智能制造环境下的数控系统发展趋势
2018-6-28 来源:徐工消防安全装备有限公司 作者:李 云
摘要:阐述未来数控系统的发展趋势,即数控系统向开放型发展,集成CAM软件,方便编程及模拟;与MES系统集成,实现设备间数据互通;注重检测功能,能实时反馈数据。
随着我国《中国制造2025》行动纲领的实施,工程机械各大主机厂商都在进行以智能制造为目标的技术升级改造,建设以创新、绿色、智能为主题,信息化与工业化深度融合的数字化、网络化的智能制造车间,响应智能制造、绿色制造、服务制造的强国战略,数控系统制造企业只有坚持客户导向,满足企业智能化升级改造需求,在数控系统开放性方面深入研究,不断提升系统的网络化、开放化水平,为用户定制个性化的数控系统,才能取得长足的发展。未来先进数控系统将具有以下几方面特点。
1 . 数控系统向开放型发展,集成CAM软件,方便编程及模拟
目前比较常见的FA N U C数控系统,虽然也具有程序检查功能,例如机床锁住和辅助功能锁住功能,能够不移动刀具而显示其位置的变化,能锁住所有轴或指定轴,并禁止执行M、S和T指令(见图1),检查程序是否编制正确,但是这种方法仅能检查出程序语句方面的错误,不能直观显示刀具路线轨迹,不能避免潜在的风险。未来开放的数控系统将在自动编程及仿真方面有所改进。传统的Mastercam、UG等编程软件生成的数控程序,需要经过后处理,才能应用于生产现场,然而软件自带的后处理程序,并不能完全适应用户特殊定制的机床,只有较专业的技术人员才能修改后处理程序,这给生产造成一定的障碍。未来开放式数控系统往往采用N C嵌入P C 的模式,这种数控系统的优点是能够借助已经成熟的计算机Wi n d o w s平台,方便集成各类计算机软件,数控系统内嵌专门的编程及仿真软件,这样就实现了C N C 与软件之间的无缝连接,技术人员无需考虑后处理格式、机床仿真三维模型是否正确的问题,这样就使得操作更加高效准确,借助计算机CAM软件强大的编程仿真功能,用户可以直观地观察刀具轨迹路线,进、退刀方式,切削量等方面的信息(见图2),这样就能更大程度地避免因编程错误造成的生产事故。
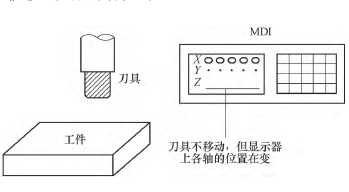
图1 FANUC数控系统机床锁住功能
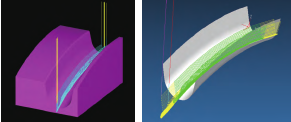
图2 CAM软件刀具轨迹显示界面
2 . 数控系统将更好地与M E S系统集成,实现设备间数据互通
未来规划的智能车间中,生产流程更加简单高效,尽量避免人工干预。订单下达至生产线,设备会读取当前产品的订单号、批次号和ID号,MES系统向生产现场下达生产任务,同时MES向相关设备传输生产开始指令,通过DNC向设备传递NC程序并触发设备加工程序准备,加工完毕后,MES系统会读取设备加工运行数据和标准数据,并从加工质量方面对加工参数进行分析并改进,形成良好的闭环管理,记录设备运行信息,作为产品过程质量信息,为SPC分析基础数据和质量追溯使用,具体流程如图3所示。
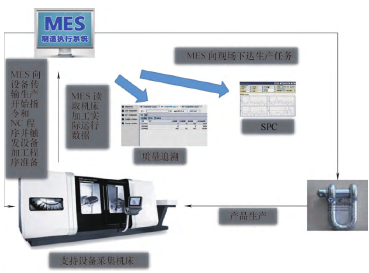
图3 车间智能制造图解
3. 数控系统更加注重检测功能,能实时反馈数据
随着传统机械行业人工成本的增长,智能化工厂的用工人数呈下降趋势,由劳动密集型行业转型成技术集中型行业,一方面对技能工人的要求更高,技能型蓝领人才需求大幅增加;另一方面,对数控系统厂家提出了更高的要求,要求数控系统更加注重检测功能,能实时反馈数据,例如数控系统共享激光跟踪仪测量数据,将激光跟踪仪球坐标数据转化为右手直角坐标系数据,并图2 CAM软件刀具轨迹显示界面图3 车间智能制造图解进行反馈,避免事后检测返工的情况,目前各大机床厂商,例如友佳、日发等机床企业已经注重在机床中配置Renishaw探头、在线对刀仪等设备(见图4),丰富了数控机床的功能,提高了生产效率。另一方面,检测功能还体现在数控程序上,例如江苏一重为日本某企业研制的数控钻床,实现了无人化加工,机械手上料定位,液压夹具夹紧等过程都由程序代码控制,钻孔及攻螺纹过程中,实时监测主轴扭矩,加工过程中如果发生丝锥断裂,主轴扭矩值就会发生变化,系统宏程序会发出报警,提示操作人员更换丝锥,体现了数控系统的检测功能在智能制造中的重要作用。
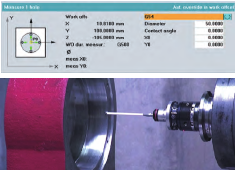
图4 Renishaw测量系统
4. 结语
随着《中国制造2025》制造强国战略的实施,企业只有提高制造过程的智能水平,才能保证产品质量,降低人工成本。为满足客户需求,数控系统厂商只有不断丰富系统功能,在编程仿真、数据互通及实施检测等方面深入研究,为用户量身定制个性化的数控系统,才能取得长足的发展。
投稿箱:
如果您有机床行业、企业相关新闻稿件发表,或进行资讯合作,欢迎联系本网编辑部, 邮箱:skjcsc@vip.sina.com
如果您有机床行业、企业相关新闻稿件发表,或进行资讯合作,欢迎联系本网编辑部, 邮箱:skjcsc@vip.sina.com
更多相关信息