数控车削安全攻略
2019-7-5 来源:山东临沂技师学院 作者:赵培哲 徐淑琛
摘要:针对不同数控车削加工过程,本文介绍了安全操作的注意事项以及如何减少安全事故的出现。
生产中的安全包含两个方面:“人”的安全和“物”的安全,并且“人”的安全是首要的、优先的,任何可能造成人身伤害的因素都应消除在萌芽状态。“物”的安全是指刀具、工件、机床等生产资料的安全。机械加工过程中如果出现事故,轻则刀具、工件损坏,造成不必要的浪费,重则造成机床部件的重大损坏甚至报废,而修复机床造成的时间、金钱的损失、机床加工精度的下降及生产过程的延误都是巨大的(见图1)。
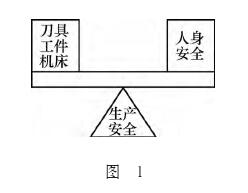
车削加工从普通手动车床到现代数控车床的变化,不仅仅是加工手段上的变化,在安全防护上更是有了极大的提升。从普通车床的切屑、切削液四处飞溅的开放加工环境,到全封闭的数控车床,在加工过程中,操作者只能通过观察窗监测加工过程。只有在防护门打开、机床停止运转的情况下,操作者才能接触到机床内部。容易造成划伤的切屑清理工作也由人工清理变为用排屑机进行机械清理,数控化的机床在生产环境和条件上有了极大的改善。可以这样说,数控加工条件下,人身伤害的因素降低到了一个很低的水平。
反观数控加工生产过程中,由于操作者的原因而引起刀具、工件和机床的损伤可以说是司空见惯、比比皆是。数控加工过程中“物”的安全上升到一个必须严肃对待的水平。国内数控机床整体开机率不高的原因不仅是机床质量上的问题,更多的应该归咎于操作者不当操作损伤(损坏)机床而造成的停机。良好的操作习惯,可以在较大程度上减少加工事故造成的损失,同时也减少了因此而可能引起的人身伤害。机床从开机到合格工件的产出的整个过程中,在很多环节都存在加工事故的风险。针对不同环节的特点,采取相对应的对策,则可以把这些风险降至最低的可控程度内。
1. 数控车床开机安全攻略
现在越来越多的数控车床装备了绝对编码器,开机后省略了机床回零操作,但是安装相对编码器的数控车床开机后的基本操作仍是回零。这个环节容易出现的问题是回零操作时刀架与尾座发生碰撞,这主要是回零操作时先进行Z 轴回零而引起的。正确操作是先进行X 轴的回零,待刀架移至X向最大行程时再进行Z轴的回零操作,则会避免这种问题的发生,这也是数控车床回零操作的基本原则(见图2)。
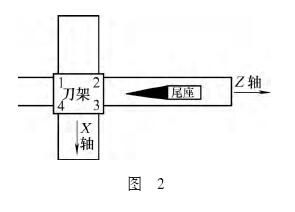
2. 数控车床对刀安全攻略
数控车削时对刀是重要的操作,对刀数据的准确与否决定了后续的工件试切的安全。常见的对刀错误:
( 1 ) 例 如 当 前 刀 具 为 2 号刀具,对刀数据虽然准确,但却输入到1号刀具补偿位置,程序运行时调用2号刀具及2号刀具补偿时,则会出现重大数据错误而引发事故。对刀的基本原则是:“刀具号码与刀具补偿号码对应,程序调用刀具号码与实际刀具对应”。当前2号刀具不是只能调用2号刀具补偿,也可以调用其他1号、3号……刀具补偿数据,但是保持三者的对应有利于发现和减少对刀数据出现重大失误。
(2)使用电子手轮试切后退刀时手轮摇反方向,应该退刀反而进刀切入工件,此时一般是刀具或工件损坏,不会造成较大的损失。避免此类误操作的方法是:可以使用手轮试切对刀,但是退刀时一定转换到手动模式,机床操作面板上4个方向键对应刀架4个方向的移动,是极难出错的,这也是对刀过程的基本安全攻略(见图3)。
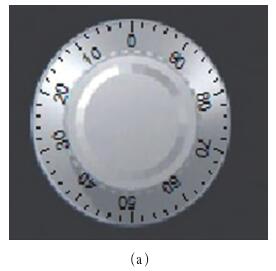
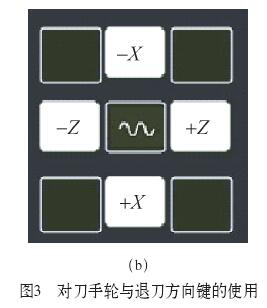
3. 首件试切的重要性及安全攻略
数据加工首件试切是最重要的操作,也是最难的操作,同时也是最容易出现加工事故的环节。根据我们在数控加工实践教学的不完全统计,约有一半以上的加工事故出现在首件试切环节,因此针对此环节的安全防备措施也是最多的。对刀数据准确与否从对刀过程并不能看出,只能通过试切环节才能检验出对刀数据是否有错误。下面以一个简单的加工实例介绍首件试切的安全攻略(见图4)。
