现代航空发动机整体叶盘及其制造技术
2014-1-6 来源:数控机床市场网 作者:黄春峰
[ 摘要] 整体叶盘是现代航空发动机的一种新型结构部件, 对于提高其性能具有重要作用。本文主要介绍了航空发动机整体叶盘结构的特点、应用现状、发展趋势及其制造技术。
关键词: 发动机结构 整体叶盘 特种加工 制造技术
现代航空发动机的结构设计和制造技术是发动机研制、发展、使用中的一个重要环节, 为满足以 F119、F120、 EJ200 为标志的第 4 代战斗机用发动机以及未来高推比新概念发动机的性能要求, 除采用先进技术减少飞机机体结构、机载设备的重量外, 关键是要求发动机的推重比达到 10 这一级, 重点突破发动机部件的气动、结构设计、材料、工艺等方面的关键技术。其中,在发动机风扇、压气机、涡轮上采用整体叶盘(Blisk) 结构( 包括整体叶轮、整体叶环) 是重要措施。
1 整体叶盘结构的特点
(1) 整体叶盘是航空发动机的一种新型结构部件,它与常规叶盘连接相比有以下特点:·不需叶片榫头和榫槽连接的自重和支撑这些重量的结构, 减轻了发动机风扇、压气机、涡轮转子的重量。英国 R· R 公司在发动机中采用整体叶盘结构后, 与传统的叶片、轮盘分体结构相比, 重量可减轻50%; 若采用金属基复合材料 (MMC) 的整体叶环(Bling), 则可减重 70%。·原轮缘的榫头变为鼓筒; 盘变薄, 其内孔直径变大; 消除了盘与榫头的接触应力, 同时也消除了由于榫头安装角引起的力矩产生的挤压应力; 减轻了盘的重量, 提高了叶片的振动频率。
·整体叶盘可消除常规叶盘中气流在榫根与榫槽间缝隙中逸流造成的损失, 使发动机工作效率增加, 从而使整台发动机推重比显著提高。
·由于省去了安装边和螺栓、螺母、锁片等连接件, 零件数量大大减少, 避免了榫头、榫槽间的微动摩损、微观裂纹、锁片损坏等意外事故, 使发动机工作寿命和安全可靠性大大提高。
·如整体叶盘叶片损坏, 为避免拆换整个转子, 将整体叶盘与其他级用螺栓相连, 形成可分解的连接结构。
·由于高压压气机叶片短而薄, 叶片离心力较小,轮缘径向厚度小, 采用整体叶盘结构减重不显著。例如F414发动机的高压压气机, 前3级采用整体叶盘后重量只减少3.632kg;而两级风扇采用整体叶盘减重20.43kg, 因此EJ200发动机的高压压气机仅第一级采用整体叶盘结构。
(2) 航空发动机整体叶盘结构在研究发展中也存在一些问题。
·整体叶盘加工困难, 只有制造技术发展到一定水平后, 整体叶盘的应用才成为可能。
·发动机在使用过程中, 转子叶片常遇到外物打伤或因振动叶片出现裂纹, 整体叶盘要更换叶片非常困难, 有可能因为一个叶片损坏而报废整个整体叶盘。因此风扇的第1、2级一般不用整体叶盘结构, 整体叶盘叶片的修理技术也是整体叶盘扩大应用必须解决的关键问题。
·由于整体叶盘的叶型复杂, 精度要求高, 叶型薄, 受力后变形大, 所以机械加工非常困难, 又因为齿数多、齿密, 所以加工量非常大。因此叶型加工是整体叶盘制造的主要工序。
2 整体叶盘结构的应用
随着航空制造技术的不断发展, 近年来整体叶盘结构在新研制航空发动机中已得到广泛应用( 表 1)。
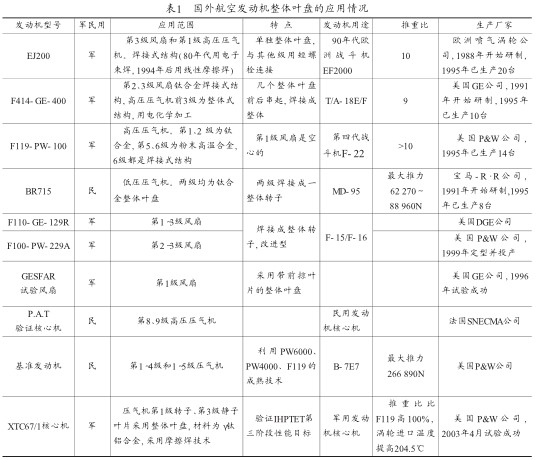
2.1 美国整体叶盘的应用
