刀具轮廓对滚齿磨损特征的影响分析
摘要: 滚齿加工技术在外齿轮的制造中占据重要地位, 它是将运动学和刀具轮廓修正技术相结合的一项技术。 齿轮加工前,尽管刀具轮廓的初始配置是由相关标准规定好的,但在实际操作中常常需要改变刀具轮廓以满足齿轮对强度和接触比的要求。 用这些已修正轮廓的刀具加工出的齿轮, 其几何形状和磨损特征会相应改变。 现常用的修正轮廓刀具加工技术基于操作人员的经验所定,没有系统的标准和依据。 本文总结了刀具轮廓对磨损机制的影响,结合各种不同的刀具轮廓和齿轮几何形状在加工中进行了测试。
关键词:滚齿加工;刀具轮廓;磨损特征;模拟齿轮磨损
1、引言
现代高性能齿轮箱一般需要专门设计齿轮的几何形状,以满足特殊工程机械应用需求[1]。专门设计的齿轮,主要是为了提高齿根强度、降低啮合噪音。 通过改变压力角或者增加齿轮轮廓来增强齿的强度,通过增加齿轮之间的接触比降低齿轮的啮合噪音。 通常,增加齿高或齿轮的螺旋角可以实现更大的接触比;改变啮合角或调整齿轮轮廓几何形状来提高齿根强度;或者增加齿轮与齿轮之间的接触面积和啮合度来减小啮合噪
音[2,3]。
通常, 滚齿工艺的设计符合齿轮的外形几何要求(用于硬加工或直接应用),并优化制造成本[4-6]。 为了获得量身定制的齿轮,需要定制标准化的刀具轮廓, 这些刀具往往随着使用过程发生一定的磨损, 这必然影响齿轮的加工精
度。
2、过程模拟
通过传动装置模拟切削负载对刀具轮廓磨损的影响,证明产生的磨损现象和刀具寿命相互关联。 齿轮加工仿真软件能够提供数字化的切削长度、切屑厚度、间隙等信息,还有每个单独点的角度和接合切削刃所生成的位置。 此外,最大相对刀具尖端切屑去除量描述了前刀面尖端区域的变形载荷。 一维载荷参数的有关理论不能完全解释所测试齿轮箱的磨损行为。 滚齿过程的一个特征是背离沿切削刃的切屑厚度,单个切片的厚度可达到 5~300 mm, 有限元模拟中的切削单元尺寸的增加不会减少计算时间。 滚齿过程的FEM 模拟见图 1。
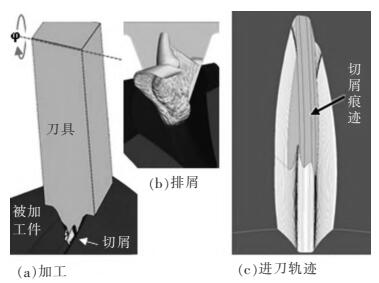
图1 滚齿过程的 FEM 模拟
3、检测结果
3.1 尖端半径对磨损的影响
从具有尖端的标准参考刀具配置文件中派生出尖端半径为ρaP 0=0.2mn,mn 为刀具法向模量。在尖端半径使用值为ρaP 0,1=0.2mn 的情况下,对不同尖端半径ρaP0,2=0.3mn 和ρaP 0,3=0.4mn 的磨损影响进行分析。
在切割测试中,增加尖端半径的情况下将影响刀具寿命。 根据刀具寿命,水平进刀的切割速度也随着半径的增大而提高。 将尖端半径从0.2mn 更改为 0.4mn,Vc 的值根据框架条件增加了7%到 30%。 啮合时,尖口磨损更集中在前刀面尖端区域的小尖端半径的轮廓处。 尖端半径的增加与齿尖磨损关系对比见图 2。
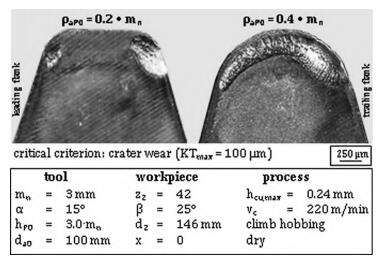
图 2 尖端半径对齿牙形状磨损的影响
尖端半径对齿轮磨损的影响与切片变形有关。 在滚齿过程中,切屑材料中从尖端和侧面方向流过前刀面,当尖端半径很小时,切屑物料流在两齿面间流过,切片材料在那里得到压缩和变形;尖端半径较大时,前刀面上的变形量降低,此尖端区域产生的切片体积的比率减少,意味着具有较大尖端半径的刀具将减少整体变形载荷。
3.2 刀具轮廓角对磨损的影响
在滚齿快速切削模拟中,根据边界条件轮廓角取ρaP0,1=158和ρaP0,2=208时,这种齿轮轮廓的改变会导致不同的磨损效果。 在有限元仿真加工过程中,一定切削弧度下排屑时刀具前端温度的变化情况见图 3(通过前刀面方向观看),温度增加, 具有较大轮廓角度刀具的临界月牙磨损更快,切削速度下降 5%。
