数控火焰切割系统 Z 轴高度补偿功能的实现
2018-6-11 来源:武汉工程大学材料科学与工程学院 作者: 马凡杰,王学华,王华龙,李安翼,刘 苏
摘要:采用工业计算机和运动控制卡等硬件构建开放式数控火焰切割系统,以 Visual Basic 6.0 为开发工具,开发了提高异形工件火焰切割过程平稳性的系统控制软件. 采用激光位移传感器对被加工件进行非接触式扫描,获取工件在加工路径上的高度信息,并以此为依据进行切割轨迹的规划和高度补偿. 试运行结果表明,当工件表面高度发生变化时,由伺服系统进行三轴直线插补或三轴螺旋插补,能够在切割过程中使割炬与工件表面之间的距离始终保持一致,位置精度±0.02 mm,重复定位精度±0.05 mm. 整个系统保证了良好的切割质量,达到了切割过程平稳高效的目的。
关键词:火焰切割;数控系统;Z 轴补偿;异形件切割
1、 引言
数控火焰切割机是一种利用燃气的热能对金属板材进行切割加工并利用数控装置控制机床的切割轨迹的特种加工设备. 因具有切割质量高、割面垂直度好、切割厚度大以及成本低廉等优点,成为机械、压力容器、造船、车辆、金属结构等行业的重要装备。目前主流数控火焰切割设备都是以平面切割控制系统为主. 当工件存在高低不平、倾斜、弯曲、凸瘤、深坑等特征时,传统的控制方式会影响切割质量和平稳性. 因此,在切割过程中采用合适的控制方式保持割炬与被切割工件之间的距离恒定对完成平稳切割加工有重要意义. 王春、宋凯云等人研究的电容式自动调高系统是目前解决此类问题的主要手段,其中蒋翔俊等人设计了基于模糊控制方法的自动调高控制系统,使电容式自动调高系统工作过程有了更好的稳定性和精度. 黄金花等人引入结构和参数自适应思想对标准遗传算法进行了改进,利用爬山法对 PID 调节器进行最佳参数辨识,使电容式自动调高系统的动态性能有了大幅提高,精度和鲁棒性好. 但是当工件在厚度方向上发生有一定程度的翘曲时,安装有电容式自动调高系统的火焰切割机的切割效果并不理想,而且由于电容的性能受到温度、湿度以及寄生电容的影响,设备对温度、湿度、屏蔽和接地均有一定要求.本文采用环境适应性更强的激光位移传感器作为 Z 轴高度补偿的数据来源,采用 Visual Basic6.0 开发了数控火焰切割系统的图形处理和运动控制软件。
通过激光位移传感器获取被割工件高度信息,并根据被加工对象的轮廓进行空间切割轨迹规划,实时自动沿 Z 轴方向的高度补偿,实现了切割过程的稳定控制.
2 、系统结构
根据数控火焰切割机的加工工艺要求和工作环境恶劣的特点,采用工控机+运动控制卡为控制单元构建 NC 嵌入 PC 的开放式数控系统. 主要硬件有 IPC510 型工业控制计算机、PCI-1245 型运动控制卡、8622 型多功能数据采集卡、CD33-250NA型激光位移传感器、伺服系统等. 采用这种控制方式,不仅结构简单,而且系统有良好的稳定性和拓展性. 系统的硬件结构示意图如图 1 所示.
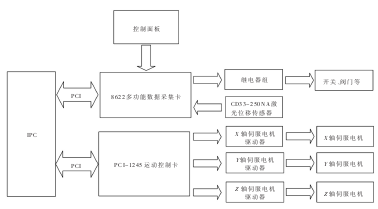
图 1 系统硬件结构示意图
工业计算机(IPC)作为数控火焰切割系统的上位机,运行所开发的数控火焰切割系统上位机控制软件,通过调用系统资源,驱动机床完成切割加工,同时 IPC 还作为系统的人机界面,具有设置系统工作参数、显示运行状态、跟踪切割轨迹等功能. 激光位移传感器输出的模拟量信号传送至多功能数据采集卡,经过 A/D 转换后,数控火焰切割系统即可得到工件在切割方向上的轮廓高度,作为 Z 轴自动补偿的数据来源. PCI-1245 作为 4 轴通用 PCI 步进/脉冲型伺服电机控制卡,用于驱动伺服系统进行 XYZ 三轴直线插补或三轴螺旋插补,实现预定轨迹的运动控制功能.
