航空发动机风扇单元体高效孔加工技术
【摘要】: 论述了涡扇发动机风扇单元体孔的特征、加工难点和加工刀具的设计思路。针对特征孔加工周期长、质量差的问题,设计了新型加工刀具及改进加工工艺路线,提高了加工效率和零件质量,形成一套高效的孔加工方案,有利于提升航空发动机整体制造水平。
【关键词】: 高效孔加工 ; 航空发动机 ; 自动化
1.引言
风扇单元体是航空发动机中的重要支撑和连接部件,特征孔加工难度大,迄今少数国外企业垄断了特征孔的高效加工技术和装备。 由于国内特征孔高效加工经验不足,金属切削加工技术欠缺,特征孔的高效加工已成为制约我国装备制造业高速发展的瓶颈之一。
特征孔的加工难点在于多特征孔、深孔和反锪孔加工,如 CF34-10A 的风扇单元体中有较多的输油孔、吊挂孔和连接孔,加工难度大、周期长,一直是生产加工中的难点。因此,本文通过设计专用加工刀具和改进加工工艺方案对加工难度大的特征孔进行高效加工研究,以解决孔加工周期长、精度差等问题。高效孔加工可以为加快我国先进发动机生产进度提供技术保障,且具有较大的应用价值和广阔的应用前景。
2. 特征孔的加工难点
以 CF34-10A 的风扇单元体为研究对象,加工难度大的特征孔主要分为深孔、多特征孔和反锪孔,其数量众多且结构复杂,目前的通用加工刀具无法做到一次成型,因此需要众多工步和繁杂的工艺路线,加工周期较长。
2.1 深孔加工难点
深孔特征在航空发动机中较为常见,某型号零件的深孔结构特征如图 1 所示。
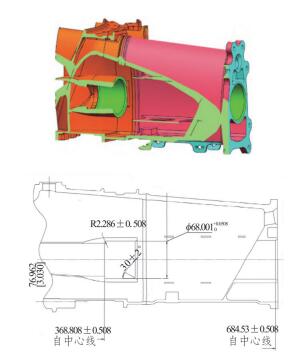
图 1 深孔加工结构特征
具体加工难点有 :
加工状态不可见 : 如图 1 所示,深孔位置在风扇框架的内腔中,加工时无法观察到刀具的下刀位置,只能根据声音判断加工过程中零件的状况和刀具的磨损状况,在一定程度上给编程和加工带来了难度。
精度高 : 该孔为装配精密孔,尺寸公差要求严格(直径φ68.001+0+0.0508mm,位置度φ0.0508,粗糙度 Ra1.6),加工中刀具的磨损、排屑状况和刚性导致的振动都会造成尺寸超差。
刚性差 : 从图 1 可以看出,该部位属于深孔加工(加工深度 315.772mm),长径比 L/D ≥4,且无法支撑薄壁,部件刚性较弱,加工时容易产生振动和变形,导致零件超差,无法保证孔的精度。
孔特征多 : 孔底部有 R2.286mm±0.508mm圆角,孔口有深度 3.81mm±0.508mm、角度30° ±2°的倒角,造成工步分散,加工周期长。切削热不易散出 : 深孔加工排屑困难和排屑通道长,零件加工一直处于封闭环境,产生大量的切屑热不易散出,由于热量会对零件和刀具产生影响,在冷却不到位情况下易造成钛合金零件尺寸超差。
2.2 多特征孔加工难点
多特征孔大多有四五处加工特征,需要经过多道加工工艺且公差要求较严,因此在加工过程中周期长成为主要难点,图 2 为多特征孔结构。
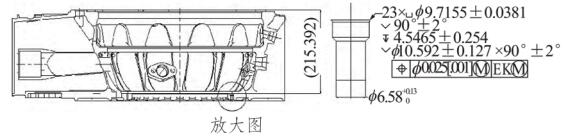
图 2 多特征孔加工结构
