金属切削加工振动机理及工程消除方法
2019-2-19 来源: 中航工业洛阳电光设备研究所 作者: 杨新一
【摘要】: 振动问题是金属切削过程中普遍存在的现象, 通过研究切削振动的产生机理, 并采用仿真模拟计算与加工试验相结合的方法, 介绍了金属切削过程中振动的分类与产生机理。结合具体的工程应用, 利用刚性辅助增强法和加工参数优化法这2 种常用的振动消除工程方法, 提出了判别金属切削过程中振动产生的原因, 以及抑制切削振动的工艺设计思路, 对消除切削过程中的振动以及提高零件加工质量有着积极的意义。
【关键词】: 振动机理; 颤刀纹; 工艺技术。
在金属切削过程中, 工艺系统时常会发生振动。特别是随着产品轻量化、功能多样化的需求,导致薄壁件、长悬伸零件的设计越来越多, 结构件形状越来越复杂, 在机械加工过程中, 时常会因为零件刚度差、刀具刚度差和切削参数设置不当等因素导致切削过程中产生振动。
切削过程中的振动是一种极具破坏性的有害现象, 会干扰和破坏成形运动, 引起刀刃崩裂,缩短切削系统寿命, 降低生产效率, 产生噪声污染; 因此, 研究金属切削过程中的振动产生的机理, 探讨抑制振动产生的工艺措施, 一直是机械加工领域的重要研究课题。
1.切削加工振动的分类
切削过程中的振动类型, 包括自由振动、强迫振动以及自激振动等3 种形式。其中, 自激振动可分为再生型颤振、耦合型颤振和摩擦型颤振。
2.振动的基本原理
一个单自由度的结构可以简化为由质量m 、阻尼C 和刚度k 组成的单自由度系统( 见图1)。
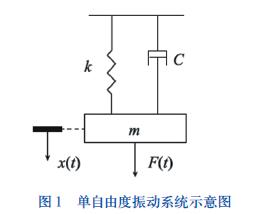
如果系统受到激励或是静止位置偏离原来的平衡位置时, 并使其进行自由的恢复运动, 系统将做自由振动。由于阻尼C 的作用, 其振动幅值随时间以系统阻尼常数的函数衰减。振动频率主要取决于系统的刚度k 和质量m 。
2.1 自由振动
假设质量为自由质量, 不受外力的作用, 静态位移为x 0 , 将系统释放, 由于工艺系统的阻尼作用, 这类振动会在外界干扰去除后迅速自行衰减, 对加工过程影响较小。
2.2 强迫振动
当系统受到外力时, 系统将进行强迫振动。若施加的外力为恒力时, 系统将经过一段时间的过渡振动, 然后在静态偏离处稳定, 当外力是谐波力时, 则会出现持续振动。
金属切削过程中引起强迫振动的因素很多,例如机床上齿轮传动不均匀和轴承制造精度不
够, 刀具上各切削刃间存在高度误差, 工件上存在断续切削或者余量不均、硬度不一致等。
2.3 自激振动(颤振)
外界不给予机床系统任何干扰, 该平稳切削加工的过程将一直保持下去; 然而在真正的生产实践中, 往往会受到很多外界干扰的影响, 也就是说, 上述的平稳切削加工过程一定会受到外界的干扰而发生振动。
2.3.1 再生型颤振
简便起见, 考虑正交切削的情况, 由外界激励引起的机床振动使得刀具与工件之间在工件进给方向上产生相对振动, 则在第1 层切削时, 在原本表面光滑的加工工件表面留下波纹, 该波纹轨迹为x (t —T ), 当第2 层开始时, 加工的内外表面都有波纹, 该波纹轨迹为x (t ), 主轴旋转1周所需的时间为T , 本次理论切削厚度为h 0 。其动态切削厚度变为:

再生型颤振产生示意图如图2 所示。从图2中可以看出, 当连续两振纹之间的相位差为0 或2π 时, 无论机床如何振动, 动态切削厚度都不会发生变化, 此时, 切削加工过程是稳定的; 当连续两振纹之间的相位差为π 时, 动态切削厚度达到最大值, 切削过程中的颠振现象最为严重。
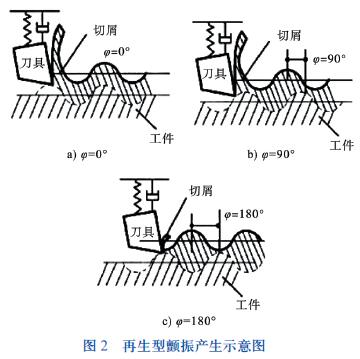
2.3.2 耦合型颤振