3 、Z 轴高度补偿功能
3.1 加工路径的预处理
在对工件进行加工之前,数控系统需要先获取切割路径中工件表面的轮廓高度,为后续加工过程中控制割炬沿 Z 轴方向进行高度补偿提供数据源. 因此,CD33-250NA 激光位移传感器需要固定在机床的 Z 轴上,采用垂直于 XY 平面的方式进行安装. 加工路径预处理流程见图 2.

图2 加工路径预处理流程图
首先系统根据输入的几何图形,获取图形中的要素,生成 XY 平面的运动路径,伺服系统沿上述路径进行插补运动,同时开启 Z 轴激光位移传感器的连续检测. 系统可以获取工件在切割路径中沿高度方向的轮廓信息,并将其离散化,变为一系列的空间点坐标. 但其中大部分为冗余信息,需要从中提取出关键的刀位点坐标(x,y,z). 当工件表面存在高度变化时,X 轴和 Y 轴沿运动路径插补过程中,系统将当前位置的 Z 坐标与链表中上一个结点里所存储的刀位点的 Z 坐标进行比较,当两者差值不在割炬的有效范围内时,则向链表中添加一个新结点,记录当前刀位点的 X、Y 坐标,以及同步的 Z 轴坐标.
图形路径的生成过程代码如下:
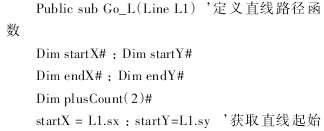
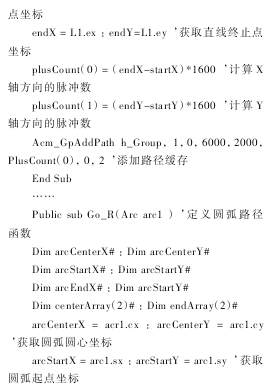
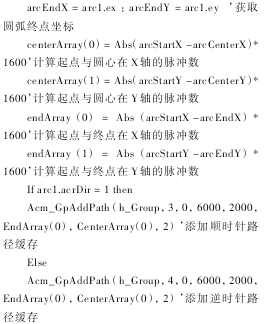
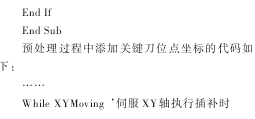
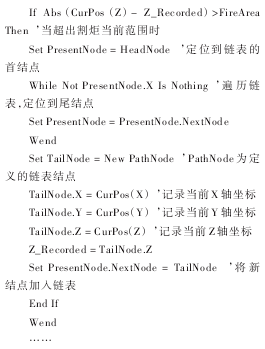
此外,链表中还需要加入直线的起止点、终止点,圆弧的起始点、终止点、圆心等图形要素的坐标,使链表中包含完整的加工路径信息.
3.2 Z 轴高度补偿
通过对加工路径的预处理,完成对链表中路径结点信息的添加后,在加工过程中,数控火焰切割系统通过读取链表结点中存储的关键刀位点的坐标,即可控制伺服系统沿 Z 轴方向进行高度补偿,与 X 轴、Y 轴实现三轴联动,沿空间轨迹进行插补,完成工件切割过程. 以 PCI-1245 运动控制卡为接口,实现数控系统的 XY 轴直线插补与割炬沿 Z轴方向实时进行高度补偿的代码如下:
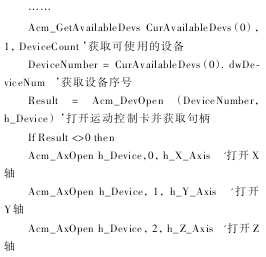
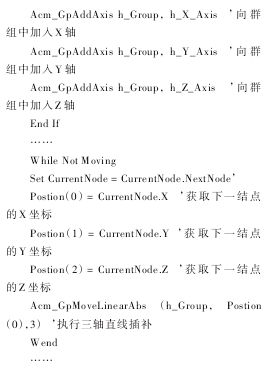
当 XY 轴进行圆弧插补时 ,可以通过调用PCI-1245 运动控制卡中提供的三轴螺旋插补函数Acm_Gp Move Helix Abs,控制伺服系统执行螺旋插补,实现圆弧切割过程中 Z 轴方向的高度补偿. 由于任意的平面几何图形均可离散为直线和圆弧,因此,通过三轴直线插补和三轴螺旋插补可以实现任何复杂几何图形的切割.