特征多是该孔主要加工难点,具有沉头孔、两处倒角、通孔等特征,需要多种加工工艺(见图 3),现场操作中需要多次更换刀具和两次零件装夹,造成同轴度易超差、加工内容繁杂、工序分散、加工周期长、加工效率低等问题。

图 3 多特征孔加工路线
2.3 反锪孔
反锪孔在风扇部件中是重要的装配特征,数量众多且孔径尺寸公差要求较为严格(见图4)。
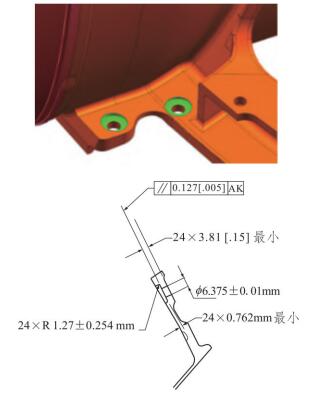
图 4 反锪孔结构特征
主要加工难点有 :
结构特殊导致加工难度大 : 由于沉头在反面,所以无法应用普通刀具,目前国内使用分体式反锪刀进行加工,需要在加工时手动装卸刀头,完成一个孔的加工需要三次装卸,自动化水平低,严重制约生产效率 ; 如果忘记装卸刀头则会和零件发生碰撞,加工风险高,严重时会造成零件报废。
刚性差 : 从图 4 可以看出,反锪孔位于零件边缘且周向分布,此位置壁厚相对较小,刚性弱,加工时需要将刀柄深入通孔底部后再装刀进行反向切削,因而刀柄直径较小(通孔直径±0.01016mm),加工状态不可控,尺寸易超差。
冷却不充分 : 因为加工位置在背部,冷却液浇注难度大,会对零件质量造成极大影响,因此在加工中必须采取有效的冷却方式来降低切削区域温度。
3. 解决方案
3.1 深孔解决方案
由于深孔的特点在于长径比较大,加工时无法进行观察,参数设定较高容易使刀具产生振动,影响特征孔的表面质量和尺寸精度,因此可以在保证质量的前提下设计专用的深孔刀具 : 一把粗镗刀去除大余量和一把精镗刀保证尺寸精度。专用镗刀的设计目的是改善深孔加工的加工效率和加工质量,因此需对镗刀的尺寸大小、重量和结构进行分析,最大程度地保证加工状态的稳定性和高效性。
3.1.1 刀具参数
深孔加工需要利用镗刀长度和直径尺寸控制刀具的摆动偏差,进而保证加工的稳定性。 图 5和图 6 为刀具摆动偏差和刀具尺寸的关系。
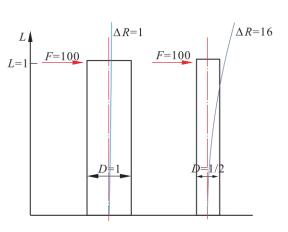
图 5 长度对摆动偏差分析
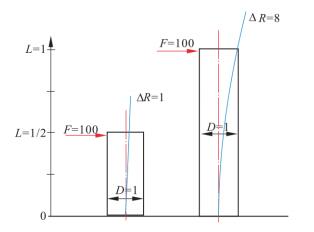
图 6 直径对摆动偏差分析
针对镗刀长度,有

式 中,Δ R 为 摆 动 偏 差(mm); F 为 切 削 力(N); L为刀杆长度(mm); E为弹性模量(N /mm2); I为截面惯性矩(mm4)。
从式 (1) 中可以看出,ΔR 和 L3 成正比,因而在满足加工要求的条件下,镗刀越短摆动偏差越小,刚性越好,因此刀具长度应尽可能接近深孔深度。
针对镗刀直径,有

式中,I为截面惯性矩 (mm4); D为刀柄直径(mm)。
从式(2)可以得出,I和 D4 成正比,刀柄直径D越大,截面惯性矩I就越大,摆动偏差△R就越小,因此在满足加工的条件下刀柄直径越大越好。
综上所述,为保证零件加工时的稳定性,尽量选择长度短、直径大的镗刀。
3.1.2 冷却系统
深孔区域加工内容较封闭,冷却液不易冲到,因此需要增加内冷系统,不仅可以有效降低切削区域温度,保证加工质量,也可以通过内冷将铁屑冲出,防止堵屑。
