基于三菱 PLC 的双面铣床控制系统程序设计
2017-5-4 来源:江苏商贸职业学院 作者:王亚东
摘要:采用三菱 PLC 对双面铣床进行技术改造,针对双面铣床的控制要求,给出两种程序设计方案,并简单分析了各自的优缺点,PLC 的应用不但大大提高了系统运行的可靠性和抗干扰能力,降低了设计运行的故障率,同时给设计维护带来极大的便利,对同类设备的技术改造有较大的参考价值。
关键词:PLC;铣床;工作方式;IST
PLC 的全称是 Programmable Logic Controller(可编程控制器),刚引入国内时,曾简称为 PC。后来,IBM-PC 获得广泛应用,PC 成了个人电脑的代名词,才改为 PLC。PLC 是一种智能产品,是在电器控制技术和计算机技术的基础上开发出来的,并逐渐发展成为以微处理器为核心,把自动化技术、计算机技术、通信技术融为一体的新型工业控制装置。目的是用来取代继电器、执行逻辑、记时、计数等顺序控制功能,建立柔性的程控系统。国际电工委员会(IEC)于 1987年颁布了可编程控制器标准草案第三稿,明确强调了 PLC 直接应用于工业环境,具有通用性强、使用方便、适应面广、可靠性高、搞干扰能力强,编程简单等特点。在工业领域中,PLC 控制技术的应用已成为世界潮流。
在传统的机床控制系统中,都是采用继电器——接触器等元器件组成的硬件逻辑控制电路,在 PLC 出现之前,一直占主导地位,应用广泛。但是电气控制系统存在体积大、可靠性低、查找和排除故障困难等缺点,特别是其接线复杂,工艺难度高,不易更改,对生产工艺变化的适应性也差,所以用 PLC 控制取代传统机床电气控制系统是机床控制发展的主要趋势。它可以完美的解决传统机床电气控制系统的可靠性、柔性、开发周期、故障自诊断等问题。
铣床作为机械加工的通用设备,在汽车等配件生产加工中起着不可替代的作用。而双面铣床由于两面可同时加工,加工效率高,应用更为广泛,本文主要进行双面铣床的 PLC 控制程序设计。
1.双面铣床控制系统控制要求。
工作台来回往返运动由液压驱动,工作台速度和方向由限位开关SQ1—SQ3 控制。工作台与主轴循环工作过程为:工作台启动——向右快进(左动力头)——减速工进,同时主轴启动,加工结束——停止工进,主轴延时 10S 停转——工作台向左快退回原位——进入下一循环工作状态。右动力头的运行方向与左动力头相反。
控制要求:PLC 设计时,工作方式设为自动循环、点动、单周循环和步进 4 种;主轴只在自动循环和单周循环时启动;要有必要的电气保护和联锁装置;自动循环时按下图的顺序动作。
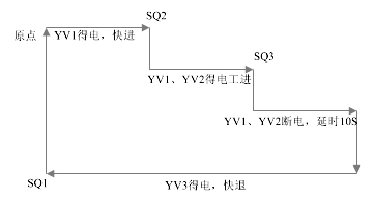
图 1 双面铣床动力头的动作顺序
2.PLC 设计设计
2.1 采用 IST 指令实现程序设计
根据控制系统要求,该程序主要需包括四种工作方式,分别为自动循环、点动、单周循环和步进,最为简便的编程方法是使用功能指令的初始化指令 IST(FNC60)。
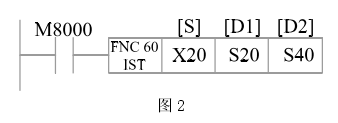
梯形图源操作数 S 表明的是首地址,它有共 8 个位连号软元件元件组成,由开关量输入继电器 X20~X27 组成,其功能分别是:
