数控轧辊磨床磨削技术的新方向——4点测量3D磨削
2018-9-28 来源: 山东安卓数控科技有限公司 作者:庞景方
在造纸机上,不断提高的运行速度和对可接受振动范围的减小已经对造纸机辊筒的圆度、偏心率和圆柱度提出了新的要求。圆度更好的辊筒遇到的振动问题更少,条痕问题更少,造纸机的运行性能也更好(较少的纸卷断裂),从而也会降低造纸机的维护费用。为解决以上问题,芬兰赫尔辛基工业大学机械设计系的几位研究人员,研究出了针对造纸机辊筒在数控轧辊磨床加工时的4点测量和3维磨削软件。轧辊研究国际有限公司(Roll Research)为造纸行业的轧辊磨床提供新一代4点测量系统和3维磨削技术。
1 、 4点测量、3D磨削概念
3D是M D和C D测量的叠加,M D是平面的、二维的。通常说的测量技术是3D,但对于磨削工作,它本身就是一个3D的工作空间。首先,4点测量技术是水平和垂直面的叠加,是三维的,而传统的只是水平面的,是二维的。通过4点测量能精确测量出轧辊误差的整体情况(两点测量是检测不出实际情况的),能通过测量数据计算出补偿磨削曲线,进行二次磨削。再依据补偿磨削曲线,经过Z轴和微量进给U轴的相互运动完成补偿磨削。再次,4点测量技术的理论依据和方法是:圆度测量的两点法和三点法。两点法适于测量具有偶数棱边形状误差的外圆;而三点测量适用于测量具有奇数棱边形状的外圆,只有使用这两种方法才能测量出圆度的真实情况。现在轧辊磨床大多使用的数控测量方法,都是采用单一的两点测量为理论依据的,所以它所测量出的数据是不准确的。
另外,4点测量对校直误差和下弯误差的测量也优于两点测量;还有就是利用4点测量的方法能过滤掉对测量没有用的信息,只把有用的信息显现出来,避免了无关信息的干扰,提高了测量数据的真实性。在测量学上,对于同一组数据,采用不同的数学模型、不同的算法,最后得出的结论是有区别的。国内习惯重视硬件的投入,忽略软件的价值。对于西门子来说,它最有价值的不是那些电机等硬件,而是它嵌入到这些设备中的控制代码。现在具有战略眼光的厂商,对软件研发上的投入越来越多。如图1所示,在影响测量的因素当中,hardware硬件占35%,software软件占45%,controller控制器占20%。这个数据是美国的GIDEP(政府工业数据交换项目)中提出来的。
4点测量系统的硬件,应用当今流行的碳纤维材料较传统的铁件更轻便、刚性好、稳定性好、成本低等。应用4点测量技术,配以专业、先进的数控系统使测量技术在轧辊磨床上的应用实现了突破性的飞跃,应用意义重大。
2、 数控轧辊磨床
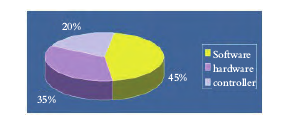
图1 影响测量不确定的重要因素

图2 3D磨削、4点测量数控轧辊磨床7轴联动
1-砂轮床身 2-工件床身 3-头架 4—砂轮 5-大拖板 6-磨架(横向
进给) 7-中心架 8-尾架 9-测量架 10-测量臂
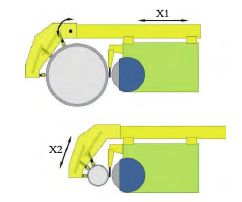
图3 4点测量装置安装位置与测量臂运动
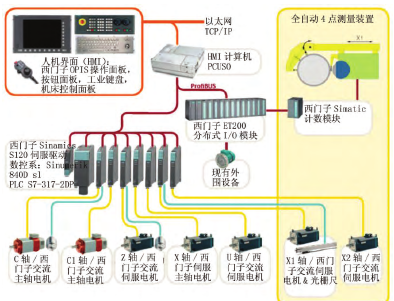
图4 4点测量装置与3D磨削系统的自动化系统布局
2.1 4点测量、3D磨削数控轧辊磨床各轴(如图2)
各传动轴:砂轮回转主轴—C1轴、工件回转主轴—C轴。五个为伺服驱动轴:拖板移动—Z轴、磨架移动—X轴、磨头微量移动—曲线U轴、测量架移动—X1轴、测量臂移动—X2轴。