耦合型颤振是由于振动系统在2 个方向上的刚度相接近时导致2 个固有振型相耦合, 因而引起颤振。在切削过程中由于切削力的持续周期性变化, 导致了工艺系统的耦合振动。
2.3.3 摩擦型颤振
摩擦型颤振是指切削速度方向上刀具与工件之间的相互摩擦而引起的颤振, 产生的机理主要是在切削过程中切削力随切削速度的增大具有下降的特性, 因而产生1 个负摩擦力。而在切削过程中, 切削速度不断地发生着细微的变化, 导致了切削力不断地变化, 从而使加工系统发生颤振。总之, 自激振动是由于刀具与工件之间切削力的不断变化而导致切削厚度随着发生变化, 所以等到下一次切削时又会产生新的振纹, 如此循环反复, 在刀具与工件之间形成了一个闭环控制系统, 这个闭环控制系统是以切削力激发、动态切削厚度作为反馈的, 且切削厚度的动态变化与主轴旋转周期T 时刻前的切削振动有关的延时反馈系统。
3.切削加工过程中振动消除的工程应用
在工程应用中, 切削过程的参与者包括机床、刀具、夹具和零件, 金属切削过程中产生的振动等不稳定切削现象和其切削参与者密切相关。通过更改切削过程中参与者的结构及切削参数可以达到消除振动的目的。常用的振动消除工程方法如下所述。
3.1 刚性辅助增强法
随着我国工业技术的不断发展, 轻量化、复杂化的结构设计越来越多, 结构件的刚度问题逐渐成为导致加工质量差的关键因素, 切削振动问题频发。
由于产品性能限制, 加工零件的结构刚度差,导致切削过程不稳定, 产生振动现象。工程中常用的刚性辅助增强方法有刚性支撑法、填充法、粘结法和工艺柄辅助法等。下述以某型零件为例,介绍工程中消除振动所应用的刚性辅助增强示例。
方位部件是某型产品中的关键机械部件, 其涉及到多组精密空间孔系, 装调过程困难, 很难通过装调达到设计目标, 因此采用组合加工的方式来保证各空间孔系的设计精度。该零件的空间孔系几何公差要求达到IT5~IT6, 且结构特征中, 包含长度>190mm 的悬臂结构, 加工难度大, 设计精度难以保证。组合加工件中各零件的装配关系以及组合加工件中的悬臂特征如图3 和图4 所示。
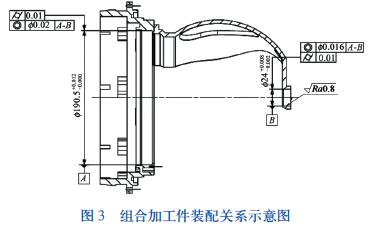
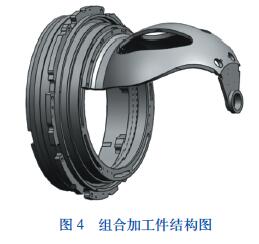
在精镗Φ24 内孔时, 内孔表面经常会出现颤刀纹。该孔系是保证产品精度的关键孔系, 其
加工质量决定了产品的使用性能, 因此, 查找该孔系的颤刀原因, 有针对性地制定解决方案是十
分重要的。
按照加工时的装夹关系对零部件进行仿真计算。结果显示零件的前4 阶振型主要是Φ24 内
孔位置产生较大变形, 因此Φ24 内孔位置为加工过程刚度薄弱点。
利用刚性- 非刚性辅助支撑方法, 在零件Φ24 内孔位置设置1 个支撑装置( 见图5), 用于
辅助增强零件的加工刚度, 零件的装配方式如图6 所示。

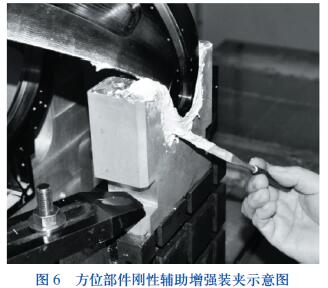
刚性支撑工装不与加工零件直接接触。刚性支撑上设有1 个容腔, 用以盛装非刚性材料, 其特点是流态时可以填充任意型腔, 固态时具有很大的刚性。辅助增强零件刚度后, 零件的首阶振动频率提升到934.54 Hz, 加工系统刚度得到了很大的提升, 进而加工颤刀纹得到了消除。
3.2 加工参数优化法
加工过程中的进给速度、切削厚度、主轴转速与切削力呈复杂的指数关系, 切削参数的选择直接影响到加工零件时的切削力大小。对于低刚度零件, 切削参数选择不当会导致零件产生过大变形, 从而会导致加工让刀或者切削振动现象。主轴转速的选择同时还关系着零件加工过程中的共振, 对于非连续切削, 零件承受着周期性变化的切削力, 若切削力变化频率与零件的固有频率相近, 将会导致零件产生共振, 影响零件的加工质量。下述以某型零件为例, 介绍主轴转速的优选方法。