美国GE公司最早在20世纪70年代就在T700发动机的压气机上大量采用整体叶盘结构, 尔后又陆续将这一技术应用到CT7、CFE738、GE23A、YF120、F414和F110发动机上。YF120的2级风扇和5级高压压气机全部采用整体叶盘结构的转子, 风扇叶片采用低展弦比叶片, 其中第1级为空心叶片。F414的第2、3级风扇采用低展弦比叶片的串列转子采用惰性气体焊接的钛合金(Ti17) 整体叶盘结构,且两个整体叶盘还焊接在一起形成整体转子, 使风扇转子重量比F404减轻了20.41kg; 高压压气机前3级也采用了整体叶盘, 第1、2级用Ti17合金制成, 且焊成一体, 第3级采用Inconel 718镍基合金制成, 使压气机的重量减轻3.63kg。F404整台发动机5级整体叶盘转子比常规叶盘连接的零件减少了484个, 与原型机F404相比, 其推重比由7.5提高到9.1。由几个整体叶盘前后串起焊成一体的设计, 是F414优于EJ200发动机的显著特点, 它能进一步降低转子的重量, 提高发动机耐久性。F110- GE- 129改型为F110- GE- 129R时, 即将3级风扇全改成宽弦叶片、整体叶盘结构, 零件数减少了2/3。由于风扇效率与空气流量提高, 使发动机推力增加5.9%。如维持原推力, 则热端部件寿命由4000TAC循环( 战术空间循环) 提高到6000TAC循环。
90年代GE公司还研究了一种前掠叶片的整体叶盘结构风扇, 并在前掠气动研究试验台(GESFAR) 上成功地进行了试验。这种新型风扇部件具有高速、小展弦比、前掠叶片的特点, 整体叶盘由高强度钛合金制成, 叶尖直径约为508~ 635mm, 空气流量约为100kg/s。试验结果表明该风扇不仅减轻了重量, 而且比常规风扇的效率高4%, 其中尖部效率提高8%, 失速裕度提高3%~ 5%, 因而使发动机抗流场畸变能力提高80%。目前GE公司已将其安装到IHPTET验证机上进行了评估, 并将用于改进现役发动机, 如F414等。
80年代初, 美国P&W公司开始在PW5000发动机上使用和验证风扇压气机整体叶盘结构, 目前已应用到F119和F100发动机上。P&W公司为先进战术战斗机ATF/F22研制的推重比为10的F119- PW- 100发动机, 3级风扇、6级高压压气机的转子, 全部采用了整体叶盘,是唯一一种在风扇与压气机中全部采用整体叶盘结构的发动机, 6级轴流高压压气机整体叶盘的第1、2级为钛合金, 叶片和轮盘用线性摩擦焊将其焊成一体; 第3~6级为粉末高温合金, 叶片与轮盘的焊接采用了锻接扩散连接技术。有的F119压气机转子还采用ALLOY- C型阻燃钛合金整体叶盘。ALLOY- C型钛合金不但具有良好的阻燃性能, 而且具有良好的高温变形、冷轧、延展、焊接和铸造性能, 其钣金成形延展率可达40%~ 50%。
在F100- PW- 229发动机改型(F100- PW- 229A) 中的第2~ 3级全部采用整体叶盘结构。 改型后的发动机在保持推力不变的情况下, 涡轮进口温度降低49℃, 发动机的可靠性和寿命得到提高。在PW7000发动机方案中, 5级高压压气机全部采用大后掠、高效率叶片的整体叶盘结构转子。90年代初, P&W公司还研究了带后掠叶片的整体叶盘结构的两级风扇, 其尺寸和流量与F119的风扇的基本相同, 目前该叶片为后掠实心叶片,但将来可能采用空心的金属叶片或复合材料叶片。该风扇效率比当时的IHPTET基准风扇的效率高50%左右, 每级风扇的压比比IHPTET基准风扇的高30%, 不久将装到IHPTET验证机发动机上进行试验验证。
