微铣刀制备技术与实验研究
2016-10-19 来源:中国工程物理研究院机械制造工艺研究所 作者:杨正杰,张勇斌,徐凌羿
摘要:微铣刀制备技术是微细铣削的关键技术之一,对微细铣削加工出的微小零部件的特征尺寸和表面质量有重要影响。从微铣刀具的材料与涂层及其制造工艺两方面,对微铣刀制备技术进行了介绍,并通过线电极电火花磨削方法制备了刀头直径为100 μm 的微铣刀,初步验证了基于自研μEM-200CDS2 微细组合电加工机床开展微铣刀在位制备的能力。
关键词:微铣刀;材料与涂层;制造工艺;在位制备
近年来, 高精度的微小零部件在航空航天、生物医学、电子工业、环境工程、通信及汽车制造等行业的应用需求不断增加。微小零部件的加工需采取可靠性高、可重复性好的加工方式,目前其加工方式主要有:LIGA 技术、激光加工、离子束加工、超声振动加工、微细电火花加工、微细切削加工等[1]。在微细切削加工领域中,微细铣削能以较高的材料去除率加工多种工程材料,并能加工复杂形状的三维结构,使微细铣削在微小零部件加工中的重要性显著增加[2]。
在微细铣削过程中,由于铣刀尺寸与结构的缩小会引起铣刀热膨胀的减小和静态刚度的增大,同时由于固有频率的提高会增加切削系统的动态稳定性[3]。但在微细铣削加工中,由于刀具及其切削参数的缩小会带来尺度效应(图1),使切削力增大,刀具易磨损和破损,切削状态极其复杂[4-5]。因此,微铣刀直接影响微小零部件的特征尺寸和表面质量,其制备技术一直是微细铣削的关键技术之一。
本文将从微铣刀的刀具材料与涂层、刀具制造工艺两方面对微铣刀制备技术进行概述,并对基于自研μEM-200CDS2 组合微细加工机床开展的微铣刀制备实验进行介绍。
1. 刀具材料与涂层
1.1 刀具常用材料
微铣刀通常是由高速钢、硬质合金、PCD(聚晶金刚石)等耐磨超硬材料制成。硬质合金具有硬度高、耐磨、强度和韧性较好、耐热、耐腐蚀等一系列优良性能,尤其是具有在高温下仍能保持很好的硬度和强度的特性(图2)[6],被广泛用作刀具材料。目前硬质合金微铣刀技术已较成熟,可商品化生产直径<0.5 mm 的硬质合金球头微铣刀和平底微铣刀,且国内已能生产直径0.2 mm的微铣刀,国
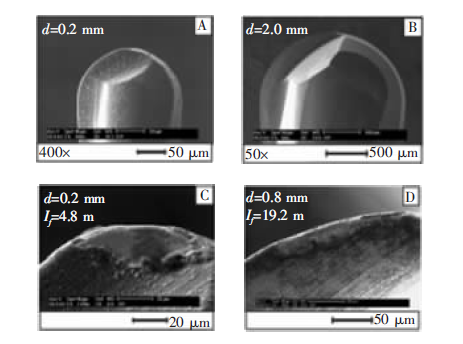
图1 刀具几何形貌与磨损的尺缩效应
外已推出最小直径达10 μm 的微铣刀[7]。图3 是硬质合金材料制作的一种典型的双刃微铣刀[1]。图4 是用线电极电火花磨削加工出的直径100 μm 的硬质合金微铣刀[8]。然而,传统的硬质合金刀具材料越来越不能满足微细加工对于刀具硬度和耐磨性的要求,需不断开发刀具材料的新牌号,使其更适应被加工材料和切削条件, 从而达到提高切削效率的目的[9-10]。