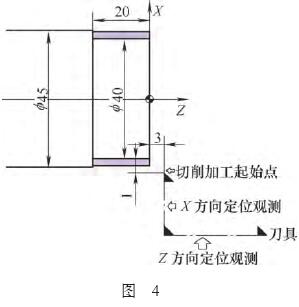
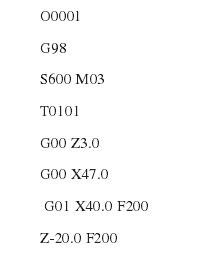
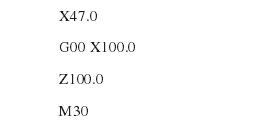
首件试切常用的三种安全策略是:低速移动、单段运行和定点观测。低速移动是指首件试切时刀架的移动倍率开关放在较低的位置,发现异常或危险情况可以及时暂停,首件试切安全结束后,连续工件的加工则可以使用较高的移动倍率,以提高加工效率。单段运行也是首件试切的常用手段。使用单段运行,第一可以把可能的错误控制在本程序段内,第二则是程序单段运行时自动暂停。此时可以借助观察绝对坐标数值和刀具的实际位置,判断上段程序运行是否准确,预测下段程序是否可能出现错误。对刀数据的正确与否只有通过试切环节才能检验得出,但往往出现问题的是:当加工出现事故后才发现对刀数据出现错误,此时刀具和工件甚至机床的损坏已经造成。那么可以使用第三种策略:“定点观测”,也是最重要、最常用且最有效的方法,这种方法可以在不造成损失的情况下提前判断对刀数据的错对。定点观测需要编程和机床操作的配合,在低速移动和单段运行的基础上应用。定点观测需要在工件毛坯附近设立一个点,称之为“加工起始点”。此点以前刀具均为快速移动定位阶段,从此点以后刀具则开始慢速切削加工过程。例如本实例中,加工起始点设置在(X47.0,Z3.0)处,距离毛坯外圆1.0mm,距离端面3.0m m。在编程中使用如下两段程序:G00 Z3.0;G00 X47.0;使用G00指令单轴移动。通常这两段程序一般一句:G00 X47.0 Z3.0;因为G00指令双轴同时斜向移动,很难提前判断对刀数据的对错,往往是出现事故才意识到对刀出错,但此时已经造成损失。
程 序 段 G 0 0 Z 3 . 0 ; G 0 0 X 5 2 . 0 , 在 单 段 运 行 时 先 定 位Z5.0,此时X 轴方向刀具远离工件,刀架Z 向移动不会有碰撞工件的危险。程序单段暂停时,从X 轴水平观察,刀具刀尖应位于距离端面3.0mm处(此时可以有少许误差,但不能有较大的偏差),远离工件或位于毛坯内侧均属偏差(见图5),发现对刀出现错误后加工就不需再进行。如果Z 向定位没有错误,那么可以继续单段运行G00 X52.0至加工起始点(X52.0,Z3.0),程序单段暂停时,从Z 轴水平方向观察刀具刀尖应贴近外圆,远离工件或深入工件内侧均表明对刀错误(见图6),但此时因刀具距离毛坯端面3.0左右,即使X向对刀错误,因为是X 向单轴移动,此时也不会出现撞刀事故。在加工初始点判断X、Z两个方向对刀数据均正确,就可以继续进行后续加工,这种方法对各种刀具及编程均适用。如果是批量加工工件,可以在首件安全结束后,将G00 Z3.0;G00 X47.0两段程序合为一
段G00 X47.0 Z3.0,以提高程序运行效率。

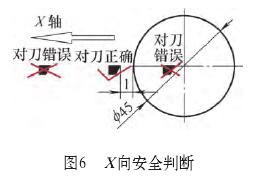
4. 编程中的安全攻略
数控加工中模态指令的应用带来了编程上的便利,但也容易引发编程加工上的错误。最常见的是G00指令快速退刀后,再次进刀切削加工时漏掉了G01 直线插补指令,程序模态沿用上段的G00指令快速切削,造成刀具和工件的损坏。常用的固定循环指令G70~G76不仅可以简化编程,还可以消除应用这种模态指令所带来的风险,因为固定循环指令中的进刀、退刀均由系统内部自动设定,不会出现模态指令的误用问题;另外,固定循环指令的一大特点是:固定循环指令无论从哪一个加工起始点开始加工,到循环结束后,一定都会自动返回原加工起始点,固定循环的加工起始点一般位于毛坯外部,从此点退刀,更可以减少撞刀的风险,所以编程中尽量使用固定循环指令,也是一种安全攻略。数控试切编程中刀具快速移动定位一般使用单轴移动,比如上面例子中G00 X42.0 Z3.0 一般写为两段 G00 Z3.0;G00 X42.0;避免刀具双轴移动可能造成的损失。刀具退出工件结束加工时也是如此,外轮廓加工刀具先沿X向退出工件,然后再沿Z 向退至安全位置,内轮廓加工则相反。如果试切加工安全合格,双向进刀和退刀在批量加工时也是必须的。