4 、加工实例
以图 3(a)所示的弧形零件切割过程为例,根据输入的图形文件进行平面投影得到在 XY 平面上的轮廓[图 3(b)]为加工路径的数据来源,由激光位移传感器采集工件在参考平面高度(设为 50mm)上的数据,作为高度调整的数据来源.
首先,在上位机中输入零件的几何图形,投影得到如图 3(b)所示的轮廓. 根据加工工艺要求,在零件的轮廓上选定切割起点,并以切割起点为终点,确定方向和长度,绘制切割引入线和点火点.本例中选取的切割起点为 A,OA 段为切割引入线,O 点为点火点.
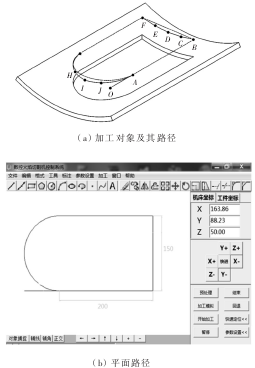
图3 加工轨迹生成实例
数控系统根据输入的零件的几何图形,控制伺服系统的 XY 轴按如图 3(a)所示 O→A→BF→→A→O 的顺序执行高速插补. 其中 GA 段为圆弧插补,其余均为直线插补. 在此过程中,系统根据输入的几何图形的要素以及激光位移传感器的采集数据,将 O 点、A 点、B 点、C 点、D 点、E 点、F 点、G点、H 点、I 点作为关键刀位点,将其坐标存入加工路径链表中. 当伺服系统按照 500 mm/min 的速度执行切割时,预处理前后数控系统的理论坐标和实际运动轨迹坐标见表 1,可以看出当工件高度发生变化时,关键刀位点的坐标被成功加入到加工路径数据链表.
在完成对链表中结点的添加后,火焰切割数控系统控制割炬下降到指定高度位置,并在 O 点位置进行点火,对工件表面进行预热后,伺服系统按正常的切割速度,沿空间切割轨迹执行插补. 首先,伺服系统沿切割引线 OA 段进行插补,到达零件切割起点 A 处,随后沿 AB 段进行插补. 在此过程中,由于 OA、AB 所在位置的零件表面高度一致,因此割炬此时无需进行高度补偿. 随后,系统通过BC、CD、DE、EF 四段连续的三轴直线插补,逼近工件的表面轮廓,实现 Z 轴方向的高度补偿和零件的切割。FG 段的插补与 AB 段类似. 最后,伺服系统通过 GH、HI、IJ、JA 四段连续的三轴螺旋插补,完成圆弧形工件的切割. 在切割过程中通过伺服编码器获取运动位置坐标,见表 1 的实际运动坐标,可见运动精度较高,位置精度均在±0.02 mm 以内,与激光位移传感器的测量精度一致.
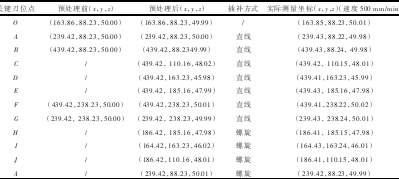
表 1 特征点坐标与实际运动结果
5 、结语
针对实际生产的需要,开发的开放式数控火焰切割系统实现了对于 Z 轴方向的高度补偿功能,试运行结果表明该系统具有良好的稳定性和较高的运动精度,其位置精度±0.02 mm,重复定位精度达到±0.05 mm. 该系统在工件表面存在翘曲、凹陷、凸瘤、深坑等特征的情况下,依然能够进行有效地切割,并保证良好的切割质量,扩大了火焰切割系统的应用范围,同时有效地弥补了现有数控火焰切割系统不能很好完成异形工件加工的不足.
投稿箱:
如果您有机床行业、企业相关新闻稿件发表,或进行资讯合作,欢迎联系本网编辑部, 邮箱:skjcsc@vip.sina.com
如果您有机床行业、企业相关新闻稿件发表,或进行资讯合作,欢迎联系本网编辑部, 邮箱:skjcsc@vip.sina.com