2.2 自动4点轧辊测量设备(如图3)
4点测量装置部分组成部件
● 水平测量臂。
● C型支架,碳纤维,卸装轧辊时液压驱动上抬。
● C型支架上三个测量头。1个固定在支架上,另外两个测量头安装在线性导轨上。
● 1个磨轮侧测量臂。液压旋转机构。
● 可更换测量端子。
● 海德汉传感器。
● 参照盘,用于参照绝对直径测量。
2. 3 数控轧辊磨床所配备的西门子电气、数控、传动系统
西门子公司向Rol l Re s e a r c h公司提供欧洲标准版本的西门子Sinumerik 840D sl数控系统和标准的电器系统、驱动系统。Si nu mer i k 840D sl数控系统包括集成的Si matic S7‐317 PLC CPU(中央处理器),西门子Sinumerik 840D sl软件许可,所有需要的西门子数控软件选项许可,840D sl数控软件,用于西门子S7‐317 P L C的P LC软件,基于W i n d o w s 7的测量系统软件(中文版),独有的数控4点测量3D磨削软件。如图4所示。
3 2点测量与4点测量技术对比
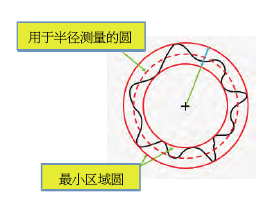
图5 圆度及轮廓的定义
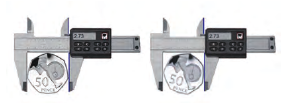
图6 圆度测量
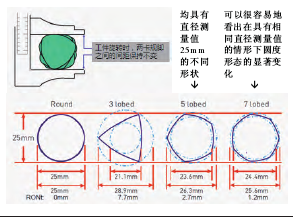
图7 等径外形,具有相同的直径、不同的圆度
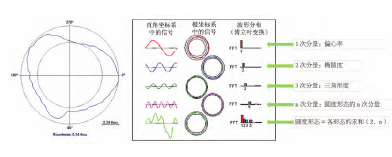
图8 圆度形态及其波形分布
3.1 圆度(如图5)
圆度形态:在I S O 1101中被定义为两个在给定横截面内的同心圆所限定的区域。圆度:在I S O 1101中被定义为两个在给定横截面图9 采用混合4点测量设备(左)和两点测量设备(右)测量的胶带内的同心圆的半径差。由于旋转轴线的运动,使得对大型旋转柱形的圆度及圆柱度测量非常困难,它等同于一台标准圆度测量仪的主轴误差。为了测得圆度,必须分离旋转轴线和圆度轮廓。在径向跳动信号测量中,是无法知道信号是来自于物体的运动还是其圆度轮廓的。在标准圆度测量仪上,通过采用非常精确的主轴来避免这个问题。
3.2 圆度的测量——2点测量技术
根据圆度在I S O 1101中的定义,对直径进行测量不能够获得圆度信息。采用卡规技术测量圆度,如图6.
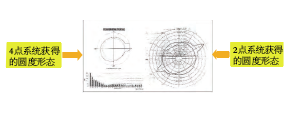
图9 采用混合4点测量设备(左)和两点测量设备(右)测量的胶带
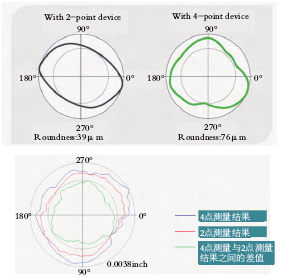
图10 圆度形态测量结果(示例)
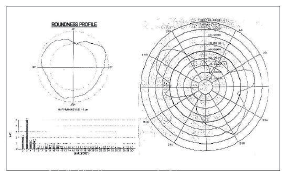
图11 由混合4点测量设备(左)和两点测量设备(右)测量的三角形轮廓
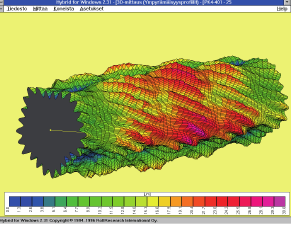
图12 轧辊在生产时可能会产生振动
如果不进行准确测量,是无法确定什么地方出了问题图7中显示了具有不同奇数叶瓣(波动每转)但直径相同的外形。如果采用2点测量方法,比如游标尺,来测量这些外形的圆度,当旋转具有这些外形的工件时,是无法发现任何差异的。在轧辊几何尺寸测量中使用的传统设备都是基于2点测量方法的。如图8所示。2点测量技术:不能测量目标对象的真实圆度形态;偶数波形的形态(例如椭圆度、四边形度等)可以获得,但是奇数波形无法采集到。
