舱体非连续内型面数控铣削控制系统设计
2020-4-30 来源: 上海航天精密机械研究所 作者:张维轩 黎朝晖 何 军 周愿愿 张小龙
摘要: 为了提高舱体内型面加工的效率和自动化程度,突破舱体加工工艺瓶颈,研制了基于西门子 828D数控系统的铣削专用加工设备。并针对设备结构特点和加工的特殊需求,设计开发了该设备的数控系统,完成数控系统的 PLC 程序和舱体内型面加工的数控编程,并通过了实际工件的工艺试验验证。试验结果表明该设备及数控系统运行稳定可靠,满足零件加工需求,有效提高了加工效率。
关键词: 舱体内型面; 西门子 828D; 铣削加工
非连续内型面结构可以有效地减轻舱体重量、降低成本,此类结构遍布于多种武器型号镁铝合金铸造舱体中[1]。以某型号舱体为例,舱体内型面结构如图1 所示。
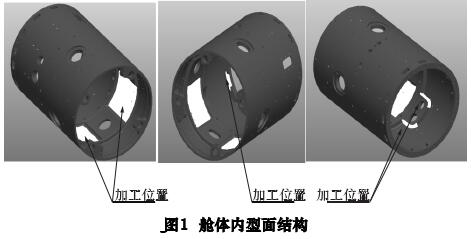
对其内型面结构进行了工艺分析: 该舱体大致呈圆柱体,选择舱体左端面为夹持面( 借用舱体左端面的销孔进行定位) ,刀具从右端面进入舱体内部加工。舱体内型面结构十分复杂,为了提高舱体加工效率,保证舱体加工精度和质量,迫切需要研制一台专用的数控铣削专用机床。机床结构部分已经设计完成,需要研制一套可以配合机床结构的控制系统,满足舱体内型面加工要求并提高加工效率,进而实现舱体的批量生产加工。
1 、设备控制系统硬件布局
控制系统的设计主要包括两部分: 硬件结构的布局和软件程序的设计。其中,硬件结构的布局主要是数控装置、PLC、伺服驱动器、伺服电动机、反馈系统以及其他辅助装置的集成; 软件程序设计主要包括机床参数设置、PLC 编程等程序设计。控制系统是数控机床的核心部分,主要包括数控系统、驱动系统以及反馈系统三部分[3]。数控系统由数控装置、PLC、控制面板、手轮、人机接口单元组成,信息通过控制面板和手轮输入到数控装置中,经处理后再传输到 PLC 和驱动器中; 驱动系统具体由电源模块、电动机模块、伺服电动机等部件组成,主要任务是执行加工信息,带动机床移动部件实现舱体内型面铣削加工; 反馈系统主要由光栅尺、圆光栅、编码器和集线器等部件组成,它的作用是实时测量加工的当前位置,通过编码器处理将信息反馈给控制系统,使控制系统实时对驱动系统进行调整和误差补偿。控制系统原理如图 2 所示。
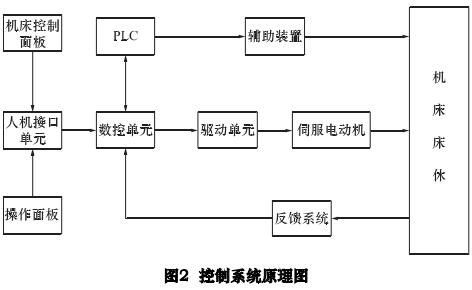
1. 1 数控系统布局与选型
数控系统是控制系统的核心部分,数控系统的型号对机床的工作方式、工作效率有决定性作用。根据机床工作原理和舱体加工需求对数控系统进行选型,考虑可靠性和性价比等因素,最终选择西门子SINUMERIK 828D 数控系统,它是将 CNC、PLC、HMI( 人机界面) 、闭环控制功能和通讯功能集合成一个数控单元 NCU 的数控系统[4],极大地提高了系统的耐久度和可靠性。西门子 828D 数控系统实物如图 3所示。
