数控车床上下料调控系统的研究
2024-4-26 来源: 江苏省海安中等专业学校 作者:徐晓燕
摘要:针对机床采用人工上下料所存在的劳动强度大、生产效率低的问题,提出了一种以机械手为核心的机床自动上下料系统。对该系统的结构、工作原理及控制流程进行了详细的分析。根据实际应用表明,该数控车床自动上下料系统能够实现数控机床的自动上下料,减少 2 名操作员工,为落后机床的自动化改造提供了指导,具有极大的应用推广价值。
关键词:数控车床 上下料 自动控制
引言
随着国内“工业 4.0”进程的不断发展,对制造业的智能化和自动化要求不断提升,目前国内多数的车床在上下料方面均采用的是人工上下料,不仅劳动强度大、效率低,而且人工在取放料的过程中存在着较大的危险性,严重限制了数控机床生产效率的进一步提升。
为了提高数控机床生产的效率和安全性,同时控制改造成本,本文提出了在数控机床旁增加一个机械手装置,利用 PLC 控制系统控制机床和机械手联动的改造方案。该方案只需增加一个机械手,同时对数控机床的控制系统进行升级,实现了机床和机械手的联动运行控制。根据实际应用表明,该机床上下料控制系统能够实现物料的自动取放,将机床生产效率提升了 2.6 倍,消除了人工取放定位精度差、安全性不足的隐患,具有极大的推广应用价值。
1、自动上下料系统构成
为了满足自动上下料系统的控制精确性和可靠性需求,该系统包括了硬件和软件两个部分,其自动上下料部分的硬件布局结构如图 1 所示。
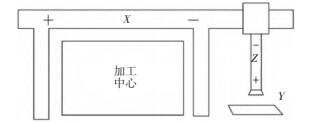
图 1 自动上下料系统结构示意图
该控制系统中的硬件结构包括控制器、伺服系统、交流电机、各类传感器等,而其软件系统则主要是用于控制数控机床和机械手的联动运行,其控制程序设置在示教器和远程控制中心内,同时满足就地控制和远程控制的需求。
1.1 自动上下料控制系统
对于数控机床的自动上下料控制来说,首先要保证上下料定位的精确性,其次要能保证自动上下料的效率满足数控机床的生产节拍需求。因此该自动上下料控制系统必须能够保证控制精确性、快速性的需求。在对多种运动机器人控制器的应用情况进行分析后,最终选用了一款滑轨机器人控制器,其具有体积小、容量大的特点,其数据通信系统采用了工业以太网总线,能够满足瞬时大容量的数据通信需求,而且采用了双屏蔽电缆,能够有效抵抗外界干扰,确保信息传输的精确性。在设定控制逻辑时,首先需要根据数控机床、滑轨机器人的布局情况合理选择上下料的路线,并根据上下料路线设置上下料控制程序,使滑轨机器人的运行保持在一定的范围内,保证数控机床在自动上下料过程中的安全性。
为了满足自动上下料控制系统的拓展需求,在控制器选择时,选择了具有 21 路输入接口和 24 路输出接口的多接口控制器,各个接口均采用了标准化端口,能够快速的进行模块的添加,从而能够满足不同情况下的拓展需求。
该数控机床控制系统构成如图 2 所示。
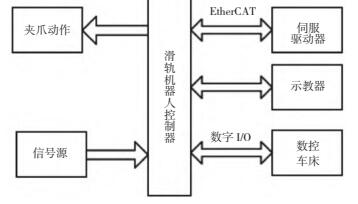
图 2 数控机床控制系统框架
1.2 伺服系统