3. 3 4点测量方法与2点测量方法的比较
胶带测试:在轧辊表面贴上一小段胶带后,采用这两种系统来进行测量。从图9中看出某主要轧辊磨床制造商的两点测量设备(右)无法区分奇数波形的圆度轮廓。传统的测量设备仅仅能够测得不同轮廓的径向跳动和直径差异外形。圆度形态测量结果(如图10~图12)。因为造纸机辊筒振动问题,通过造纸机辊筒常规测量、磨削与4点测量3D磨削得出了一份对比:(1)质量差的造纸机辊筒比质量好的造纸机辊筒在机运行时间的缩短,要超过40%;(2)带轴承磨削,3D补偿磨削要比传统的补偿磨削,辊子的圆度形状提高了97%;(3)造纸机的开机率提高;(4)造纸机辊筒维修成本降低;(5)造纸机生产利润提高。
4 4点测量、3D磨削
4.1 3D磨削(图13)
(1)基于对M D形态(圆度形态和跳动)以及CD形态(直径差异形态和校直等)的精确测量,轧辊得以根据M D和CD曲线进行补偿磨削从而获得高精度的轧辊形态。
(2)在磨削前利用4点测量设备对M D形态(圆度形态和跳动)以及CD形态(直径差异形态和校直等)精确测量。
(3)测量结果在磨削中作为补偿曲线利用。
(4)获得理想的轧辊形态。
(5)MD→用于圆度形态和跳动。
(6)CD→用于直径差异形态及校直等。
4.2 3D辊子外形测量技术,辅助辊子精密研磨
如图14所示,4点测量系统与3D磨削技术为轧辊测量带来无与伦比的准确度,辊子轮廓的测量结果接着被处理成一个表面状况的三维图像,这在两点测量技术是不可能的。处理后的图像与纸页全幅纵、横向分布相结合,这个三维图像就可以很容易地定出缺陷所在的位置。在随后的研磨过程中,辊子表面轮廓根据预定的同心几何形状进行修整,结果就成了理想的辊子几何形状。
4. 3 影响磨削质量的因素及解决方法
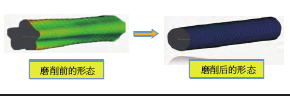
图13 磨削前后的形态变化
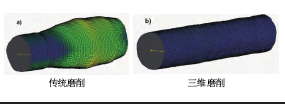
图14 轧辊磨削后的几何形态
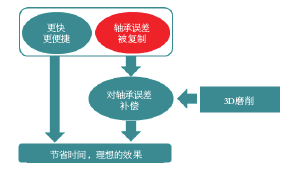
图15 带箱磨削
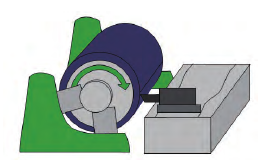
图16 导轨误差补偿磨削
4. 3.1 带(轴承)箱磨削时为了避免轴承误差,通常在磨削前把轴承座从轧辊上拆卸下来,使得对轧辊的服务需要更长的时间。 在采用对轧辊的3D测量和3D补偿磨削,对轴承误差进行补偿,就可以进行带箱磨削,并且能够得到理想的轧辊形态。如图15。
4. 3.2 导轨误差补偿磨削(图16)
直径变化主要是由于机床导轨直线度误差引起的。轧辊加工的精度不再仅仅是关于机床本身的精度,还和测量系统以及控制系统的精度紧密相关。由于有了测量和控制系统,现在对机床的主要要求是其稳定性,而不是其机械精度。对轧辊的校直也不再像以前那么重要。
4. 3. 3 圆度误差自动补偿磨削(图17)
如果轧辊的圆度误差在其整个长度上不是均一分布,也将导致直径变化外形误差。在补偿轧辊直径变化时,将所测得的数据存储在控制系统中,通过计算得到补偿曲线,进行补偿磨削。 轧辊刚性差异会导致圆度误差,系统对由轧辊刚性差异引起的圆度误差进行补偿磨削。
4. 3.4 校直误差自动补偿