根据所选数控系统的型号设计适合其工作原理的控制系统电气图,控制系统电气图是控制系统总体和局部设计的说明书,主要包括 AC 电源电气图、数控系统电气图、驱动连接电气图、反馈系统电气图、其他辅助电气图等。总电源为 380 V/50 Hz 交流电,通过变压器、整流器和电抗器转化为 24 V 直流电给数控系统、电源模块和反馈系统供电。数控系统连接如图 4所示。
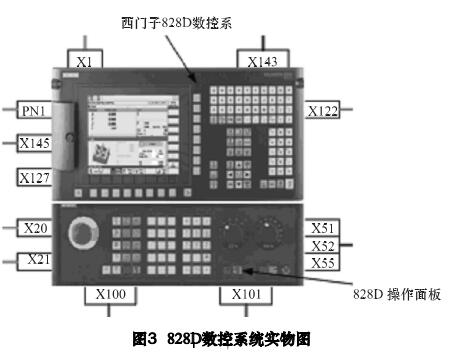
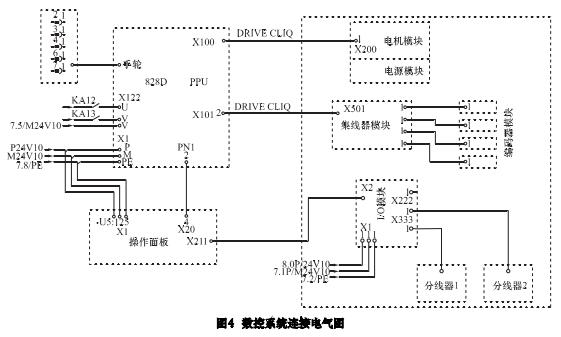
1. 2 驱动系统设计与选型
驱动系统是控制系统的重要组成部分,主要包括伺服驱动器、伺服电动机、驱动电路等部件。其中,伺服电动机和伺服驱动器是主要部件。
伺服电动机分为永磁同步伺服电动机和感应异步伺服电动机。永磁同步伺服电动机在反应速度、控制精度、可靠性等各个方面都优异于感应异步伺服电动机,因此选择永磁同步型。在伺服电动机具体型号的选择上,分别根据转速要求计算、转动惯量要求计算和转矩要求计算综合考虑伺服电动机型号的选择; 又依据价格、系统兼容性等实际问题,最终选择西门子1FK7 系列伺服电动机。具体为 2 个 1FK7103 -2AC71-1RH1 型号、2 个 1FK7084-2AF71-1RH1 型号和 1 个1FK7083-2AF71-1RH1 型号的伺服电动机,其容量分别为: Y 轴和 Z 轴 ( 3. 1kW/20N · m) 、X 轴 和 主 轴( 5. 2kW/36N·m) 、A 轴( 3. 8kW/16N·m) 。
为了配合西门子 1FK7 型号系列伺服电动机,选择西门子公司最新一代驱动器———Sinamics S120 驱动器。该驱动器采用最先进的硬件、软件和通讯技术,可以自动识别 1FK7 系列伺服电动机,具有更好的控制精度和动态控制特性。根据各轴伺服电动机的总容量,最终选择了 Sinamics S120 书本型非调节驱动器,包含 16 k W 的电源模块、主轴 X 轴共用的双轴电动机模块、Y 轴 Z 轴共用的双轴电动机模块和 A 轴的单轴电动机模块。驱动器连接如图 5 所示。
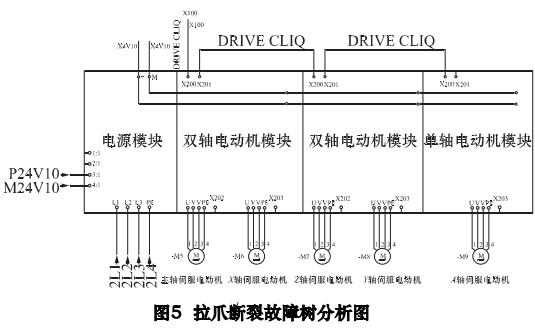
电流经过熔断器、滤波器、电抗器等电路元件进入电源模块,再由电源模块给 3 个电动机模块供电; 主轴 Z轴电动机模块的 X200 接口通过 DRIVE CLIQ 通讯电缆与数控系统 X100 接口连接通讯,3 个电机模块之间也通过 DRIVE CLIQ 通讯电缆连接通讯; 电动机模块的 X202、X203 接口与各台伺服电动机连接通讯。
1. 3 反馈系统设计
在实际加工中,由于很多不确定因素和机床固有问题的存在,导致了多种类型的加工误差,因此需要一个反馈系统对加工情况进行实时监测和信息反馈,使数控系统及时做出调整以补偿加工误差。数控系统、驱动系统和反馈系统构成了一套完整的闭环控制系统,根据反馈系统测量位置的不同,分为半闭环控制系统和全闭环控制系统,如图 6 所示。
