汽车内外饰验证台架设计与开发
2021-6-21 来源:东风汽车公司技术中心 作者:杨 兴
摘要 : 随着中国汽车市场竞争加剧,顾客对于汽车品质提出更高的要求,无论从外观、内饰,智能网联化、综合能耗、声噪指标都有新的诉求。作为汽车研发部门,东风汽车技术中心已初步具备仿真、色彩、验证模型设计及主模型加工能力。汽车内外饰验证台架设计及开发主要解决整车开发前期设计方案是否合理和装配验证是否干涉的作用。本文通过东风自主轿车内外饰验证台架 X53 项目设计与开发过程,对今后该类工程模型自制工作做了有益的探索。
一、汽车内外饰验证台架的概念和用途
内外饰验证台架是为了在 ET0 前验证车身内外饰件结构数据,验证汽车零件结构,验证装配可行性,验证 DTS 制作的工程验证模型。通过内外饰验证台架,不仅能够进行零件装配验证,同时能够进行感知质量评价,在 ET0 阶段作为车身内外饰件检具,验证设计结构作为标准白车身,安装 RP 件或 ET0 件进行人机验证。
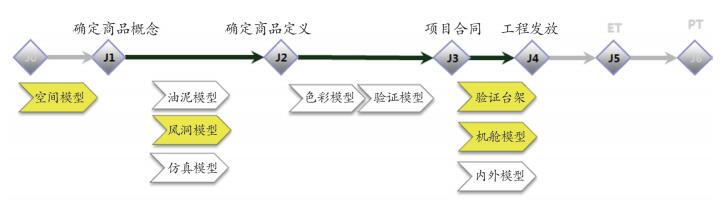
图 1 汽车相关模型开发流程图
二、汽车内外饰验证台架主要的技术要求
1.内外饰验证台架模型材料要求
采用钢管骨架,5166 代木为型面材料,表层加工厚度 30mm 以上。采用钢板底座,底板厚度要求 15mm 以上,检具本体采用可加工树脂板材为型面材料。型面轮廓材料为 5166 代木,其性能要求 : 密度≥ 1.2g/cm3, 硬度邵氏 D ≥ 75,线性热膨胀系数 (10-6m/℃ ): ≤ 35。定位面及支撑面材料采用 SK5 或相当材料,其结构必须采用可拆卸式结构,不允许采用胶水粘结。
2.内外饰验证台架骨架制作要求
①骨架材料为 A3 钢,120×60mm 方钢管厚度为 5mm,50×50mm 方钢管厚度为 3mm。
②骨架制作根据设计定义的整车姿态,可以调整姿态 ; 骨架要求具备用于二次加工的复位基准和对刀块 ; 有可连接风洞五带系统的固定结构 ;有可拆卸的副骨架,用于支撑模型,以确保模型在长途运输途中安全。
③骨架满焊,焊缝无虚焊、气孔、裂纹,骨架外表面焊痕磨平,焊接完进行不低于 48 小时人工时效处理,骨架制作完成后,本体需涂防锈漆,基准块涂防锈油。
④ 骨架基准面垂直及平行度≤ 0.05mm ,安装基准孔距公差≤ 0.02mm,整体安装后的骨架总体尺寸误差小于 2mm。
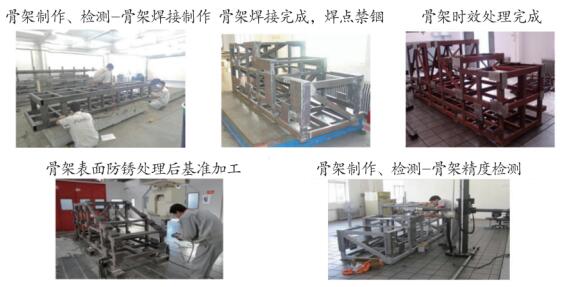
图 2 内外饰验证台架骨架制作流程图
3.内外饰验证台架试制精度要求
①精确制造检具所有的部件包括检具基座、定位基准和检验零件,以保证产品检验所需精确度。
