基于转盘镗孔仿真的正交实验参数研究
2017-4-26 来源:鹤壁汽车工程职业学院 作者:赵帅,毕雅萱
摘要:文章利用 DEFORM-3D 有限元软件建立了转盘镗孔的三维仿真模型,根据转盘零件在不同切削参数条件下模拟出不同的切削力、形变量的数值,并通过设立正交实验得到最优化的切削工艺参数:切削速度 v = 120 m / min,进给量 vf = 0. 02 mm / r,切削深度 vp = 0. 03 mm。 最后,经三坐标测量机测得试验零件各孔误差均在合理范围内,该方法为以后零件在选择切削参数方面起到了一定的借鉴作用。
关键词:DEFORM-3D;切削参数;正交实验
0.引言
目前,我国制笔行业产销量在世界范围内遥遥领先,产品出口遍及全球,但我国用于中高端制笔设备却依赖瑞士和德国的进口。 据统计,国内现已累计进口原装瑞士米克朗 24 工位笔头机 250 余台;同时,订购后需 14 个月才能提货,使我国笔类产品的生产严重受制于国外发达公司。
在笔头制造技术方面,高精度的圆柱笔头广泛采用多工位机床来加工,加工精度要求达到 ± 0. 5 μm。我国从上世纪九十年代就开始引进瑞士的 24 工位笔头加工机床,由上海七〇四研究所立项研制,由于国外技术封锁,缺少相关资料,虽已出样机,但其加工效果待进一步提高。 2001 年,以丰华股份公司为首、轻工机械研究所、七〇八研究所共同立项再次研发类似的设备,由于机床上关键部件加工未达到要求,总体装配后加工精度不理想,不能大批量工业化推广。 因此,研发高精度多工位笔头加工机床对我国制笔行业和制造装备业具有重要意义。
1.结构特点分析
高精度多工位笔头加工机床的核心部件包括转动圆盘、上下动力头座,俗称“三明治” 机构。 如图 1 所示,转动圆盘是机床的分度回转工作台,台面上安装有夹具和工件;上下动力头座分别位于转动圆盘的上下两侧,起到支撑动力头的作用。 如图 2 所示,转盘零件属于精密多孔类结构件,台面上孔的加工量占整个零件加工量的一半以上,外沿孔径的尺寸精度要求在 ± 5μm,圆度精度要求在 8μm。 因此,转盘孔的加工质量要求格外严格,其制造精度的好坏直接影响到整机的性能,现以转盘镗孔加工为例进行研究。
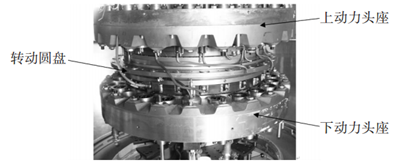
图 1 “三明治”机构图
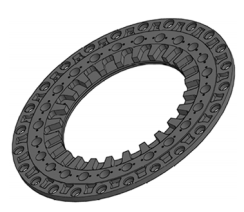
图 2 转盘零件结构图
Deform-3D 是一套基于工艺模拟系统的有限元系统,专门设计用于分析各种金属成形过程中的三维流动,在一个集成环境内综合建模、成形、热传导和成形设备特性进行模拟仿真分析。 与传统的试错法相比,利用软件仿真可使过程分析形象化和可视化,费用低、耗时短,节省人力物力,在考虑多因素时其优势尤为显著。因此,本文利用 Deform-3D 有限元软件对转盘孔的切削过程进行仿真模拟,根据不同切削参数条件,模拟出不同的切削力、形变量数值,并将这些数值通过正交实验得出最优化切削参数组合。
2.建立 Deform-3D 仿真平台
2. 1 建立有限元模型
由于 Deform-3D 分析软件不具备三维造型功能,所以本文选择在 Solidworks 软件中建立模型。 在 Solidworks 中建立的镗刀装配模型,如图 3 所示,其中镗刀前角 γ0 =8°,后角 α0 =10°,刀尖圆弧半径 rε =0. 2mm。 模型文档另存为 STL 文件格式,并在选项中选择“在单一文件”保存装配体的所有零件。 进入 Deform-3D 软件中 Machining 模块后,导入预先构造的刀具模型,刀具材料选择硬质合金WC。 设定工件尺寸,材料选用 QT700-2。
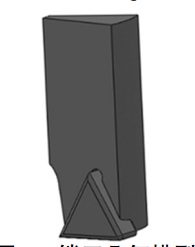
图 3 镗刀几何模型
2. 2 模型的网格划分
划分网格时首先要考虑网格数量,数量越多划分的越细密,分析精度越高,但计算规模也将成倍增加。具体到镗孔加工过程中,刀具切削部分应该实现网格细分,其他部分网格应该加粗,这样既保证了局部变形的求解精度,又节省了求解时间和内存消耗。 在本实验中,刀具网格类型为相对网格类型,其单元总数为15000 个,Size Radio 为 4,工件网格类型为绝对网格类型,网格最小尺寸为 0. 01mm,其单元总数为 26357 个。
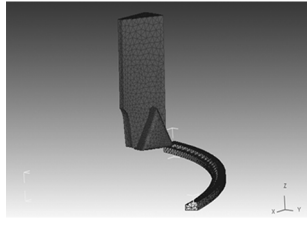
图 4 三维模型的网络划分
2. 3 模拟参数设置
