高速微铣削铝合金铣削力与表面粗糙度研究
摘要: 随着航空航天技术的发展,微小零部件变得越来越重要,对制备具有表面质量好、尺寸精度高、加工误差小的微机械结构提出了新的挑战。通过高速微铣削技术在 7075 航空系列铝合金表面铣削微细直槽结构,以主轴转速、进给速度与轴向切深为研究因素,采用多因素正交试验与极差、方差分析法分别对铣削力和表面粗糙度进行研究。结果表明:铣削参数对铣削力的影响按从大到小依次为进给速度、轴向切深、主轴转速;增大主轴转速,减小进给速度和轴向切深可获得较小的铣削力与较高的加工精度;主轴转速对表面粗糙度 Ra 影响最大,进给速度次之,轴向切深对其影响最小;当主轴转速为 48000r/min,进给速度为 30mm/min,轴向切深为 20μm 时,高速微铣削铝合金微细直槽表面质量最优。
关键词: 高速微铣削;正交试验;铣削力;表面粗糙度
0 引言
随着航空航天、生物、医学、建筑、以及汽车制造业的发展,对微小机械的功能、结构复杂性、可靠性的要求越来越高,从而对加工具有一定尺寸精度和表面质量要求的精密三维微小零部件的需求也越来越广泛。高速微铣削技术以其加工精度高、工艺简单、材料约束少、加工效率高,可实现复杂形状三维微小结构的加工等优点在国内外得到了大量应用。
近年来,铝合金材料由于其塑性好、强度高、重量轻以及具有优良的导电性、导热性和抗腐蚀性等特性被广泛地应用于航空航天制造领域中。为减少飞机的重量和提高其使用性能, 在飞机结构设计中大量采用铝合金制备梁、肋、桁条、隔框、整体框架和起落架等结构,但是,这类结构件的刚度较低,对于低刚度的复杂构件,加工时由于切削力、切削热以及主轴跳动等原因很容易发生变形,严重的影响了工件的加工质量和表面精度。因此要提高低刚度构件的加工质量与精度,就要减小工件在加工过程中的变形。经过大量分析得出切削力是引起加工变形的一个主要原因,因此减小切削力就可以有效减小低刚度构件的加工变形。李艳聪等采用直径为 16mm 的铣刀对不锈钢、铝合金的平面加工精度进行了研究,得出了切削力与切削参数的关系。但是,对于微米级结构件铣削力的研究却很少。本文采用直径为 0.2mm 的微径铣刀在铝合金表面加工微细直槽结构,采用正交试验研究铣削参数对铣削力与表面粗糙度的影响规律并进行参数优化,最终得到最优铣削参数使加工表面质量最优。该研究为获得表面质量好、尺寸精度高的微小零部件的高速铣削加工提供了依据。
1 试验研究
1.1 试验条件
该铣削试验采用课题组自行研制的小型高速微铣削机床,主轴最高转速可达 100000r/min,主轴回转精度为 1μm,工作台位置精度为 ± 0.5μm/100mm,重复定位精度为 ± 0. 2μm;采用 Kistler 三向动态压电测力仪、5070A 电荷放大器和计算机数据采集系统测量与记录铣削力;利用 MarSurf LD120 轮廓与粗糙度测量仪测量微细直槽底面的粗糙度;刀具选用双刃整体硬质合金涂层微径立铣刀,刀柄和刀刃直径分别为 4mm 和0.2mm,刃长为 0.5mm,螺旋角为 45°,刀尖圆弧半径为 10μm,涂层材料为 TiAlN;工件材料为 7075 航空系列铝合金;铣削加工过程中采用油雾润滑与冷却。图
1 为铣削力测试系统原理图。
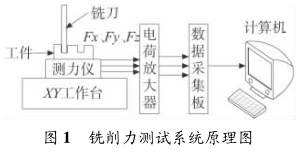
1.2 试验方法