3.1.3 切削齿数
传统粗加工用整硬铣刀进行螺旋层铣去除大余量,此方法受力不均匀,加工效率低,周期长。通过增加切削刀片的数量,采用多刃对称镗刀对零件进行加工,以达到部件受力均匀效果。改进前后的受力效果如图 7 所示,这种粗镗刀加工方式类似于铰孔,比螺旋层铣更加高效、稳定。
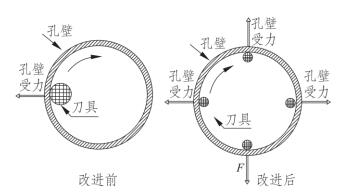
图 7 受力效果对比
3.2 多特征孔解决方案
针对多特征孔的加工难点对刀具进行改进设计 : ①风扇单元体多为导热性差的钛合金,所以刀具需要有内冷孔 ; ②定制一把专用的多特征台阶钻(见图8),可以将原工艺路线从钻孔、扩台阶孔、铰孔、倒角集中为钻孔工艺,达到工序集中目的,提高加工效率,解决加工周期过长的问题,并且缩短工艺路线,也可以提高加工质量(同轴度)和容错率 ; ③将弹簧刀柄替换为专用热缩刀柄,增加刚性。
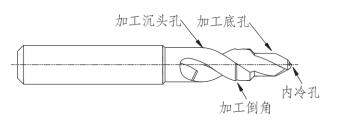
图 8 台阶钻
3.3 反锪孔解决方案
反锪孔的难点是分体式反锪刀需要人工装卸,步骤繁琐,容错率低。为解决加工低效的难题,设计一把专用的整体式反锪刀,其设计理念为通过冷却系统和离心力控制刀片的收放,解决人工装卸问题,进而达到缩短周期、提高自动化程度的效果。
3.3.1 自动化控制刀片
可以通过控制冷却液和转速来实现自动控制刀片收放,打开内冷刀具收回,打开转速则刀具伸出(见图9)。自动化控制刀具收放可以减少人为操作,提高零件加工质量和加工效率。
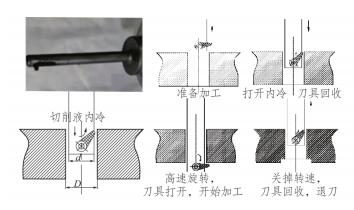
图 9 高效反锪刀加工
3.3.2 刀杆设计
加工反锪孔的刀杆直径比底孔小,在反锪孔加工过程中刀具振动会造成反锪孔有振纹,无法满足粗糙度要求,因此需要通过增加减振装置来提高刀杆刚性,控制加工质量。
4. 效果分析对比
4.1 深孔加工效果对比
深孔加工工艺是用整硬铣刀螺旋层铣去除大余量后用镗刀进行精加工,再倒角。分析深孔加工难点,利用专用粗镗刀提高加工效率并缩短加工周期,以某外贸零件为例分析对比改进效果。
4.1.1 加工周期
深孔加工时间为

改 进 前, 工 艺 路 线 为 先 螺 旋 层 铣 再 精镗,螺旋层铣见图 10,加工参数为 : 螺旋铣S600F80 ,螺旋铣层数 66; 精镗 S60F6。理论螺旋铣时间 126.9345min,精镗(两刀加工)时间为 44min,总时间为170.9345min,现场实际加工时间为 200min。
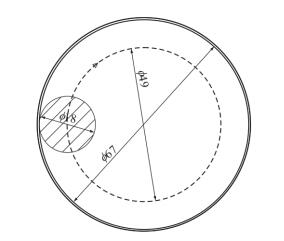
图 10 螺旋层铣
使用专用镗刀后,工艺路线为先粗镗再精镗,加工参数为 : 粗镗 S85F15,精镗 S70F7。理论粗镗(一刀)加工时间 8.8min ,精镗(两刀)加工时间 38min,总时间 46.8min,现场实际加工时间 50min。
4.1.2 加工质量