②硬质模型工作型面的精度误差应小于0.20mm。
③所有用于被测零件的定位基准在检具上的位置公差都必须限制在 ±0.10mm 以内。
④ 硬质模型的所有用于检测被测零件的零件包括检验销和导套,在检具上的位置公差都必须限制在 ±0.15mm 以内。
⑤用于内部线条 / 塞片检验的表面轮廓特性在检具上的位置公差都应该限制在 ±0.15mm 以内。
⑥用于边缘线条 / 塞片检验的表面轮廓特性在检具上的位置公差应限制在 ±0.20mm 以内。
⑦ 模板( 活装块)在检具上的公差应限制在 ±0.20mm 以内。
⑧作为目测基准的公差应在 ±0.30mm 以内。
⑨零件制造公差分列如下。
坐标线 :0.05mm; 无搭接装配要求的全部形状 :±0.30mm; 有搭接装配要求的形状 :±0.15mm; 支承及定位公差 :±0.1mm; 对称形状的不对称度 :0.20mm; 左 / 右检具的不对称度 :0.30mm; 最大加工刀痕深度 :0.05mm;非功能孔目测刻度 :±0.30mm; 用销规检查的一般功能孔位置度 :±0.15mm; 用销规检查的重要功能孔位置度 :±0.10mm; 一般轮廓对齐处 :±0.30mm; 重要轮廓对齐处 :±0.15mm; 某一产品的特性偏离上述规范时,检具的公差可采用 1/4 准则,在产品图纸上针对某一特别产品特性标注公差的 1/4 可用作检具制造公差。
4.内外饰验证台架试制骨架强度要求
①内外饰验证台架骨架必须进行退火处理,保证整个骨架的强度和刚度。
②在搬运、包装及试验时要求保证模型的完好性,保证整车、零部件及零部件之间的连接不发生断裂、脱落等损坏事件,油泥表面不发生开裂现象。
三、内外饰验证台架零件构成与关键
总成零件设计要点
1.设计使用的CAD软件
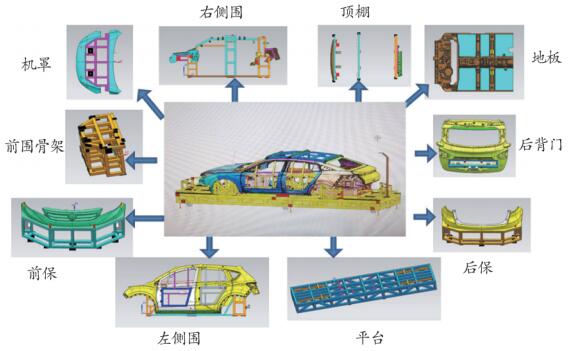
图 3 汽车内外饰验证台架零件构成
UG(Unigraphics NX) 是 Siemens PLMSoftware 公司出品的一个产品工程解决方案,它为用户的产品设计及加工过程提供了数字化造型和验证手段。Unigraphics NX 针对用户的虚拟产品设计和工艺设计的需求,提供了经过实践验证的解决方案。本次设计使用的设计和编程软件为 UGNX12 版本。
2.关键总成零件设计要点
(1)前保总成设计方案
长 =(车头最前位置 - 前轮眉边界)-30mm(柔性板厚度),考虑不同车型在柔性骨架上的通用 ; 宽 = 右侧前保安装面 - 左侧前保安装面 ;高 = 前格栅下边界 100mm 处-前保下边界100mm 处 -30mm(柔性板厚度)选取最低高度为柔性骨架,针对高度高的车型可在柔性板和模型间增加垫块。