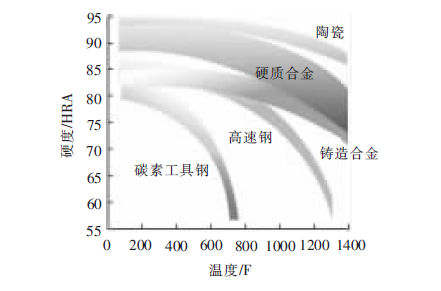
图2 典型刀具材料硬度随温度的变化

图3 WC 材料的典型双刃微铣刀
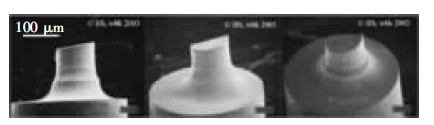
图4 WEDG 加工出直径100 μm 的WC 材料D 型微铣刀
金刚石刀具分为天然金刚石和人造金刚石刀具,具有硬度高、抗压强度高、导热性及耐磨性好等特性。金刚石作为一种超硬刀具材料应用于切削加工已有数百年历史,20 世纪70 年代人们利用高压合成技术合成了PCD, 解决了天然金刚石数量稀少、价格昂贵的问题,使金刚石刀具的应用范围扩展到航空、航天、汽车、电子、石材等多个领域。与硬质合金相比,PCD 的硬度约为硬质合金的8~12 倍,导热系数约为硬质合金的1.5~9 倍, 摩擦系数一般仅为0.1~0.3(硬质合金的摩擦系数为0.4~1),热膨胀系数约为硬质合金的1/5,因而PCD 刀具更锋利、耐用。然而,由于PCD 的高硬度与耐磨性,也使PCD微铣刀刀刃很难加工。
由于碳对铁的亲和作用,尤其是在高温下金刚石与铁会发生化学反应,故PCD 刀具不适宜加工铁及其合金材料。同时,PCD 刀具与有色金属、非金属材料间的亲和力很小,在加工过程中切屑不易粘结在刀尖上形成积屑瘤,故PCD 刀具常用作加工各种有色金属和极耐磨的高性能非金属材料,如铝、铜、镁及其合金、硬质合金、纤维增塑材料、金属基复合材料及木材复合材料等[11]。
1.2 刀具涂层
涂层是在韧性较好的硬质合金或高速钢刀具基体上涂覆一层耐磨、耐高温的金属化合物而获得的。涂层技术是解决刀具材料中硬度、耐磨性与强度、韧性之间矛盾的一个有效措施,涂层的应用极大地改善了刀具性能。目前,PCD 涂层刀具与CBN涂层刀具得到越来越多的重视, 硬质合金基底的PCD 涂层刀具不但有高硬度、高耐磨性、高导热性、低摩擦系数、低热膨胀系数等PCD 的优点,还具有硬质合金良好的强度和韧性[12]。Goto 等[13]研制了直径30 μm 的CBN 涂层铣刀, 并对其加工效果进行了分析。Tugrulözel 等[14]通过有限元分析及实验验证了CBN(氮化硼)涂层微铣刀比无涂层的微铣刀更耐热耐磨。图5 是PCD 涂层刀具的一般结构,图6是有涂层与无涂层磨损的比较。
2. 刀具典型制造工艺
微铣刀的刀具制造有精密磨削、聚焦离子束加工、电火花加工、激光加工、超声振动研磨及组合复合加工等多种工艺,目前对于微铣刀制备的研究主要集中在精密磨削、聚焦离子束加工及电火花加工工艺方面。
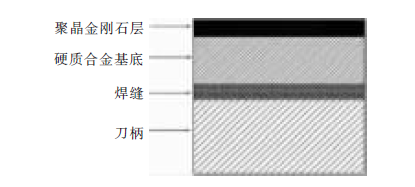
图5 PCD 刀具的一般结构示意图
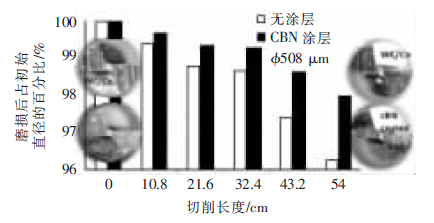
图6 由于磨损引起的电极直径变化的比较
