加工中心主轴松拉刀功能的优化控制
摘要:松拉刀控制作为数控机床主轴系统的核心功能对加工中心运行的稳定性和可靠性都有重要意义。针对加工中心运行中可能出现的机床运行前未紧刀、主轴运行中松刀、刀库换刀前刀具异常以及手动松刀误动作等松拉刀故障在 PLC 控制系统中设计相应的优化,实现在机床电气控制端对机床机械故障进行防控的优化功能。重点优化圆盘式刀库换刀机械手在换刀过程中由于换刀机械手动作未到位引起的松拉刀故障。优化功能在 KND 2000 Ci数控系统加工中心上进行了可行性验证,控制效果佳。
关键词 :松拉刀 主轴系统 PMC 设计
1、引言
加工中心主轴系统的松拉刀控制功能用于实现主轴上刀具在自动换刀及手动工作方式下松刀与紧刀的操作。自动松拉刀系统是主轴系统的核心组件,加工中心正常工作时,主轴通过内部的拉刀爪拉紧刀具,刀具紧紧地卡在主轴上;加工中心在手动换刀或者自动换刀时,气动系统提供松刀力压缩主轴内部的拉刀爪,主轴刀具被松开[1-2]。试验机床选用台湾 HSK BT40 拉刀爪(见图 1),最大可提供 18kN拉刀力,65Nm 锁紧扭矩,打刀行程 6mm。选用亚德客 NPM 3.5T 打刀气缸(见图 2),出力 3.5 T,打刀行程 13mm 以内,顶刀量在 0.4~0.7mm 之间。
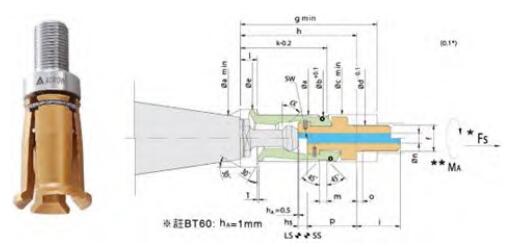
图 1 主轴松拉刀结构
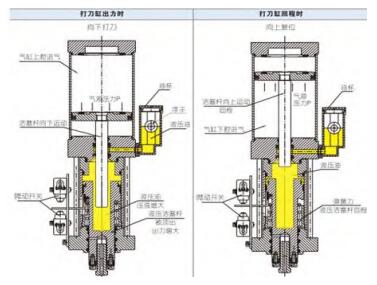
图 2 打刀气缸工作原理
2、松拉刀控制功能
主轴松拉刀功能的基本控制目标是拉紧刀具时,要求刀具必须在主轴上卡紧,不得松动;松开主轴刀具时,松刀动作要快速稳定且可靠性高。加工中心主轴自动松拉刀控制常规的功能如下:
(1)自动运行(AUTO)和 MDI 方式:主轴停止状态下,实现任何位置的松刀和拉刀操作。
(2)手动方式(JOG):由一个按钮实现主轴松拉刀控制:按下按钮时,松刀输出;松开按钮时,紧刀输出。由非手动方式转为手动方式时,总是输出拉刀信号。由手动方式转为非手动方式时,保持手动方式下松拉刀状态[3-4]。
3、加工中心松拉刀功能优化控制
由上所分析,松拉刀功能与主轴运行、换刀动作密切相关,除常用的预警外,为防止加工中心主轴在运行过程中出现刀具掉落,圆盘式刀库中换刀机械手在换刀过程中出现撞刀或者由于松刀未到位导致换刀失败等故障,特别是加工中心运行中松刀动作的误操作很容易造成的严重故障[5-6],本文探讨了加工中心的松拉刀额外的优化控制功能。
(1)防止手动松刀按钮误动作优化:设定松拉刀手动按钮在 1 秒之内人为或者系统线路异常跳动3 次,即视为异常,系统报警。
PLC 控制梯形图如图 3 所示:X0.0 是松拉刀手动按钮的输入信号,DIFD2 指令捕捉 X0.0 的下降沿信号并置中间变量 R200.1=1,R200.1 信号触发定时器 TMRB T2 工作;X0.0 同时触发 CTR 计数器ACT 输入信号,计数器启动,CTR 计数参数=3;在 T2 定时器 1s 时间之内,计数器 CTR 指令记录手动松刀按钮信号的跳动值,当手动松刀按钮指令跳动次数超过 3 次时,中间变量 R200.3=1,R200.3触发系统报警;当在 T2 定时器到达 1s 后,中间变量 R200.2=1 触发 CTR 指令的复位端口 RST 信号,计数器 CRT 重新计数。
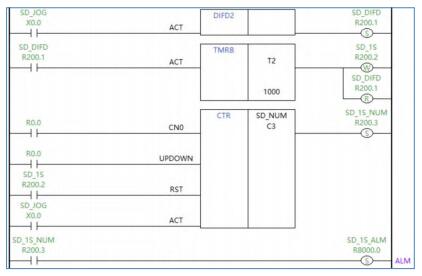
图 3 手动松刀按钮误动作优化
(2)主轴运动过程中,防止松刀信号误输出优化:如果主轴处于旋转状态,系统收到松刀指令,或者手动松刀按钮被误操作,系统报警,主轴进入复位状态[7-9]。
