大型曲轴磨床典型结构与先进的磨削工艺
2014-1-19 来源:常州机电职业技术学院 作者:虞行国 刘江
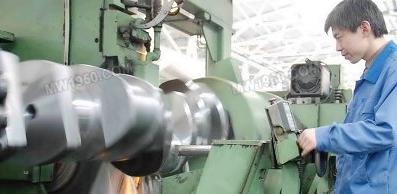
图一
对于曲轴加工设备来讲,磨床是使产品零件达到工艺要求的最终加工机床,固对其精度要求极高、复杂程度极难。对于工件长度超过6m,重量超过5t,工件的主轴颈和连杆颈粗糙度值要达到R a=0.4~0.6μm,主轴颈、连杆颈直径公差在0.008mm,主轴颈和连杆颈直线度在0.01 / 200 mm,连杆颈圆柱度0.015 mm,连杆颈分度±15′的技术要求并且加工不同角度和不同偏心量的连杆颈磨削的大型曲轴磨床,其要求就更高了。
根据目前现有设备状况和加工工艺,曲轴在磨床上的加工是分两步执行的,也就是说加工磨削主轴颈和连杆颈是由两种机型分开实施的,这主要是受到设备结构的限制和约束。一般磨削主轴颈选择在大型的普通外圆磨床进行,曲轴依靠外圆磨床的头架单驱动,在二顶尖和中心架的支撑下逐步对主轴颈进行磨削。在磨削主轴颈的过程中,产品的尺寸精度和技术要求都由人工直接干预。特别是对中心架两个方向支撑力量的控制,这就要看操作工人的熟练掌握程度,但要长期依靠人为因素来保证质量稳定是难以做到的,也是不科学的。如图1所示,在加工磨削连杆颈直径时,是选择专用的曲轴磨床来进行加工的。这种曲轴磨床的头尾座卡盘是可以以头尾座中心轴线为基准,按照曲轴主轴颈和连杆颈的冲程偏心量进行调整,使头尾座卡盘夹持连杆颈的中心围绕头尾座主轴的旋转中心,对连杆颈直径进行磨削加工。如图2所示。
因为曲轴技术设计的原因,它在长度质量分配上存在着比较大的偏心,如果不采取措施,曲轴在加工旋转中会出现运转不均匀的现象并产生有离心力状况,这样磨削加工的表面粗糙度肯定会受到影响。所以在机床的头尾座后侧都配制了配重装置,通过观察头尾座的驱动电动机电流的情况进行调整,从而可以改善和均衡头尾座的旋转稳定性。因为曲轴本身结构的原因,在头尾座同时夹紧曲轴两头时,头尾座在旋转时不同步就会造成曲轴的扭曲而影响加工精度。目前为了保证头尾座的同步,曲轴磨床头尾座的传动方式有两种,一是通过同步轴传递,即头座作为主传动经过一系列的传动链传递到尾座,使它们实现曲轴磨床的头尾座卡盘同步,保证曲轴在运转过程中不造成扭曲的现象。这种传递的方式制造成本低,但不可避免地存在机械传动链过长有间隙和磨损的现象,给调整带来诸多的不便。另一种是利用头尾座旋转作为两轴,采用数控同步技术,使头尾座在旋转的过程中旋转误差达到最小。有的在采用了头尾座旋转作为两轴的数控同步技术的制造厂家,为了防止因设备故障和突然停电造成头尾座失步,使设备损坏以及造成产品的报废,把砂轮电动机作为突然停电后的大直径砂轮的惯性当作发电机使用,把发出的电提供给头尾座电动机作为临时电源,临时保证头尾座能够在短时间内有旋转的空间防止故障的扩大。同时为防止头尾座电器系统本身的故障而引起失步,在头尾座机械部分设计有超越离机构作为保护装置,在实际运行中因头座调速系统模板故障造成头尾座失步3°,正因为在该装置的作用下防止故障进一步扩大和保全近30万元的工件报废。
