机械螺纹类零件的数控机床加工技术探讨
2021-2-3 来源: 毕节职业技术学院 作者:余鹏,肖双平
摘要:现阶段,我国科学技术水平的飞速发展,使数控机床成为现代工业生产中的重要机械设备。数控机床在零件生产加工方面具有巨大的技术优越性,现如今,数控机床已经被广泛应用于建筑、汽车、轮船以及航天等众多领域,在人类生产生活中的许多方面都经常能够看到各种数控加工产品。通过数控机床加工技术的应用,能够实现对机械螺纹类零件的精密化、批量化加工,从而确保零件整体质量得到有效提升,使机械螺纹类零件能够更加高效地投入各个行业使用中,从而使生产成本得到降低的同时,也能使生产效率大幅提高,并为企业创造更多的经济效益。鉴于此,本文便对数控机床的主要类型进行分析,并简要概述其加工技术,分析了数控机床在机械螺纹类零件中的加工技术原理,在此基础上,深入探讨了并机械螺纹类零件的数控机床加工技术,同时,分析了数控机床对机械螺纹类零件的主要加工步骤,以期能够进一步提高我国对机械螺纹类零件的加工精度,实现工业零件加工技术的优化与创新,并为我国现代工业的高速发展提供一些借鉴和参考。
关键词:机械螺纹;零件;数控机床;加工技术
对于一个国家来说,其综合国力的高低在很大程度上取决于其制造业水平,而且制造业也是一个国家在航空、航天、生物、医学、能源、交通等诸多领域得以不断发展的重要基础。制造业的飞速发展,对社会生产及人类生活都产生了极为深远的影响。现阶段,信息化时代的来临,使各种高新技术,如计算机技术、微电子技术、物联网技术等得以不断涌现,这些高新技术为制造业的发展带来了强力的技术支持。例如,CIMS 的产生,便促进了其相关制造技术的革新,从而形成了并行工程、柔性制造、敏捷制造等一系列的全新工业概念。数控机床则是众多先进制造技术得以实现所不可或缺的基础设备,对数控机床进行技术创新与优化,也正日益引起人们的广泛关注。
1、 数控机床的发展现状及其现实意义
在汽车、电力等现代工业领域中,也已经广泛应用数控机床,许多高科技产品,如机电一体化产品、数字通讯技术产品等,都离不开数控机床的应用。可以说,数控机床的应用及制造,正对越来越多领域的技术发展产生直接的影响,特别是在我国,越来越多的厂家开始意识到,产品质量是提高企业核心竞争力的根本所在,这也使企业愈发重视通过数控机床加工技术的革新提高产品质量,虽然我国在数控机床技术方面取得了很大的进步,不过,相比国外发达国家的数控机床来说,则还有一些差距。当前,经济型数控机床在我国仍旧占据着很大比重,在 20 世纪 90 年代,我国才开始对数控机床进行普及应用,而对于高级型数控机床,由于其成本较高,这使其在我国现代工业发展初期并未大量引用,这也导致其在工业生产中所占的比例较小。但是,不断扩大高级型数控机床却也已经成为我国现代工业的未来发展趋势。
用于加工机械螺纹类零件的数控机床属于一种专用高效的特殊机床,其相比普通的通用机床有着很大区别,这需要该类机床具有较高的切削效率、较高的自动化水平以及极高的加工精度,通过对机械螺纹类零件的数控机床进行加工技术革新与优化,能够使机械螺纹类零件的生产效率大幅提高,并且也能使现代工业的生产效率得以提高,从而起到一举多得的作用,因此,对机械螺纹类零件的数控机床加工技术,进行深入的探讨与研究是具有重要现实意义的。
2、 数控机床类型及其加工技术概述
