PCD 车刀断屑器的结构设计
2020-2-14 来源: 宁波大学 机械工程与力学学院 作者:吴剑钊,陈家琦,兰 浩,徐 磊,于爱兵
摘 要: PCD 车刀被广泛应用于航空航天、汽车零部件等精密制造业,但在切削加工中产生的切屑缠绕在工件与车刀上,降低工件表面质量和生产效率,缩短车刀使用寿命。根据切屑折断条件,提出了“两夹一调”的设计准则,设计并制作了一种应用于 PCD 车刀的断屑器。该断屑器具有不改变车刀原有结构并且断屑范围可调节的特点,可以作为 PCD 车刀的附件。以铝合金材料为例进行了切削试验,并观察切屑形状,试验结果表明该断屑器能够解决断屑问题且效果稳定,可以提高机械加工过程中的加工质量和效率,也为研制其他类型刀具的断屑器提供了借鉴思路。
关键词: 断屑; PCD; 断屑器; 刀具
PCD 车刀在航空航天、汽车零部件等精密制造业加工中得到广泛应用。PCD 车刀在刀具使用总量中所占比重越来越大,年耗量以 8%-10%的速度增长。断屑问题一直是 PCD车刀在切削加工过程中亟需解决的难题,连续不断的切屑缠绕在工件或刀具上,会加大工件已加工表面粗糙度,降低生产效率,缩短刀具使用寿命,甚至危害工作人员的安全。因此,在 PCD 车刀的切削加工过程中需要对切屑进行控制,
切屑控制的首要任务就是解决断屑问题。目前,仅有极少数公司,例如德国 Becker 刀具公司能够生产出带断屑槽的 PCD 车刀,但带断屑槽的 PCD 车刀的生产难度大、加工成本高且会影响到刀片的强度,因此,带断屑槽的超硬车刀在市场上几乎很少应用,难以得到推广。本文设计并制作出一种适用于 PCD 车刀的断屑器,在不改变车刀原有结构的前提下实现断屑功能,具有装夹牢固、调节方便的特点,并通过实验验证其断屑效果。
1 、断屑器的设计思路
1.1 断屑原理
如图 1 所示,断屑块使切屑向上卷曲,如果切屑流过断屑块上部,切屑的根部就会加上一个弯曲力矩,在靠近前刀面一侧附加了一个拉应力,在远离前刀面一侧附加了一个压缩应力,这样运动的结果就形成了向上卷曲的切屑。
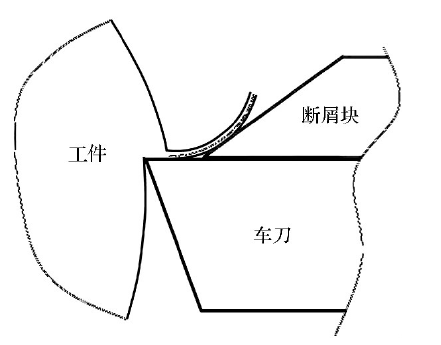
图 1 切屑生成示意图
以最大应变理论作为切屑折断判断的依据,切屑折断条件可由式( 1) 表示。

式中: ε—切屑内部应变; α—断面形状系数; hch—切屑厚度;RC—切屑生成时的卷曲半径; RL—切屑断裂时的卷曲半径;εB—切屑断裂应变。利用断屑块使切屑产生变形,增加切屑内部应变 ε,减少切屑曲率半径,从而使切屑折断,实现良好的断屑效果。
1.2 设计准则