2.1 精密磨削法
精密磨削是用微小型金刚石砂轮磨削实现对硬质合金、高速钢、金刚石等超硬材料的刀刃成形。精密微细磨削技术是较成熟的微细铣刀制备和修正工艺, 能满足一定直径尺寸的微细铣刀的制造。但当微细铣刀的特征尺寸降低到某一特征值后,微细铣刀在磨削成形时会因刚度变差而导致其应力变形大甚至断裂失效,成为微细铣刀发展的一个技术瓶颈[15]。Onikura 等[16]通过超声振动磨削方法加工出直径11 μm、长160 μm 的高深径比刀具。Aurich等[17]采用精密磨削方法加工出直径10~50 μm 的微立铣刀(图7)。
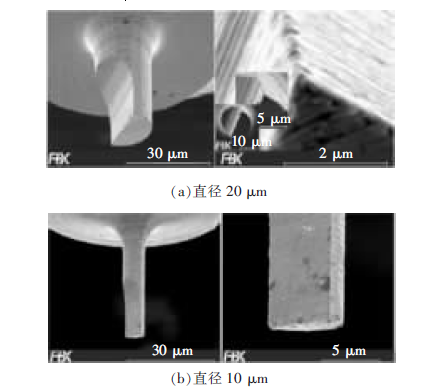
图7 D 型微立铣刀
2.2 聚焦离子束法
聚焦离子束溅射技术(FIB)的基本原理是在离子柱顶端的液态离子源上加强电场,形成数十KeV的正电荷离子束,并通过计算机控制高能离子束聚焦轰击工件表面,将高能离子束的动能传递到工件的原子或分子上,从而产生溅射效应达到去除材料的目的。加工原理示意图见图8。
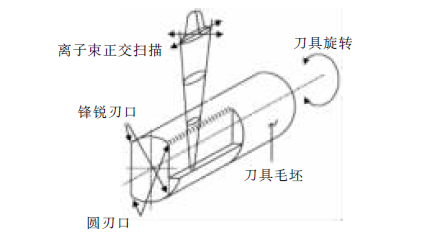
图8 FIB 的基本原理示意图
利用FIB 技术可对硬质合金、高速钢、单晶金刚石等多种刀具材料进行显微加工。与精密磨削相比, 基于FIB 技术的刀具成形过程没有机械力的作用,刀具在制造过程中不会破损,能制备出具有极小特征尺寸及纳米级刃口半径的微刀具。但FIB 的缺点在于设备价格高、材料去除速度慢及难以获得凹曲面形状。图9 是用FIB 技术制作的直径约为25 μm 的微铣刀,其轮廓形状有两面体、四面体和六面体,切削刃分为2 刃、4 刃和6 刃,刀具材料为高速钢和硬质合金[18]。利用这些刀具可分别对铝、黄铜、4340 钢和PMMA 等工件材料进行微细铣削加工。图10 是张少婧[19]研制的直径50 μm 的双刃立铣刀(图10a) 和直径约15 μm 的三刃立铣刀(图10b)。
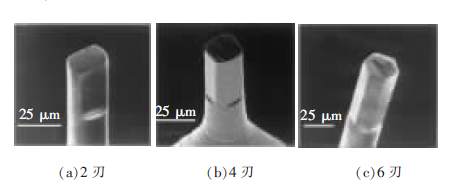
图9 FIB 加工出的微铣刀
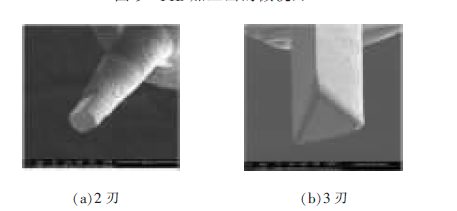
图10 FIB 加工出的微铣刀
2.3 电火花加工法
线电极电火花磨削(WEDG)是目前微细刀具制造技术的研究热点。该工艺的材料蚀除机理与普通电火花加工相同,通过导电电极丝和工件材料之间脉冲放电时产生的电腐蚀来蚀除多余材料,以达到对工件形状、尺寸和表面质量的要求,多用于高强度、高刚度、高硬度的难加工材料(如PCD)的加工。对于电火花加工微铣刀的研究主要集中在制作直径更小的微铣刀及获取更好的加工质量方面。Yan 等[20]通过线电极电火花方法制造了直径50 μm非圆截面的微细立铣刀。Fleischer 等[21]通过有限云方法设计出单刃微细立铣刀,并用线电极电火花方法制造出直径50 μm 的微铣刀(图11)。Gao 等[2]研究了采用线电极电火花方法加工微铣刀时放电参数对微铣刀加工质量的影响。
