基于 PLC 的磨床砂轮动平衡系统研究
2020-4-5 来源:浙江大学 化工机械研究所 作者:张志新,万可达,付豫龙
摘要: 针对目前磨床砂轮动平衡方式难以同时满足易操作、高精度及低成本的要求,提出了一种以 PLC 为主机,单片机为从机的新型磨床砂轮动平衡系统。讨论了砂轮动平衡系统的整体结构、基于互相关分析的砂轮不平衡量提取、基于3 平衡块的不平衡校正方法,以及基于 RS-485 标准数据通信的主从机数据通信。通过搭建模拟砂轮试验台,验证了动平衡仪的可靠性,取得了良好的平衡效果。
关键词: 磨床; 动平衡; 互相关分析; 不平衡校正方法; 单片机; PLC; 触摸屏
砂轮是用磨料和结合剂树脂等制成的原型固结磨具,是磨具中使用量最大、使用面最广的一种。由于长时间的磨削工作导致质量分布不均匀而产生不平衡离心力,引起轴承的振动,影响工件的磨削质量,降低磨床的使用寿命,因此需要对砂轮进行动平衡。砂轮动平衡技术按自动化程度分成 3 大类[1]: 人工平衡,半自动平衡和自动在线平衡。人工平衡受平衡架导轨水平精度、滚动摩擦和装配误差的影响,砂轮平衡精度低,花费时间长。半自动平衡需要通用的现场动平衡仪作为测试工具,成本高、实时性低以及现场应用不便[2]。
目前自动在线平衡技术成本昂贵,因此,开发出一种新型的低成本砂轮现场动平衡测试系统具有重要意义课题组研制出一种以 PLC 为主机,单片机为从机的磨床砂轮动平衡系统。该系统采用主从结构,主机利用 PLC 和触摸屏,主要实现人机交互与动平衡过程监控,从机由单片机完成数据采集与不平衡量识别。通过基于 RS-485 标准的数据通信协议实现单片机与PLC 之间的通信,可解决上述 3 类动平衡方法的缺点,具有成本低,人机交互性好,通信可靠的优点。
1 、砂轮动平衡系统的整体结构
基于 PLC 的砂轮动平衡系统的整体结构框图如图 1 所示,主要由传感器模块、信号处理模块、单片机模块和主机控制模块 4 部分组成。振动传感器负责测量砂轮的振动数据,转速传感器负责获取动平衡所需的基准信号; 信号处理模块的功能包括信号采集和信号预处理; 单片机 STC12C5410AD 则主要负责数据采集、分析计算[3]; 主机控制模块包括 PLC 和触摸屏,主要负责人机交互和显示。PLC 和单片机采用 RS-485接口,采用无协议通信。

图 1 砂轮动平衡系统整体结构框图
整个动平衡系统的工作原理如下: 通过触摸屏控制 PLC 传送相应命令给单片机,单片机根据接收的命令执行相应的动作,主要有平衡测试及平衡计算。磁电式速度传感器吸附在砂轮附近用于拾取平衡所需的振动信号,光电式转速传感器对准粘贴有反光标签的砂轮来拾取平衡所需的基准信号。振动信号与基准信号经过测量放大、低通滤波、量程切换和直流偏置等预处理后进行 A/D 转换,单片机对经过预处理后的数字信号进行互相关运算、平衡解算,并将计算结果传送给PLC,再通过触摸屏显示。
2、 不平衡量提取和校正方法
2. 1 砂轮不平衡量提取
引起振动的原因有很多,除了不平衡质量引起的工频分量,还有转子不对中引起的二倍频分量、轴承引起的高频分量及随机噪声信号。其中,由不平衡量引起的工频分量是砂轮振动的主要来源。振动传感器拾取的振动信号,可表示为[5]:
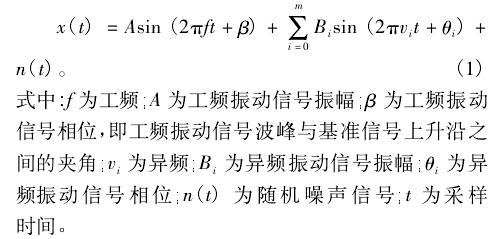