美国联合攻击机JSF的升力风扇也采用了整体叶盘结构, 这是迄今为止最大的整体叶盘, 外径1.27m, 毛坯重1 500kg,成品重100kg。艾利逊公司1998年在XTC16/1A核心机上试验了涡轮整体叶盘, 这是用锻接工艺将单晶Lamilloy叶片粘接在粉末冶金盘上的,Lamilloy转子叶片比常规气膜冷却叶片少用30%的冷却空气, 寿命增加100%, 整体叶盘结构减少重量25%~30%。据《航空周刊》最新报道, 美国P&W公司在IHPTET计划下成功完成了XTC67/1先进发动机核心机的试验。XTC67/1核心机压气机的第1级转子、第3级静子叶片采用了比强度高的γ 钛铝合金整叶片盘, 目的用于验证IHPTET计划第三阶段的性能目标, 推重比要比F119发动机提高100%, 涡轮进口温度提高204.5℃, 4级压气机的压比比F119的6级压气机压比还要高。该核心机在美国空军阿诺德工程发展中心的J1试验台上进行了6批次试验, 截至2003年4月累计时数28h。另外, 为满足波音公司的B- 7E7飞机推进系统和成本目标, 美国P&W公司的基准发动机也将采用已验证技术和先进制造技术。其中B- 7E7发动机前4级或前5级压气机将采用整体叶盘。P&W公司还将在美国空军阿诺德工程发展中心(AEDC) 进行7E7发动机的高空模拟试验, 累计试验时数将达到15 000个工作循环。这项计划已于2004年正式启动。
2.2其他国家整体叶盘的应用
英国、德国、意大利和西班牙合作研制的EJ200发动机, 其3级风扇压比为4.2, 最初只在远离进口处的第3级风扇上采用了电子束焊接的整体叶盘结构, 后来在第2级也采用了整体叶盘结构, 目前第1级上也已采用整体叶盘结构, 并有可调进口导流叶片以保证有足够的压气机喘振裕度。其材料为钛合金, 用线性摩擦焊取代电子束焊制造整体叶盘。
在宝马- R · R公司研制的BR715发动机上, 由于第1级风扇叶片采用了RB211- 535E发动机的宽弦无凸台夹芯叶片, 尘砂进入极少。风扇后的两级低压( 增压) 压气机都采用宽弦空心叶片的整体叶盘, 并将两级焊成一体, 形成不可分散的连接结构, 这是整体叶盘在民用高涵道比发动机上首次应用。加工和修理整体叶盘结构除采用电子束焊外, R· R公司与MTU公司还共同开发了线性摩擦焊工艺。
法国国营航空发动机制造公司SNECMA在20世纪90年代初开展了一项为发展新型民用发动机核心机的技术验证计划, 即P.A.T计划( 技术活动计划, Plan Act~ion Technologies)。在该计划中, 11级压气机中第8、9两级采用了整体叶盘结构, 这实际上也是为整体叶盘结构在大型民用发动机中推广进行的技术储备与探索。
我国正在研制带箍的整体叶盘结构, 目的是为了克服前掠叶片的颤振。这种叶片带箍设计, 即叶片尖部加一个环带, 这样叶片振动受到了约束, 颤振可以消除; 但叶片箍的受力非常大, 一般金属材料是无法承受的。利的。利用碳纤维可以承受极大的拉力这一特性,在金属箍外面加绕碳纤维的复合材料, 叶片、盘及箍产生的离心力由碳纤维复合材料承担。由于碳纤维复合材料密度只有 1.6~ 1.7g/cm3, 而钛合金材料为 4.6g/cm3左右, 所以箍的重量不大。常规设计中, 叶片受的是拉伸应力, 现在带箍叶片上半部受的是压缩应力, 叶片受的应力下降, 所以叶片厚度可以下降很多, 盘的重量也可以大大下降, 重量大约是常规叶盘结构的50%。预计在不久的将来, 这项技术会普遍应用在航空发动机的风扇和高压压气机设计中。