全球经济一体化的不断推进以及科学技术的飞速发展,使数控机床迅速风靡于全球,并成为现代工业生产中的重要生产技术。现阶段,数控机床有着很多种类,如人们熟知的数控冲床、数控车床以及数控铣床等,此外,还包括一系列的柔性制造单元等。对于数控技术来说,其是对数字电子信息技术的更深层次应用,通过数字电子信息技术的应用实现各种零部件的生产。在此过程中,人们需要对数控机床中的相关操作程序进行编程,以此实现对数控机床加工工艺参数、刀具位移量、机床运动等数据的设定,从而确保数控机床能够按照预先设定的操作程序进行各种类型零部件的加工。在对数控系统的程序进行编写时,编程人员需要结合零件的具体用途及其几何形状,并根据零件的具体用途、加工精度等要求来对相应的加工方法进行确定,以此确保所选的加工路线能够趋于合理、科学,然后,通过一系列的数学方法对零件样式进行精确计算,从而实现对刀具运行轨迹数据的可靠获取。此外,还要对机械螺纹类零件的坐标系及其基准进行确定,使零件得到正确的定位,然后,在数控系统中将编制的操作程序进行输入,从而使数控系统能够在设定的操作程序驱动下,实现对机械螺纹类零件的自动化加工。在对机械螺纹类零件进行加工过程中,相比传统的机床加工技术而言,数控机床加工技术能够使机械螺纹类零件的生产效率得以极大提高,并使得机械螺纹类零件的加工质量及其精度得到有效提升。由此可见,数控机床加工技术在现代工业生产中具有极大的技术优越性,这也使其能够为我国现代工业发展打下坚实的基础,并且能够更好地迎合现代工业的新时代发展要求。
3、 数控机床对机械螺纹类零件的加工原理分析
在对机械螺纹类零件进行加工时,经常采用数控机床进行零件加工,这是因为数控机床加工技术能够极大提高机械螺纹类零件的加工精确度,同时,确保零件加工安全,保障零件加工质量,提升螺纹类零件的加工效率,进而更好地推动我国现代工业的发展。现阶段,在市面中机械螺纹类零件的螺纹加工类型,主要有内螺纹、单线螺纹、变螺距螺纹、外螺纹、多线螺纹以及固定螺距螺纹等。以往的机床加工技术是根据螺纹线路切割与加工零件的。不过,机械加工则是以车削加工技术为主,通过机械传动带来对刀具进行驱动,以此实现零件加工。车床加工方法能够使零件加工质量有效提高,并使零件加工周期大幅缩短。数控机床在对机械螺纹类零件进行加工时,需要应用坐标式、尺寸测量等技术手段,以此全方位掌握机械螺纹类零件的尺寸及位置,例如,机械螺类零件的点、线、面等方位角度,这些数据都是实现合理编程的重要基础,由于在对机械螺纹类零件进行数控加工时,需要避免产生较大的误差累积,为了达到这一目的,往往需要对局部分散标注法中的部分尺寸进行改动。如表 1 所示为螺纹类零件的几种常用尺寸表。
表 1 螺纹类零件的几种常用尺寸表

在应用数控技术时,还要确保刀路使用能够尽量简洁化,使数控机床能够有序开展切削程序,考虑到数控机床在对机械螺纹类零件进行加工时应避免产生轮廓误差。因此,在加工过程中,还应确保零件直线轮廓能够平行于坐标轴,从而确保机械螺纹类零件得到高精度的加工,需要注意的是,在对机械螺纹类零件中的拐点进行处理时,要确保不会产生直角过渡。此外,还要合理、均匀地去除刀路材料,以减少刀路材料对加工刀具的冲击,这样能够有效提高零件的加工精度。
4 、机械螺纹类零件的数控机床加工技术研究
对于机械螺纹类零件的数控机床加工技术来说,其对零件的内外螺纹加工技术,主要有切削、铣削、磨削、研磨、攻丝、套丝以及滚压等六种加工技术方法,以下便对这六种加工技术方法进行深入的研究。
