机床滑座变形问题的分析与研究
2025-4-15 来源: 沈阳机床股份有限公司 作者:王云萍 刘东波
【摘要】: 滑座作为机床结构中的主要部件直接影响整机的几何精度与运动精度。分析影响机床滑座变形的因素,研究相应的解决方案并进行实验论证。从而对保证机床的加工精度,提升加工性能有着重大影响。
十字滑台式结构作为典型的机床结构形式,在立式加工中心、卧式铣镗床、卧式加工中心等机床型谱中被广泛采用。滑座是十字滑台式结构中的重要组成部件。以立式加工中心为例 : 滑座向上连接工作台,向下连接床身,且负责两个轴的运动,在整机结构中起到承上启下及传动枢纽的作用。所以,滑座的自身精度直接影响机床的几何精度和运动精度。但是,由于滑座自身结构所限,在实际的生产活动中容易产生变形。本文将尝试从结构设计、毛坯铸造、切削加工、装配工艺等整个生产链条分析滑座变形的原因,研究相应的解决方案并通过实验来印证方案效果。
1. 结构设计因素引起的滑座变形
滑座由于不合理的结构设计导致的变形,主要是由于研发设计过程中未能充分考虑结构刚度问题,包括几点 : ①两侧导轨悬伸量过长 ; ②设计内部筋格布局未能兼顾重要受力位置 ; ③滑座内部开口结构。
前两点问题在于研发人员设计经验不足、考虑不周。滑座两侧导轨悬伸量过长时可以加装副导轨或牵拉装置解决工件刚度不足导致变形的问题。另外,当设计内部筋格布局时不必拘泥于对称原则或是刻意追求质心位置。虽然质心驱动设计的十字滑台结构具有较好的对称性,能够减轻机床在切削时的自激振现象,提高机床整机的固有频率。但应优先保证诸如导轨面、滑块面、电机座面、轴承座面等主要受力位置的结构刚度,可以结合有限元分析软件进行拓补优化合理布局。
然而,许多技术人员往往忽略第三点 : 滑座内部开口结构也是影响工件整体刚度的重要因素。如图 1、图 2 所示某型立式加工中心滑座 :轴承座一侧设计成闭合结构、相反电机座一侧则为开口结构。经 AnsysWorkbench 静力学分析,当仅施加额定载荷时,电机座一侧相较于轴承座一侧变形量大0.005mm;当施加极限重载及冲击载荷时,开口结构的电机座一侧变形量成倍放大。因此在设计过程中应尽量避免滑座内部的开口结构。
2.毛坯铸造环节滑座变形分析
毛坯铸造环节有以下几个误区容易引起滑座变形 : ①毛坯尺寸公差等级过大,特别是需要机械加工面的余量。②一味提高铸件牌号,错误地意图通过提高工件机械强度来提高刚性。下文将具体分析这两点如何影响滑座变形。
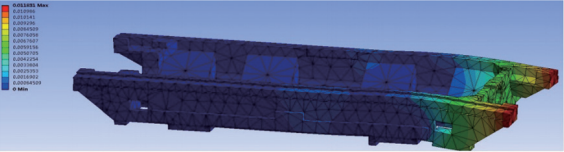
图 1 轴承座侧静力学模型图
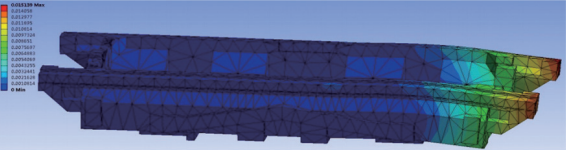
图 2 电机座侧静力学模型图
关于毛坯机械加工余量,可根据 GB/T6414-1999《铸件尺寸公差与机械加工余量》国标查询确定。然而实际生产活动中,铸造厂家往往将机械加工余量等级放至 H~K 级别(以 2000mm 内的滑座为例,加工余量可达 6~15mm)。究其原因无外乎以下两点 : ①铸件以重量结算价格,厂家追求利润有意放大加工余量。②铸造缺陷大多出现在毛坯表层,放大余量,并经过加工后可降低废品率。
过大的毛坯余量势必增大后续切削加工环节的金属去除量,累积更大切削残余应力,从而加剧滑座变形。与此同时过多无用的毛坯余量也会提高物料成本及机加工费用。因此必须降低毛坯余量。经实际检验 : 机械加工余量等级确定至E~G 级别较为合适,即长度在 2000mm 以内的滑座理想的加工余量为 3~5mm。
关于铸件牌号问题,设计时机床大件通常选用HT200或HT250。然而部分技术人员一味提高铸件牌号至 HT300~HT350,将机械强度与结构刚度混为一谈,单纯地认为提高机械强度能够减小工件变形,殊不知滑座变形主要是工件的整体弹性变形及加工面在切削过程中热力耦合作用下的微观变形,很少能到达到整体塑性变形阶段。刚度是主要因素,而刚度是结构性质,与材料的弹性模量及工件的结构有关。另外由于铸件抗拉强度与硬度存在一定的对应关系式 :