图 4 前保总成装配图
(2)后保总成设计方案
后保设计方案使用柔性安装板。柔性安装板为 30mm 厚度铝合金板,均布直径 10mm 销孔,孔间距为 50×50mm,安装板尺寸参考骨架本体尺寸 ; 连接方式 : 骨架与柔性板之间使用螺栓紧固连接 ; 柔性板与模型之间通过柔性板上销孔使用螺栓和销等方式连接。
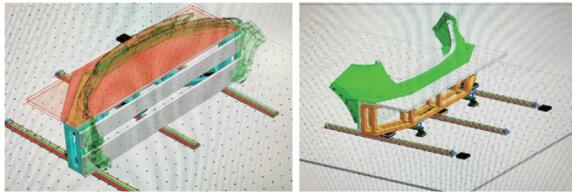
图 5 后保总成装配图
(3)前门总成设计方案
内外饰验证台架验证门总成使用单边一侧进行验证,设计为左侧前门,B 面保留完整钣金面。玻璃导轨、B 面和 A 面一体式加工,玻璃导轨外表面加厚 10mm。模型上保留大小 20×20mm的加工基准,门前后各一处。参考车身门钣金保留车身内饰件和后视镜等安装点,安装点处布置金属镶块,内嵌于模型内。玻璃单独加工,水切处设置螺栓孔用于固定。前门分别设置三处拧紧在侧围上的销孔,上端两处下端一处,锁紧方向为正 Y 向 ; 并预留相应的销控垫板结构。为便于门的拆迁,将铰链处 A 面门板作为附件,单独安装在门板主体上。
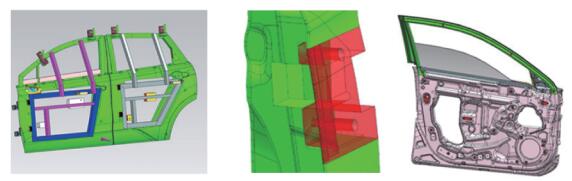
图 6 前门总成装配和内部结构图
(4)后门总成设计方案
后门主体骨架是 “口” 形,加上横竖两条加强筋,另焊接两根连接骨架与车门模型上端连接,连接骨架位置和间距按车门尺寸均布。骨架前段焊接与铰链连接的安装铁块,后方无锁扣结构。骨架与代木主体之间采用糊状代木连接,无螺栓等连接结构。主体框架距离钣金边界距离≥ 110mm。模型避让门板主体骨架外边界距离≥ 5mm。材料 45 钢,厚度 5mm ,20×40mm管材焊接而成 。车门开启角度以设计输入为准。
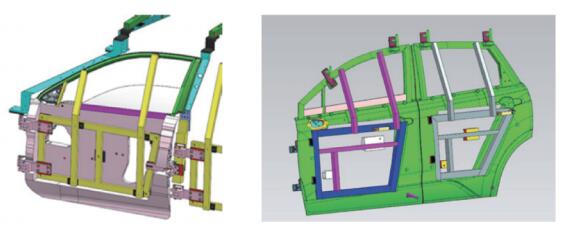
图 7 后门总成装配和内部结构图
(5)后尾门总成设计方案
尾门结构设计包含 : 模型设计及骨架设计。模型设计 : 参考尾门内外钣金数据、预留与骨架铰链安装点、预留尾门饰板安装点,与侧围配合安装点,基准块布置 ; 骨架设计 : 与顶盖处铰链骨架连接,预埋加强钢管骨架,尾门支撑杆处骨架 ; 尾门本体模型设计结合内外钣金数据设计成一体。
台架主体骨架通过铰链与尾门骨架连接 (; 参考数据撑杆安装点高度,开启角度 77° - 开启角度 90°)尾门模型内预埋钢管与尾门铰链及支撑杆骨架连接 ; 保留饰板以及尾灯安装点,安装点布置销套 ; 尾门模型主体通过左右两侧边定位销限位 ; 尾门模型钣金翻边单独加工并与主体粘贴 ;设计四个基准块 30×30mm,位置左右对称均布。