4.1 螺纹切削加工技术
其中,切削螺纹通常采用模具或成型刀具来对工件螺纹进行加工,包括车削、攻丝、旋风切削,铣削、套丝、研磨等。在对螺纹进行车削、磨削以及铣削时,工件每转一转,需确保机床传动链能够按照工件轴的方向进行均匀、准确的移动,在进行套丝或攻丝时,需要确保板牙或丝锥能够相对于工件采取相向旋转运动。同时,由螺纹沟槽来对刀具进行轴向移动引导。在数控机床对螺纹进行车削时,需要采用螺纹梳刀或成形车刀来实现。在使用成形车刀来对螺纹进行车削时,考虑到刀具在结构上较为简单,因此,成形车刀非常适合对机械螺纹类零件进行单件加工或小批量的加工。而在应用螺纹梳刀对螺纹进行车削加工时,因其刀具有着较为复杂的结构,但其生产效率却极高,因此,该刀具非常适用于对短螺纹工件进行一般批量或大批量的生产与加工。通常而言,普通的数控车床对机械螺纹零件的车削螺距精度可在 8 ~ 9 级。而对于专业高效的特殊类数控机床来说,其对螺纹的加工精度以及生产效率都能够得到显著提高。
4.2 螺纹铣削加工技术
螺纹铣削加工技术主要是采用梳形铣刀或盘形铣刀来实现机械螺纹类零件加工的,其中,盘形铣刀是通过蜗杆、铣削丝杆来对工件的梯形外螺纹进行铣削加工的,而梳形铣刀则能够对锥螺纹、外普通螺纹以及内普通螺纹进行铣削,考虑到梳形铣刀是利用多刃铣刀来加工零件的。因此,相比盘形铣刀来说,该类型铣刀具有更大的螺纹加工长度。所以,对于机械螺纹类零件来说,应用梳形铣刀的数控机床只需按照 1.25 ~ 1.5 转进行旋转加工,即可获得较高的零件加工效率。通常来说,螺纹铣削加工技术的螺距精度上能够达到8 ~ 9 级,而其表面粗糙度则能够达到 R5 ~ 0.63 微米,该加工技术能够对精度要求不高的机械螺纹零件进行螺纹加工或磨削前的批量化粗加工。如图 1 所示为盘形铣刀与梳形铣刀的铣削加工工艺技术。
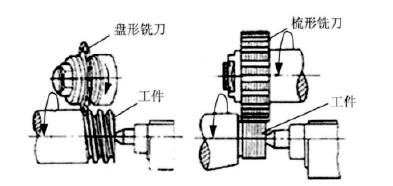
图 1 盘形铣刀与梳形铣刀的铣削加工工艺技术
4.3 螺纹磨削加工技术
还有一种是螺纹磨削加工技术,该技术是通过螺纹磨床对淬硬工件进行高精密度螺纹加工的技术手段。根据不同的砂轮截面形状,可将螺纹磨削划分成单线与多线两种磨削加工技术。其中,单线磨削是采用单线砂轮进行零件加工的,其加工螺旋的精度能够达到 5 ~ 6 级,而其表面粗糙度则能够达到 1.25 ~ 0.08 微米。通过单线砂轮能够使零件的修整更加方便,该技术非常适合对精密丝杆、蜗杆、螺纹量规等机械零纹零件实施小批量的磨削加工,技术优势较为明显。 而对于多线磨削,则是通过多线砂轮进行螺纹磨削加工的,该加工技术可以划分成切入磨法和分纵磨法工艺。分纵磨法所采用的砂轮宽度要比被磨螺纹的长度小,砂轮在进行单次或多次纵向移动过程中,其移动行程便相当于螺纹的最终磨削尺寸。而在切入磨法工艺中,采用的砂轮宽度则要比被磨螺纹长度大,多线砂轮在进行工件加工时,需要径向切入工件的表面,将工件旋转 1.25 圈左右,便可达到磨削目的,因此,该工艺具有较高的生产效率。不过,多线磨削工艺的加工精度较低,而且对工件进行砂轮修整也较为麻烦,切入磨法所采用的多线砂轮适合对紧固用途的标准螺纹、丝锥研磨进行大批量的磨削加工。
4.4 螺纹研磨加工技术
