基于 ANSYS Workbench櫜的滚丝机主轴优化设计
2017-8-9 来源:青岛大学 机电工程学院山东青岛 作者:陈洋 管殿柱 焉兆超 魏代善
摘要:以生产高强度螺纹的滚丝机主轴为研究对象,基于有限元理论,运用 SolidWorks建立滚丝机主轴三维模型,并采用有限元分析软件 ANSYS Workbench对其在实际工况条件下进行静力分析,从而得出主轴的应力分布和变形情况,并找到其应力薄弱环节。在此基础上,以主轴的部分特征尺寸为设计变量,以实际强度和刚度条件作为约,以主轴质量最小为目标函数,进行主轴的特征尺寸优化设计,并对优化后与优化前的主轴受力情况进行对比。结果表明,在满足实际的强度和刚度条件下,主轴质量降低了5.1%。对优化后主轴进行了模态分析,校核临界转速以避免主轴产生共振情况,使得主轴整体力学性能得到了提升,并降低了成本。
关键词:主轴;ANSYS Workbench;优化设计;滚丝机
引言
生产高强度螺纹的滚丝机要求精度很高,而其主轴结构是整套滚丝机设备的关键零件之一,主轴在实际高速旋转工况下,若整体变形过大或发生共振则会影响滚丝的精度和效率,甚至会威胁到生产制造的安全性。因此,在设计主轴时,有必要对其强度、刚度和临界转速进行校核。以往的工程师要么运用经验来对滚丝机主轴进行设计,要么通过标准机械设计方法对滚丝机主轴进行强度和刚度的计算,都是依靠实际运行情况来进行校核测试。近来,随着虚拟样机技术的发展,国内外从事机械设计行业的工程师普遍采用先进的有限元分析理论及相应的有限元分析软件对设计的零件进行强度、刚度和临界转速的校核。因此,本文利用有限元分析软件 ANSYS Workbench对滚丝机主轴的力学性能进行分析,并根据结果对主轴部分尺寸进行优化分析,使其在满足实际工况条件下,提高整体力学性能,并降低主轴质量,从而降低成本。
1 滚丝机主轴优化设计流程
在滚丝机主轴优化设计中,首先通过三维建模软件SolidWorks对现有主轴进行参数化建模,然后导入ANSYS Workbench中建立有限元模型,根据实际情况选定材料属性并施加约束和载荷,从而对主轴进行静力学分析,根据分析结果,找到应力薄弱环节,选择主轴部分特征尺寸作为设计变量,以实际强度和刚度要求为约束条件,以主轴质量最小为目标函数,对主轴进行优化分析。并将优化后结果与优化前结果进行对比,验证优化过程的正确性。最后通过模态分析找出优化后主轴第一阶固有频率,并转化为临界转速与主轴实际转速对比,验证其动态特性满足不共振条件,从而实现滚丝机主轴的优化设计。主轴优化设计流程如图1所示。
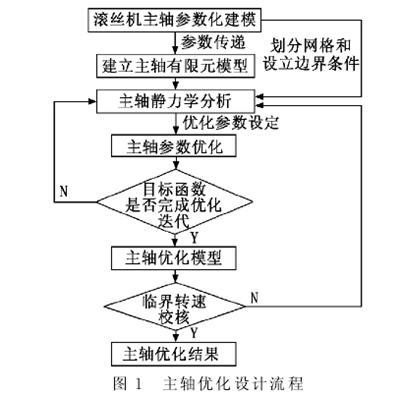
2 滚丝机主轴结构
目前,滚丝机已经广泛应用于高强度螺纹的制造,能制造出高强度、高精度、高硬度以及高表面质量的螺纹联接件。图2为一种滚丝机主轴的结构简图。主轴两端通过两组轴承安装在主轴箱内,主轴轴承采用高精度角接触轴承,能承受较大载荷,起径向和轴向支撑作用。滚丝轮由套筒限制其轴向移动,在加工螺纹时,主轴主要受到滚丝轮径向反力、轴向扭矩以及较小的轴向力。主轴右端由传动轴提供扭矩作为旋转动力。