由于计算不平衡量的大小与相位需要从振动信号中提取工频分量,课题组采用整周期互相关方法来处理振动信号。该方法可以消除振动信号中除工频分量外的绝大部分异频分量,且运算量较小,具体过程如下: 以基准信号的任意一个上升沿为起点,从 N 个采样值中选取 k 个完整周期振动信号,将基准信号的上升沿作为零相位。以转子的工作频率 f 为频率,构造工频函数:
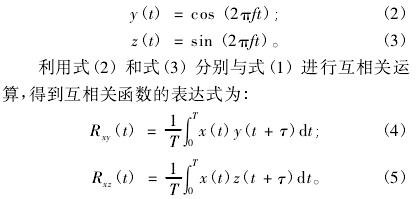
式中: T 为整周期采样时间; τ 为基准信号与振动信号的时差。
根据正弦函数系的正交性,振动信号中的异频分量与 y( t) ,z( t) 进行互相关运算后,幅值为 0,而噪音分量 n( t) 与 y( t) ,z( t) 进行互相关运算后,幅值也趋于 0。取延时 τ = 0,互相关函数可以近似表示为:
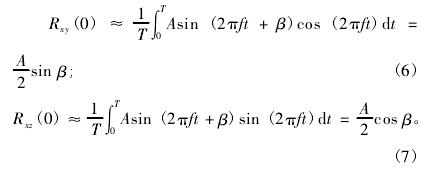
对于实际测试过程,通常是转换成离散数字信号进行处理,只能通过 N 个采样值来计算互相关函数的值,得到
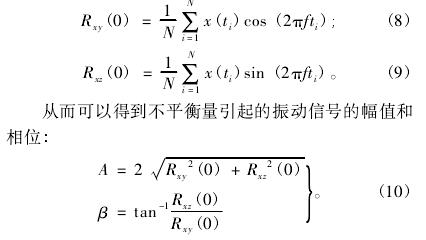
按照式( 10) 来分别计算 k 个周期的幅值和相位,取其平均值作为工频分量的幅值和初相位。
2. 2 砂轮不平衡量校正方法
根据计算结果所指示的位置[6],在砂轮法兰盘环形槽内相对应位置上安装 2 ~ 3 块平衡块( 配质量块) ,每块平衡块的质量与形状相同。在砂轮动平衡过程中,为使配质量位置准确,通常在法兰盘圆周上刻上角度值,如图 2 所示。图中光标位置为平衡块的角度基准,据此进行平衡块的调整以达到平衡。由于 2 个平衡块的平衡装置的精度和效率低下,一般工程上法兰盘采用3 个平衡块的装置。本实验中每个平衡块质量为23 g。
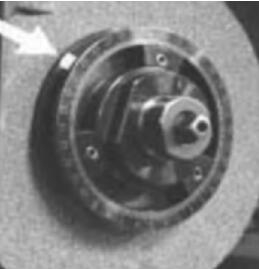
图 2 3 个平衡块的砂轮法兰盘
采用影响系数法计算出砂轮原始不平衡量的大小和角度后,首先让一块平衡块移动到加质量角度 φ处,然后调整剩余 2 个平衡块使其偏重质量等于加重质量( W) 和单个平衡块质量( M) 之差,具体操作见图 3。
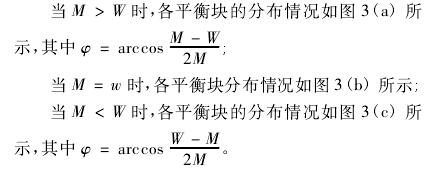
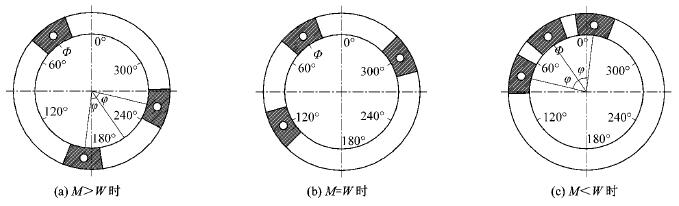
图 3 平衡块分布图
3 、通信协议
主机 PLC 和单片机( 从机) 之间采用无协议通信方式与 RS-485 接口进行通信[7-8]。MAX485 芯片 RO和 DI 端分别为接收器的输出和驱动器的输入端,分别与单片机的 RXD( 输入端) 和 TXD( 输出端) 相连即可; MAX485 芯片为半双工模式,因此只需要将单片机 的一个引脚P3. 3与MAX485的接收使能端和输出使能端连接来控制 MAX485 的接收和发送。PLC 的通信扩展口 FX3G-485BD 的 SDA 端子和 RDA 端子短接后与 MAX485 芯片的 A 端 子 相连接,SDB 端 子 和RDB 端子短接后与 485 芯片的 B 端子相连接。电路连接如图 4 所示。
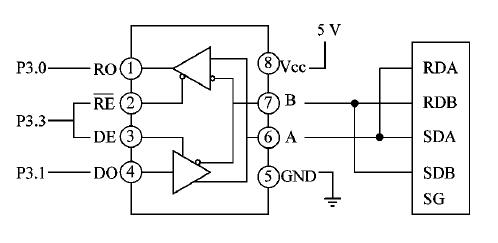
图 4 通信连接示意图