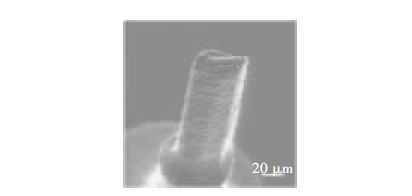
图11 直径50 μm 的螺旋型微铣刀
总体而言,相比于精密磨削加工,特种加工方法的非接触加工、无宏观切削力及适于微三维结构加工等优势,使其更适合微铣刀的制备。而对于目前在微铣刀制备中应用较广的电火花加工和聚焦离子束加工技术,电火花加工在去除率和加工成本方面更具优势,但其表面特性和尺寸精度落后于聚焦离子束溅射技术。今后,微铣刀制备技术的发展将趋于获得更小尺寸、更好表面质量、更高加工效率和更可靠的加工稳定性,电火花、FIB 等特种加工的复合或组合加工方法,将会是微铣刀制备领域的重要手段。
3. 微铣刀在位制备实验
中物院机械制造工艺研究所从2000 年开始对微细电加工技术进行研究, 研制出的μEM-200CDS2 微细组合电加工机床(图12)综合了微细电火花、微细电解及微细超声等先进的工艺手段,配置了自主研发的高精度高稳定性床身、宏微结合的进给装置、高频窄脉宽微能脉冲电源、多功能高精度复合主轴、双功能在位精密磨削装置及在位精密测量装置等关键单元。其中,宏微结合进给装置的分辨率可达0.05 μm, 高频窄脉冲电源的脉宽可达到60 ns,机床直线轴的分辨率可达0.1 μm,能满足微铣刀在位精密制备的精度要求。
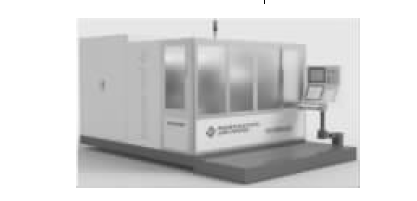
图12 16 轴的μEM-200CDS2 型微细组合电加工样机
为了充分利用μEM-200CDS2 机床的在位精密微细修整能力,实现微铣刀的在位精密制备,本文在该机床平台上开展了刀头直径为100 μm 的微铣刀精密制备实验。
3.1 微细立铣刀的设计与加工
简单异形结构的微铣刀与目前商品化的螺旋刃微铣刀相比,具有刚度好、制备容易等优点,因而本实验制备的微细立铣刀采用结构简单的直刃D 型(图13),主要特征尺寸如下:刀柄直径0.9 mm,刀颈直径300 μm,刀头直径100 μm,刀头长度300 μm,铣刀总长20 mm,主切削刃与底切削刃前角均为0°,底切削刃后角为20°。微细立铣刀材料选用目前微铣刀制备最常用的硬质合金材料。
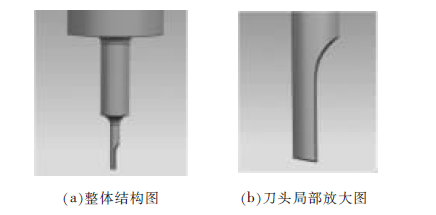
图13 微细立铣刀的结构