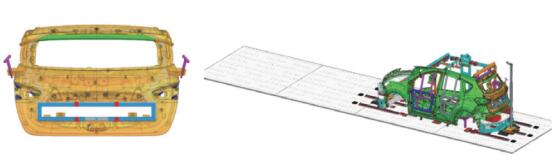
图 8 尾门总成装配和内部结构图
(6)地板总成设计方案
型面 : 以钣金面为基础,人的脚部踩踏区域设计为平面。数控加工 : 将前排座椅间隙和人的脚部踩踏区域与整体切分开,其 他区域一体式加工或者拆分为 2 个大块加工。定位 : 在中部区域开槽与骨架匹配 + 螺栓定位。材料使用 : 主体采用密度 1.2g/cm3 的代木 ; 所有安装孔位制作金属镶套 ; 前排座椅间隙和人的脚部踩踏区域采用密度 0.2g/cm3 的 PU,厚度约 30mm。
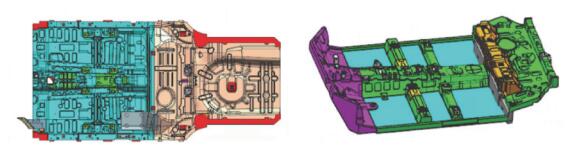
图 9 地板总成装配和内部结构图
(7)发动机罩总成设计方案
支撑点位:后端两点为铰链,中前段3点支撑。
中间为钢骨架,周边采用代木制作。由于机舱不安装零部件,B 面只保留边界 50mm 的钣金结构,其余地方做成平面或光滑曲面(简化处理)。
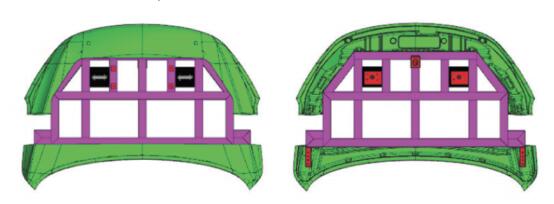
图 10 发动机罩总成装配和内部结构图
(8)侧围总成设计方案
驾驶员侧完整结构,副驾驶侧只有骨架支撑结构 , 结构必须采用可拆卸式结构,不允许采用胶水粘结。中间为钢骨架,周边采用高密度代木(密度 >1.2g/cm3)制作。安装的孔位和定位采用实车状态,安装孔位必须镶嵌金属机构保证拆卸换装及强度。外观不是重点项,连接结构可以从 A 面打孔进行连接。
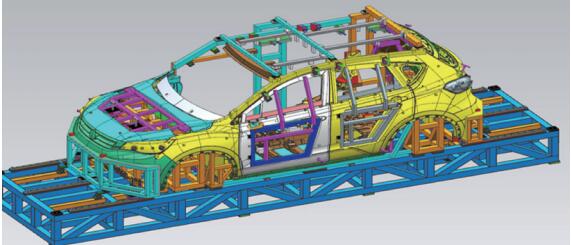
图 11 侧围总成总成装配结构图
四、内外饰验证台架工艺制造
内外饰验证台架试制分为以下几个阶段 : 第一阶段为骨架制作,包含骨架设计、下料切割、拼料焊接、热处理、安装孔和基准面机加、骨架检测和防锈处理等 ; 第二阶段为内外饰验证台架分总成主体结构设计 ; 第三阶段为零部件制作及装配,根据设计图纸要求制作分总成的毛坯,主要零件采用数控加工进行,做好每个分总成相应的装配基准,制作完成后对应主骨架的基准进行相应位置的装配工作 ; 第四阶段为检测,检测零件表面、整车姿态、定位安装孔位、间隙面差。主要工艺制作流程按照以下顺序进行 : 骨架设计→骨架确认→骨架焊接→骨架加工→骨架检测→数据处理→毛坯制作→粗加工→ NC 加工→分总成与骨架装配→五轴加工→车身附件 NC 加工→样件修配→组配→评审→喷漆→组配。
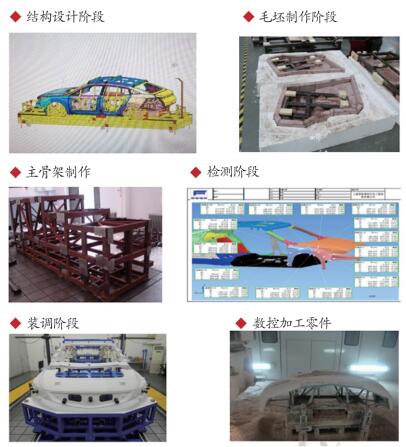
图 12 内外饰验证台架制作流程图
1.数控编程加工工艺方案