PLC 控制梯形图如图 4 所示:F2001.0、F2001.1、F2001.4 分别是主轴正转、反转、点动状态的系统反馈信号,三个信号负逻辑信号触发中间变量R100.0 再次取反,负负得正,则 R100.0 表示主轴处于旋转状态;F30.0、F30.1、F30.2 分别是 X/Y/Z轴移动的系统反馈信号,定义 R7.2 为机床处于手动、手轮或者回零工作方式状态, M50 为系统松刀指令,M51 为拉刀指令。控制逻辑为:如果系统主轴在旋转状态,或者 X/Y/Z 轴处于移动状态下, X0.0手动松刀按钮或者 M50 松刀指令试图触发主轴松刀时,系统报警被触发,主轴进入复位状态。
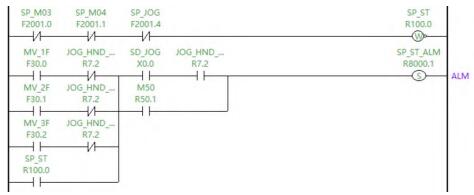
图 4 主轴运动过程中,防止松刀信号误输出优化
(3)机床准备启动运行前,刀具处于未紧刀状态优化:机床启动运行前,如果主轴刀具处于松刀或者紧刀动作未到位状态,系统发出主轴旋转指令M03/M04 或者手动方式下主轴正反转及点动;或者系统发出 X/Y/Z 轴移动指令,系统报警,机床复位[10-12]。
PLC 控制梯形图如图 5 所示:G15.1 是刀具松刀到位输入信号,G15.2 是刀具紧刀到位输入信号。在系统试图运行主轴或者移动 X/Y/Z 轴前,检测系统是否收到松刀到位或者紧刀未到位信号,如果是,则系统报警触发。
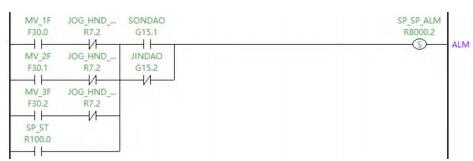
图 5 机床准备启动运行前,刀具处于未紧刀状态优化
(4)换刀动作前,刀具处于异常状态优化:加工中心换刀前,如果主轴刀具处于松刀或者紧刀动作未到位状态,系统发出换刀指令,M06 或者手动方式下换刀,系统报警,换刀指令不执行。PLC 控制梯形图如图 6 所示:中间变量 R50.6是 M06 换刀指令的译码变量,DIFU2 指令取 M06指令的上升沿信号触发中间变量 R300.0。在系统执行 M06 指令前,检测系统是否收到松刀到位 G15.1或者紧刀未到位 G15.2 信号, 如果是,系统报警触发,机床复位。
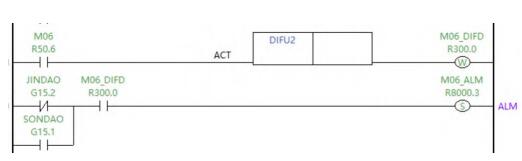
图 6 换刀动作前,刀具处于异常状态优化
(5)换刀机械手停止位置异常优化:圆盘式刀库松拉刀优化控制,防止换刀机械手动作停在刀臂原点和扣刀位置的中间,出现撞刀故障。
圆盘式刀库换刀过程中,换刀机械手在自动工作方式下动作如下(见图 7):换刀动作开始前,换刀机械手处于原点位置;系统发出 M06 换刀指令,换刀机械手第一次动作开始;当系统收到机械手第1 次扣刀到位信号,机械手停止输出,并自动进行松刀输出(见图 8);系统检测到松刀输出到位信号后,换刀机械手第二次动作开始;当系统收到机械手第 2 次扣刀到位信号,机械手停止输出,并自动进行紧刀输出;系统检测到紧刀输出到位信号后,换刀机械手第三次动作开始;系统检测到机械手原点信号后,机械手停止输出[13-14]。
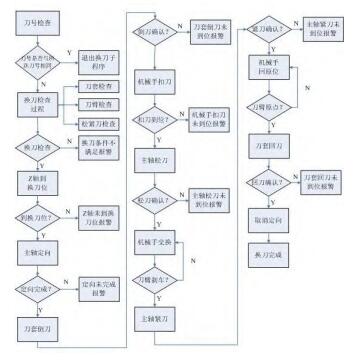
图 7 换刀机械手动作流程
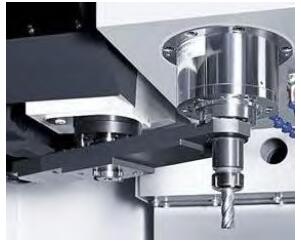
图 8 换刀机械手扣刀到位松刀输出
松拉刀动作必须和换刀机械手动作协同,让松拉刀动作发生在换刀机械手第二次动作的前后,松刀动作发生在机械手第二次动作的开始之前,紧刀动作发生在机械手第二次动作停止之后。优化控制的目的就是防止换刀机械手第二次动作停在刀臂原点和扣刀位置的中间,如果此时主轴执行松拉刀动作则会出现撞刀故障。如果换刀机械手第二次动作准备开始前,机械手扣刀信号没有到位,也即第一次换刀机械手动作停止时,换刀机械手没有停在扣刀位置;换刀机械手第二次动作结束后,机械手停止动作,可是机械手扣刀信号没有到位,也即第二次换刀机械手动作停止后,换刀机械手没有停在扣刀位置,上述情况下,松拉刀动作不能执行[15]。
