进给轴带位置环时多级变速在 840Dsl 中的实现
2019-6-25 来源: 中国第一重型机械股份公司 作者:樊 凯
摘要 : 进给轴在位置环建立后, 如果传动比突然变化, 即变速实现, 则最大速度、 进给速度、 跟随误差以及定位精度等都会相应改变, 如何平滑顺畅实现变速而不引发报警, 是一个难题。本文阐述了实现方法。
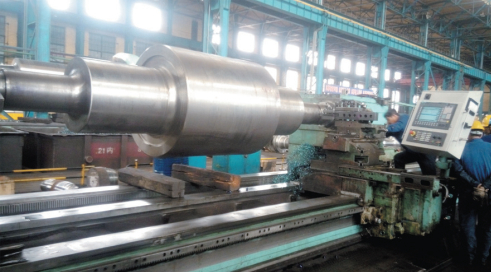
1. 课题必要性
主轴变速功能在所有使用 ISO 代码的数控系统中都规定了一些特定代码和功能, 比如西门子 840D 系列中, 辅助应答代码 M41~M45 分别代表了主轴的Ⅰ、 Ⅱ、 Ⅲ、 Ⅳ和Ⅴ挡, 这些挡位的传动比参数可以提前预设写入, 为 31050和 31060, 当主轴变速完成后, 对应接口信号 DBX16.3 为 1, 同 时 DBX16.0 和 DB16.1、DBX16.2 组合起来反馈当前挡位信号, 读取对应挡位的传动比和对应挡位的最大速度值, 则所有参数都能匹配起来, 挡位变换产生的轮廓偏差、定位误差等都可分别调整, 可以实现加工编程中的速度变换。
进给轴多级变换功能则没那么容易实现, 因为 840D 系统中没有在参数设计中充分考虑进给轴多级变速功能, 对于进给轴变速后的最大进给速度、 加速度、 定位误差、 轮廓偏差、 伺服增益系数和传动比等都没有设置对应挡位的参数组,最最关键的问题是, 西门子没有相应的接口信号通知 NC 系统该进给轴当前挡位, 无法将实际挡位与参数系统有机结合起来, 那么就会出现这种情况, 就是进给轴变速后, 由于 NC 无法得知,但速度变化引发的轮廓偏差、 定位误差等会让进给轴频繁报警, 无法工作。 当然了, 变速完成后,手动去输入所有相关参数是可以的, 但是, 这种方法太低级了, 总不能操作人员每次变速完成后,维修人员亲自去修改机床参数吧?因此, 这不是长久之计。
那么, 进给轴多级变速是否有必要保留呢?在现代新机床设计中, 进给轴多级速度很少看到,因为在新机床设计中, 通过电动机功率、 转速、传动比和安装空间匹配, 可以满足一台机床的所有加工需求, 不需要有机械变速。 但是, 在一些旧机床改造中, 则不能面面俱到。 比如以我改造的一台 SKODA 产 SUT200 型重型卧车为例, 原来通过Ⅰ级变速增大输出转矩、 降低进给速度,用于粗加工 ; 通过Ⅱ级变速提高进给速度、 降低输出转矩, 用于精加工。 做改造方案时, 如果只保留一个挡位, 由于电动机安装空间极其狭窄,可选择的伺服电动机不能满足原有加工需求, 要么进给速度太低, 要么输出转矩不够, 机床的改造就不能取得满意的效果, 所以, 必须实现进给的多级变速。
在我最近的数控机床改造过程中, 接连发现了三例这种问题, 于是, 如何平滑稳定实现进给轴多级变速, 而且使位置环不报警, 这就成了一个重要的问题。 经过多次摸索, 我们终于攻克了这个难题。
2. 实现方法
以 SUT200 型数控卧式车床为例, 刀台 X、Z 分别都具有两级变速, 其中, X 轴电动机自带编码器, 外置光栅尺, Ⅰ级传动比为 1:18, Ⅱ级传动比为 1:3, Z 轴电动机自带编码器, 外置一个编码器做位置环, 位置环编码器自带一个减速箱, Ⅰ级传动比为 1:6, Ⅱ级传动比为 1:2,位置环编码器传动箱传动比为 2:5。 这两种情况代表了两种非常典型的全环方式, 分别以这两种情况描述进给轴多级变速的实现。
(1) 光栅尺做位置环, 以 X 轴为例。 实现步骤如下。
第一步 : 检查传动比。 若机械能够确切推算传动比, 则可省略此步。 进行此步的前提是, 与传动比相关的 31050(负载齿轮箱分母) 、 31060(负载齿轮箱分子) 、 31064(附加齿轮箱分母)
和 31066(附加齿轮箱分子) 这几个参数必须设置为默认值 1, 31030(滚珠丝杠螺距) 也按默认值 10 设置, 反向间隙补偿 32450 清掉, 且 X轴应激活的是不带光栅尺的第一测量系统(DB31.