滑轨机器人的机械手在进行零件取放的过程中,需要运行平稳、取放精度高,因此要求取件的伺服控制系统具有极高的控制精度和控制平稳性,不能存在丢步现象。传统脉冲式伺服驱动系统虽然结构简单、造价较低,但其控制稳定性较差,因此在经过对比后选择了总线式伺服驱动系统,该伺服系统可以通过标准接口和控制模块相连接,保证了数据传输的精确性和高速传输需求。总线式伺服驱动系统的整体结构如图 3 所示。
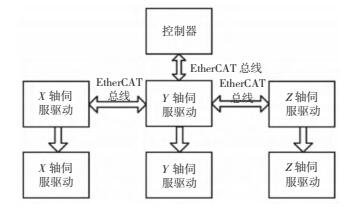
图 3 伺服驱动系统结构示意图
1.3 电机选择
目前各驱动控制系统在选型时一般优先选择步进电机,但步进电机在工作中容易出现丢步现象,将导致取料系统的定位偏差,影响数控机床的运行安全性。因此在综合对比后选择了交流伺服电机作为该上下料控制系统的驱动装置,提高上下料系统在工作中的精确性和运行平稳性。
2、上下料控制原理
该驱动系统在工作中直接对滑轨机器人进行控制,通过在 X 轴上的运动带动机械手运行,然后利用Z 轴的移动来实现机械手对物料的抓取或者释放。
为了满足滑轨机器人和数控机床联动运行的控制需求,需将两者的控制和通信系统进行改造,设置标准化的 I/O 接口,并联所需的信号与控制系统实现 I/O 数据通信。在进行上下料运行控制时,控制中心首先获取数控机床的运行状态信息,对其下一阶段的运行情况进行判断,然后提前发出控制信息给滑轨机器人,使滑轨机器人提前准备好上料或者下料,从而实现上下料动作和机床加工情况的无缝衔接,提高机床在工作时的运行效率。该自动上下料控制逻辑如图 4 所示。
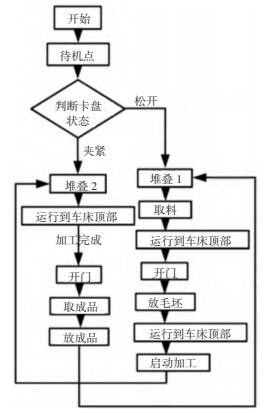
图 4 数控机床自动上下料控制逻辑示意图
3、应用现状分析
以 CKD6180D 数控机床为例[9],对其进行自动化上下料系统改造,然后对其应用前后的状态进行对比结果如表 1 所示。
表 1 不同上下料方式对比
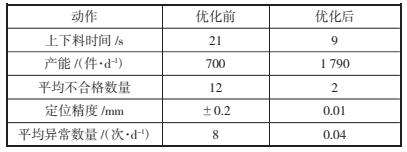
由实际验证结果可知,采用新的自动上下料系统后,每个工件的平均上下料时间降低了 57.1%,由于实现了自动化生产,因此能够显著延长数控机床的生产时间,其每天的产能比采用人工生产提升了 2.6倍,因定位不精确而导致的不合格品的数量则降低了83.3%。由于采用了精准定位模式,因此每个零件的平均定位精度比优化前提升了 95%,而由于定位不精确而导致的工件异常数量则比优化前降低了 99.5%。因此,通过实际应用分析,新的数控机床自动上下料系统,不仅能够显著提升数控机床的工作效率,而且能够有效降低其在工作过程中的异常率,极大地提升了工厂的生产经济性,因此具有极大的应用推广价值。
4、结论
1)机床上下料控制系统的硬件结构包括了控制器、伺服系统、交流电机、各类传感器等,能够显著提升其控制可靠性。
2)总线式伺服驱动系统可以通过标准接口和控制模块相连接,从而保证了数据传输的精确性和高速传输的可靠性。
3)该机床上下料控制系统能够实现物料的自动取放,将机床生产效率提升了 2.6 倍,将因定位不精确而导致的工件异常数量降低 99.5%。
投稿箱:
如果您有机床行业、企业相关新闻稿件发表,或进行资讯合作,欢迎联系本网编辑部, 邮箱:skjcsc@vip.sina.com
如果您有机床行业、企业相关新闻稿件发表,或进行资讯合作,欢迎联系本网编辑部, 邮箱:skjcsc@vip.sina.com