3 滚丝机主轴的有限元分析
利用三维建模软件 SolidWorks对滚丝机主轴进行参数化建模,考虑到主轴上的倒角、圆角等对最终的有限元分析结果影响不大,但会严重降低主轴的静力学分析 效 率,因 此,对其进行了 简化处理。 利 用SolidWorks完成主轴的建 模后,利 用 SolidWorks与ANSYS Workbench之间的无缝衔接将其直接导入到ANSYS Workbench,导入 后 的 模 型 如 图 3 所 示。ANSYS Workbench向用户提供了功能全面的网格划分工具和多种网格划分方法。若网格尺寸过小,虽然会增加有限元结果的精度,但会加大算机的负担,使效率变慢;若网格尺寸过大,则会造成运行结果不准确甚至结果不收敛。本文采用默认的四面体单元进行自由网格划分,设置单元尺寸为4mm。划分网格后的主轴模型如图4所,共有75469个单元、109530个节点
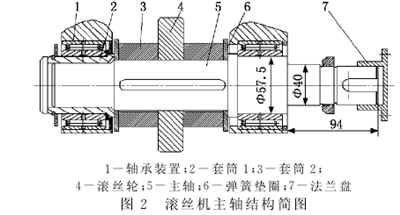
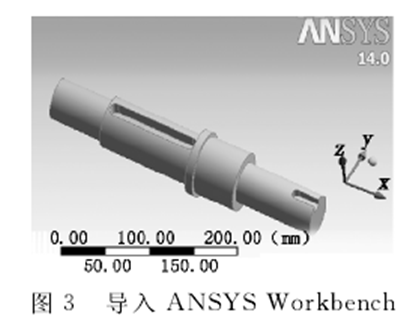
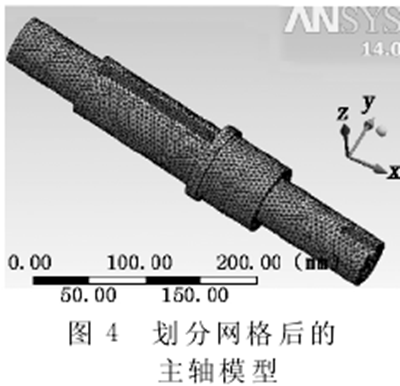
3.1 添加材料属性
本文中滚丝机主轴材料采用 40Cr,淬火处理,屈服强度σs=785 MPa,弹性模量E=2.1×105 MPa,泊松比ε=0.3,密度ρ=7 850kg/m3。
3.2 设置约束和载荷
约束和载荷施加的不同会导致不同的有限元分析结果,要想保证计算结果的准确性,应尽量按照实际工况来施加。本文中主轴的加载位置有以下4处:(1)在左侧与滚丝轮连接的键槽处施加固定约束(Fixed Support)。(2)左侧轴承采用圆柱约束(Cylindrical Support)提供径向支撑,右侧轴承采用圆柱约束(Cylindrical Support)提供轴向和径向支撑。(3)在滚丝轮匀速进给加工过程中,两端推杆提供的进给推力和滚丝轮对主轴的径向反力是一对平衡力。而实际中滚丝轮对主轴的压力很复杂,此时可简化为沿轴线方向的线性均匀载荷 P:
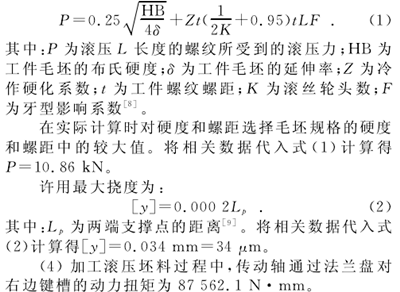
3.3 分析结果
主轴有限元静力分析结果如图5和图6所示。由图5可知,主轴整体变形最大值为19.6μm,小于许用最大挠度,满足主轴挠度要求。由图6可知,主轴最大等效应力为275.05 MPa,而40Cr材料的屈服强度为785 MPa,可知其安全系数 为 2.85,此时 满 足强度条件,并具有一定的优化空间。
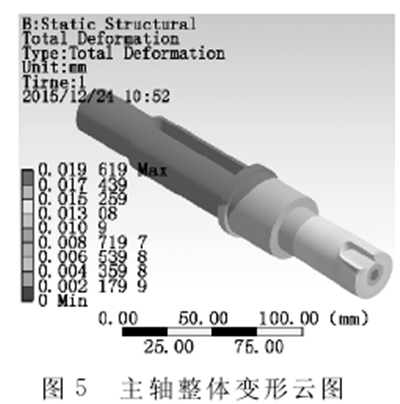
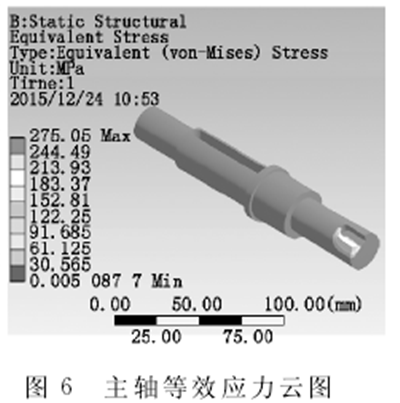
4 主轴结构优化
根据主轴整体变形云图和应力云图可知,主轴的变形和应力最大处均处于右端键槽所在轴端,故确定主轴右端两阶梯轴直径d1、d2和右端键槽所在轴长l作为设 计 变 量,取 安 全 系 数 为 =3,即 以 应 力 小 于261.7 MPa和最大形变小于34μm 作为约束条件,以主轴质量最小为目标函数。其优化模型如下:
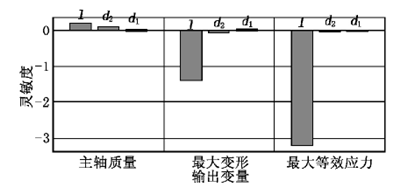
4.1 优化结果
在 ANSYS Workbench设计模块中,设置好相应输入参数后,点击 Preview 和 Update按钮,系统会自动生成一组设计点,并对其进行迭代求解。同时,进行参数灵敏度析,结果如图7所示。由图7可知,右端轴长度对应力和最大变形影响较大。选取零阶方法进行优化,最终可得出若干个备选方案。此时,选择较优方案为最终方案,并进行圆整,即d1=41.5md2=50mm,l=87.8mm 时,主轴满足强度和刚度条件且质量最小。4.2 优化前后主轴性能比较通过对滚丝机主轴部分参数优化设计,在满足实际强度和刚度条件下,降低了主轴的质量,提高了主轴的力学性能,优化后的整体变形云图和等效应力云图如图8、图9所示。由图8可知,优化后主轴整体变形为18.2μm,比优化前降低了1.4μm。由图9可知,优化后主轴最大等效应力为242.58MPa,比优化前降低了32.47MPa。优化后主轴质量为4.06kg,比优化前4.28kg减少了0.22kg,即降低了5.1%。
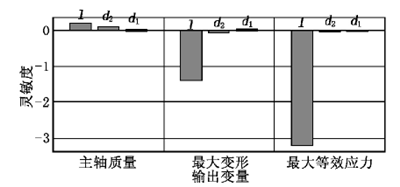
图7 参数灵敏度分析5主轴临界转速校核上述优化分析过程仅进行了静力分析
5 主轴临界转速校
上述优化分析过程仅进行了静力分析,对于主轴,其动态性能也很重要。由于主轴第1阶固有频率最小,故可以只求第1阶固有频率对应的临界转速与实际转速比较来进行校核。通过 ANSYS Workbench对优化后主轴进行模态分析,得出主轴的第1阶固有频率为3 017.5Hz,其振型图如图10所示。有频率与临界转速之间的关系为:n=60f . (3)其中:n为临界转速,r/min;f 为固有频率,Hz。由式(3)得主轴的第1阶固有频率对应的临界转速为181 050r/min,而滚丝机主轴的最高转速为600r/min,远小于该临界转速,因此主轴在正常工作时不会产生共振,具有很好的动态性能。
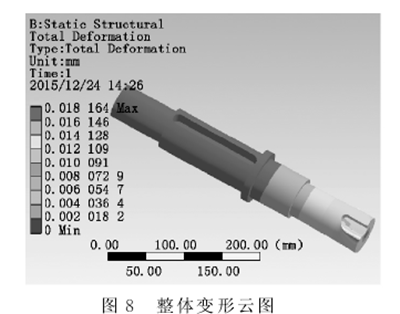
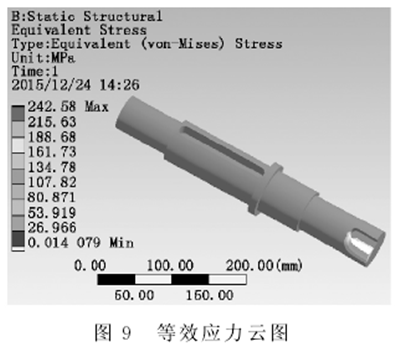
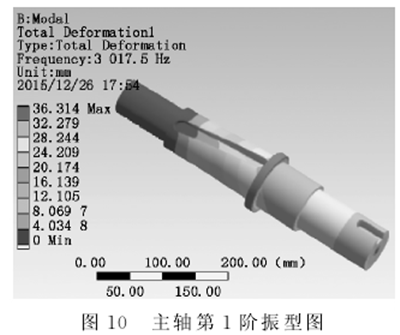
6 结论
本文运用参数化建模和优化方法,在不改变与滚丝 轮 等 机 构 配 合 的 前 提 下,运 用 SolidWorks 和ANSYS Workbench软件,对滚丝机主轴部分特征参数进行优化设计。通过分析比较优化前后主轴整体变形和应力结果,得出优化后主轴在满足实际工况要求的条件下,质 量减少了 5.1%,提高了主轴的力 学 性能;并对其进行了临界转速校核,从而验证了该设计的正确性,实现了该滚丝机主轴的优化设计,并为其他高强度滚丝机主轴的优化提供了参考依据。
投稿箱:
如果您有机床行业、企业相关新闻稿件发表,或进行资讯合作,欢迎联系本网编辑部, 邮箱:skjcsc@vip.sina.com
如果您有机床行业、企业相关新闻稿件发表,或进行资讯合作,欢迎联系本网编辑部, 邮箱:skjcsc@vip.sina.com
更多相关信息