在 5052 铝合金表面加工微细直槽结构如图 2 所示,采用全径向铣削方式,即直槽宽度与铣刀直径相等。选取主轴转速 n、进给速度 vf、轴向切削深度 ap三个参数作为研究因素,采用三因素四水平正交试验表L16(43)研究铣削参数对铣削力和表面粗糙度的影响规律,通过极差与方差分析法得到铣削力和表面粗糙度较小的因素水平组合。正交试验各因素的水平值根据试验经验选取,如表 1 所示。
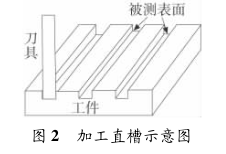
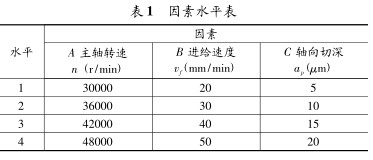
2 试验结果与分析
正交试验方案与极差分析结果如表 2 所示,方差分析结果如表 3 所示,每组参数重复进行三次,对本试验中测得的铣削力数据进行噪音去除处理,其中 Fx、Fy、Fz 为铣削力在 X、Y、Z 三个方向的分力,Ra为直槽底部的表面粗糙度。根据表 2 中所测的各铣削分力值可以看出,高速微铣削铝合金微细直槽时所产生的铣削力都很小,Fx 最大为 0.063N,Fy 最大为 0.099N,Fz最大为 0,076N。
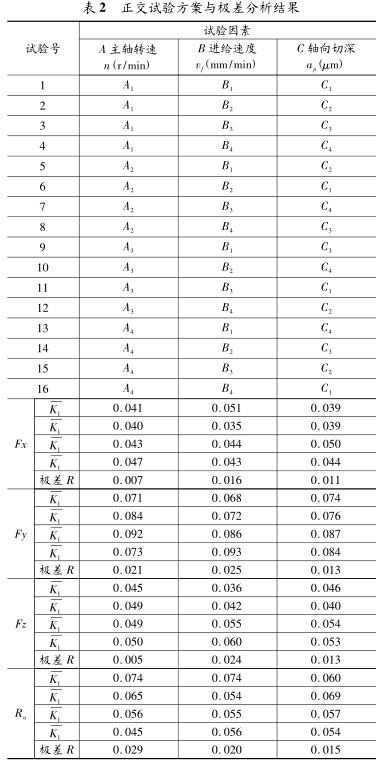
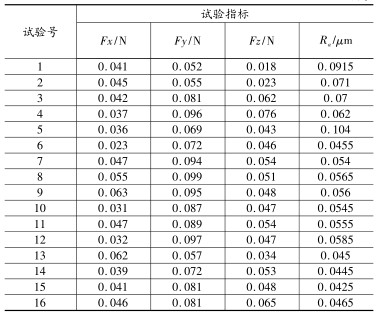
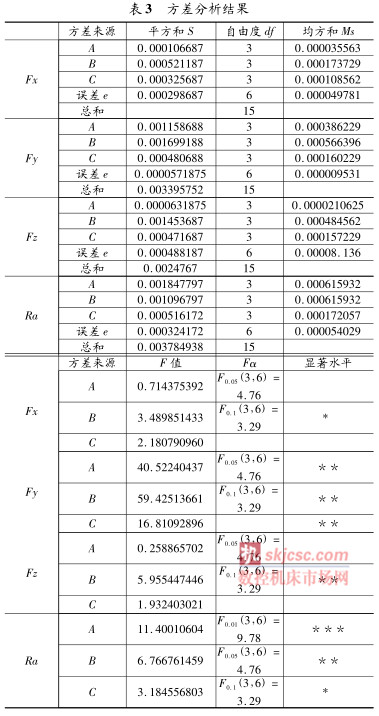
2.1 铣削力分析
图3 为采用 MATLAB 软件由极差分析结果(表 2)生成的铣削参数与各铣削分力的关系曲线图。从图中可以看出,铣削分力 Fy 最大、Fz 次之、Fx 最小。由方差分析结果(表3)可知,铣削参数对铣削分力的影响存在明显差异,各参数对主切削力 Fy 影响最大,轴向力 Fz次之,径向力 Fx 影响最小。铣削时,由于切削变形与摩擦,铣刀每一参与切削的刀齿上都受到铣削力。为了实际应用,通常假定各刀齿上的铣削力的合力 F 作用于某个刀齿上,并将它分解为三个相互垂直的分力:主切削力 Fc 、径向力 Fp、轴向力 Fo[铣削分力 Fx、Fy、Fz可近似等同于三个相互垂直的分力,即 Fx 对应于径向力 Fp、Fy 对应于主切削力 Fc、Fz 应于轴向力 Fo。主切削力 Fc(Fy)是主运动切削速度方向的分力,是最大的一个分力,它消耗了切削总功率的 95% 左右,是设计与使用刀具的主要依据,并用于验算机床、夹具等主要零部件的强度和刚度以及机床电动机功率。轴向力 Fo(Fz)是轴向切深方向的分力,消耗了总功率的 5% 左右,是验算机床进给系统主要零部件强度和刚性的依据。径向力 Fp(Fx)是进给方向的分力,它不消耗功率,但在机床、工件、夹具与刀具所组成的工艺系统刚性不足时,是造成振动的主要因素。所以,各铣削分力按大小顺序排列依次为 Fy >Fz >Fx。
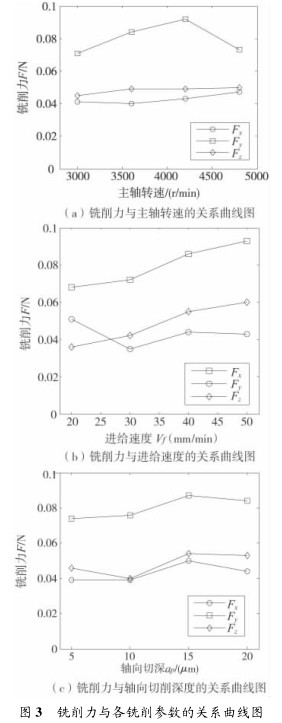
从图 3a 中还可以看出,Y 方向的铣削力随着主轴转速的增大呈开口向下的抛物线分布,随着主轴转速的增大而增大,在 n =42000r/min 时,铣削力达到最大值 0.092N,当 n > 42000r/min 时,Fy 随着主轴转速的继续增大而减小;主轴转速对铣削分力 Fx、Fz 的影响波动不大,整体呈缓慢上升趋势,即随着主轴转速的增大而缓慢增大;由图 3b 可知,铣削分力 Fy 与 Fz 的变化趋势相似,都随着进给速度的增大而增大,而铣削分力 Fx 呈二次曲线分布,即随着进给速度的增大,先减小后增大,最后又减小;由图 3c 可以看出,铣削分力Fx、Fy、Fz 的变化趋势相似,都呈抛物线分布,在 ap=15μm 时,铣削力同时达到最大值,但当 ap< 10μm 时铣削分力 Fx、Fy 随着轴向切深的增大而增大,而 Fz 正好相反,随着轴向切深的增大而减小, 当 ap> 10μm时, 三者的变化趋势相同。
