采用机器人上下料的轮毂夹具设计与分析
【摘要】: 工业机器人越来越多的应用到智能制造领域,最典型的应用之一就是配合数控机床实现机床自动上下料,从而实现一定程度的无人值守,提高生产效率,降低人工成本。结合实际情况,本文首先对机器人进行了选型,然后对夹具进行设计和分析,为系统制造提供依据。
机器人技术是机械、电子、软件等多学科交叉融合的新技术,不仅是工科领域最具代表性的前沿交叉学科之一,也是我国重点发展战略领域之一,随着我国科技的不断进步和制造业的不断升级,采用工业机器人代替人工生产,实现自动化、无人化、智能化,可以有效降低企业生产成本,提高经济效益。本文在选定成熟机器人的基础上,针对零件具体情况,设计合适的夹具以实现整个机器人上下料系统的功能。本文采用 SolidWorks软件进行夹具的设计和分析,SolidWorks 是世界知名的三维设计软件,功能强大,集设计、仿真、渲染等功能于一体,能够方便快捷实现产品设计跟优化。
1. 机器人上下料系统整体设计
如图 1 所示,数控车加工中心为主体设备,机器人放置在车床正前方,机器人左侧可设置传送线用于待加工零件的来料,机器人右侧可设置传送线用于已加工零件的走料。机器人跟车床之间通常需要留有约 1 米的间距,如果机器人出现故障,可临时沿用传统的人工吊装等方式实现上下料,不耽误生产。
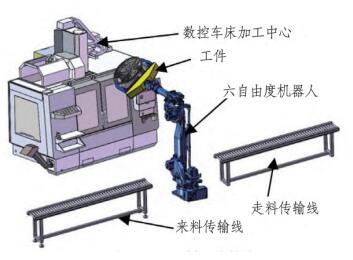
图 1 机器人上下料系统整体
2. 工业机器人
工业机器人根据用途有不同的类型可以选择,本文中上下料需要机器人有更多的自由度,因此本文选择六自由度机器人。由于零件重量为46kg,夹具重量假设跟零件重量相当,则机器人末端负载约 100kg。考虑机器人高速运动带来的额外负载以及价格因素,本文选用四大家族之一的安川 GP110 机器人。安川作为机器人品牌全球四大家族之一,其产品性能稳定可靠,功能强大。该款机器人运动半径高达 2236mm,具体技术参数如图 2 所示。
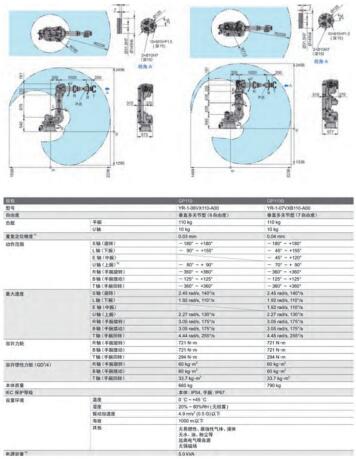
图 2 机器人主要技术参数
3. 夹具设计
夹具作为系统的主要部件之一,在设计的时候需要确保其稳定可靠。首先,需要分析被夹持工件的特点,被夹持的工件是回转件,其材料为铝合金,其重量约 46kg,夹持的时候不能损伤工件表面。其次,分析夹持要求,夹持的时候需要同时考虑夹持和定位,工件被定位后才能准确抓取到机床上。基于上述条件,夹具的构想方案如图 3 所示,夹具具备两个夹持板,夹持板上设置 2 个能够滚转的轮子用于夹持过程中工件跟夹具实现自适应定心。同时,夹持板能够在夹具基座上相对滑动,并且需要保持一定的刚性。
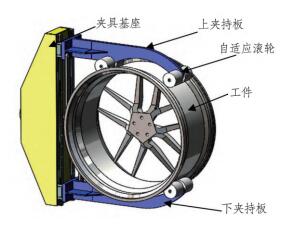
图 3 夹具方案
加工生产,效率是非常重要的因素之一,为了提高夹持响应,本文采用连杆驱动的方式,驱动夹持板的夹持和松开动作。同时,为了实现夹持定心,则需要两个夹持板能够绕夹具中心同步夹持和张开。为此,连杆采用中心对称的双曲柄滑块机构实现。夹具上的两个夹持板即为机构对应的滑块,如图 4 所示。
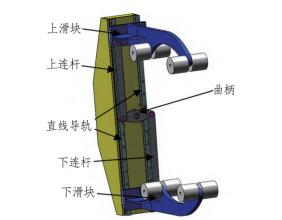
图 4 双曲柄滑块机构
4. 夹具计算及分析
(1)驱动电机计算及选择
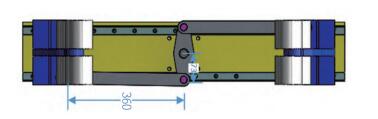
图 5 连杆尺寸
如图 5 所示,驱动轴旋转带动曲柄旋转,曲柄带动连杆拉动滑块运动,在图示处实现夹具对轮毂的夹持,此时曲柄垂直连杆,输出力最大。
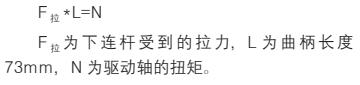
分析连杆受到的拉力,乘上一定的安全系数就能得到驱动轴所需要的扭矩,在图 5 所示状态下,下连杆受到的拉力最大,为一侧夹持板及滑持板、滑块、工件的重力合计约 550N。注意到,上夹持板及滑块的重力同样通过上连杆作用到驱动轴上,因此还需要增加上夹持板及滑块的重力约 90N,作用在驱动轴上的重力总共约 640N。则驱动轴需要的扭矩为