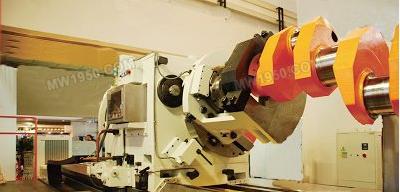
图二
曲轴属于细长轴零件,在加工时会形成中间下垂的情况,有的厂家为了克服这种状态在机床设计中加有机械、电气、液压测量等系统组成的曲轴防下垂吊系统。图3、图4所示就是该装置的外形,这个装置在机床数控系统中设置为第三轴,它的防曲轴下垂吊力由液压比例阀控制,保持和头尾座旋转角度的同步。
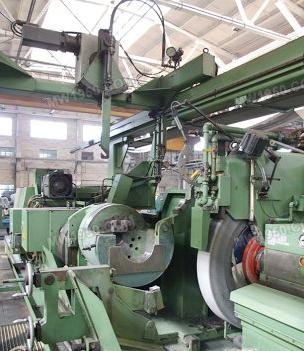
图三
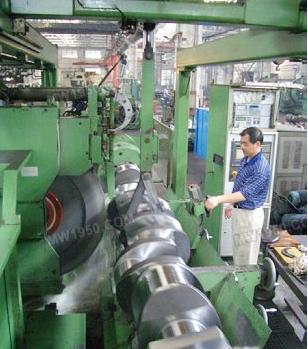
图四
随着数控技术的发展,机床功能部件水平的提高,目前国外已经发展出一种随动磨削曲轴的新设备新工艺,它只要在同一台机床上通过一次夹装就可以同时磨削加工曲轴主轴颈和连杆颈,而不需要再用两台设备依次分别对曲轴主轴颈和连杆颈进行磨削。
图5是该设备基本结构和加工工艺布置的示意图。该设备在电气系统上设计成全数控控制、全闭环反馈测量的控制模式,在机械设计上打破传统磨床的结构分布,把原来头尾座和工件Z 轴移动更改为砂轮架移动而头尾座及工件固定不动,因而床身长度就可以设计较短。由于采用了X 轴横向滑台原理,这样就可以克服和消除因工件移动而造成的机床变形等诸多因素,并且还增强了机床的刚性。固定工件的工作台台面设计成向砂轮架方向倾斜 20°,以便于冷却液方便排泄带走大量的磨削颗粒,保证了机床的热稳定性和工件因工作台倾斜 20°的设计而使头尾座能在固定工件的工作台台面上安全夹紧。因设计结构的不同,从而磨削方法也不同于一般的传统曲轴磨床,它的主轴颈磨削采用切入式磨削法,连杆颈的磨削是采用切入式随动磨削法。图6、图7是随动磨削法的曲轴与砂轮运动的轨迹示意图。
随动磨削法的公式:
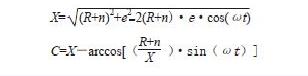
式中 X --砂轮架横向滑台移动轴;C--头尾座工件夹持旋转轴。
采用随动磨削法是比较先进的加工方法,但是它对设备有更高的要求,特别是对硬件和软件相互之间的关系更为密切配合。随动磨削法实际上是涉及到曲轴旋转位置与砂轮架直线运动二者之间的相互关系,它的关键在于:
(1)C 1、C 2和X 1必须保持同步。就是头座C 1和尾座C 2夹持曲轴二端头,偏心于主轴颈的连杆颈中心线,围绕C 1、C 2旋转轴线的运动轨迹,与X 1轴砂轮架横向滑台直线移动的前后运动的距离关系,始终要使连杆颈的外径在360°的任何角度上要与砂轮的外圆保持相切位置。
(2)机械传动链的精度、光栅反馈系统的精度、在线测量系统的精度。
(3)开发的随动磨削应用软件合理和实用性等。
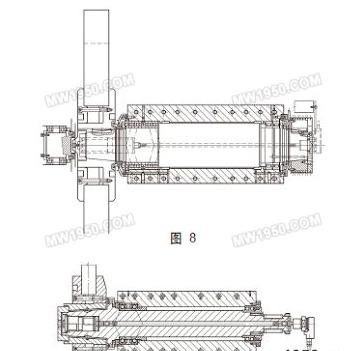