在零件加工过程中, 零件受力会呈现出周期性变化的规律, 变化周期与主轴转速密切相关,周期性变化的切削力会对零件产生周期性的冲击。若冲击周期与零件的固有频率相近时, 会使零件产生共振, 导致零件表面产生颤刀纹; 因此,合理选择主轴转速, 对于避免加工共振、消除表面颤刀纹具有积极的意义。
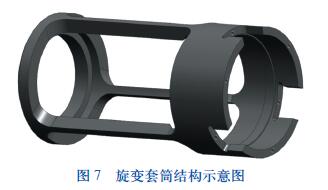
旋变套筒是某型产品中的关键零件, 其结构示意图如图7 所示。由于零件性能所限, 零件圆周面开了3 处缺口, 导致零件的刚度降低, 同时破坏了车削的连续性。该零件在加工参数选择不当时, 会在表面出现颤刀纹, 影响产品质量。
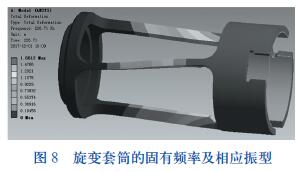
旋变套筒的前2 阶阵型图如图8 所示。结果显示, 该结构主要在3 个支撑杆右端发生变形。仿真计算结果可得, 零件的固有频率为198.95Hz。主轴转速S 与切削力激振频率p 之间的关系如下:p =zS/60。式中,p 是激振力频率,单位为Hz;z 是车削断续点个数;S 是主轴转速,单位为r/min。
为避免旋转套筒在车削过程中产生共振, 应使切削冲击频率远<200 Hz, 即控制机床主轴转速远<4 000 r/min, 因此在加工过程中应严格控制主轴转速, 避免零件因共振产生颤刀纹, 切削过程中主轴转速应控制在1 000 r/min 以内。
4.基于振动抑制的工艺设计思路
振动在金属切削过程中是普遍存在的, 有时振动不明显, 不会影响零件表面质量; 但有的振动比较剧烈, 导致加工零件表面出现严重的缺陷,必须予以减弱或消除。
加工过程中的各种振动都有其产生的机理,在实际工程应用中, 导致振动的原因也不是单一的, 需要工程技术人员根据工程实际情况, 给出合理有效的解决措施。下述给出几点减少或消除切削振动的思路。
1 ) 应排除外部振源的影响。外部振源有规律或无规律的持续振动会通过机床传递到加工零件表面, 当振动能量达到一定范围时, 零件表面会出现颤刀纹, 因此需要首先将此因素排除在外。可以为机床设备安装防震垫等措施将机床与外界进行隔离。
2) 应考虑切削过程中的断续切削、切削量不均匀问题, 该原因是导致切削过程中强迫振动的常见因素。断续切削问题可以通过调整工序设置,最后加工断续槽部分, 从而避免断续切削。切削量不均匀的问题常见于毛坯粗加工或零件拐角处,可以通过调整进刀路线、切削参数等进行消除。
3) 应考虑工艺系统刚度, 包括加工零件、刀具、工装和机床设备等各个环节的刚度。该类问题主要的表现形式为工艺系统的刚度不足以支撑该切削过程的稳定进行, 解决措施主要考虑增强工艺系统刚度或者降低切削力。零件刚度辅助增强方法主要有刚性支撑法、粘结法、填充法和工艺柄辅助增强法等形式。降低切削力主要通过调整切削参数和刀具来实现。
5.结语
随着现代工业的发展, 结构件朝着薄壁化、复杂化和整体化的方向演变, 其性能指标要求越来越高, 切削振动问题应得到有效的控制和消除。了解切削振动产生的机理及消除措施, 可以预先优化工艺设计思路, 最大程度地避免切削过程中的振动现象; 也可以有针对性地分析切削过程中的振动原因, 快速定位解决切削振动的有效方案。工程问题是复杂多变的, 同时也是有章可循的,掌握工程问题基本原理, 积累实际工程经验, 才能高效优质地完成各项工程任务。
投稿箱:
如果您有机床行业、企业相关新闻稿件发表,或进行资讯合作,欢迎联系本网编辑部, 邮箱:skjcsc@vip.sina.com
如果您有机床行业、企业相关新闻稿件发表,或进行资讯合作,欢迎联系本网编辑部, 邮箱:skjcsc@vip.sina.com