由极差和方差分析结果(表 2 与表 3)及图 3 可知,进给速度对铣削力的影响最大,轴向切深次之,主轴转速最小;并且提高主轴转速,减小进给速度和轴向切深既可以获得较小的铣削力又可以得到较高的加工精度。
2.2 表面粗糙度分析
由表 2 与表 3 可以得出铣削参数与表面粗糙度 Ra的变化趋势,如图4 所示。从图中可以得出铣削参数对表面粗糙度 Ra的影响规律:随着主轴转速的增大表面粗糙度减小,分析其原因,其它加工参数不变时,高主轴转速下的切屑与刀具前刀面发生局部融化,形成一层保护膜,大大的减小了刀具前刀面的磨损和变形,同时也减小了切屑的变形时间,切屑快速的被切离工件并带走了70% ~80%的切削热,有效的减小了切削力;随着进给速度的增大表面粗糙度先减小后增大,这说明并不是采用越小的进给量得到的表面质量越好,分析其原因可能是刀具与工件之间的摩擦力和挤压力造成的,在vf=30mm/min 的时后,表面粗糙度达到最小值 0.054μm;从图中还可知轴向切深与进给速度的变化趋势正好相反,随着轴向切削深度的增加,表面粗糙度先增大后减小,在 ap=20μm 时,表面粗糙度最小,这可能是由于最小切削厚度 12- 15 效应引起的,当每齿进给量小于刀尖圆弧半径时无切屑产生,工件发生弹性变形并产生犁耕现象,使表面粗糙度增大。
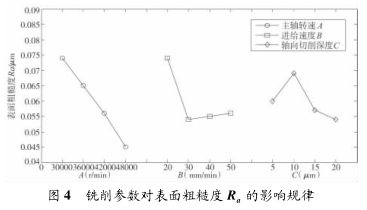
根据极差与方差分析法可知,铣削参数对表面粗糙度的影响程度按从大到小依次排列为主轴转速、进给速度、轴向切削深度。根据极差分析法可以求出最优组合为 A4B2C4,即 n = 48000r/min,vf= 30mm/min,ap=20μm 时,表面粗糙度最小,加工表面质量最好。
3 结论
通过多因素正交试验分析直径为 0.2mm 的微径铣刀铣削铝合金时的切削力与表面粗糙度,可以得出以下结论:
(1)对铣削力影响最大的试验因素是进给速度,其次是轴向切深,主轴转速对铣削力影响最小。
(2)提高主轴转速,减小进给速度和轴向切深可以获得较小的铣削力和较高的加工精度。
(3)各铣削参数对铣削分力的影响存在明显差异,各参数对主切削力 Fy 影响最大,轴向力 Fz 次之,径向力 Fx 影响最小,且各铣削分力按大小排列依次为:Fy > Fz > Fx。
(4)铣削参数对表面粗糙度的影响程度从大到小依次为主轴转速、进给速度、轴向切深。
(5) 当主轴转速为 48000r/min,进给速度为30mm/min,轴向切深为 20μm 时,高速微铣削铝合金微细直槽表面加工质量最优。
投稿箱:
如果您有机床行业、企业相关新闻稿件发表,或进行资讯合作,欢迎联系本网编辑部, 邮箱:skjcsc@vip.sina.com
如果您有机床行业、企业相关新闻稿件发表,或进行资讯合作,欢迎联系本网编辑部, 邮箱:skjcsc@vip.sina.com
更多相关信息
- target=_blank>采进口齿形链进行传动,车铣复合加工中心传动箱的设计
- target=_blank>基于M odbus协议实现施耐德PLC与变频器的通信
- target=_blank>滑动轴承还是滚珠轴承?—直线滚珠轴承与直线滑动轴承的比较
- target=_blank>减速器漏油原因分析及治理措施
- target=_blank>山特维克可乐满2015秋季刀具新品大阅兵