经过专用镗刀加工,深孔基本无振纹,深孔的直线度也得到保证,解决了光洁度、粗糙度不合格以及深孔被加工成喇叭孔的问题,总体质量优于原加工方式。
4.2 多特征孔的加工效果对比
4.2.1 加工周期
改进前的工艺路线为 : 钻中心孔—钻底孔 φ6—铰孔 φ 7—钻孔 φ9.72—倒角—倒角 ; 加工参数为 : 钻中心孔 S600F50,钻底孔 S600F20 ,铰孔S600F20 ,钻孔 φ9.72 S200F10,倒角 S240F20。单孔加工约 19min,23 个孔的总加工时间为437min 。改进后的钻孔工艺只需一刀完成,加工参数为 S780F50,加工时间为 23min。 通过对比,改进后节约时间 414min,缩短 94.32% 。
4.2.2 加工质量
通过使用台阶钻加工多特征孔,孔的位置度和同轴度有明显改进,并且在刀具中增加了内冷孔,使得加工区域完全冷却且易于排屑,进而提高了特征孔的光度和尺寸精度,相比原加工方案有明显改善。
4.3 反锪孔加工效果对比
4.3.1 加工周期
改进前的工艺路线为拆刀头—下刀—装刀头—反锪加工—退刀—拆刀头—返回起始点,加工时间为40h(现场统计)。改进后只有钻孔工艺,加工时间为 3.7h。
分体式反锪刀需要手动装卸刀头,因而加工周期不可控,加工效率极低。 通过对比可以得出,时间减少 36.3h,缩短 90.75% 。
4.3.2 加工质量
分体式反锪刀加工特征孔时,可以利用程序来控制内冷进而控制刀具的收缩,解决了人工装卸刀头的低效和高风险问题,并且整体式反锪刀刚性比分体式更高,能有效减小加工振动,提高零件质量。
5. 结语
通过设计专用刀具来加工深孔、多特征孔和反锪孔,解决了特征孔加工周期长、加工效率低的问题。以某外贸型号为例,进行加工效果对比。
(1) 特征孔实际加工总计缩短时间为2742min,较原工艺减少 90.28% ,已达到高效加工预期。
(2)专用刀具中的内冷孔可以有效冷却加工区域,并且专用刀具的刚性更高,能够降低加工中的振动,保证零件的光洁度和粗糙度。 专用刀具具有多特征加工能力,使工序集中,减少人为干预,提高容错率,保证零件的加工质量。 实际加工中,φ68mm 的深孔表面粗糙度可达 Ra1.6甚至更好,其他孔径尺寸也符合要求,超差率为 0,位置度无超差。使用专用刀具达到预期目的,提高了零件的合格率。
投稿箱:
如果您有机床行业、企业相关新闻稿件发表,或进行资讯合作,欢迎联系本网编辑部, 邮箱:skjcsc@vip.sina.com
如果您有机床行业、企业相关新闻稿件发表,或进行资讯合作,欢迎联系本网编辑部, 邮箱:skjcsc@vip.sina.com
更多相关信息
- target=_blank>一种利用普通车床加工球面的车刀工装设计
- target=_blank>薄壁零件加工车床夹具设计
- target=_blank>机加工绿色转型数字化实践:基于现场的切削液寿命快捷管理
- target=_blank>刀具轮廓对滚齿磨损特征的影响分析
- target=_blank> 数控铣削加工中刀具补偿的应用研究