以上问题将直接影响到磨削加工的精度,为此,机床厂家在X 砂轮架横向滑台移动轴上,设计成刚性好、吸振性好、精度高的静压闭式导轨系统。X 轴驱动采用定位重复性好和传动间隙小的非机械传动的直线电动机消除间隙方法。X 轴定位用直线光栅尺进行精确。
头座C 1和尾座C 2采用水冷扭矩电动机直接驱动工件,高分辨率圆光栅消除机械传动的间隙,防止在磨削时的头尾座在旋转时有上下死点的出现,并保持同步和恒线速度磨削。采取这些措施从而在理论上可以保证磨削连杆颈的圆度达到0.005mm和表面粗糙度的要求。同时为了提高砂轮主轴转速来提升砂轮线速度,普通砂轮磨削圆周(线)速度可达45m/s,电动机主轴驱动功率达到78kW,对砂轮主轴箱的结构也进行了优化,如图8、图9所示。把原先的圆桶形轴瓦支撑更改为高精度的无需保养的陶瓷球轴承结构。为了提高砂轮主轴的精度还配制了带砂轮自动平衡系统(意大利MARPOSS制造),与砂轮主轴为一体,并带有超声波间隙控制系统(噪声控制)作为防止砂轮碰撞工件的保护装置。为了使工件在机床上加工找正方便,还设计有曲轴防下垂补偿功能,曲轴的下垂可通过一个安装在砂轮头架上预先设定中心的测量头系统,来检测曲轴的实际位置,与原设定中心进行比较后,通过数控系统对数控中心架进行控制补偿。如图10所示。
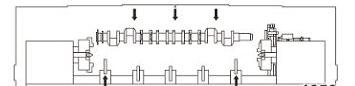
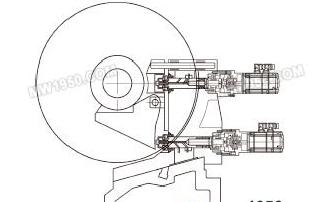
为了提高砂轮主轴的精度还配制了带砂轮自动平衡按每个操作命令实现往复运动,以测量垂直面中心高。对每个加工后的曲轴颈外圆进行多次测量,直至采用了足够数量的中心架,如图11所示。在全自动磨削时保证曲轴颈直径的一致,还配制在线直径测量头,装在砂轮头座上,可自动摆入和摆出。测量头始终跟随连杆轴颈作回转运动并具备自动圆度检测,该装置能够识别和显示采用切入式方法的圆度偏差,将椭圆度与圆度测量机床的测量结果进行比较,并直接对机床控制进行数据修正,并以人机友好的方式运行,能快速给出与圆度有关的机床参数的最佳值。在生产过程中可以对圆度进行常规检测,可以节省测量的时间。全部功能和显示都集成在机床的控制系统中。
在目前国内的磨床制造厂家中,还没能真正生产出大型的采用随动磨削结构的设备,以及大型曲轴进行随动磨削的工艺技术。这有待于我们工作在设备系统的全体科研人员共同努力,不断地对数控系统软件的开发、机床功能配套部件的研发升级。只有整体制造水平的提高,设备制造理念的更新,才能与国外仅有的几家生产随动磨削设备的厂家竞争叫板。
投稿箱:
如果您有机床行业、企业相关新闻稿件发表,或进行资讯合作,欢迎联系本网编辑部, 邮箱:skjcsc@vip.sina.com
如果您有机床行业、企业相关新闻稿件发表,或进行资讯合作,欢迎联系本网编辑部, 邮箱:skjcsc@vip.sina.com