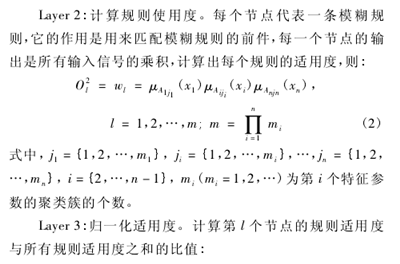
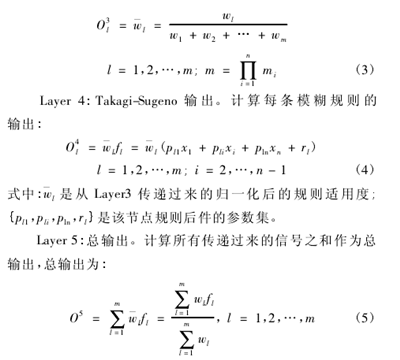
由以上分析和定义可得一个与基于 Takagi-Sugeno 模糊模型的神经网络相等价的 ANFIS 模型。在实际应用中,可以合并不同的分层构建不同的 ANFIS 模型。
3.实例分析
本研究采用一个实际的铣床监测数据集[11],数据集包含 16 组刀具全寿命周期,共 167 个运行次数的铣床刀具磨损实验数据。文中选择第 13 组刀具全寿命周期数据实现刀具磨损量监测算法。在刀具正常运行过程中,传感器每次采集数据可得到 9 000 个数据点,去空值和去奇异点后,绘制主轴直流电流信号如图 2。
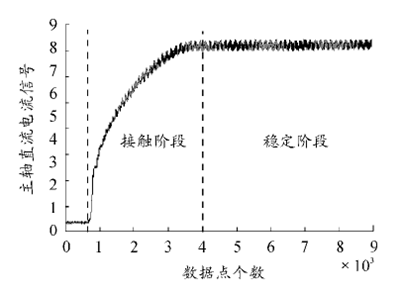
图 2 主轴直流电流信号
从图 2 中曲线可以发现,信号数据有很明显的阶段性特征,包括空转阶段、接触阶段和稳定阶段。为了使实验过程更具代表性、监测结果更具准确性,本文选取第 4 500 个点后的稳定阶段的信号作为原始数据。提取均值、均方差、方根幅值、均方根、最大值、偏斜度、峭度、峰值因子和裕度因子 9种时域特征参数,并归一化。针对不同传感器计算得到的时域特征,利用式( 6) 进行相关性分析,式中,X 表示时域特征参数,Y 表示刀具磨损量,Cov( X,Y) 为 X 和 Y 的协方差,D( X) 为 X 的方差,D( Y为 Y的方差。

利用式( 7) 进行残差分析,式中,S1( x) 和 S2( x) 是根据特征值点拟合的曲线,N 为数据点个数。结果如表 1、表 2。表 1 中 Na N 表示非数字,即 Not a Number,当分母为 0 时,计算结果为 Na N。首先,保留皮尔逊相关系数大于 0. 8 的强相关特征参数。其次,在保留下来的特征参数中,选取残差值最小[12]的特征参数组成最终的特征参数集,获得的特征参数集为: 主轴噪声信号的方根幅值、工作台噪声信号的均方差、主轴交流电流信号的最大值和主轴直流电流信号的均方根。
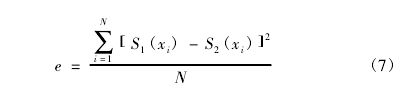
在实验获得的第 13 组的 13 个数据点中,选择 8 个数据点作为训练数据,5 个数据点作为校验数据,同种工况下采集的 4 个数据点作为验证数据。将融合得到的特征参数集输入到 ANFIS 网络进行刀具磨损量监测,结果如表 3 所示。
表 1 各时域特征与磨损量的皮尔逊相关系数
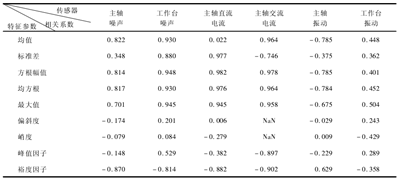
表 2 各时域特征自身间的残差值
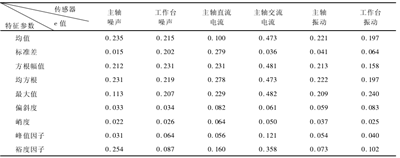
表 3 实际值与模型监测值的结果对比
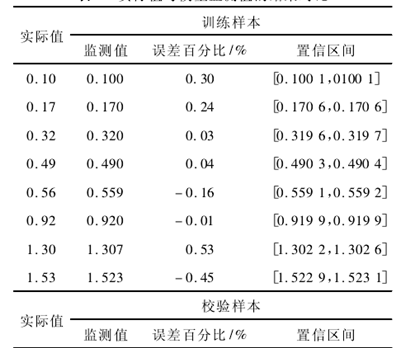

4.结束语
铣床刀具作为工业生产中与被加工件直接接触的部分:刀具的磨损会直接影响被加工件的成品品质,降低企业的经济收益。本研究提出的刀具磨损监测方法,可以在铣床正常运行过程中进行刀具磨损监测,为企业提供刀具更换与维修的依据。
投稿箱:
如果您有机床行业、企业相关新闻稿件发表,或进行资讯合作,欢迎联系本网编辑部, 邮箱:skjcsc@vip.sina.com
如果您有机床行业、企业相关新闻稿件发表,或进行资讯合作,欢迎联系本网编辑部, 邮箱:skjcsc@vip.sina.com