X20:手动工作方式的输入控制信号;X21:返回原点工作方式的输入控制信号;X22:单步工作方式的输入信号;X23:单周期工作方式的输入控制信号;X24:全自动工作方式的输入控制信号;X25:返回原点的启动信号;X26:进入自动工作方式的启动信号;X27:停止。在开关量输入 X20~X24 中,不允许有两个或两个以上的输入端同时闭合,因此,必须选用满足该条件的转换开关,且该开关至少有五挡位置,当开关扳到某挡位置时,只有该位置的触点闭合,其他各位置的触点断开。在梯形图中,目的操作数 D1 和 D2 只能选用状态器 S,其范围是 S20~S899,其中 D1 表示自动工作方式所使用的最低位状态器,D2 表示自动工作方式时所使用的最高位状态器。S0~S9 是实际发始状态器地址编号。S0 是各操作的初始状态,S1 是原点回归的初始状态。
同时, 与IST指令有关的特殊辅助继电器有 8 个。 它 们 是M8040~M8047,其中 M8040:转移禁止;M8040:转移开始;M8042:起动脉冲;M8043:返回原点完成,当 M8043 为 1 时,允许进入自动工作方式,当 M8043 为 0 时,表示返回原点未完成,不允许进入自动工作方式;M8047:STL 监控有效。
因此,如果采用 IST 指令设计该双面铣床控制程序时,可将程序设计成四部分,第一部分 IST 指令;第二部分为手动程序,设计在状态点 S0 下;第三部分为返回原点程序,设计在状态点 S1 下,且在该部分程序最后,到达原点时对 M8043 置 1,表示返回原点完成;第四部分为自动和单周程序,设计在状态点 S2 下。若 X20 为 ON 时,状态器 S0 为 1,表示工作在手动工作状态;若 X21 为 ON 时,状态 S1为 1,处于返回工作原点状态,当返回工作原点完成时,M8043 置 1,,此时如果 X22 为 ON,则工作于单步工作状态即步进状态,每按一次启动按钮,就进行一次状态转移,如果输入端 X23 为 ON,则处于单周期工作状态,每按一次启动按钮,扫行完一个周期后,停止在起始状态 S2;如果输入端 X24 为 1 时,则处于自动工作方式,循环执行用户程序。由此可见,该程序完全满足该双面铣床控制系统的四种工作方式。但是我们同时也可以发现,一旦采用 IST 指令,其输入端一次性占用 X20~X27 共 8 个输入点,对于三菱 FX2N-32MR 的 PLC 来说,有可能输入点是不够用的,并且它必须采用至少有五档的转换开关,那我们可不可以不采用 IST 指令同样也可以实现控制要求呢?
2.2 采用基本指令实现程序设计
2.2.1 程序的总体结构
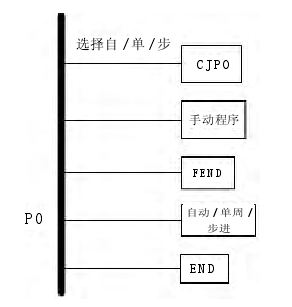
图 3 双面铣床控制系统 PLC 梯形图总体结构
图 3 为双面铣床的 PLC 梯形图程序的总体结构,将程序分为公用程序、手动程序和自动程序三个部分,其中自动程序包括单步、单周期、自动循环和自动回原点四部分。这是因为它们的工作都是按照同样的顺序进行,所以将它们合在一起编程更加简单。回原点程序放在自动程序的初始状态点 S0 中,因为自动循环等工作方式起点就要求动工作台处于原点位置,梯形图中使用跳转指令使得自动程序和手动程序不会同时执行。
2.2.2 各部分程序的设计
(1)公用程序。公用程序如图 4 所示,用于自动程序和手动程序相互切换的处理。当选择自动 X7、单周 X10、步进 X11 这三种工作方式时,程序跳转至 P0 执行自动程序,反之若选择的是手动