模拟过程中,模拟计算步长的确定是十分重要的。对于几何形状简单,边角无流变或其它局部严重变形的问题,步长可选用模型中较小单元边长的三分之一。 本实验设置仿真总步数为 5000,步数增量设为 25,切削终止角度65°。 刀具磨损模型选用适合于金属切削的 Usui’s 模型,系数 a 为 0. 0000001,b 为 855。 最后检查仿真的各项参数设置是否正确,生成数据库,开始运行仿真。
3.镗孔切削的正交实验仿真
正交实验是研究多因素、多水平实验的主要方法,它是根据正交性原则从所有实验点中挑选部分有代表性的点进行实验,从中寻找出一组最佳的水平组合。3. 1 实验方案设计
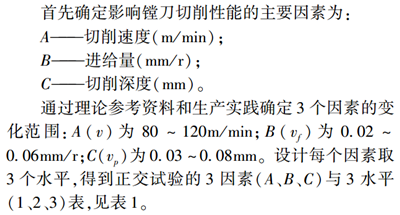
表 1 因素水平表
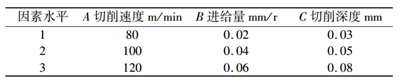
3. 2 实验结果与分析
切削参数因素水平表设计完成之后,基于已有刀具和工件有限元模型进行表 2 中的切削正交试验,实验评价指标为切削力和转盘形变量,并按照各组实验顺序记录实验结果,对结果进行整理计算。在正交实验表 2 中,各个参数下评价指标的均值如表 3、表 4 所示。 其中,K1 代表“水平 1” 的指标均值;K2 代表“水平 2”的指标均值;K3 代表“水平 3”的指标均值;极差 R 代表不同水平时各因素评价指标均值的极差,其大小代表了该因素的水平变化时评价指标的变化幅度。 极差越大说明该因素的水平变化对评价指标的影响越大,因素则据主要地位;反之则说明因素居次要地位。
表 2 转盘镗孔切削正交试验
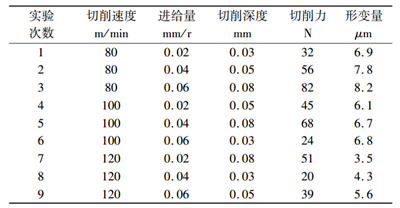
表 3 基于主切削力 FZ 的评价指标和极差分析
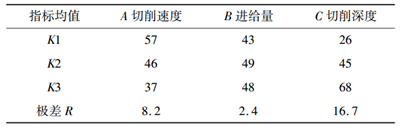
表 4 基于转盘形变量的评价指标和极差分析
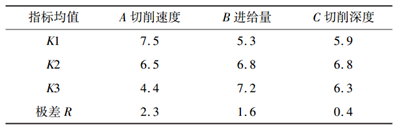
由表 3 中各因素的极差可以看到,基于主切削力FZ 的极差由大到小的排列为:C、A、B;即,对评价指标影响程度由大到小的因素分别为:切削深度、切削速度、进给量。 基于主切削力 FZ 最小作为优化目的,正交试验方案的较优组合为 A3B2C1,即切削速度 v = 120mm / min,进给量 vf = 0. 04mm / r,切削深度 vp = 0. 03mm。由表 4 中各因素的极差可以看到,基于转盘形变量的极差由大到小的排列为:A、B、C;即,对评价指标影响程度由大到小的因素分别为:切削速度、进给量、切削深度。 基于转盘形变量最小作为优化目的,正交试验方案的较优组合为 A3B1C3,即切削速度 v = 120mm / min,进给量 vf = 0. 04mm / r,切削深度 vp = 0. 03mm。
在精密镗孔切削时,工件受切削力影响会产生很强的塑性变形应力场和温度场,从而导致工件发生形变。因此,以切削力和形变量作为评价指标来衡量切削参数优劣时,切削力比形变量更具有参考价值。 因此,综合从切削力和形变量两方面考虑,并结合实际生产经验,正交试验的最优组合为 A3B1C1,即切削速度v = 120m /min,进给量 vf = 0. 02mm / r,切削深度 vp = 0. 03mm。
4.试验验证
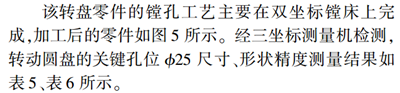
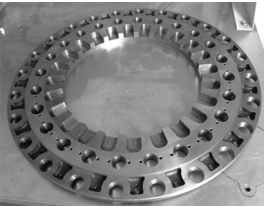
图 5 转盘实物图
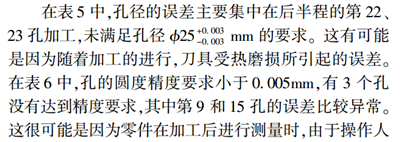
员、测量机、主客观(温度、接触力)等偶然因素直接影响了测量结果,因此应排除这两个孔的误差。
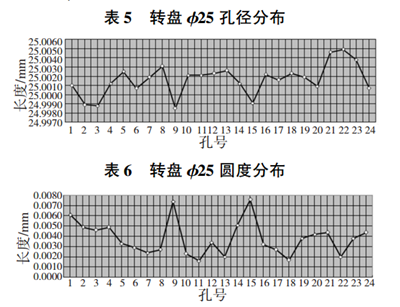
5.总结
本文基于 Deform-3D 建立了镗孔过程中的三维有限元模型,根据不同切削参数模拟获得了一系列的切削力、应变数值,并利用正交实验得出了最优切削参数组合,最后对转盘零件进行实际加工,结果也进一步验证了切削参数的合理性。 与传统加工方法相比,这种方法节省了工艺试验材料和费用,缩短了产品开发周期,为今后类似精密零件的切削加工提供了一定的借鉴。
投稿箱:
如果您有机床行业、企业相关新闻稿件发表,或进行资讯合作,欢迎联系本网编辑部, 邮箱:skjcsc@vip.sina.com
如果您有机床行业、企业相关新闻稿件发表,或进行资讯合作,欢迎联系本网编辑部, 邮箱:skjcsc@vip.sina.com
更多相关信息