无协议通信[9]是仅需要对数据格式、传输速率及起始/停止码等进行简单设定,PLC 与外部设备之间进行直接数据发送与接收的通信方式,并非通信双方不要协议。在使用无协议通信时,首先要用到一个 16 位的特殊数据寄存器 D8120 来设置通信格式。D8120 的设置方法如表 1 所示。本文选取的通信格式如下: 数据长度为 8 位,无奇偶校验,1 个停止位,传输速率为4 800 bit / s,无起始位和结束位,无校验和,无协议通信 RS-485 接口。对照表 1,可以确定 D8120 的二进制值为 0000 1100 0111 0001,对应的十六进制数为 0C71。
通过触摸屏触发 PLC 发送命令码,单片机接收到命令后进行数据的采集和保存,然后通过互相关运算进行不平衡振动识别,进而通过频谱分析判断为动平衡问题之后,利用影响系数法计算出不平衡量的大小和相位,将其分解为 3 个给定质量的平衡块,最后向PLC 返回计算结果并显示在触摸屏上。命令码设置如表 2 所示,单片机根据接收到的命令码进行判断执行相应的程序和算法。
表 1 无协议串行通信格式

表 2 单片机功能码设置

在 PLC 与单片机进行数据通信时,采用命令/响应模式,一次通信收发的一组若干个字符作为一个信息帧。PLC 发送的帧格式只包含命令码; 当命令为振动测试时,PLC 的接收帧由 608 个字符组成,如表 3所示。
表 3 振动测试时 PLC 的接收帧

当命令为不平衡量计算时,PLC 的接收帧由 10 个字符组成,如表 4 所示。
表 4 不平衡量计算时 PLC 的接收帧
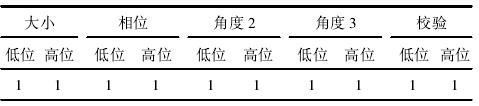
本文采用 CRC 校验方式,PLC 对从单片机传送回来的数据进行 CRC 校验,若校验成功,则将接收到的数据转移到其他寄存器地址显示到触摸屏上; 若不成功,则继续发送数据。
4 、系统软件设计
本系统采用主从机( Master-Slave) 结构,主机以FX3GA-40MR 为核心,通过触摸屏来触发 PLC,发送指令给 单 片 机 并 接 收 返 回 数 据 进 行 显 示。从 机 以STC12C5410AD 单片机[10]为核心,接收主机的指令,完成振动与转速信号的数据采集,由光电传感器来测量提供转速和基准信号,磁电式速度传感器来测量振动信号,测得的信号经过预处理传入 STC12C5410AD单片机,单片机对信号进行运算,并将计算结果传输给PLC。系统的软件功能如图 5 所示。该系统的软件模块主要由主从机通信模块、不平衡计算模块、数据存储模块、人机交互模块和显示模块组成。通信模块保证上、下位机数据的正常通信,不平衡计算模块负责从采集到的信号中识别出不平衡量与相位,数据存储模块负责保存数据,人机交互控制模块负责相关参数的输入以及测试系统的开启与关闭,显示模块将计算得到的数据和振动波形显示到触摸屏上。PLC、单片机和触摸屏分别负责不同的模块。

图 5 系统软件功能图
4. 1 PLC 软件设计
PLC 在整个系统中主要进行主动控制,通过 RS指令完成无协议通信。RS 串行通信指令是用来发送和接收串行数据的指令。指令中的[S]和 m 用来指定发送数据的地址和字节数; [D]和 n 用来指定接收数据的地址和字节数。基本格式如图 6 所示。