数控编程的精度按照规范要求,其中 A 面精度≤ 0.3mm,切削的最大残留高度≤ 0.02mm,DTS 检测值公差≤ 0.2mm,相应编程参数应与此对应。数控编程使用公差参照 GB/T 1804一般公差未注公差的线性和角度尺寸的公差和GB/T 1184 形状和位置公差未注公差值进行设定。粗加工,切削步距设定为所使用刀具直径的1/4,例如 φ20mm 球刀切削间距设定为 5mm。精加工切削间距设定为所使用刀具直径的 1/40。例如 φ20mm 的球刀取切削间距设定为 0.5mm。模型编程坐标系建立包括坐标原点选择和坐标轴确定,数控机床坐标系标准为右手笛卡坐标系,确定模型在机床上的装夹方向和相对位置。模型整体数控加工的编程按照 EQCY-5044 汽车验证模型设计规范定义的设计基准编制。使用编程软件 NX12.0, 数控加工设备JOBS 五轴加工中心和马迪克斯五轴加工中心。
2.内外饰验证台架质量控制方案
为保证整个验证台架制作顺利、有序、按时完成,在骨架制作完成、零件装配完成及交付之前三个阶段进行验收安排。第一次验收为骨架验收,需检测骨架的定位孔及定位面的尺寸精度及后处理状态,提供热处理报告及实际尺寸与数据尺寸对照表,检测全过程必须有技术人员一直在场 ; 第二次验收是零件装配完成之后,确认型面质量、样件质量等满足设计功能要求 ; 第三次验收是在整车验证台架检测后进行,确认内外饰验证台架外观、尺寸是否满足要求并整改到位达到设计零件互换要求,采用三坐标打点检测,检测总点数不得少于 500 点,测点排布原则 : 功能敏感区加密点数,在过渡区减少点数。
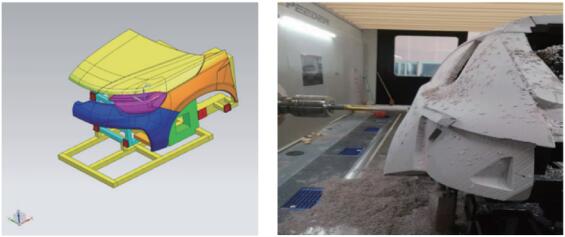
图 13 数控编程和数控加工图
五、总结
经过此次项目制作,增强了技术中心制作工程类模型的能力。主要体现在 : 提高了内外饰验证台架的设计能力 ; 通过自制缩短数控加工制作时间 ; 有效验证了汽车前期研发出现的各类问题,加快了整车研发的试制周期,在国内汽车模型制造领域具有实用和推广价值。
与国际先进模型制造企业相比,国内模型制作的能力已经接近国外先进水平,但是由于起步较晚,专业性积累较少,在现场调试数据的反馈、搜集、整理并重新融入设计再应用环节尚有一定的差距,各个模块数据库的建立还处在比较初级的阶段,随着今后经验的积累,将逐步缩小与国外先进技术差距,高端工程类模型制造能力会不断加强。
投稿箱:
如果您有机床行业、企业相关新闻稿件发表,或进行资讯合作,欢迎联系本网编辑部, 邮箱:skjcsc@vip.sina.com
如果您有机床行业、企业相关新闻稿件发表,或进行资讯合作,欢迎联系本网编辑部, 邮箱:skjcsc@vip.sina.com
更多相关信息