2.3 整体叶盘结构的发展趋势
整体叶盘结构不仅应用在研制和改进中的发动机上, 而且还将用在未来推重比为15~ 20的高性能发动机上 ,如欧洲未来推重比15~ 20的发动机和美国的HPTET计划中推重比为20的发动机, 在这些发动机上将采用效果更好的SiC陶瓷基复合材料或抗氧化的C/C复合材料制造整体涡轮叶盘。美国研制的C/C复合材料整体涡轮叶盘已在1 760℃环境中进行了地面超转试验。采用整体叶盘结构, 其转子叶片必然要设计成抗外物损伤的叶片, 以减少维修次数费用。目前风扇和压气机整体叶盘结构的转子叶片普遍采用小展弦比的钛合金叶片, 有空心、实心、掠式和非掠式的; 而下一代推重比为15~ 20的发动机必将采用气动性能先进的掠式、重量更轻的空心抗外物损伤能力强的小展弦比叶片, 如果可能, 也将用强度和刚性更好及密度更小的金属基复合材料代替高温钛合金, 这样可提高气动性能和效率, 既满足强度和可靠性要求, 又大大减轻重量, 使发动机推重比大大提高。
如果将整体叶盘中的轮盘部分去掉, 就成为整体叶环, 这时该件的重量将进一步降低。整体叶环直接固定在承力环上。由于缺少了承受负荷的轮盘, 整体叶环承受不了叶片的离心负荷, 为此, 整体叶环只能用密度较小的复合材料来制造。这种整体叶环的重量约为常规结构重量的30%, 目前, 正在研制的整体叶环是用连续单根碳化硅长纤维增强的Ti基复合材料 (TiMMC)制造的。TiMMC具有比强度、比刚度高, 使用温度高及疲劳和蠕变性能好的优点。例如德国研制的SCS- 6SiC/IMI834复合材料的抗拉强度高达2 200MPa, 刚度达220GPa, 而且具有极为优异的热稳定性, 在700℃温度暴露2 000h后, 力学性能不降低。TiMMC叶环代替压气机盘, 可使压气机的结构重量减轻70%。
美国制造的TiMMC整体叶环已成功用在P&W的XTC- 65IHPTET验证机的第3~ 4级压气机上, 由于材料和结构的先进性使转子重量大大减轻, 如第3级整体叶环转子重量只有4.5kg左右, 而常规镍基合金制造的同样转子的实际重量为25kg。由于TiMMC复合材料只能承受477℃的温度, 压气机不能在高温环境下工作, 下一步将考虑用Al- Ti化合物(Ti3Al和TiAl) 作基体, 可耐温927℃。英、法、德也研制了TiMMC叶环, 并成功地进行了台架试验, 用于改进EJ200的3级风扇、高压压气机和涡轮, 以便为EJ200在21世纪推重比达15~ 20提供技术基础。在我国与印度开展的国际合作项目中, 有一带环箍的单级风扇试验研究, 该风扇的设计参数为: 增压比3.0, 叶尖切向速度470m/s, 有17片叶片, 外径0.4m, 采用了带外箍环的整体叶环结构 ( 只能用复合材料来制作), 目前印度已成功制造出该试验件, 在国际上处于领先地位。
3 整体叶盘的制造技术
发动机整体叶盘的制造工艺和维修的复杂性是目前影响其应用和推广的两大因素。整体叶盘的机械制造加工面临越来越强的挑战。由于整体叶盘结构复杂,加工精度要求高, 尤其是叶片工作表面为空间自由曲面, 形状极其复杂; 特别是为适应其高温、高压、高转速的工作条件, 广泛采用钛合金、粉末高温合金等高性能金属材料和钛基复合材料、钛铝化合物基复合材料等先进复合材料, 因此影响了材料的可加工性, 传统的机械加工方法已难以胜任, 必须应用现代特种制造加工技术, 探索研究出更加高效、可靠的加工工艺方法。整体叶盘从结构设计上分为整体式和焊接式两类。整体式整体叶盘制造依赖于精密制坯技术、特种加工技术和数控机床的发展; 焊接式把复杂、困难的叶型加工改变成单个叶片的叶型加工, 但增加焊接工序, 焊接的精度和焊缝质量与整体叶盘的性能和工作可靠性密切相关。因此, 焊接工序只能采用先进、精密的焊接工艺, 如电子束焊、线性摩擦焊、真空固态扩散连接等。