作为原有车刀结构的附加装置,PCD 车刀断屑器需要牢固装夹于 PCD 车刀,并且可根据不同工况对断屑位置进行调节。因此,断屑器的结构需满足装夹牢固、调节方便的特点。本文秉着“两夹一调”的设计准则对断屑器结构进行设计,“两夹”指 PCD 车刀原有的压板夹紧断屑块和利用连接杆与螺母对断屑块进行辅助装夹,“一调”是指调节断屑块在前刀面上的相对位置,以满足不同的切削条件下的断屑功能。
1.3 设计思路
综上所述,根据断屑原理与“两夹一调”的设计准则设计断屑器,设计思路如图 2 所示。
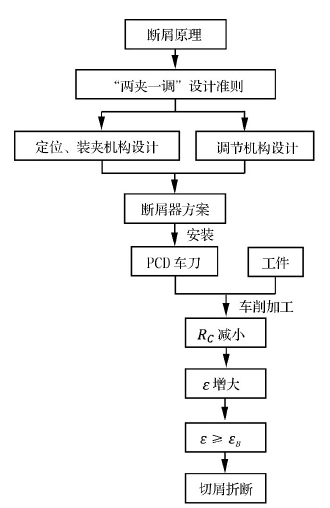
图 2 设计思路示意图
2、 断屑器的设计方案
如图 3 所示,断屑器包括断屑块、连接杆和固定螺母组件。断屑块固定在刀具原有的压板下方,且位于刀片的上端面,刀片通过刀具原有的插销固定在刀柄上,断屑块上设置有无需对车刀的原有结构进行改动的断屑块固定装置。断屑块固定装置包括连接杆,连接杆的下端一体设置有定位凸台,插销中设置有轴向的连接通孔,断屑块上设置有固定通孔,连接杆从下至上依次穿过刀柄、连接通孔和固定通孔
连接杆的上段为螺杆,螺杆向上穿过固定通孔且通过螺母组件将断屑块固定在刀片上。
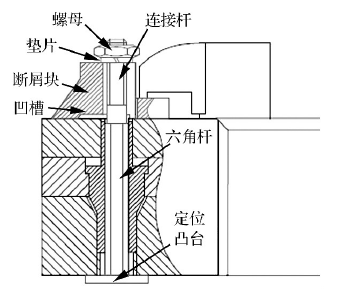
图 3 断屑器装配图
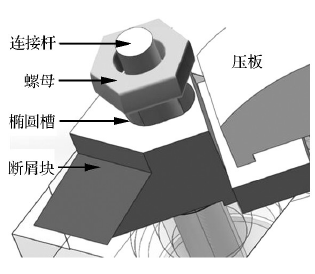
图 4 断屑器局部结构示意图
结合图 3 和 图4,“两 夹 一 调 ”的 实现方案如下:
( 1) “两 夹 ”方案: 连接杆上端与螺母通过螺纹连接,使断屑块装夹可靠。刀片压板压在断屑块后端,进一步保证固定可靠。此外,断屑块和连接杆需具备一定的特征,保证断屑功能。断屑块下端面中部设有凹槽,使其前端和后端与刀片上端面有效接触。上端面高出刀片压板前端,避免螺母装配到连接杆顶部时出现干涉。连接杆下端设置有定位凸台。连接杆需与连接通孔的形状相匹配,下端为六角杆,上段为螺杆,可与螺母连接。
( 2) “一调”方案: 断屑块顶部设有椭圆槽,便于根据实际工况调整断屑块与连接杆的相对角度与位置。综上所述,利用超硬车刀自带零件将断屑块固定在刀片的上端面,既实现了超硬车刀的断屑功能,又无需对超硬车刀的原有结构进行改动,具有普适性。并且对断屑块的定位、装夹可靠,拆装和使用方便,结构简单,成本低廉。
3 、实验验证
3.1 实验方法
首先,应用实验室的设备仪器,对所设计的断屑器零件进行 3D 打 印 和 组 装,做初步试验,优化几何 参 数。确 定 方 案后,采用线切割加工方法小批量制造实体零件,进 行 加 工、组装、调试,实物如图 5所示。