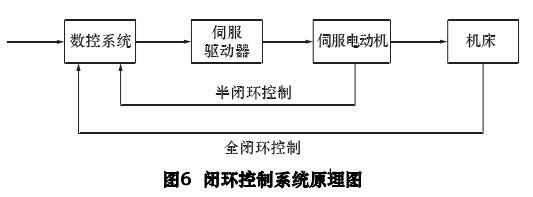
由于全闭环控制系统是直接将加工位移信息反馈给数控系统,从而使加工精度更高,因此采用全闭环控制系统方案。全闭环控制系统中,反馈系统的测量元件位于机床移动部件上,使用光栅尺作为 XYZ 轴直线位置测量元件,使用圆光栅作为 A 轴角度测量元件。根据价格性能对比,光栅尺选择海德汉公司的 LC485系列绝对式直线光栅尺,精度等级为±3 μm,输出信号为 EnDat2. 2; 圆光栅选择海德汉公司的绝对值圆光栅RBN2239。反馈系统连接如图 7 所示。
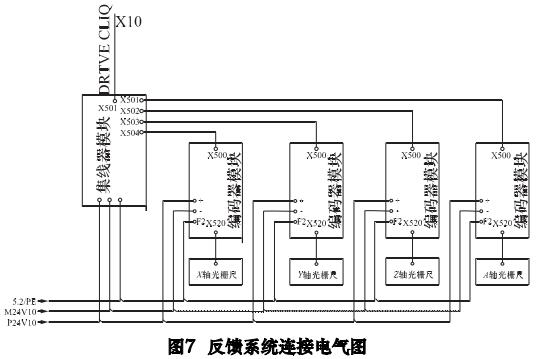
光栅尺和圆光栅测量到位置和角度信息通过编码器 SMC20 处理,将信息转换为电信号传输至集线器DMC20,信号经过放大处理传输至数控系统。数控系统再根据信号控制驱动系统对加工误差实时补偿,最终实现全闭环控制。该设备全闭环控制系统如图 8所示。
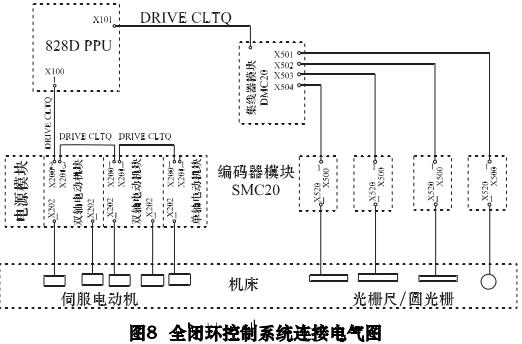
2 、设备控制系统软件编程
PLC 是实现数控系统与机床信息交换的模块,是数控系统和机床机械结构之间连接的纽带。PLC 的工作方式是采用循环扫描的模式[5],在程序开始执行的时候,所有输入的状态都被发送至输入映像寄存器,之后才开始执行用户程序。所有的用户子程序都是通过主程序 OB1 顺序调用执行的,当一个扫描周期完成的时候,所有的结果都被传送至输出映像寄存器用以控制 PLC 实际输出,如此循环往复。PLC 可以接受数控装置发出的控制指令,还可以接受机床测量系统反馈的信号,进而发送控制指令到机床驱动系统进行调整和误差补偿,同时也可以控制继电器、报警指示灯等外围元件[6]。
PLC 接口信号负责 PLC 和数控系统、PLC 和 HMI 之间的信息交换,常规的功能主要包括 MCP( 机床操作面板) 、手轮、急停、主轴进给轴使能、报警排屑等逻辑控制,对于不同功能的机床,根据系统的需要外加一些控制功能。该专机的控制程序如图 9 所示。
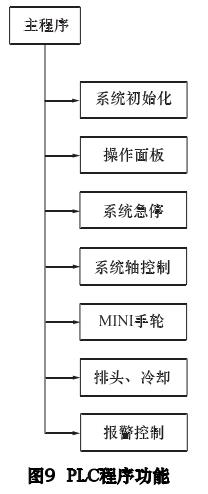
SINUMERIK 828D 集成基于 SIMATIC S7 - 200 的PLC,采用梯形图编程的方式可支持高达 24000 步指令语句,使用“Programming Tool PLC828”进行 PLC 程序的编辑、诊断,其中 OB1 只能用来调用子程序,具体如图 10 所示。
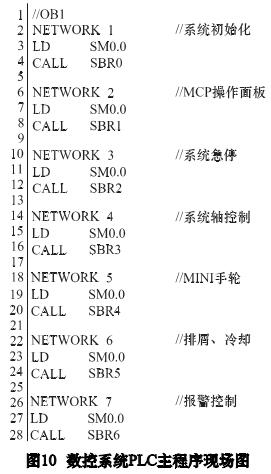
PLC 软件的设计直接影响着数控机床加工的质量。PLC 的编程采用梯形图的方式,具有直观易懂的优势,以快速进给控制功能梯形图为例,如图 11所示。