PLC 控制梯形图如图 9 所示:换刀机械手在整个换刀过程中一共动作三次,定义 R2000.1 为机械手第一次动作结束状态,R2000.2 为第二次动作开始启动状态,R2000.3 为第二次动作结束状态,R2000.4 为第三次动作结束状态信号,定义 M56 为换刀机械手动作指令。在优化控制程序中,我们重点关注机械手第二次动作前后的机械手扣刀信号R2010.1 的状态。如果出现以下四种状态,都表示换刀机械手停在异常位置,是主轴松拉刀动作不能执行的条件之一:(1)当换刀机械手第一次动作结束状态复位 R2000.1=0,机械手第二次动作开始启动R2000.2=1,但是机械手扣刀信号未达到 R2010.1=0;(2)或者换刀机械手停止动作信号触发 R2000.5=1,但是换刀机械手第三次动作未完成 R2000.4=0,机械手扣刀信号也未到达R2010.1=0;3)加工中心MDI 工作方式下,主轴返回第二参考点信号未达到F50.2=0;4)加工中心 AUTO 运行工作方式下,换刀机械手臂未回到零点位置 R2010.0=0。
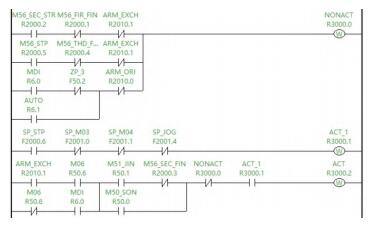
图 9 防止换刀机械手停止位置异常优化
此外,还可以将上述优化功能的 2 和 4 的加载至圆盘式刀库换刀的优化控制功能中,也即主轴旋转或者扣刀信号未达到时,主轴松拉刀动作不能执行。故有,松拉刀动作不能执行条件之二:如果主轴处于旋转状态,F2000.6=1 是主轴静止状态反馈信号,并且系统 F2001.0 主轴正转、F2001.1 主轴反转、F2001.4 主轴点动的反馈信号都为 0 的状态下,认为主轴处于绝对静止状态,输出 R3000.1 信号。松拉刀动作不能执行条件之三:扣刀信号未达到R2010.1=0,M06 换刀指令不能执行;扣刀信号达到 R2010.1=1,M06 信号才能执行。中间变量R3000.2 是松拉刀动作可以执行的条件,当换刀机械手处于正常位置 R3000.0=0,主轴处于非旋转状态 R3000.1=0,则 M50/M51 松拉刀指令可以执行。
4、结语
以往对于主轴松拉刀控制功能的优化大多围绕于主轴松拉刀机械结构的改进与优化,以提高主轴系统的稳定性与可靠性,利用电气 PLC 控制功能预警主轴松拉刀异常动作的优化方面(如图 10),涉及文献甚少。本文以松拉刀按钮误动作、主轴启动保护、机床运行启动保护、换刀准备动作保护、以及圆盘式刀库换刀过程中的换刀机械手停止位置异常保护为优化目标展开,所有优化程序在 KNDK2000 Ci 数控系统加工中心上进行了可行性验证,都得以实现且控制效果佳。
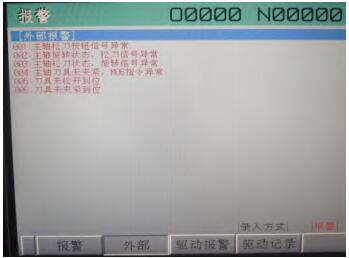
图 10 KND 数控机床试验报警
投稿箱:
如果您有机床行业、企业相关新闻稿件发表,或进行资讯合作,欢迎联系本网编辑部, 邮箱:skjcsc@vip.sina.com
如果您有机床行业、企业相关新闻稿件发表,或进行资讯合作,欢迎联系本网编辑部, 邮箱:skjcsc@vip.sina.com
更多相关信息
- target=_blank>误操作导致自动换刀系统故障典型案例分析
- target=_blank>DMU70E加工中心双刀链刀库的维修与调整
- target=_blank>基于HT665车铣复合加工中心刀库常见故障与维保方案研究
- target=_blank> FANUC 高速加工功能在模具加工中的应用
- target=_blank>西门子 828D 刀库功能解析及实现