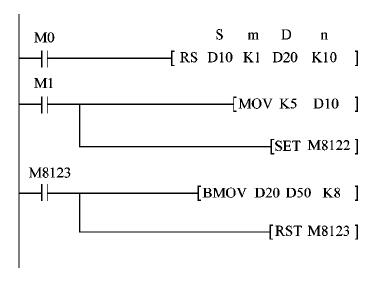
图 6 无协议通信基本格式
4. 2 触摸屏软件设计
课题组采用 EasyBuild8000 软件对 TK6070iP 触摸屏进行编写设计,该软件是集编写、调试与仿真于一体的 WEINVIEW 触摸屏编程软件,带有各种功能元件,能够对 PLC 的寄存器进行实时的控制和显示,操作简便直观。触摸屏主要完成的任务有以下几点:
1) 触发原始振动按钮,得到砂轮的原始振动数据,并跳转到波形显示子界面,对转速波形和振动波形进行监测;
2) 在砂轮转子上加试质量块,同时在触摸屏上输入试质量块质量和相位,然后触发试质量振动来获取试加质量后的振动;
3) 触发平衡计算按钮,计算出不平衡量的大小和相位,并跳转到平衡块指示界面,以图形的方式直观地显示在触摸屏的界面上;
4) 最后根据第 3 步的显示结果,在砂轮的对应位置配置平衡块,然后触发平衡振动测试平衡后振动,并显示动平衡效果与振动下降率。根据上述任务,设计完成整个动平衡过程的人机交互主界面,如图 7 所示。
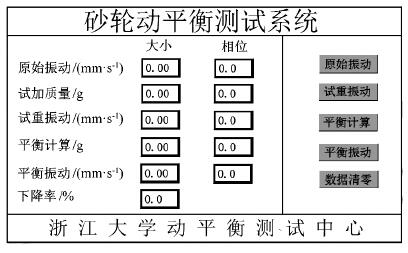
图 7 动平衡测试系统主界面
4. 3 单片机软件设计
单片机初始化之后被置于接收等待状态,一旦接收到 PLC 的数据后就关闭串口中断,根据接收到的SBUF 中的命令码执行相应的功能,完成后返回数据给 PLC,重新打开串口中断,等待下次接收数据。在通信程序中,MAX485 芯片是半双工工作模式,发送和接收不能同时进行,所以必须用单片机 P3. 3 引脚控制 MAX485 芯片的收发。在初始化时将 P3. 3置低,MAX485 芯片处于接收状态,在收到数据之后关闭串口中断,同时将 P3. 3 置高,经过后续的运算之后发送数据,然后再将 P3. 3 置低,如此再进行下一次的数据传输。
5 、实验
将砂轮动平衡测控系统应用于实验室的模拟砂轮试验台,如图 8 所示。
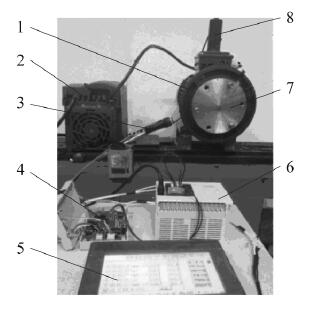
1—电机; 2—变频器; 3—光电传感器; 4—从机电路板; 5—触摸
屏; 6—PLC; 7—法兰盘; 8—振动传感器。
图 8 砂轮动平衡系统测试
使用质量为 5. 2 g 的质量块作试加质量,进行 3次动平衡实验,实验数据如表 5 所示。由实验数据可知: 经过平衡计算得到的不平衡量的大小和相位基本保持一致; 砂轮磨床动平衡系统平衡精度高,平衡效果好,可以满足实际生产需求。
表 5 动平衡实验数据

6 、结语
课题组提出了一种基于 PLC 的磨床砂轮动平衡机系统,并通过模拟砂轮试验台,证明了该方案是可行的。相比之下,现有的磨床砂轮半自动化平衡通常需要利用一台动平衡仪来巡检,效率和实时性较低,而自动在线动平衡系统价格高昂,中小型磨床厂难以承受。文中所设计的砂轮动平衡机系统具有人机交互性好、结构简单、通信可靠和价格低廉的优点,因此,该系统在磨床砂轮动平衡中有很好的应用前景。
投稿箱:
如果您有机床行业、企业相关新闻稿件发表,或进行资讯合作,欢迎联系本网编辑部, 邮箱:skjcsc@vip.sina.com
如果您有机床行业、企业相关新闻稿件发表,或进行资讯合作,欢迎联系本网编辑部, 邮箱:skjcsc@vip.sina.com
更多相关信息