微细立铣刀毛坯为直径0.9 mm 的硬质合金棒料, 装夹在可沿Z 向作进给运动的机床主轴上,线电极装夹在可沿X 向作进给运动的工作台上,该线电极直径为0.12 mm。加工过程分为4 步:外圆面粗加工、外圆面精加工、前刀面精加工和底面精加工。为提高加工精度,每步均采用分层加工的方式。如表1 所示,外圆面加工时主轴旋转,其自下而上的运动为主运动,每加工一层,线电极沿X 向进给一次。粗加工时电压为100 V,单层进给量为20 μm;精加工时电压为80 V,单层进给量为5 μm。前刀面加工时主轴定位到0°不旋转,其自上而下的运动为主运动,每加工一层,线电极沿X 向进给一次,加工电压为80 V, 单层进给量为2 μm。底面加工时主轴定位到180°不旋转,主轴与工作台联动实现20°斜面的加工,每加工一层,线电极沿Z 向进给一次,加工电压80 V,单层进给量1 μm。
3.2 实验结果
如图14 所示, 扫描电镜下的微细立铣刀有良好的几何位置精度,表面较平整,刃口半径<3 μm,刀刃锋利, 初步验证了μEM-200CDS2 机床具有良好的微铣刀在位制备能力。
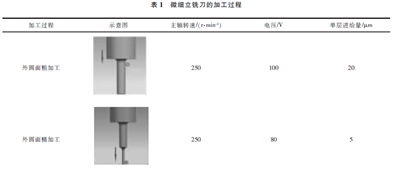
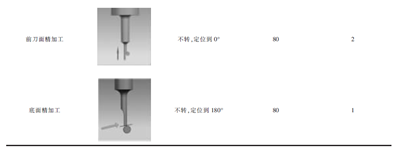
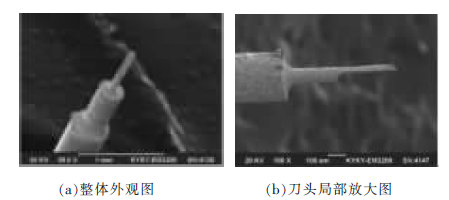
图14 直径100 μm 的直刃D 型微细立铣刀扫描电镜图
4. 结束语
在微细铣削加工技术领域,刀具材料以硬质合金为主, 研究热点集中在开发新牌号的硬质合金上,同时对PCD、PCBN 等其他耐热耐磨材料的研究也越来越多。刀具涂层的发展特点是多样化和系列化,在层出不穷的涂层新产品中,既有适应高速切削、干切削和硬切削的耐磨、耐热涂层,也有适应断续切削的韧性涂层,还有适用于干切削及需要降低摩擦系数的润滑涂层, 以硬质合金为基底的PCD、CBN 等涂层刀具的研究越来越受到重视。
随着微型铣刀的发展, 刀具形式趋于多样化,刀具形状一般区别于常规的普通铣刀。微型铣刀的切削刃有类似于普通铣刀刃口形状的螺旋刃,也有特别经过设计的独有的三角形截面立铣刀、半圆形单刃铣刀和正六边形的六刃立铣刀。所有目前常用的微铣刀制造工艺以特种加工为主,加工效果较好的方法为聚焦离子束加工,而性价比较高的方法为电火花加工。今后,微铣刀制备技术的发展将趋于获更小尺寸、更好表面质量、更高加工效率和更可靠的加工稳定性,电火花、FIB 等特种加工的复合或组合加工方法,将会是微铣刀制备领域的重要手段。
实验证明,中物院机械制造工艺研究所自行研制的μEM-200CDS2 微细组合电加工机床能满足微铣刀在位精密制备的要求,具有良好的微铣刀在位制备能力。
投稿箱:
如果您有机床行业、企业相关新闻稿件发表,或进行资讯合作,欢迎联系本网编辑部, 邮箱:skjcsc@vip.sina.com
如果您有机床行业、企业相关新闻稿件发表,或进行资讯合作,欢迎联系本网编辑部, 邮箱:skjcsc@vip.sina.com