5. 数控车削螺纹时的安全
攻略无论是在普车加工还是数控车削中,螺纹加工都是难点和危险点。特别是数控加工螺纹都是高速、高效切削,主轴转速、刀具进给速度极快,如果出现错误而引起螺纹加工事故,其损失是极为严重的。其原因有两方面:一是螺纹加工一般是工件加工的最后阶段,如果螺纹加工出现问题而报废,前面加工工序在工件上形成的附加值也会全部丢失;二是数控车削螺纹与车削外圆不同,外圆车削过程中可以在任意位置暂停刀具运动,以观察加工状况,螺纹数控车削过程则不同,如果螺纹加工过程中发现可能出现问题按下暂停按钮,刀具不会立即暂停运动(只有紧急停止按钮能停止刀具运动,但此时主轴也停止运动,刀具和工件会一起报废),而是会一直加工至螺纹终点才会暂停(不同的数控系统功能不同,有些数控系统在螺纹加工中暂停后会从螺纹中部斜向退出以保护螺纹)。因而螺纹加工出现事故时,刀具和工件基本一起报废,事故严重时机床部件都会受损。数 控车削螺纹的安全攻略是:整体偏移、分次进刀。基本方法是:先确定螺纹加工长度无误,再分次进刀加工螺纹至合格。下面以一个简单的加工实例介绍具体方法。螺 纹 车 削 的加工起始点位于(X 42.0,Z 3.0),快速定位时仍采用单轴定位,以预判对刀数据是否出错。螺纹刀对刀完成后,放大X 向的刀补数据20.0~30.0m m,Z 向刀补数据向右偏移一段距离,一般是螺纹的加工长度,这样螺纹的实际加工路线就整体挪至偏移加工路线处(见图7)。
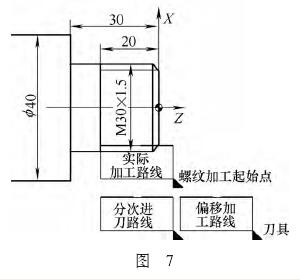
此时试运行螺纹加工程序,刀具将远离工件,即使对刀出现错误,也有较多的时间来发现和处置,出现事故的风险是很低的。运行程序至螺纹加工结束单段暂停时,从水平方向观察,螺纹刀尖应正好位于实际螺纹加工的开始处,此时可以判定螺纹刀Z 向对刀数据无误,同时从工件轴向水平观察螺纹刀尖与毛坯的X 向间距的大小,预判螺纹刀X 向对刀数据的正误。螺纹数控加工的Z 向起点一般不允许变化,否则会产生螺纹乱扣而报废。本例中螺纹刀Z 向刀具补偿先向右偏移螺纹长度2 0 . 0 m m ,程序试运行检验螺纹刀Z 向刀具补偿无误后再向左偏移20.0m m分次进刀加工路线处(选择平移距离20.0mm,一是可以方便观察Z 向对刀数据和螺纹加工长度是否有误,二是即使螺纹刀X 向对刀出错也不会产生实际的螺纹加工而造成事故),此时螺纹刀具不能再修改Z 向刀补数据,只能分次减少X 向刀具补偿,观察刀具与毛坯表面的间距是否出现异常,直至刀具切入工件,加工螺纹至合格尺寸。内螺纹的数控加工策略和外螺纹加工相似,不过由于受内轮廓加工的限制,螺纹刀X 向刀补数据向内减小的数值不能太大,以免引起加工干涉;至于长螺纹加工,例如:螺纹的加工长度200.0m m,编程时可以试切加工2 0 . 0 m m 的长度,以节省调试时间,程序试运行无误后则可将程序中的20.0mm改为200.0mm,螺纹加工固定循环指令有斜向退刀功能,在20.0mm长螺纹结束时的退刀不影响整体螺纹加工的质量。数控车削过程中 , 主要的安全隐患来自以上介绍的机床操作、首件试切和螺纹切削等方面,其中首件试切是最容易出问题的环节。但遵循以上的安全攻略进行机床操作,可以把发生加工事故的可能性降至最低,从而保障数控加工过程的顺利进行,同时保护加工过程中“人”和“物”的安全。
投稿箱:
如果您有机床行业、企业相关新闻稿件发表,或进行资讯合作,欢迎联系本网编辑部, 邮箱:skjcsc@vip.sina.com
如果您有机床行业、企业相关新闻稿件发表,或进行资讯合作,欢迎联系本网编辑部, 邮箱:skjcsc@vip.sina.com