X12,则执行手动程序。当执行手动程序时,首先将状态点 S0~S13复位,同时将输出 Y0~Y4 复位,再进行手动工作方式,必免同时有两个活动步的异常情况,同时为避免手动工作时的越程故障,可在左动力头和右动力头输出上分别加上 SQ3 和 SQ1 的常闭触点,进行位置限制。
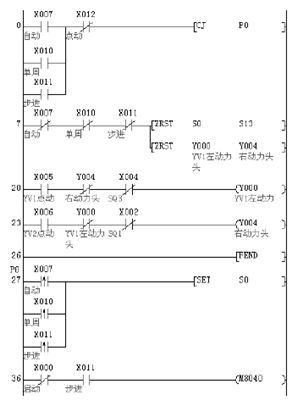
图4 公用程序
自动程序初始状态点 S0 的激活,由自动 X7、单周 X10、步进X11 三个输入的并联进行触发,并采用边沿触发,如果采用普通触发,当以上三个输入开关闭合时,会出现初始状态点 S0 一直处于激活状态,当自动程序开始执行时,会同时出现两个活动步的异常情况,而采用上升沿触发,只有当开关合上一瞬间,初始状态点 S0 才会被激活,当下一个状态点满足条件激活时,S0 状态点关闭。
步进工作状态依靠特殊辅助继电器 M8040 来实现,由启动按钮X0 的常闭触点和步进工作状态选择开关 S11 的常开状态驱动特殊辅助继电器 M8040。当步进选择开关 S11 闭合,没有按下启动按钮X0 时,M8040 为 1,禁止状态转移,按下启动按钮 X0 时,常闭触点断开,M8040 为 0,允许状态转移,即跳转至下一个状态点,执行下一步动作,由此,每按一次,自动程序执行一步,即实现了步进控制。
(2)自动程序。自动程序功能图如图 5 所示,其中包含单周、自动循环以及自动回原点程序。其中单同和自动循环通过状态点 S13下的跳转实现,当选择单周或步进时,程序跳转至状态点 S0,当选择自动或步进时,程序跳转至状态点 S10。自动回原点程序设计在初始状态点 S0 下。当返回原点后,即到达行程开关 SQ1 位置,给出原点信号 Y5,作为下一个状态 S10 激活的条件之一。同时需注意的是,因为步进工作方式与自动程序是合在一起编程的,当程序工作在单周或自动时,满足下一个状态点激活条件时,则跳转至下一个状态点执行,而工作在步进工作状态时,尽管满足了下一个状态点激活条件,但没有按下启动按钮,程序不会执行下一个状态点的动作,即当前状态点一直处于激活状态,当前状态点也一直有输出,为了避免这种情况的出现,在每个状态点的输出元件上,加上条件限制,当满足跳转条件时,尽管没有跳转,当前状态点也无输出。如在状态点 S10 的输出元件前串上 SQ2 的常闭触点。
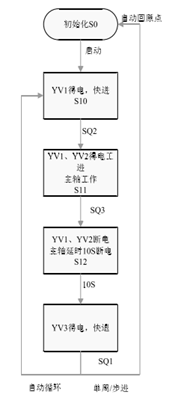
图5 自动程序的功能表图
(3)程序调试。程序调试时,可各部分程序分别调试,然后再进行全部程序的调试,也可直接进行全部程序的调试。
3.总结
本文介绍的在双面铣床控制系统中应用 PLC 替代继电器—接触器电气控制线路的技术改造,经过实际运行,系统运行稳定可靠,能很好的保证其加工精度和定位精度,两个编程方法各有优缺点,采用IST 指令,编程方法简单,程序结构清晰,但在工作方式的选择开关上一定要采用五档转换开关来实现,采用普通指令,编程较为复杂但开关无特殊要求。总之,PLC 的应用不但大大提高了系统运行的可靠性和抗干扰能力,降低了设计运行的故障率,同时给设计维护带来极大的便利,对同类设备的技术改造有较大的参考价值。
投稿箱:
如果您有机床行业、企业相关新闻稿件发表,或进行资讯合作,欢迎联系本网编辑部, 邮箱:skjcsc@vip.sina.com
如果您有机床行业、企业相关新闻稿件发表,或进行资讯合作,欢迎联系本网编辑部, 邮箱:skjcsc@vip.sina.com
更多相关信息