DBX1.5=1) 。
前置条件满足后, X 轴切换到Ⅰ级, 在 X 轴终端压上一块百分表, 向一个方向开 1mm, 此时可消除反向间隙, 然后百分表清零, 再向前开1mm, 实际百分表走多些, 比如实际百分表动0.2mm
, 则传动比为 1 ∶ 0.2=5 ∶ 1, 将此传动比写入 31064、 31066, 然后再压百分表, 看是否准确。 界面如图 1 所示。 如果有微量误差, 将传动比细分为 500 ∶ 101、 5 000 ∶ 999 等进行尝试, 直到误差进一步减小到可忽略不计。 如果追求更加精确的数显精度, 可以通过激光干涉仪进行螺距误差补偿(LEC) 。
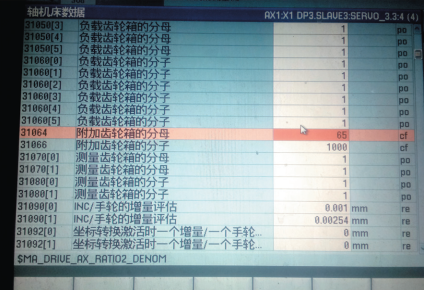
图 1
记录下Ⅰ级的传动比, 然后切换到Ⅱ级, 将31064、 31066 清掉, 重新进行上述步骤, 得到Ⅱ级的传动比。 这里需要特别说明的是, 为什么传动比写入 31064、 31066, 而不写入 31050、31060 ?因为 31064、 31066 的生效方式是 CF(NEW CONFIG) , 不 需 停 电 重 启, 而 31050、31060 的生效方式是 PO(POWER ON) , 需要停电重启。
第二步 : 建立定义文件。 得到Ⅰ、 Ⅱ级的传动比后, 开始写定义文件。 在 840Dsl 的 “调试”菜单里找到 “系统数据” 菜单, 再找到 “定义”文件夹。 在该文件夹内新建一个定义文件, 默认客户自定义文件名为 MMAC.DEF。 打开该文件,在该文件内写入如下内容 :
DEF M51 AS MLX1; 书写 M51 调用 MLX1.SPF 子程序。
DEF M52 AS MLX2; 书写 M52 调用 MLX2.SPF 子程序。
然后保存退出, 则系统开始自动编译该定义文件, 如果文件内容书写无错误, 则编译可顺利通过, 若编译不通过, 请检查书写。 这里,MLX1.SPF 为 X 轴Ⅰ级变速子程序, MLX2.SPF为 X 轴Ⅱ级变速子程序。
第三步 : 建立变速子程序。 定义文件建立后, 可以在 “制造商循环” 文件夹内建立 MLX1、MLX2 变速启动子程序。 该子程序的作用有两个,一个是驱动 PLC 程序进行变速执行元件的动作,比如离合器、 电磁阀等 ; 一个是写变速相关参数,包括传动比、 伺服增益系数和最大进给速度等。子程序以 MLX1.SPF 为例, 书写子程序如下 :
M53; 驱动 PLC 开始进给变速的条件。
G4F3; 停顿 3s, 给挡位切换时间。
$MA_DRIVE_AX_RATIO2_DENOM=1; 写31064。
$MA_DRIVE_AX_RATIO2_NUMERA=18; 写31066, 传动比为 1 ∶ 18。
$MA_POSCTRL_GAIN=0.6; 写伺服增益系数 32200。
$MA_MAX_AX_VELO=1000; 写轴最大进给速度 32000。
NEW CONF; 上述参数即时生效。
M30; 程序结束。
注意上述四个参数的生效方式均为 CF, 可以使用 NEW CONF 即时生效, 生效方式为 PO的则不可以。 所以, 使用这种方法可写的参数必须生效方式只能为 CF。 程序界面如图 2 所示。
第四步 : 编制 PLC 程序。 NC 方面的准备已经就绪, 接下来就可以编制 PLC 程序了。 这里,不赘述 PLC 程序, 大家可以根据实际情况自行编制。
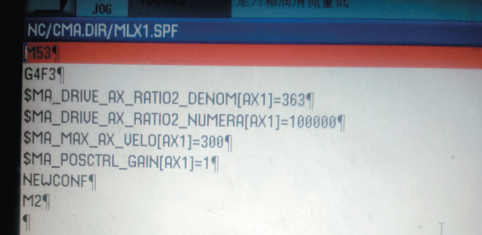
图 2
第五步 : 全环试车。 上述步骤完成后, 则可以进行半环试车, 可以看到, 当在 MDA 方式下执行 M51 时, 则 31064、 31066、 32200 和32000 等自动按照 MLX1.SPF 内设置而更改 ; 执行 M52 时, 上述参数按照 MLX2.SPF 内设置而更改。 在Ⅰ挡、 Ⅱ挡速度下, 明显可以看到同样的电动机速度, 驱动 X 轴的速度已经按传动比切换过来。 此时, 可以激活带光栅尺的第二测量系统(DB31.DBX1.6=1) 。
按照常规设置, 将 3 1 0 0 0(是否光栅尺) 、31040(位置环检测是否直接安装到机床上而没有中间变速) 均设置为 1, 全环设置完成。 注意,若 31040 为 0, 则 NCU 会检测 31050、 31060
的数值, 当挂光栅尺时, 会出现轮廓监控报警、不受控制等现象。 由于光栅尺直连, 31070(编码器齿轮箱分母) 、 31080(编码器齿轮箱分子)默认为 1 即可。
(2)编码器外带减速箱做位置环, 以 Z 轴为例。 实现步骤与上面完全一样, 但设置参数有略微差别。 31000、 31040 必须设置为 0, 同时,31044(编码器是否有中间变速) 必须设置为 1。由于编码器中间有传动比, 31070、 31080 必须设置。
3. 结语
通过西门子 840Dsl 的配套软件 NC-VAR 也可以实现该功能, 但需要大量复杂的编程工作,有兴趣的同行可以自行尝试。 进给多级变速通过这种方法实现, 不仅仅拓宽了设备维系人改造机床的思路, 减少了不必要的机械结构修改, 而且为其他一些特殊功能的实现提供了更加简便易行的思路。
投稿箱:
如果您有机床行业、企业相关新闻稿件发表,或进行资讯合作,欢迎联系本网编辑部, 邮箱:skjcsc@vip.sina.com
如果您有机床行业、企业相关新闻稿件发表,或进行资讯合作,欢迎联系本网编辑部, 邮箱:skjcsc@vip.sina.com