目前, 制造整体叶盘有以下5种技术途径。
3.1 精密制坯技术
现代精密制坯技术( 精密铸造和锻造) 的发展日臻完善。精密铸造和精密锻造采用CATIA软件、预测模型和计算机模拟技术实现了“实体造型” 以及铸、锻过程用计算机模拟仿真, 这些技术提高了金属填充和凝固质量, 消除了疏松, 避免了热裂, 可取代常规的试铸法,从而提高了精密铸造和精密锻造的质量与效率, 降低了成本。
(1) 精密锻造技术的发展使锻压工艺彻底突破了毛坯生产的范畴, 可以加工出接近成品的零件。现在,整体叶盘大多采用精密锻造作为制坯手段, 能节省贵重金属材料, 减少难加工材料的机械加工量, 提高整体叶盘的疲劳强度和使用寿命。美国GE公司已用等温锻造技术制造出了带叶片的压气机整体叶盘转子, 材料利用率提高4倍。精密锻造零件的尺寸精度可以达到 (0.1~ 0.25)mm, 表面粗糙度可以达到Ra0.4~ 1.6μ m。整体叶盘精密锻造的精度和质量主要依靠计算机对锻造过程进行控制。GE公司已用热等静压法将钛合金粉末高温合金盘与精锻叶片复合成形为钛合金整体叶盘;在精密锻造时还采用了超塑等温模拟技术, 获得了优异的组织和力学性能。
(2) 精密铸造技术。由于精密铸造工艺的新发展,特别是金属材料定向凝固和热等静压理论的深入研究, 使得铸造合金组织和性能大大改善, 解决了叶片疲劳断裂的裂纹沿垂直于叶片主应力方向的晶粒边界发生; 熔模铸造内部存在缩松缺陷等问题, 使叶片的抗疲劳性、应力断裂寿命大为提高, 并且可以减少焊后裂纹, 降低铸件的性能变化和分散程度。目前, 较为成熟的精密铸造技术有实型铸造和熔模铸造。
我国航空材料研究院整体叶盘的精密铸造技术已取得重要成果。采用 K4184 镍基高温合金, 成功铸造出了直径为 120mm, 带有 34 个叶片的动力涡轮整体叶盘。采用的方法是将轮盘铸造成细晶, 将整体叶片铸造成定向柱晶或单晶, 不同晶粒形态各有优势, 细晶具有较好的低周疲劳和拉伸性能, 适合于中低温下使用;而方向性柱晶则具有较好的冷热疲劳、低周疲劳和抗振动疲劳性能, 适合于高温下工作。
为了进一步提高采用精密铸造制造的整体叶盘坯件的密度, 改善力学性能, 应将坯件进行等静压处理和真空热处理
3.2 锻接法
美国 P&W 公司在制造粉末高温合金整体叶盘时, 应用了锻接扩散连接技术( 即扩散连接技术), 它用局部加热法将单晶精铸叶片直接连接到锻造涡轮盘的轮缘上。 涡轮盘轮缘局部加热至变形温度后, 用待连接的单晶叶片在局部加热的轮缘连接部位施压, 使局部加热区域产生变形, 即在将叶片植入轮缘内的同时进行扩散连接, 将叶片牢固地连接在涡轮盘的轮缘内。锻接法的关键是正确有效地控制局部加热和变形参数( 温度、压力、变形量), 这对叶片与轮盘之间消除松动,产生完全致密的高强度结合面是很重要的。用此法制造的整体叶盘结构必须确保锻接过程中叶片始终准确定位, 并始终保持定位的位置。P&W 公司已研究出叶片/盘的锻接专利工具, 可准确地保持叶片的正确位置。