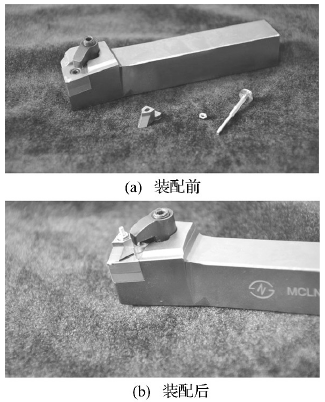
图 5 断屑器零件实物图
以 PCD 可 转 位车刀为例,选用铝合金棒料,对所制作的PCD 车刀断屑器进行断屑性能测试。车削试验在 CAK3665型数控车床上进行,无冷却液,切削用量为: 切削速度vc= 100m / min,切削深度ap= 0.39 mm,进给速度 f = 0.1 mm / r。
3.2 实验结果
图 6 为切屑对比。图 6( a) 为普通 PCD 车刀切削形成的切屑,切屑呈带状,连绵不断,断屑效果差; 图 6( b) 为装夹有断屑器的 PCD 车刀切削形成的切屑,断屑器在前刀面上被调节至合理位置,因此切屑细碎,折断效果好。这是因为,装夹有断屑器的超硬车刀切削形成的切屑流出时受到断屑台的直接阻碍,进而变形和卷曲,导致切屑内部应变 ε 值变大,当 ε 值超过切屑断裂应变εB时,切屑折断[7]。上述结果表明,在 PCD 车刀上装夹断屑器,可以实现良好的断屑效果。
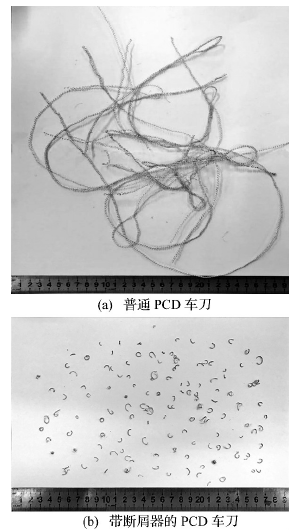
图6 有无断屑器切削形成的切屑对比
根据实验结果,收集带断屑器的 PCD 车刀车削时产生的切屑,进行切屑种类划分并统计各类切屑的数量和占比,结果如图 7 所示。
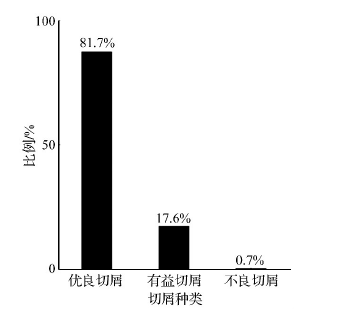
图 7 各类切屑的数量和占比
从图 7 中可以看到,切屑种类分为: 优良切屑、有益切屑、不良切屑三种。其中,优良切屑占比约为 81.7%,有益切屑占比约为 17.6%,不良切屑占比约为 0.7%,因此,超硬车刀断屑器断屑率为 99.3%,断屑效果良好。
4、 结 论
本文基于 PCD 车刀使用中的断屑需求,设计并制作出一种断屑器,车削实验表明,该断屑器具有良好的断屑效果。所设计的 PCD 车刀断屑器具有以下特点: 结构简单,不改变车刀原有结构,使断屑器成为 PCD 车刀的附件,不影响刀具性能; 装夹可靠,并具有一定调节功能,可以根据不同工况针对性地改变断屑块的位置,从而扩大断屑范围。PCD 车刀断屑器可以解决 PCD 车刀在车削加工中的断屑问题,提高机械加工过程中的加工质量和效率,也为后续设计制作其他类型刀具的断屑装置提供了借鉴思路。
投稿箱:
如果您有机床行业、企业相关新闻稿件发表,或进行资讯合作,欢迎联系本网编辑部, 邮箱:skjcsc@vip.sina.com
如果您有机床行业、企业相关新闻稿件发表,或进行资讯合作,欢迎联系本网编辑部, 邮箱:skjcsc@vip.sina.com
更多相关信息