对于螺纹研磨加工技术来说,是通过铸铁等较软材质对螺杆型或螺母型的螺纹加工模具进行制作,针对工件中产生螺距误差的螺纹部位实施正向和反向的旋转研磨,以此确保螺距精度提高,一般来说,螺纹研磨加工技术还可以对淬硬的内螺纹进行加工,以此在降低螺距误差的同时,还能提高研磨精度的。
4.5 攻丝、套丝螺纹加工技术
在攻丝、套丝螺纹加工技术中,数控机床会通过自动旋转丝锥向工件施加一定的扭矩,以此使工件被加工出相应的内螺纹,而套丝则是数控机床通过板牙来对工件的外螺纹行切出。在该加工技术中,数控机床采用的板牙及丝锥精度会在很大程度上影响工件螺纹的加工精度,当然,除了可以通过钻床、车床等数控机床来进行螺纹加工以外,还可以用套丝机或手工的方式来对工件的螺纹进行加工。如图 2 所示为数控机床中的丝锥攻丝加工技术。
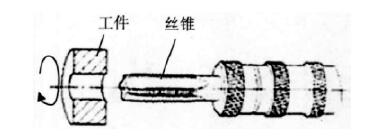
图 2 丝锥攻丝加工技术
4.6 螺纹滚压加工技术
螺纹滚压加工技术是通过成型滚压模具对工件进行加工,以使工件在加工过程中产生塑性变形,从而达到螺纹加工目的。数控机床在应用攻丝、套丝来对零件进行螺纹加工时,往往要在机床上安装自动开合螺纹滚压头,并配备搓丝机与滚丝机,该加工技术适合对标准紧固件、螺纹连接件中的外螺纹进行大批量加工,滚压螺纹的外径通常需要控制在 25 毫米以内,而其螺纹长度则不应超过 100 毫米。该加工技术所加工的螺纹精度能够达到二级,全部批件直径相当于被加工螺纹中径。仅仅采用滚压模具通常是无法对内螺纹进行加工的,不过,如果工件的材质较软,则可以通过无槽挤压丝锥对内螺纹进行冷挤,这种加工原理和攻丝是比较类似的。再通过无槽挤压丝锥对内螺纹进行冷挤时,其扭矩要大于攻丝的一倍左右,但在表面加工质量及精度上,也要略高于攻丝。螺纹滚压加工技术具有以下优越性:其一,相比车削、磨削以及铣削等螺纹加工技术来说,具有更小的表面粗糙度;其二,在对螺纹进行滚压加工后,其表面由于冷作硬化,因此,能够使加工硬度及强度提高;其三,螺纹滚压能够对材料进行更加充分的利用,不过,其生产率相比切削加工来说要更长,但是,也更易于通过数控机床实现螺纹的自动化加工;其四,螺纹滚压所采用的滚压模具具有较高的使用寿命,不过,需要确保机床加工的零件材料硬度不能超过 HRC40。当然,螺纹滚压加工技术需要确保毛坯尺寸精度较高,并且在滚压模具硬度及精度上也有着很高的要求,因此,对滚压模具进行制造是较为困难的,该加工工艺无法对牙形不对称螺纹进行加工。根据数控机床中不同的滚压模具,可将螺纹滚压划分成滚丝与搓丝两种,其中,搓丝是将有螺纹牙形的两块搓丝板按照 1/2 的螺距来进行错开布置,并确保静板处于固定状态,而动板则相对于静板来进行平行、往复的直线运动。如果工件处于两板之间,则由动感进行前进搓压,以确保工件表面能够产生塑性变形,以此形成相应的螺纹。滚丝则可采用滚压头滚丝、切向滚丝以及径向滚丝,其中径向滚丝的数量为2 ~ 3 个,这些滚丝轮具有螺纹牙形,需要将其安装于平行轴上,而工件则处于两轮间支承位置。在应用数控机床进行加工时,两个滚丝轮会沿着同一方向以相同的速度进行旋转,其中,一个滚丝轮还会进行径向进给运动,而工件则能够在滚丝轮带动下进行旋转。这时,工件的表面便会受到径压作用而形成螺纹。如果在加工丝杆时对精度没有较高的要求,也可通过类似的方法来进行滚压成型。如图 3 所示为数控机床对零件的径向滚丝加工工艺。
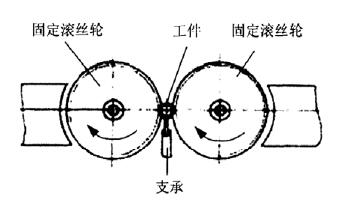