锻接工艺可有效用于超级耐热合金和钛合金之间的连接和修补, 可用于风扇、压气机和涡轮整体叶盘结构的制造、修补和更换叶片。
3.3 电子束焊接法
在各种先进精密的焊接工艺中, 电子束焊发展较早, 也较成熟, 并最先用于整体叶盘的制造过程中。整体叶盘因其主要用于风扇的第 2、3 级和高压压气机的第 1、2 级, 故材料多为钛合金。由于钛合金电子束焊具有大穿透、小变形、无氧化、高强度、焊接尺寸精度高、质量稳定、效率高等优点, 因而在我国高性能航空发动机制造中很多钛合金零件都采用电子束焊接工艺。
EJ200 也采用此法制造, 即先将单个叶片用电子束焊接成叶片环, 后用电子束焊接技术将锻造和电解加工成形的轮盘腹板与叶片环焊接成整体叶盘结构。这种整体叶盘结构比传统的榫头连接的叶盘转子结构重量减轻 30%。
3.4 线性摩擦焊(LFW)
线性摩擦焊是一种固态连接技术, 是旋转摩擦焊的重要发展, 类似于扩散连接。扩散连接从结构上讲,连接处看不出“焊缝” 来, 且其强度与弹性均优于本体材料。 线性摩擦焊与扩散连接不同之处在于: 在扩散连接中, 连接的工件是在炉中加温使其达到高温的; 而线性摩擦焊中, 工件的高温是通过两配合面间的相互高频振荡产生的。 用线性摩擦焊将叶片焊接在轮盘上,可节省大量叶片的连接件和结构重量。它先将叶片夹紧在轮缘的叶根上, 并使轮盘周向以高速振动, 在叶片和轮盘叶根界面产生一个窄的摩擦加热区, 当加热区的温度达到要求的温度时即停止振动, 叶片与轮盘固定直至固结在一起。最后再在五坐标数控铣床上用铣刀将多余材料铣掉。F119 的 2、3 级风扇和 6 级高压压气机以及EJ200 发动机的 3 级低压压气机的整体叶盘是线性摩擦焊接技术成功应用的顶级标志。其中, 用LFW 技术加工的 EJ200 发动机的整体叶盘, 所用设备是英国 Blacks 公司制造的线性摩擦焊机。该焊机由 1个主驱动电机( 功率 89kW)、振动器及夹具组成, 振动器可产生线性振动, 振幅 0~ 3mm。夹具带有分度机构,可对工件进行分度、定位和固定, 并传递夹紧力、顶镦力和摩擦力。振动器可以在焊接工序完成时的几分之一秒内使振幅为零, 保证被焊叶片的定位精度。瑞士的一家公司可以提供与之配套的高速磨床和理想的软件包。目前 R · R 公司和 MTU 公司已用 LFW 技术成功地制造了宽弦风扇整体叶盘, 并将为 JSF 的发动机提供LFW 整体叶盘。用 LFW 技术加工整体叶盘与用整体锻坯在五坐标数控铣床上加工或电化学加工相比, 可以节约大量贵金属; 用 LFW 技术可从发动机上更换掉被撞击损坏的叶片。也可用 LFW 技术将叶片与用不同材料制造的轮盘焊接在一起, 以获得最佳的减重效果。
扩散连接和线性摩擦焊是在接合表面产生塑性变形和加热条件下, 达到表面原子间结合, 并互相扩散形成焊接头, 加热温度一般为被焊材料熔点温度的 70%,因此焊接接头的质量比熔焊( 电子束焊) 的质量高, 可以使叶片和盘的过渡区的晶粒组织变得很细, 其静态、动态力学性能超过非焊接的基体材料。
采用线性摩擦焊加工整体叶盘有下列好处:
(1) 可以节约大量贵重的钛合金。例如 R · R 公司为 JSF( 联合攻击机) 用的升力风扇发动机生产整体叶盘的风扇转子( 该转子是目前世界上最大的整体叶盘,其外径为 1.27m) 时, 采用整体锻坯用五坐标数控铣床加工, 坯料重 840kg, 加工后成品件重 97.6kg, 即材料损耗高达 88%; 而采用线性摩擦焊时, 焊接后铣去的材料不多, 并且还可减少加工时间。