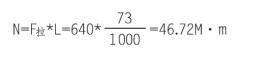
取 2 倍安全系数则驱动轴需要的扭矩约93N · m。假设夹持过程需要耗时 1s,夹持过程驱动轴需要旋转 60°。则驱动轴所需转速为 10r/min。电机所需要功率如下 :

考虑后期提速并且保留更多余量,电机选用松下 200W 伺服电机,配置速比 150 的减速机。电机及参数如图 6 所示。
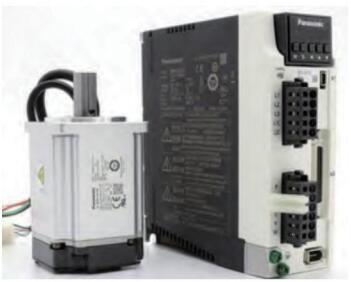
图 6 伺服电机及参数
(2)直线导轨的选择
根据上文中计算,直线导轨主要需满足扭矩需求,为确保夹具刚性,直线导轨在 100N·m扭矩基础上再取一定安全系数选择 IAS23-H42-L600 型直线导轨,其行走方向扭矩高达550N · m。具体参数如图 7 所示。
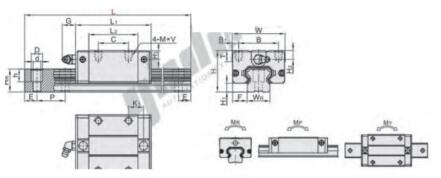
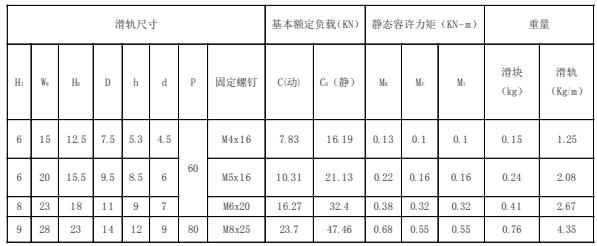
图 7 直线导轨参数
(3)夹持板仿真
仿真采用三维软件自带插件 ——Simulation,Simulation 是 SolidWorks 公司推出的一套有限元分析软件。它作为嵌入式分析软件与 SolidWorks 无缝集成,运用simulation,普通工程师就可以进行工程分析并可以迅速得到分析结果。
夹具的导轨有具体的参数指标,而且按照很高的安全系数选取,因此不需要担心性能。夹持板为关键零件且为自制件,需对其进行仿真分析,上下两个夹持板完全对称,因此,对一侧夹持板分析即可。
对需要仿真的模型参数进行设定,确定零件实际受力方式,如图 8 所示。夹持板底座固定在导轨滑块上,两处安装滚轮的夹持轴孔受到夹持的反作用力。因此,设定夹持板底座为固定,设定夹持轴孔受力,根据角度分布,其合力为工件的重力 460N,取一定安全系数,取每个夹持孔受力大小为 300N,方向垂直圆弧切面且反向指向圆心。
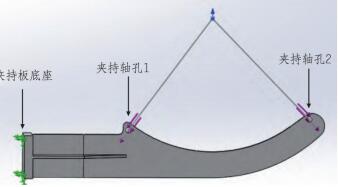
图 8 夹持板参数设定
准备好模型后,对其进行网格划分,如图9 所示。
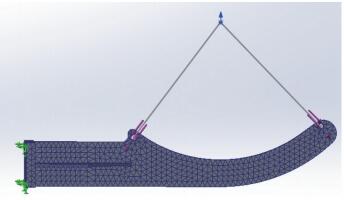
图 9 夹持板网格划分
网格划分好后就可以开始仿真,仿真结果如图 10、图 11 所示。可以看到,夹持板的强度和刚性均满足要求。
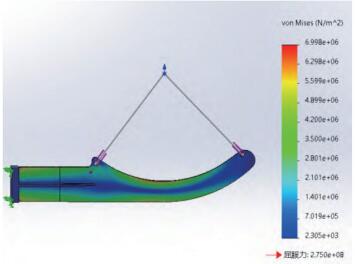
图 10 夹持板强度仿真结果
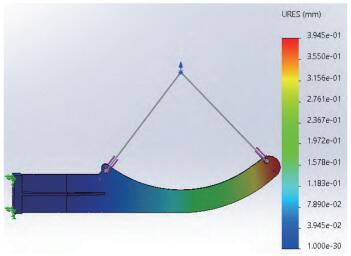
图 11 夹持板刚度仿真结果
5.结论
本研究通过 SolidWorks 绘制夹具的三维模型,并且通过计算和仿真确定了夹具的器件及关键自制件满足设计要求,为机器人自动上下料系统的夹具制作及系统制作提供了理论依据,为用户提供一种基于三维建模的快速夹具设计环境。
投稿箱:
如果您有机床行业、企业相关新闻稿件发表,或进行资讯合作,欢迎联系本网编辑部, 邮箱:skjcsc@vip.sina.com
如果您有机床行业、企业相关新闻稿件发表,或进行资讯合作,欢迎联系本网编辑部, 邮箱:skjcsc@vip.sina.com
更多相关信息
- target=_blank>钛合金薄壁件 3D 打印工艺技术
- target=_blank>高速切削在铝合金变速器壳体加工中的应用研究
- target=_blank>聚焦航空航天数智、高效生产——访巨浪中国 CEO 任家平先生
- target=_blank>FANUC 立式加工中心机械手刀库设计
- target=_blank>一种小直径刀具辅助水平夹持装置