当σb≥196MPa时,HB=RH(100+O.438σb )(1)当σb<196MPa时,HB=RH(44+0.724σb )(2)式中相对硬度 (RH) 值主要由原材料、熔化工艺、热处理工艺及铸件的冷却速度所确定。如式中所述 : 提高铸件强度同时势必会增加硬度,反而增大铸造应力及加工环节的切削阻力导致滑座变形,因此如无特殊原因不宜提高铸件牌号。
3.切削加工过程中变形因素分析
滑座在切削加工过程中产生的变形主要包括 : ①产前准备期间不规范的定位、卡压产生的变形。②加工过程中热力耦合作用产生的导致工件微观相变或变形。③工艺编排不合理造成应力累积变形。
机加工产前准备期间工件不合理的定位、卡压容易导致滑座变形。首先工件定位位置与卡压位置应尽量保持在一条线上。简单举例 : 如图 3所示某型滑座底面加工示意图,其定位位置与卡压位置不在一条线且该卡压方式没有在四周加侧顶装置,夹紧时仅靠摩擦力限制自由度,故需较大的压紧力。经有限元分析软件计算,螺栓夹紧力为45000N,在压紧时受弯曲应力导致变形量为0.09mm。图 4 所示定位位置与卡压位置在一条线,并加装侧顶装置限制自由度,其螺栓夹紧力为 10000N,而且滑座几乎不受弯曲应力,变形量
几乎为 0。
3
图 3 (定位位置与卡压位置不在一条线)
4
图 4 (定位位置与卡压位置在一条线上)
实际生产活动中,操作者往往错误地认为粗加工时采用图3装夹方式不会影响后续加工精度,工件会快速恢复形状。然而经长期实践证明,工件经此方式长时间装夹后 7~24 小时自然时效才能基本恢复,对精加工有着深远影响。
金属在切削加工过程中刀具对工件产生强大的挤压力,使切削层在高应力,高应变,高切削温度的情况下与基体产生分离,形成已加工表面。
故此,已加工工件中存在较大的残余应力,也是滑座变形的重要因素。本文作者作为基层技术人员未在此方向上做深入研究,仅根据实际工作经验提出应对切削残余应力的若干措施 :
(1)尽量减少工件总的金属去除量即毛坯余量。
(2)满足设计要求条件下较低的毛坯硬度。
(3)切削参数方面宜采用平转数,小吃刀量、快进给的方式。
(4)加入人工时效处理工艺。
加工工艺是影响滑座变形的另一个因素,不合理的工艺规程编排容易造成应力累积导致变形。滑座作为机床机械结构中重要部件在毛坯出厂前和粗加工后都应进行时效处理,如去应力退火、振动时效等。另外,各工序间应适当进行自然时效以充分释放应力。
举例说明某型立式加工中心滑座工艺规程 :毛坯出厂退火→粗底面→粗上面→四周面→人工时效处理→钳序攻丝→油漆→精底面→精上面→磨底上面→成品检验(上诉各工序间时效 7 小时)然而实际生产活动中,机加工车间由于指令计划更改或其它因素影响经常变更或加速排产,导致工序过度集中或时效时间不充分从而影响工件的应力释放。
4. 滑座装配环节变形因素分析
在滑座装配环节中,部件或整机的装配刚度是影响滑座变形的主要原因,而装配刚度取决于部件的结构刚度及装配工艺的编排,实际生产活动中应注意以下几点 ;
(1)滑座在机加工后、装配前应在台位螺栓松开状态下静置 24 小时以充分释放铸造及加工环节的内应力。
(2)导轨螺栓与挤块螺栓拧紧顺序为从中央到两端的把紧方式,保证直线导轨与滑座导轨面充分贴合。
(3)挤块及压板压紧导轨侧面的方式压力较大,容易造成导轨基准面挤压变形。可酌情改为偏心螺钉方式压紧。
5. 结语
综上所述,滑座作为机床结构中的主要部件直接影响机床整机精度。本文从滑座结构设计、毛坯铸造、切削加工及整机装配几个环节阐述和分析了其变形的主要因素及控制措施。对滑座的整个生产链条具有一定的借鉴意义,从而有效控制滑座变形问题,能够快速提升机床产品性能和行业的竞争力。
投稿箱:
如果您有机床行业、企业相关新闻稿件发表,或进行资讯合作,欢迎联系本网编辑部, 邮箱:skjcsc@vip.sina.com
如果您有机床行业、企业相关新闻稿件发表,或进行资讯合作,欢迎联系本网编辑部, 邮箱:skjcsc@vip.sina.com
更多相关信息