(2) 可以对损坏的单个叶片进行修理。在采用(特别是在风扇第 1 级采用)整体叶盘时, 能否对整体叶盘进行修理是要考虑的一个重要问题, 因为发动机在使用中, 不可避免地会遇到外来物(特别是鸟类)撞伤叶片的情况, 在常规的设计中, 可以轻易地更换损伤的叶片; 而整体叶盘就不能更换叶片, 如没有方便而适用的修理损坏叶片的方法, 整体叶盘的应用就受到限制。有了线性摩擦焊的加工方法, 可以将损坏的叶片切去后再焊上新叶片, 由于有此优越性, EJ200、F119 发动机风扇第 1 级转子也采了整体叶盘 (EJ200 最初的设计中, 仅风扇第 3 级、高压压气机第 1 级采用整体叶盘)。
(3) 可以将 2 种不同材料焊在一起, 这样可根据叶片、轮盘的工作条件选用不同材料, 从而充分挖掘转子结构材料的性能潜力, 使转子结构的重量进一步降低。
3.5 数控电解加工技术
整体叶盘由于构型复杂, 特别是由难切削材料制成的、带薄型叶片、结构复杂的整体叶盘用数控铣削、精密铸造方法加工时就更困难, 甚至不能加工( 如带冠整体叶轮)。此时特种加工方法便显示出它突出的优越性, 其中, 电解加工与数控技术相结合的数控电解加工技术, 作为一种补充技术, 可以解决数控铣削精密铸造不能加工的难题, 为整体叶盘制造提供了一种优质、高效、低成本、且具有快速响应能力的新加工技术。整体叶盘的数控电解加工技术能综合发挥计算机数控和电解加工的技术优势, 同时又能取长补短。这种工艺具有电解加工的优点, 即工具阴极无损耗, 无宏观切削力, 适宜加工各种难切削材料和长、薄叶片及狭窄通道的整体叶盘, 加工效率高, 表面质量好, 这些优点是数控铣削所不具备的; 它又具有数控的优点, 能以计算机数控方式实现型面三维运动, 可用于加工各类复杂结构、多品种、小批量零件, 甚至单件试制的生产中,这些优点又是一般拷贝式电解加工所不具备的。 因此,这种工艺技术非常适合于加工用数控铣削、精密铸造难加工或不能加工的零件, 如小直径、多叶片、小叶间通道(1.5~ 3mm宽度) 零件, 难切削材料变截面扭曲叶片整体叶轮, 以及数控铣无法加工的带冠整体叶轮等。研究及应用情况表明, 整体叶盘电解加工与五坐标数控铣削方法相比有很多优点:
·工时可减少50%以上 ( 加工带长叶片的整体叶盘工时减少更多);
·可以加工任何高强、高硬度的难切削金属材料;
·不会产生残余应力和变形, 这对薄型叶片的整体叶盘加工尤为重要。
美、英、俄和中国都高度重视整体叶盘数控电解加工技术的研究并已得到应用, 在新型航空发动机及航天火箭发动机的研制中发挥了重要作用。
(1) 美国GE公司的五轴数控电解加工。
美国GE公司在电解加工先进航空发动机的整体叶盘时, 采用了以成形或近成形阴极进行多坐标数控送进运动的加工方式。在制造为装备 “先进战斗机ATF(即F22)” 而研制的GE37/YE120发动机的钛制整体叶盘及F414发动机整体叶盘时, 与美国Lehr.precision公司合作发展了五轴数控电解加工技术。与原用五坐标数控铣削叶片相比, 加工时间减少约85%, 同时还避免了在叶片加工中产生的残余应力。电解加工仍分粗加工和精加工两道工序, 加工出的叶片叶型厚度公差+0.1mm, 型面公差+0.1mm, 可不需手工抛光。
(2) 美、俄仿形电加工带冠整体叶轮。
