基于 3D 打印的泵壳快速铸造方法
2023-5-9 来源: 北京浩鹏科技有限公司技术中心 作者: 武志良
摘要 : 传统的砂型铸造工艺在铸件生产时,首先需要制作模具,存在周期长、费用高等问题,不能完全满足新产品研发的周期要求。采用 3D打印砂型或者砂芯,一方面减少对技术工人的依赖,增强了产品品质。另一方面速度快,缩短了交货期。最后,为产品设计的灵活性提供了保障,3D 打印能够及时应对设计变更,提升产品研发的验证效率。
1.引言
本文主要介绍了三维铸造工艺设计、砂型3D 打印技术、光学三维扫描技术在小批量铸件开发中的应用,结合泵壳的制造过程,比较了3D 打印砂型和传统铸造工艺的特点,结果表明,采用砂型 3D 打印的数字化铸造技术,能够明显缩短交货期、降低产品研发成本,而且精度高,工艺性能稳定。
3DP 砂型 3D 打印的原理 : 将树脂砂铺在 3D打印平台上,用刮板机刮平,层厚大约在 0.28-0.5mm。打印头根据三维模型的二维切片生成的路径喷射呋喃树脂胶,将树脂砂粘接在一起,然后如此往复,完成整个三维模型的打印。3DP 打印砂型的优点就是成本低,效率高,力学性能好。
通过比较 3DP 砂型打印快速铸造和传统铸造工艺流程不难看出,3D打印砂型快速铸造实现了无模制造,节省了模具设计、制造、造型、制芯等工序,同时 3D 打印砂型精度高,质量稳定,节约生产制造周期。
2. 铸造工艺设计
在砂型和砂芯 3D 打印之前,需要在产品三维数模上进行工艺设计,包括预留加工余量、浇铸系统设计,必要时进行铸造仿真模拟,及时发现铸造缺陷。
(1)添加加工余量
某水泵壳体,材质为 HT200,考虑到铸件在凝固过程中有收缩,所以需要对产品数模进行一定比例的放大,灰铁的收缩率为 1%。在 UGNX11 软件中,比例因子选择 1.01。见图 1。
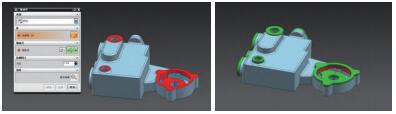
图 1 图 2
然后需要根据二维图纸,对安装面增加加工余量,目的是保证成品的尺寸公差。加工余量的大小对产品质量和生产效率有很大影响,加工余量过大,不仅增加机械加工的工作量,增加能源消耗,也降低了生产效率。而加工余量过小,机械加工无法加工掉铸造缺陷,也无法补偿加工过程中产生的装夹误差,从而产生废品。所以我们参考砂型铸造的精度,加工余量增加 5mm。见图 2。
(2)浇铸系统设计
浇铸系统是铸型中液态金属流入型腔通道的总称,浇铸系统的设计主要考虑金属液流动的速度和方向平稳、连续、均匀,不冲击砂芯和型壁,不产生飞溅和涡流,不卷入气体。浇铸系统要结构简单,不影响铸件的外观。对于案例中的壳体设计浇铸系统采用收缩式,也就是直浇道的横截面大于横浇道的横截面,也大于内浇道的横截面。见图 3。
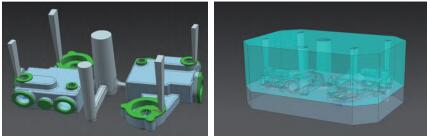
图 3 图 4
3. 砂型(芯)设计与 3D 打印
我们采用 UG NX 11 软件,对三维数模进行砂型和砂芯分模设计,需要考虑产品结构、3D打印设备的打印范围等因素。对于本次壳体的砂芯和砂型设计,考虑到尺寸最大是 200mm。一次成型两件也在 3D 打印设备范围内,所以砂型和砂芯采用整体打印。分上下两部分合模,方便清理浇道内多余的砂子。
打印砂型的精度是 ±0.5mm,3D 打印砂型的材料是呋喃树脂自硬砂,砂子粒度为 70 目。3D 打印设备成型尺寸为 2000mm×1000mm×800mm,砂型的抗拉强度在 1.4-1.9MPA,发气量 12-15ML/g。要打印的砂型和砂芯。见图 4。
4.合型、浇铸
砂型打印完成之后,清理表面的浮砂,然后合型,围箱浇铸。浇铸重量 10kg,浇铸温度为 :1370-1380℃。浇铸完成后,冷却 12 小时,然后敲掉砂型和砂芯,做抛丸处理,并打磨掉浇铸口,检查铸件有无气孔、砂眼、夹渣、缩孔、缩松、裂纹等铸造缺陷。最后对配合面进行数控加工,确保尺寸公差在要求范围内。见图 5。
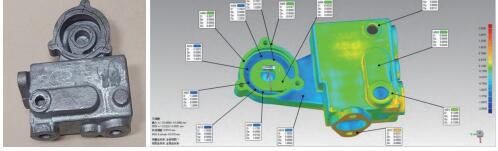
图 5 图 6
5. 尺寸检测
尺寸检测的方式很多,可以采用三坐标、二次元、光学三维扫描仪等。其中光学三维扫描仪具有精度高、操作方便等优点,而且是全尺寸检测,所以广受欢迎。光学三维扫描属于非接触式扫描,可以对柔软、易碎的物体进行测量,其缺点是很难扫描高反光、高透光的表面,而且扫描后的点云质量一般,需要喷显像剂才能提高扫描的点云质量。光学扫描仪根据光源的不同,分为白光、蓝光、激光等不同的类型。
白光和蓝光都属于结构光,适合扫描小件,精度高,但是使用不如激光扫描仪方便。激光三维扫描仪在中大型产品的扫描上比较出色。对于本次泵壳的尺寸检测,采用蓝光三维扫描。因为产品小,精度要求高。蓝光三维扫描仪的设备参数见下表。
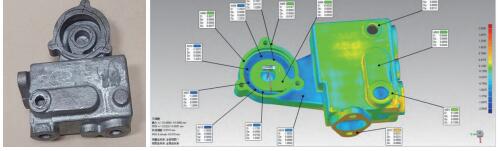
将数控加工后的泵壳进行 3D 扫描,获取点云数据,在 Geomagic Qualify 软件中,将产品的 3D 数模和点云数据导入,根据基准进行对齐,做 3D 尺寸比较。最后得到全尺寸的检测报告。见图 6。
6. 结论
本文介绍通过砂型 3D 打印技术在快速铸造方面的应用,将泵壳的开发周期从 2 个月降到 20天内,缩短了接近 70%。同时因为减少了模具设计、开发、制造等工序,降低了成本。最后,砂型 3D 打印快速铸造的工艺减少了砂芯的数量,也就减少了组芯的误差,能有效保证铸件的精度,适合在新品开发中推广应用。
投稿箱:
如果您有机床行业、企业相关新闻稿件发表,或进行资讯合作,欢迎联系本网编辑部, 邮箱:skjcsc@vip.sina.com
如果您有机床行业、企业相关新闻稿件发表,或进行资讯合作,欢迎联系本网编辑部, 邮箱:skjcsc@vip.sina.com
更多相关信息