图 3 径向滚丝加工工艺
切向滚丝又叫做行星式滚丝,其滚压工具的主要构成包括三块固定弧形丝板以及一个旋转的中央滚丝轮,在进行滚丝加工时,需要确保工件能够被不间断地送进,这使其相比于径向滚丝以及搓丝来说,要具有更高的生产率。滚压头滚丝则需要利用数控机床来进行自动化的自螺纹加工,其通常能够对工件中的短螺纹进行加工。在工件外周滚丝轮中,均匀分布着 3 ~ 4 个滚压头,再进行滚压过程中,工件会在滚压轮的驱动下进行旋转,而滚压头则会径向给进,以使工件被滚压出相应的螺纹。如图 4 为切向滚丝加工工艺。
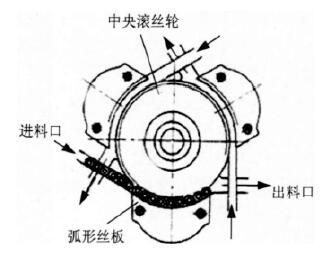
图 4 切向滚丝加工工艺
5 、数控机床对机械螺纹类零件的加工步骤分析
数控机床对机械螺纹类零件的加工步骤如下:其一,在机械螺纹类零件的图纸设计完毕,还需要确保程序编写、工件选择以及刀具的选择能够合理;其二,操作人员需要通过数控机床对机械螺纹类零件进行加工,在此过程中,需要结合工件的设计图纸要求进行加工,不过,要确保设计图纸能够对机械螺纹类零件的各个尺寸及精度进行详细标明,这样才能确保选择的加工方法合理,从而不会影响零件的加工精度;其三,在对机械螺纹类零件进行加工之前,还需要确保数控机床的编程能够提前预留出足够的余量,以确保机械螺纹类零件在按照编写的程序进行加工时,能够实现对机械间隙的灵活补偿,此外,还要尽量保证一次装夹便可使端面得以顺利加工;其四,在加工机械螺纹类零件过程中,加工人员还要确保计算机加工程序能够得到合理的编写与完善,通过自动化编程实现自动化、数控化加工,计算机具有强大的识图、计算功能,这使其能够对编程的准确性进行有效改进,从而防止在加工时产生各种错误,并且还能确保机械螺纹类零件在加工时的精度得到保证。加工人员在利用数控机床进行机械螺纹类零件加工时,要对零件加工所涉及的工艺及其图样行深入、细致的研究,选择最合理的数控加工技术,并确保零件的加工效率得到最大化提高。依据设计图纸中的要求,对走刀路线进行预先设计与完善,确保走刀路线能够在设计图纸中得到有效落实,并使编程步骤得到简化。在通过数控机床对机械螺纹零件进行加工的过程中,加工人员还要对数控系统的操作流程、系统结构、系统不足等进行全面的了解,以此避免在使用数控机床进行加工时发生误操作,并在确保工件加工质量得到可靠保证的同时,使机械螺纹类零件的加工效率得以不断提高。
6 、 结语
总而言之,随着全球经济一体化的不断推进,各国在经济、技术等方面的交流变得日益密切,这也使越来越多的新技术、新工艺、新设备得以不断涌现,在此过程中,数控机床加工技术在机械螺纹类零件加工生产中的技术优越性也变得愈发明显,随着数控机床加工技术的发展与进步,其必将使机械螺纹类零件的加工效率及加工质量得到进一步提高。可以说,数控机床在现代工业中的应用,不仅使产品的综合性能大幅提高,也使螺纹零件的生产与制作变得更加细致,有效优化了现代工业的生产程序,相信在不久的将来,我国现代工业的发展必将更加依赖于数控机床,而数控机床也将促使我国现代工业迎来更加美好的明天。
投稿箱:
如果您有机床行业、企业相关新闻稿件发表,或进行资讯合作,欢迎联系本网编辑部, 邮箱:skjcsc@vip.sina.com
如果您有机床行业、企业相关新闻稿件发表,或进行资讯合作,欢迎联系本网编辑部, 邮箱:skjcsc@vip.sina.com