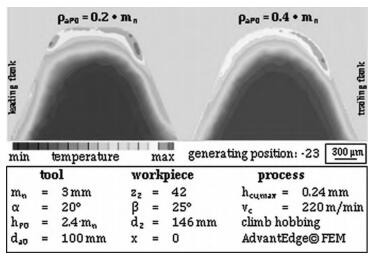
图 3 尖端半径对模拟前刀面温度的影响
通常,较大的轮廓角导致齿轮侧翼的间隙角增大。 经仿真模拟显示,有效间隙角在整个侧翼范围内从起始尖端半径增加到尖端半径最大值。实际模拟侧翼的间隙角从 2.25°增加到 3.0°,当侧翼角度增加时,较大的切削后角减少了刀具后刀面和工件材料之间的摩擦负荷,使刀具侧面磨损速度变慢,见图 4。
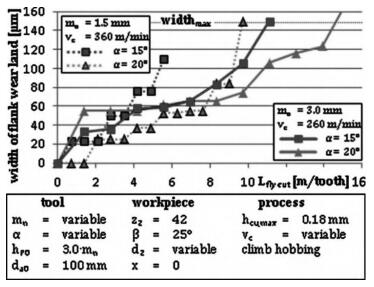
图 4 轮廓角对后刀面磨损发展的影响
除了间隙角的变化规律, 当增加轮廓角度时,切割长度减少,导致刀具寿命增加。 预估轮廓角度从 158 增加到 258,相应地,刀具增加 6%~18%的进刀切割速度。
3.3 齿轮螺旋角对磨损的影响
螺旋角作为工件的几何尺寸决定参数,对刀具的磨损有较大影响。 实验对象除了螺旋角为25.8°的标准齿轮外, 还参考了螺旋角为 0°的正齿轮。
在这两个研究案例中,正齿轮导致刀具寿命减少,相应地,月牙磨损导致后刀面焊盘宽度磨损,如图 5 所示。
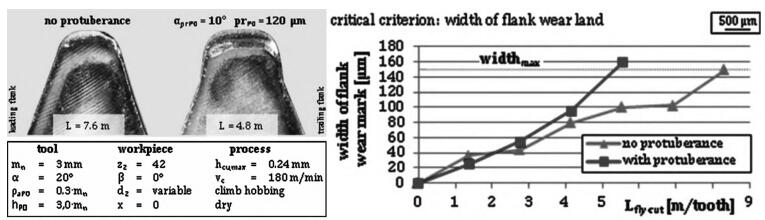
图5 突起的磨损影响
月牙磨损较早地出现在轮齿的前侧翼区域内。 此外,后刀面磨损发展得更快,第一次切割齿轮会导致更多的磨损。
特别注意极端的后刀面磨损现象,这种现象主要是切削长度(+32%)和切屑厚度(+5%)减少了螺旋角。 在此之后,切片体积也增加,切屑体积增加后刀尖端区域的总负载也相应增加,反映在前刀面上负载的差异,如图 6、图 7 所示。
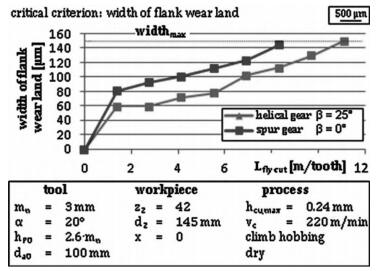
图 6 螺旋角对磨损发展的影响
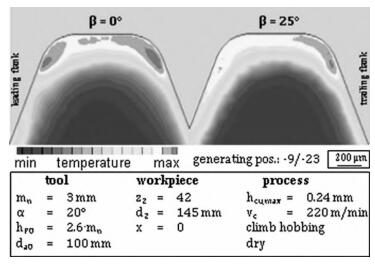
图 7 螺旋角对前刀面温度(FEM)的影响
水平切削切割正轴时,速度设置为较低水平(Dvc10=8%~32%),齿轮与斜齿轮的切割量比较稳定。
4、结论
在滚削中改变刀具轮廓或齿轮螺旋线的角度均会引起刀具寿命改变。
对齿轮加工过程中的不同磨损机制和磨损行为变化进行建模,通过有限元模拟分析,在加工新的齿轮时,无需再次进行过程模拟即可评估刀具轮廓。
根据评估后的齿轮加工刀具设计标准,应用优化后的滚齿工具,选择相应的切削参数,能够降低加工成本。
来源:(1. 中国煤炭科工集团 太原研究院有限公司 2. 山西天地煤机装备有限公司, 3.煤矿采掘机械装备国家工程实验室 )
投稿箱:
如果您有机床行业、企业相关新闻稿件发表,或进行资讯合作,欢迎联系本网编辑部, 邮箱:skjcsc@vip.sina.com
如果您有机床行业、企业相关新闻稿件发表,或进行资讯合作,欢迎联系本网编辑部, 邮箱:skjcsc@vip.sina.com
更多相关信息
- target=_blank> 数控铣削加工中刀具补偿的应用研究
- target=_blank>切削参数对金属切削刀具磨损与寿命的影响
- target=_blank>TF2000 型数控不落轮镟床刀具补偿调整方案研究
- target=_blank> 数控加工中心多把刀对刀方法分析
- target=_blank>基于 SINUMERIK 828D BASIC 数控系统的 三轴五面铣床立卧刀库换刀的用户界面开发