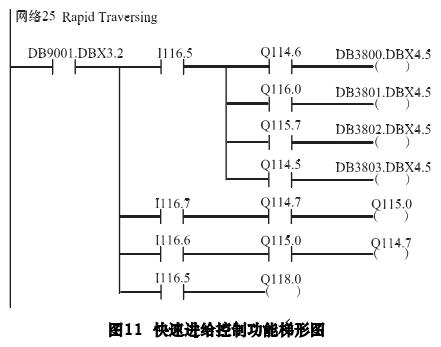
3、 工艺试验
工艺试验是检验该设备是否可以满足加工生产要求的有效途径,工艺试验流程如图 12 所示。
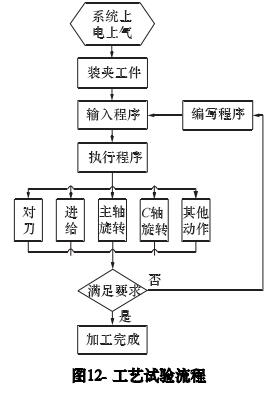
3. 1 数控铣削 G 代码编程
在 Pro /E 制造模块中,设计并生成走刀路径和刀位信息,如图 13 所示。
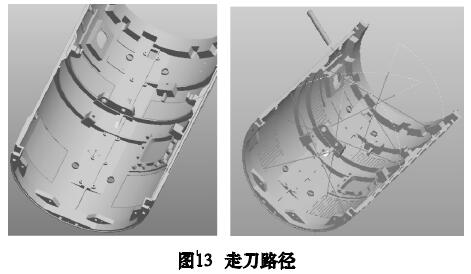
通过设计后置处理系统,编辑并生成 NC 代码。NC 代码分为开端、主体、结尾,程序内容如下:
( 1) 程序开端
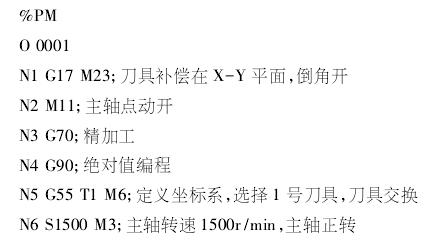
( 2) 程序主体
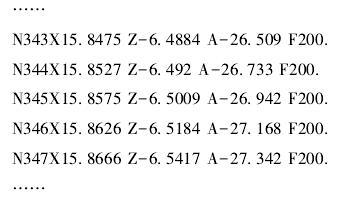
( 3) 程序结尾
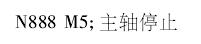
3. 2 工艺应用试验与结果分析
使用 VERICUT 软件进行仿真加工,经过仿真模拟,如图 14 所示,发现了加工干涉的问题,经分析是坐标系设置和 Z 向插补过深等问题引起,对 NC 程序进行改进,解决了加工干涉等问题。
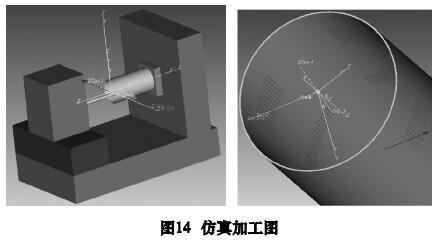
对某型号舱体做数控加工试验,舱体装夹定位后,使用上述编译完善的数控程序进行铣削加工,依据镁铝合金切削手册和舱体内型面加工经验对主轴转速和进给速率的优化进行工艺试验和结果分析,加工现场如图 15 所示。

实际试验中发现数控系统运行时遇到电磁干扰的问题,为此重新设计了电气柜结构,将电气柜的强电弱电分隔开; 初次试验时加工表面粗糙度以及加工效率未达到预期要求,主要是由于程序设定的切削参数以及刀轨路径不够优化等问题引起,为此对后置处理进行优化,使加工质量和效率得到明显提高。经过多次加工试验结果表明: 当主轴转速 S 为 1 500 r/min,X轴进给速率为50mm/min,Y轴进给速率为50 mm / min,Z 轴进给速率为 200 mm / min,该专机满足加工要求; 该数控铣削专机的加工效率相对于手动铣削机床提高了 3 倍; 加工后的舱体内型面精度符合要求,合格率达 100%。
4 、结语
该设备的数控系统经设计和工艺试验验证,系统硬件和软件设计正确,数控加工的程序编制合理可行。通过实际舱体内型面的铣削加工,加工精度和效率能够满足典型舱体内型面结构的加工需求,设备运行稳定可靠,可应用于型号产品批量生产。
投稿箱:
如果您有机床行业、企业相关新闻稿件发表,或进行资讯合作,欢迎联系本网编辑部, 邮箱:skjcsc@vip.sina.com
如果您有机床行业、企业相关新闻稿件发表,或进行资讯合作,欢迎联系本网编辑部, 邮箱:skjcsc@vip.sina.com
更多相关信息