在轧辊安装时,轧辊无需非常精确地平行于Z轴进行校直。校直偏差可以通过以下方式进行补偿:采用最初的校直测量数据和补偿、在每次补偿磨削中自动补偿。
4. 3. 5 偏心补偿(图18)
没有偏心补偿功能的情形下,在开始磨削前,轧辊必须在磨床上空转几个小时来消除轧辊上的热膨胀差异。 采用偏心补偿功能,轧辊的偏心误差可以进行测量并在磨削时进行补偿,从而允许轧辊在磨床上的安装工作完成后可以立即开始磨削工作。
4 . 4 辊筒数据管理系统
辊 筒 数 据 管理系统基础版包括安装于磨床测量用计 算 机 上 的 本 地SQL数据库和相关软件。本 地 数 据 库软件,安装于测量用计算机上的混合磨削控制软件包含以下数据库:辊筒测量数据、辊筒、TECHNOLOGY技术进步辊筒类型(当为数据库创建新轧辊时可用作模版)、砂轮、砂轮类型(新砂轮的修整)、操作人员、报表语言。
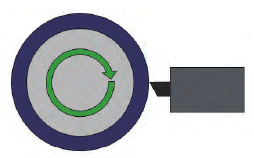
图17 圆度误差自动补偿磨削
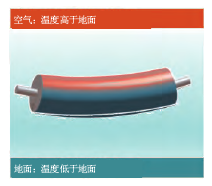
图18 偏心补偿
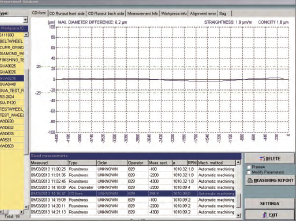
图19 测量数据库
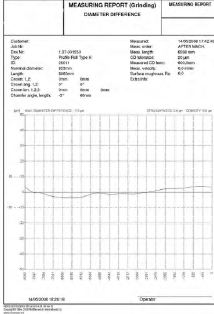
图20 辊筒的卡规形态(外形误差)变化
4. 5 数据库软件
如图19所示,某个测量数据可以通过首先选择轧辊列表(黄色列表)中的轧辊序列号,然后从测量数据清单中找到。测量设备将所有测量数据存储于测量数据库中。上一次指定轧辊的测量数据可以从存档中选出读取。工件的其它测量和加工信息也可以保存下来。软件会存储加工使用过的程序清单。当下次磨削同一根轧辊时,可以调用上一次的磨削程序清单。用户不需要重新输入所有的参数信息,这样工作效率更高。测量设备可根据I S O9000系统的要求进行校准。圆度校准采用通过M I K E S(芬兰计量鉴定中心)测量的测试碟进行校准。
4.6 辊筒的测量报告示例
如图20、图21所示,采用三维测量,可以创建工件外壳示意图。测量数据可选用不同方式进行表述:用圆柱坐标(作为辊筒整体)或者用直接坐标系统以轧辊外壳扩展图像的方式进行表述。如果需要,工件可以以不同方式进行旋转和缩放,使得制作的报表清晰明了。
5 4点测量、3D磨削技术的优点 在轧辊磨削车间:
● 带(轴承)箱磨削→节省时间,更好的磨削效果
● 自动校直误差补偿→节省时间,更好的磨削效果
● 对轧辊刚性差异引起的圆度→更好的磨削效果
● 误差补偿
● 偏心补偿→节省时间,更好的磨削效果
● 轧辊问题的快速分析(需RRI技术协助)→更好的磨削效果在造纸过程中:
● 改善辊筒振动问题
● 改善纸张的两面差及平滑度
● 延长辊筒在造纸机上的运行时间
● 降低造纸机振动水平和振纹
● 降低由振动引起的生产中断
● 提升造纸机速度的可能性
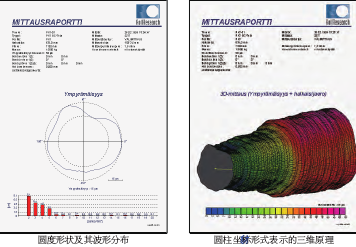
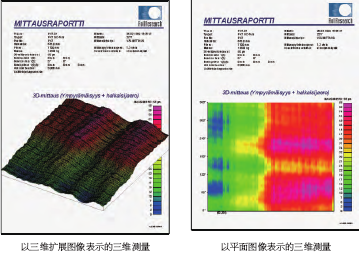
图21 测量后生成的三维图像
投稿箱:
如果您有机床行业、企业相关新闻稿件发表,或进行资讯合作,欢迎联系本网编辑部, 邮箱:skjcsc@vip.sina.com
如果您有机床行业、企业相关新闻稿件发表,或进行资讯合作,欢迎联系本网编辑部, 邮箱:skjcsc@vip.sina.com
更多相关信息