在带冠整体叶轮的加工中, 美国采用精密数控电火花工艺, 俄罗斯则采用机械仿形电火花与电解加工的组合工艺。电解加工既可以提高加工速度, 又可以去除电火花加工后的表面变质层, 提高表面质量。电火花—电解加工的组合工艺在新型发动机, 特别是火箭发动机带冠整体涡轮的研制中发挥了重要作用。
(3) 国内数控电解加工整体叶盘的研究。
在国内, 南京航空航天大学从 20 世纪 80 年代中期就开始进行数控展成电解加工的研究, 其中重要研究成果有: “直线刃” 阴极数控展成电解加工, 成形或近成形阴极柔性电解加工。
“直线刃”阴极数控展成电解加工与数控铣相似,以简单的 “直线刃” 阴极进行数控展成运动, 基于电化学阳极溶解原理而实现整体叶盘叶间槽和叶片型面的粗、精加工。
数控展成电解加工通常需要 5 轴联动, 即直线位移 x、y、z 轴以及阴极摆动 CT轴和工件旋转 CW轴。该研究成果已经应用于加工改型航空发动机整体导风轮( 外径190mm) 并装机使用。
成形或近成形阴极柔性电解加工是南京航空航天大学正在研究的加工非可展直纹面的一种新方法, 采用成形或近成形阴极相对零件作数控仿形运动, 可实现带冠整体涡轮、整体叶环和组合式整体叶轮的加工。
4 整体叶盘结构的维修
航空发动机上风扇/压气机叶片经常被打坏, 在以往的常规设计中, 遇到这种情况时更换受损的叶片就可以了, 但是叶盘结构就不能因为一个叶盘上有几个叶片打伤而报废一个叶盘, 所以必须发展整体叶盘中个别损坏叶片的修理技术。GE 公司发展特殊的修理技术后才在 F414 中使用了5 个整体叶盘。在 IHPTET 计划实施中, 利用激光曲线焊接(Laser Twist Weld) 方法对整体叶盘进行修复, 叶片修复后强度与原叶片差不多。这样, 叶盘结构具有了生命力, 就能在航空发动机上得到更广泛的应用。
5 结束语
(1) 航空发动机部件结构正朝着轻量化、整体化方向发展。美国的先进战斗机(ATF) 计划中把整体叶盘设计制造列为重要核心技术, 美国国防部的高性能涡轮发动机技术(IHPTET) 的第三阶段计划要求, 到 2020年, 战斗机上发动机的涡轮都将采用整体叶盘结构。由此可见, 整体叶盘( 环) 已经作为新型航空发动机、火箭发动机的重大改进部件, 不仅应用在研制中和改进的发动机上, 而且还将用在未来 10~ 15 年后推重比为25~ 30 的发动机上, 用性能更加优异的 SiC 或 C/C 增强复合材料制造出整体叶盘或整体叶环。
(2) 随着新的更难切削材料的采用及结构的更复杂化(扭曲叶片整体叶盘、带冠整体涡轮), 航空发动机的加工将更困难。美、英、俄等工业发达国家都在加紧研究优质、高效、经济的加工方法并正逐步取得成果。
(3) 整体式叶盘的制造将依赖于精密制坯技术、特种加工和数控机床的发展。其中数控电解加工能综合发挥电解加工和计算机数控技术的优势, 同时又能互相取长补短, 弥补各自的不足之处, 是优质、高效、低成本、快速响应地解决整体叶盘加工难题的一条重要途径。这种方法具有显著的技术经济效果。
焊接式整体叶盘的焊接工序只能采用先进的精密的焊接工艺( 电子束焊、真空扩散连接和线性摩擦焊),特别是线性摩擦焊的加工成本低, 焊接质量高, 可用于各种材料的焊接或整体叶盘的制造、修理和更换叶片,在整体叶盘的制造中可以发挥独特而重要的作用。
投稿箱:
如果您有机床行业、企业相关新闻稿件发表,或进行资讯合作,欢迎联系本网编辑部, 邮箱:skjcsc@vip.sina.com
如果您有机床行业、企业相关新闻稿件发表,或进行资讯合作,欢迎联系本网编辑部, 邮箱:skjcsc@vip.sina.com